- お役立ち記事
- Specific measures to reduce defects and improve yield during prototyping
月間76,176名の
製造業ご担当者様が閲覧しています*
*2025年3月31日現在のGoogle Analyticsのデータより
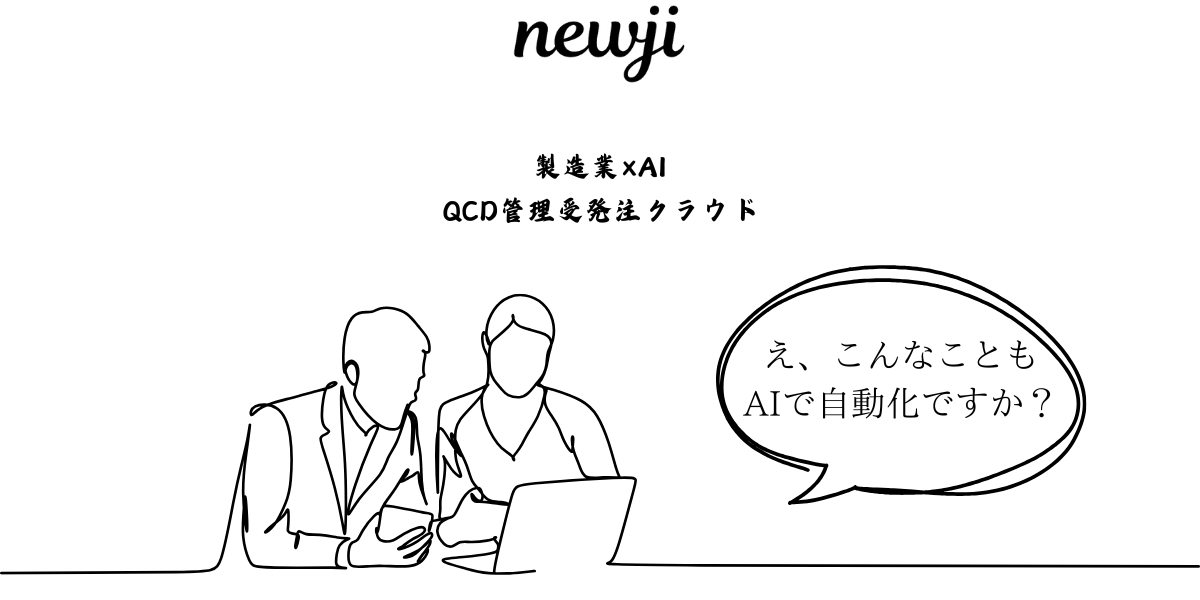
Specific measures to reduce defects and improve yield during prototyping
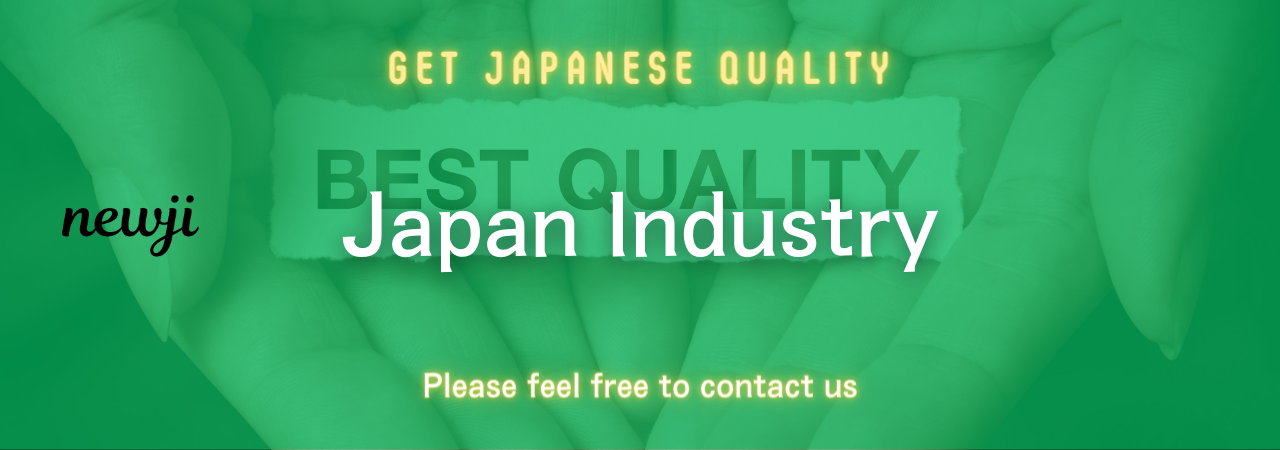
目次
Understanding the Importance of Reducing Defects
Defects in prototyping can lead to significant costs and delays, which is why it’s crucial to implement specific measures to minimize them.
During the prototyping phase, identifying and addressing issues early can prevent larger problems down the road.
This proactive approach not only reduces defects but also improves the overall yield of production.
Early Design Reviews
One effective measure to reduce defects is by conducting early design reviews.
Bringing engineers and designers together at the initial stages allows for identification of potential issues.
This collaborative approach enables teams to make necessary adjustments before production begins.
Implementing Quality Control Processes
Quality control processes are essential for catching defects before they progress too far.
Setting up checkpoints throughout the prototyping process ensures that any issues can be addressed promptly.
These processes include inspections, testing, and reviews, which help maintain high standards.
Utilizing Simulation Software
Simulation software can be a game-changer in reducing defects.
By testing designs in a virtual environment, teams can foresee potential problems and make corrections.
This not only saves time but also resources, as issues can be fixed before they manifest in physical prototypes.
Creating a Feedback Loop
A feedback loop between the design team and the manufacturing team is integral to improving yields.
Constant communication ensures that any observed defects can be relayed back to the designers for improvement.
This iterative process helps in refining future prototypes, minimizing errors, and enhancing efficiency.
Improving Yield Through Better Material Selection
Material selection plays a crucial role in both the performance and reliability of prototypes.
Choosing the right materials can prevent many defects related to durability and functionality.
Conducting Material Testing
Thorough testing of materials before use is necessary to ensure they meet the project’s requirements.
This process helps in selecting materials that are best suited for the prototype, thereby reducing the chances of defects.
Supplier Collaboration
Working closely with suppliers can greatly improve the quality of materials received.
Building strong relationships with suppliers can lead to better material recommendations and access to high-quality resources.
This collaboration is vital in maintaining consistent material quality, ultimately leading to improved yield.
Enhancing Yield with Advanced Manufacturing Techniques
Adopting advanced manufacturing techniques can significantly boost yield during prototyping.
3D Printing
3D printing technology offers the flexibility needed for rapid prototyping.
It allows for precise creation of complex geometries and quick modifications, reducing the time and defects associated with traditional manufacturing.
Automation and Robotics
Incorporating automation and robotics into the prototyping process can reduce human error.
These technologies ensure consistent production quality and precision, leading to fewer defects and higher yields.
Continuous Monitoring and Adjustment
Implementing systems for continuous monitoring throughout production can help identify defects early in the process.
This approach allows for immediate adjustments, which can significantly reduce the incidence of defects.
Investment in Training and Development
Investing in training and development of staff is essential for reducing defects and improving yields.
Knowledgeable and skilled workers are key to identifying and addressing potential issues effectively.
Regular Training Sessions
Regular training sessions keep the workforce updated on the latest techniques and technologies in prototyping.
This ongoing education helps workers enhance their skills and stay ahead of potential issues.
Encouraging Innovation
Creating an organizational culture that encourages innovation can lead to new ideas for reducing defects.
Empowering employees to suggest improvements and experiment with new approaches can have a positive impact on yield and quality.
Developing a Problem-Solving Culture
Fostering a problem-solving culture within the organization encourages employees to proactively address defects.
When everyone is involved in identifying and solving issues, it leads to a more efficient and high-quality prototyping process.
Conclusion
Reducing defects and improving yields during prototyping are critical to the success of any manufacturing process.
By implementing strategic measures such as early design reviews, quality control processes, and advanced manufacturing techniques, organizations can enhance their prototyping efforts.
Additionally, investing in training and fostering a culture of innovation and problem-solving are pivotal in achieving higher yields.
Through these actions, companies can ensure a smoother transition from prototype to production, saving time, resources, and reducing costs.
資料ダウンロード
QCD管理受発注クラウド「newji」は、受発注部門で必要なQCD管理全てを備えた、現場特化型兼クラウド型の今世紀最高の受発注管理システムとなります。
ユーザー登録
受発注業務の効率化だけでなく、システムを導入することで、コスト削減や製品・資材のステータス可視化のほか、属人化していた受発注情報の共有化による内部不正防止や統制にも役立ちます。
NEWJI DX
製造業に特化したデジタルトランスフォーメーション(DX)の実現を目指す請負開発型のコンサルティングサービスです。AI、iPaaS、および先端の技術を駆使して、製造プロセスの効率化、業務効率化、チームワーク強化、コスト削減、品質向上を実現します。このサービスは、製造業の課題を深く理解し、それに対する最適なデジタルソリューションを提供することで、企業が持続的な成長とイノベーションを達成できるようサポートします。
製造業ニュース解説
製造業、主に購買・調達部門にお勤めの方々に向けた情報を配信しております。
新任の方やベテランの方、管理職を対象とした幅広いコンテンツをご用意しております。
お問い合わせ
コストダウンが利益に直結する術だと理解していても、なかなか前に進めることができない状況。そんな時は、newjiのコストダウン自動化機能で大きく利益貢献しよう!
(β版非公開)