- お役立ち記事
- Specific measures to combat robotization and labor shortages in the manufacturing industry
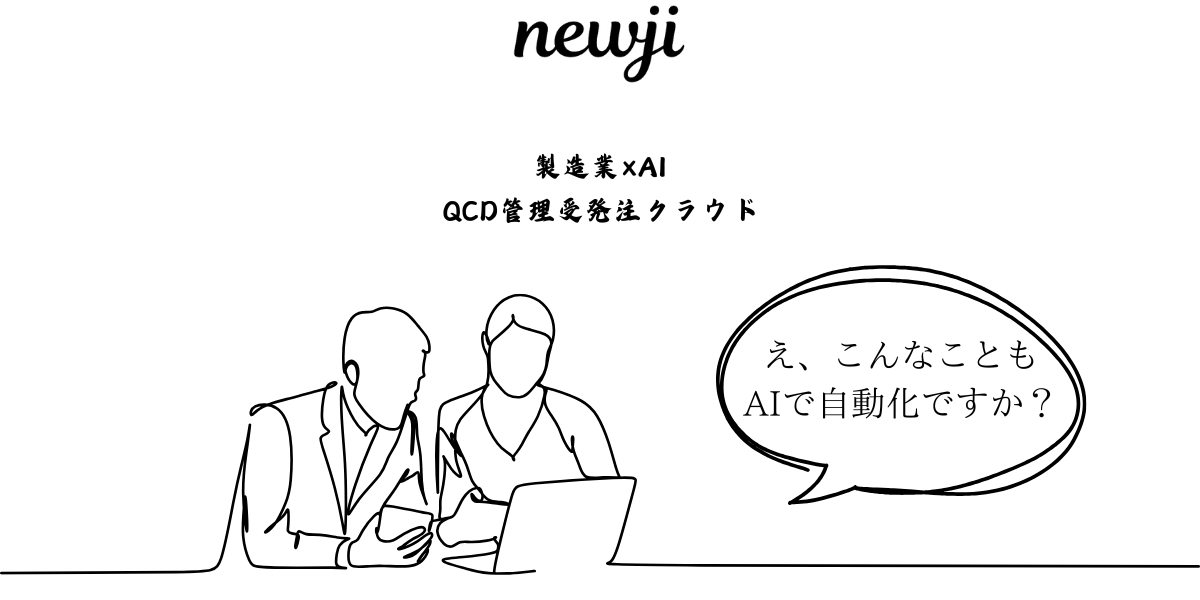
Specific measures to combat robotization and labor shortages in the manufacturing industry
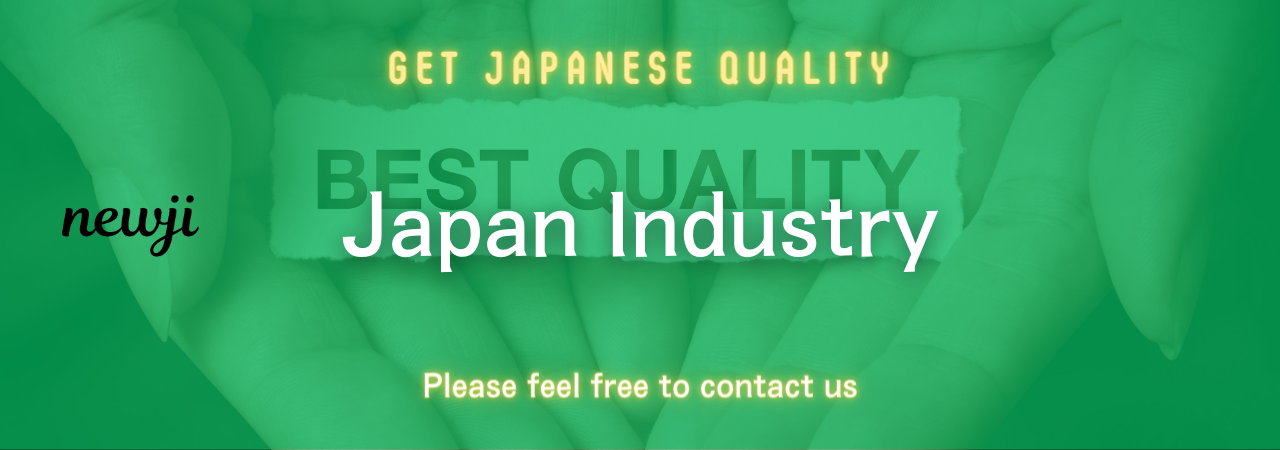
目次
Understanding the Impact of Robotization on the Manufacturing Industry
As technology continues to advance at a rapid pace, robotization has become a significant factor in transforming the manufacturing industry.
Robots have the ability to perform tasks with precision and efficiency, leading to increased productivity and reduced costs for manufacturers.
However, while robotization has its benefits, it presents challenges as well, particularly when it comes to labor shortages within the industry.
The Dual Role of Robots in Manufacturing
Robots play a dual role in the manufacturing industry by both alleviating and exacerbating labor shortages.
On one hand, they help fill the gap left by the decreasing workforce by taking on repetitive and physically demanding tasks, reducing the need for human involvement.
This allows companies to maintain a steady level of production even amid labor shortages.
On the other hand, the rise of robotization can lead to job displacement, which may further contribute to the labor shortage issue.
As robots become more capable of performing complex tasks, there is a growing fear that human workers might be pushed out of their jobs.
This fear, combined with a lack of skills needed to work alongside advanced technology, can create a reluctance among the workforce to pursue careers in manufacturing.
Strategies to Address Labor Shortages in the Manufacturing Sector
To combat labor shortages and harness the benefits of robotization effectively, several strategies can be implemented in the manufacturing industry.
1. Emphasizing Workforce Training and Development
One of the key measures to address the impact of robotization is investing in workforce training and development.
By providing current employees with opportunities to upskill and reskill, companies can ensure their workforce can work effectively alongside robots.
Training programs focused on robotics, automation systems, and advanced manufacturing techniques can help workers adapt to the changing landscape of the industry.
Organizations should collaborate with educational institutions and industry associations to create specialized training programs that align with the needs of the modern manufacturing environment.
Mentorship programs and apprenticeships can provide practical experience and boost employee confidence in dealing with technology.
2. Fostering Innovation and Collaboration
Innovation and collaboration are essential for creating a resilient manufacturing workforce.
Companies should encourage innovation by creating a culture that embraces change and rewards creativity.
This can result in new solutions for integrating humans and robots, allowing for seamless collaboration.
Manufacturers can also collaborate with tech companies, research institutions, and other industry players to develop advanced robotic systems that focus on complementing human workers, rather than replacing them.
By participating in collaborative projects, manufacturers can ensure that technological advancements are designed with the workforce in mind.
3. Redefining Job Roles and Responsibilities
The introduction of robots in manufacturing calls for a reevaluation of job roles and responsibilities.
Companies need to rethink traditional job descriptions and create new roles that focus on monitoring, maintaining, and programming robotic systems.
By assigning employees to roles where they can leverage their critical thinking and problem-solving skills, organizations can make the most of both their human and robotic resources.
Redefining roles also involves creating pathways for career development.
Manufacturers should offer clear career progression opportunities for employees willing to adapt and grow alongside technology.
This can help attract new talent and retain existing employees.
4. Promoting STEM Education and Awareness
To combat labor shortages effectively, it is crucial to address the root cause: the dwindling interest in manufacturing careers among younger generations.
By promoting STEM (science, technology, engineering, and mathematics) education, companies can inspire students to pursue careers in the manufacturing industry.
Manufacturers can partner with schools and universities to provide practical experiences, such as workshops, internships, and factory visits, to give students a real-world understanding of what manufacturing entails.
By highlighting the potential for innovation and technology integration, companies can paint a more appealing picture of the industry for the future workforce.
Implementing Sustainable Practices with Robots
In addition to addressing labor shortages, companies should focus on implementing sustainable practices with robotization.
Sustainability is increasingly becoming a priority for consumers, and adopting eco-friendly practices can enhance a company’s reputation.
1. Enhancing Energy Efficiency
Robots can be integrated into manufacturing processes in ways that enhance energy efficiency.
By optimizing robotic systems to use minimal energy without compromising performance, manufacturers can reduce their overall energy consumption and carbon footprint.
Smart sensors and data analytics can be used to monitor energy use and identify areas for improvement.
Adjusting production schedules and using energy-efficient robots can lead to significant savings in energy costs while promoting sustainability.
2. Reducing Waste and Resource Consumption
Advanced robots can be programmed to minimize waste and resource consumption in production processes.
By optimizing material use and ensuring precision in manufacturing, companies can reduce excess waste, saving costs and contributing to environmental conservation.
Robots can also be employed in recycling operations, helping with the sorting and processing of materials for reuse.
This contributes to a circular economy, where resources are efficiently managed and repurposed.
Conclusion
The manufacturing industry is at a crossroads where technological advancements and labor challenges coexist.
Through strategic planning and the implementation of innovative practices, companies can address labor shortages and leverage robotization to their advantage.
By focusing on workforce training, redefined roles, and fostering collaboration between humans and robots, the manufacturing sector can achieve sustained growth and productivity.
Moreover, by promoting sustainable practices, manufacturers can ensure they are not only competitive but also responsible global citizens.
These measures can create a manufacturing environment that is both technologically advanced and human-centric, providing solutions to the current challenges while securing a prosperous future for the industry.
資料ダウンロード
QCD調達購買管理クラウド「newji」は、調達購買部門で必要なQCD管理全てを備えた、現場特化型兼クラウド型の今世紀最高の購買管理システムとなります。
ユーザー登録
調達購買業務の効率化だけでなく、システムを導入することで、コスト削減や製品・資材のステータス可視化のほか、属人化していた購買情報の共有化による内部不正防止や統制にも役立ちます。
NEWJI DX
製造業に特化したデジタルトランスフォーメーション(DX)の実現を目指す請負開発型のコンサルティングサービスです。AI、iPaaS、および先端の技術を駆使して、製造プロセスの効率化、業務効率化、チームワーク強化、コスト削減、品質向上を実現します。このサービスは、製造業の課題を深く理解し、それに対する最適なデジタルソリューションを提供することで、企業が持続的な成長とイノベーションを達成できるようサポートします。
オンライン講座
製造業、主に購買・調達部門にお勤めの方々に向けた情報を配信しております。
新任の方やベテランの方、管理職を対象とした幅広いコンテンツをご用意しております。
お問い合わせ
コストダウンが利益に直結する術だと理解していても、なかなか前に進めることができない状況。そんな時は、newjiのコストダウン自動化機能で大きく利益貢献しよう!
(Β版非公開)