- お役立ち記事
- Specific examples of Poka-yoke introduction and error prevention that are attracting attention from equipment maintenance departments
月間76,176名の
製造業ご担当者様が閲覧しています*
*2025年3月31日現在のGoogle Analyticsのデータより
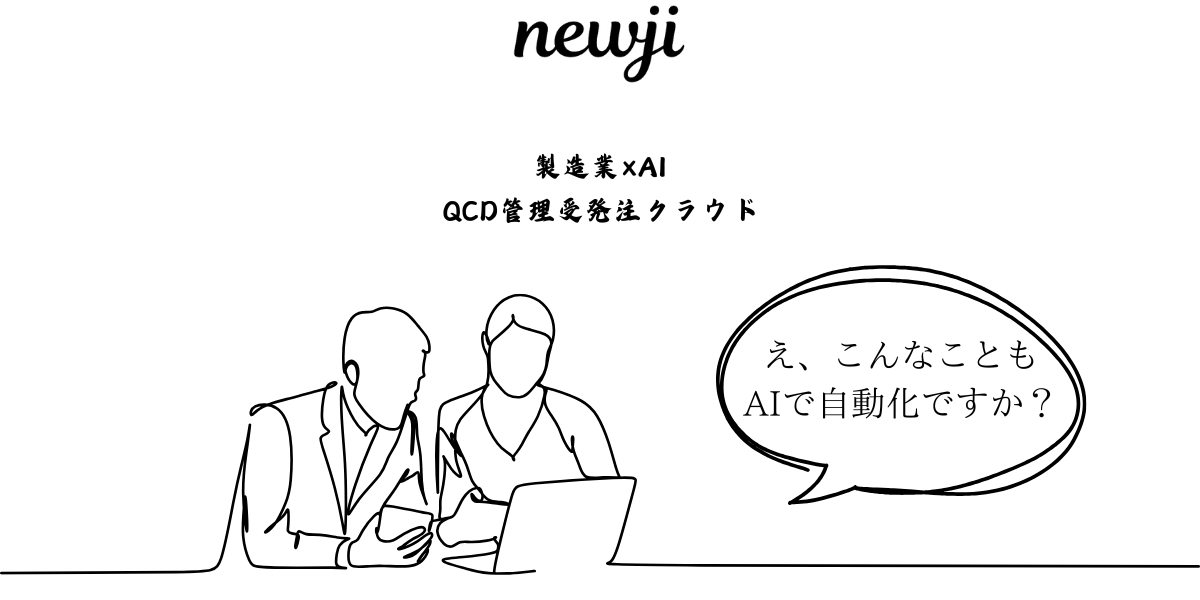
Specific examples of Poka-yoke introduction and error prevention that are attracting attention from equipment maintenance departments
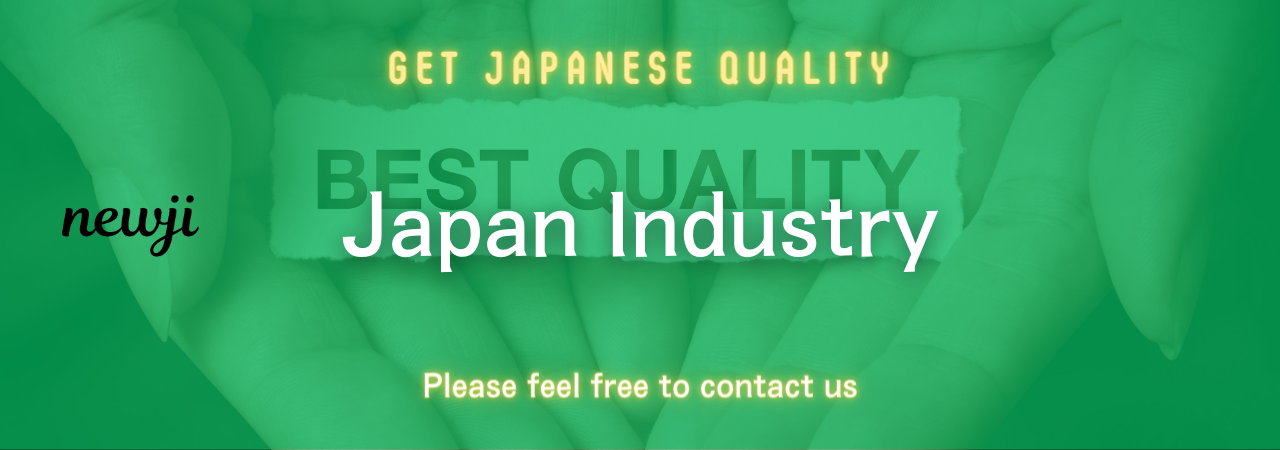
目次
Understanding Poka-Yoke
Poka-yoke is a Japanese term that means “mistake-proofing” or “error prevention.”
It is a mechanism used in lean manufacturing processes that helps prevent errors in the production line.
The concept, introduced by Shigeo Shingo, is all about creating a fail-safe mechanism to help workers avoid mistakes before they happen.
It ensures quality through design, allowing people to focus on tasks rather than worrying about possible errors.
This method is gaining popularity in equipment maintenance departments worldwide because it helps increase efficiency and reliability.
The Importance of Poka-Yoke in Maintenance
Equipment maintenance departments are responsible for ensuring machines operate smoothly.
Unexpected breakdowns not only delay production but also increase costs.
Poka-yoke plays a crucial role in preventing these unexpected failures.
By incorporating poka-yoke techniques into routine maintenance, errors can be minimized, reducing equipment downtime and ensuring smooth operations.
This approach not only improves productivity but also extends the lifespan of machinery.
Reduced Human Error
Humans are prone to making mistakes, particularly during repetitive tasks.
Poka-yoke introduces checks at various stages of a process, which helps prevent human error.
For instance, if a maintenance worker needs to tighten a bolt to a specific torque, a poka-yoke solution might involve a torque wrench that signals when the correct tension is achieved.
Enhanced Machine Performance
Implementing poka-yoke can also enhance the overall performance of machinery.
By preventing errors, machines can operate consistently at their optimal level, reducing wear and tear.
This proactive approach ensures machines are always in good condition, maximizing their efficiency and output.
Examples of Poka-Yoke in Equipment Maintenance
Let’s explore some practical examples where poka-yoke mechanisms can transform maintenance tasks within an organization.
Color Coding and Labeling
One simple yet effective poka-yoke technique is the use of color coding and labeling.
In maintenance, different tools, equipment, and parts can be labeled or color-coded based on their functions.
For instance, using distinct colors for lubrication tasks can help workers select the correct lubricant quickly, reducing the chance of using an unsuitable product that could cause equipment damage.
Error Detection Sensors
Another advanced poka-yoke method is the use of sensors to detect potential errors before they result in significant problems.
Sensors can be installed on machinery parts prone to failure, such as belts or motors, to detect irregularities.
These sensors can alert maintenance personnel to take corrective actions before a breakdown occurs, maintaining production continuity.
Checklists and Standardized Procedures
While not a physical mechanism, checklists can be a powerful poka-yoke tool when used correctly.
Standardizing maintenance procedures ensures that each task is performed consistently and nothing is overlooked.
For example, maintenance personnel can use a checklist when inspecting a machine to ensure all critical components are examined and serviced as needed, reducing the possibility of missing an important step.
Physical Barriers
Physical barriers are another form of poka-yoke frequently used in equipment maintenance.
They prevent workers from accessing machine parts or performing tasks until specific conditions are met.
Consider a situation where a machine cannot be operated until a safety guard is securely in place.
This poka-yoke method ensures the equipment is only used under safe conditions, preventing accidents and promoting safe maintenance practices.
Benefits of Implementing Poka-Yoke
Incorporating poka-yoke into equipment maintenance processes delivers several advantages, making it an attractive approach for organizations committed to excellence.
Improved Safety
Poka-yoke dramatically increases workplace safety by preventing errors that could cause accidents or injuries.
By incorporating failsafe mechanisms, workers are less likely to engage in unsafe practices.
Cost Savings
Reducing errors and avoiding equipment failures results in significant cost savings.
Fewer breakdowns mean less money spent on repairs and replacement parts, leading to more efficient budget management.
Increased Equipment Lifespan
Machines that are maintained properly without errors tend to have longer operating lives.
This longevity translates into better return on investment for companies, as equipment doesn’t need to be replaced as frequently.
Challenges of Implementing Poka-Yoke
While the advantages of poka-yoke are evident, implementing these mechanisms is not without challenges.
Initial Setup Costs
The initial cost of installing poka-yoke mechanisms can be high, especially for sophisticated technology like error detection sensors.
Organizations may also need to train staff on new processes, which can involve additional time and resources.
Resistance to Change
Employees accustomed to traditional methods might resist change.
Convincing them of the long-term benefits of poka-yoke often requires clear communication and training efforts from management.
Integration with Existing Processes
Integrating poka-yoke with existing workflows can be complex and demanding.
Companies must carefully plan the integration to avoid disruptions and ensure a seamless transition.
Conclusion: A Worthwhile Investment
Despite the challenges, introducing poka-yoke mechanisms into equipment maintenance is a worthwhile investment for organizations aiming for operational excellence.
The benefits of reduced errors, improved safety, cost savings, and increased equipment lifespan cannot be overstated.
By embracing this innovative approach, companies equip themselves to maintain a competitive edge in today’s fast-paced business environment.
Focusing on error prevention ensures that maintenance teams can work more efficiently, paving the way for sustainable growth and success.
資料ダウンロード
QCD管理受発注クラウド「newji」は、受発注部門で必要なQCD管理全てを備えた、現場特化型兼クラウド型の今世紀最高の受発注管理システムとなります。
ユーザー登録
受発注業務の効率化だけでなく、システムを導入することで、コスト削減や製品・資材のステータス可視化のほか、属人化していた受発注情報の共有化による内部不正防止や統制にも役立ちます。
NEWJI DX
製造業に特化したデジタルトランスフォーメーション(DX)の実現を目指す請負開発型のコンサルティングサービスです。AI、iPaaS、および先端の技術を駆使して、製造プロセスの効率化、業務効率化、チームワーク強化、コスト削減、品質向上を実現します。このサービスは、製造業の課題を深く理解し、それに対する最適なデジタルソリューションを提供することで、企業が持続的な成長とイノベーションを達成できるようサポートします。
製造業ニュース解説
製造業、主に購買・調達部門にお勤めの方々に向けた情報を配信しております。
新任の方やベテランの方、管理職を対象とした幅広いコンテンツをご用意しております。
お問い合わせ
コストダウンが利益に直結する術だと理解していても、なかなか前に進めることができない状況。そんな時は、newjiのコストダウン自動化機能で大きく利益貢献しよう!
(β版非公開)