- お役立ち記事
- Specific measures for purchasing departments to improve supply chain reliability
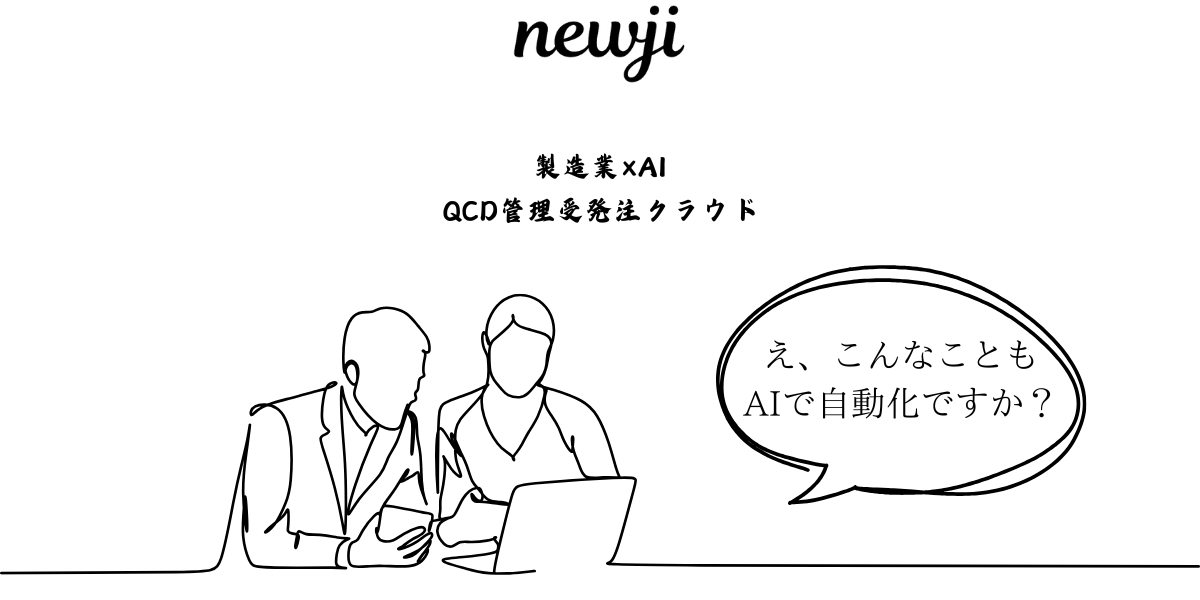
Specific measures for purchasing departments to improve supply chain reliability
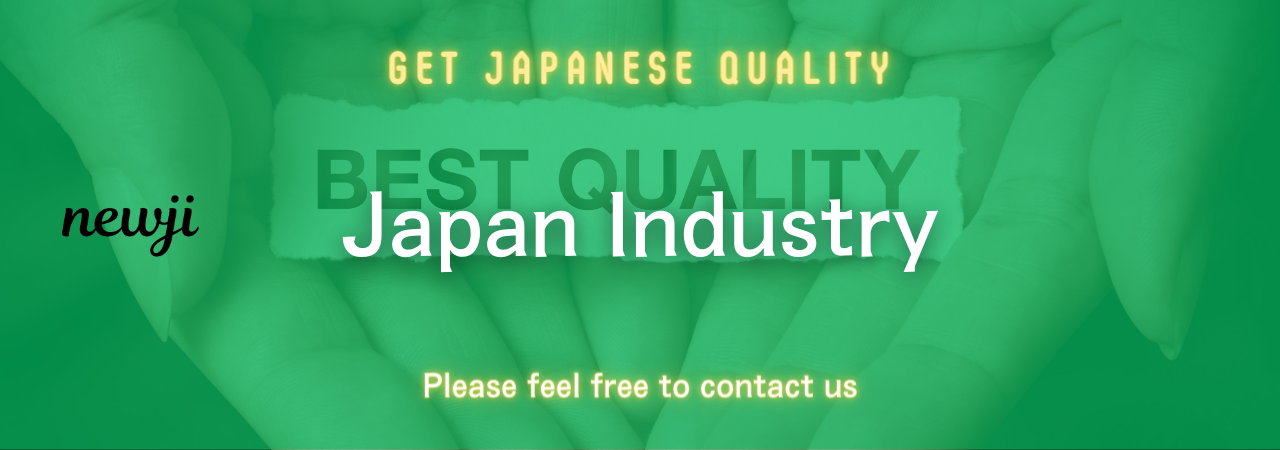
目次
Understanding the Importance of Supply Chain Reliability
In today’s globalized economy, the reliability of a supply chain is pivotal for a company’s success.
Supply chain reliability ensures that goods and services are delivered on time, reducing disruption and maintaining smooth operations.
For purchasing departments, improving supply chain reliability is not just about efficiency but also competitiveness.
When a supply chain falters, it can lead to delays, increased costs, and dissatisfied customers — all of which harm a business’s reputation and bottom line.
Assessing Current Supply Chain Performance
Before implementing any new strategies, purchasing departments need to assess their current supply chain performance thoroughly.
This assessment should identify any existing weaknesses and areas of opportunity.
Analyzing data on delivery times, supplier reliability, and product quality gives a clear picture of where improvements are needed.
From this analysis, specific and targeted measures can be developed.
Evaluation Tools and Techniques
Several tools and techniques are available to help purchasing departments evaluate supply chain performance.
For instance, the use of Key Performance Indicators (KPIs) such as lead time, order accuracy, and fill rate are standard metrics to measure efficiency and reliability.
Also, advanced analytics, including predictive analysis, can provide insights into potential risks and help prepare for unforeseen circumstances.
Building Strong Relationships with Suppliers
One of the most effective ways to enhance supply chain reliability is by building strong relationships with suppliers.
Regular communication and transparent business dealings create a trustworthy environment.
When suppliers understand a company’s needs and challenges, they are more likely to deliver high-quality services consistently.
Strategic Supplier Partnerships
Developing strategic partnerships with key suppliers can have a significant impact on reliability.
This can be achieved through long-term contracts, joint initiatives, and integrating technologies to share information better.
Such collaborations can lead to innovation and improvements in service delivery that benefit both parties.
Supplier Performance Management
Implementing a supplier performance management system is crucial.
Using scorecards and regular performance reviews will keep suppliers accountable and ensure they meet the required standards.
This proactive approach helps in resolving issues quickly and maintaining steady supply chain operations.
Implementing Advanced Technology
Leveraging advanced technology is critical for modernizing and improving supply chain reliability.
Automation, Artificial Intelligence (AI), and the Internet of Things (IoT) are revolutionizing how purchasing departments operate.
Real-time Tracking and Inventory Management
Real-time tracking systems enable constant monitoring of inventory levels, helping prevent shortages and overstock situations.
These systems provide vital data that assist purchasing departments in making informed decisions about inventory replenishment, ensuring a balanced supply chain.
Enhancing Predictive Analytics
Predictive analytics uses historical data to forecast future supply chain trends.
It helps purchasing departments anticipate demand changes, potential disruptions, and needed adjustments.
By being proactive rather than reactive, companies can mitigate risks and boost their supply chain’s reliability.
Developing a Risk Management Strategy
A comprehensive risk management strategy prepares the purchasing department to handle unexpected challenges.
This strategy should encompass the identification of potential risks, such as natural disasters, supplier insolvencies, or geopolitical issues.
Risk Assessment Practices
Conducting regular risk assessments helps in understanding vulnerabilities within the supply chain.
Simulating various scenarios prepares the department for quick and effective action when a risk materializes.
By carefully analyzing these risks, purchasing departments can create contingency plans to minimize impact.
Building Flexibility into Supply Chains
Flexibility is vital in responding to fluctuations and disruptions effectively within the supply chain.
For example, increasing the number of suppliers or having backup suppliers ensures continuous supply even if one source is compromised.
Additionally, diversifying sourcing locations reduces dependency on a single region, protecting against regional disruptions.
Investing in Staff Training and Development
A well-trained team is essential for implementing and managing the strategies for improving supply chain reliability.
Investing in continuous education programs enhances employees’ skills in using new technologies and understanding advanced supply chain management concepts.
Training Programs
Purchasing departments should establish regular training programs that cover technology updates, trends in supply chain management, and crisis-handling techniques.
Staff equipped with the latest knowledge are more adept at problem-solving and efficient management.
Encouraging Cross-functional Collaboration
Encouraging collaboration between different departments within an organization leads to a more cohesive approach to supply chain management.
Integrating insights from sales, marketing, and operations helps the purchasing department align purchasing decisions with the company’s overall strategic goals.
Continuously Monitoring and Improving Processes
Improvement in supply chain reliability is an ongoing process that requires consistent monitoring and optimization.
Using the data collected from performance metrics, purchasing departments can identify process bottlenecks and implement necessary improvements.
Feedback Systems
Establishing feedback mechanisms with both suppliers and end customers provides valuable insights into potential problem areas.
Continuous feedback and open communication ensure that any issues are addressed promptly, further strengthening the reliability of the supply chain.
In conclusion, improving supply chain reliability is a multifaceted endeavor requiring strategic planning, technology integration, risk management, and ongoing process improvement.
By focusing on these areas, purchasing departments can ensure a more resilient and efficient supply chain, ultimately leading to greater customer satisfaction and organizational success.
資料ダウンロード
QCD調達購買管理クラウド「newji」は、調達購買部門で必要なQCD管理全てを備えた、現場特化型兼クラウド型の今世紀最高の購買管理システムとなります。
ユーザー登録
調達購買業務の効率化だけでなく、システムを導入することで、コスト削減や製品・資材のステータス可視化のほか、属人化していた購買情報の共有化による内部不正防止や統制にも役立ちます。
NEWJI DX
製造業に特化したデジタルトランスフォーメーション(DX)の実現を目指す請負開発型のコンサルティングサービスです。AI、iPaaS、および先端の技術を駆使して、製造プロセスの効率化、業務効率化、チームワーク強化、コスト削減、品質向上を実現します。このサービスは、製造業の課題を深く理解し、それに対する最適なデジタルソリューションを提供することで、企業が持続的な成長とイノベーションを達成できるようサポートします。
オンライン講座
製造業、主に購買・調達部門にお勤めの方々に向けた情報を配信しております。
新任の方やベテランの方、管理職を対象とした幅広いコンテンツをご用意しております。
お問い合わせ
コストダウンが利益に直結する術だと理解していても、なかなか前に進めることができない状況。そんな時は、newjiのコストダウン自動化機能で大きく利益貢献しよう!
(Β版非公開)