- お役立ち記事
- Specific methods and success stories of production line robotization
月間76,176名の
製造業ご担当者様が閲覧しています*
*2025年3月31日現在のGoogle Analyticsのデータより
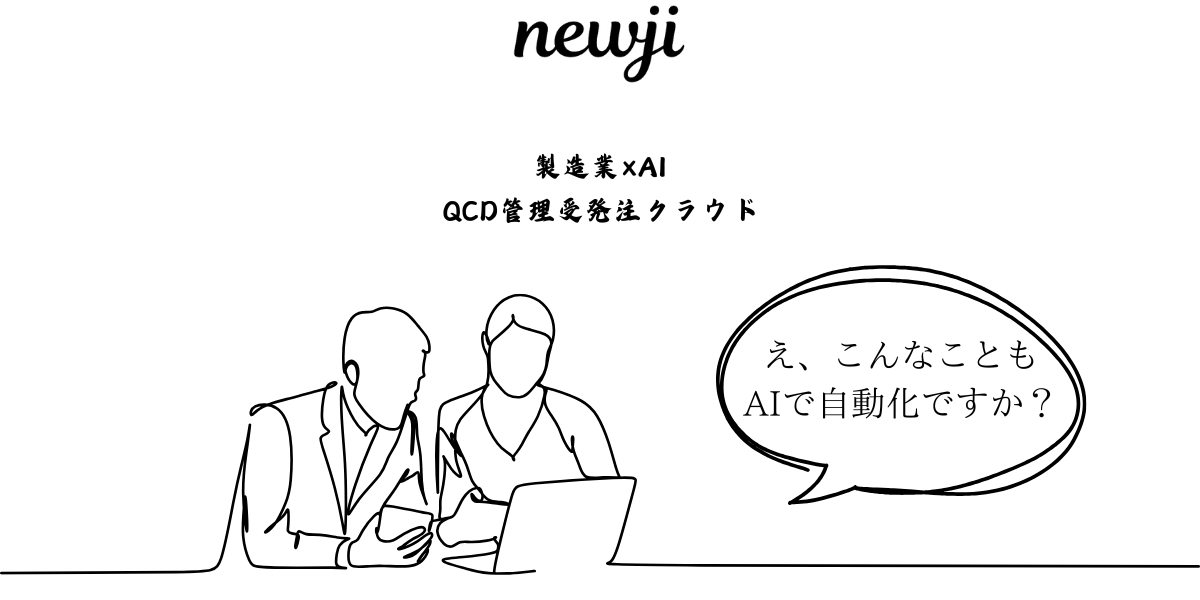
Specific methods and success stories of production line robotization
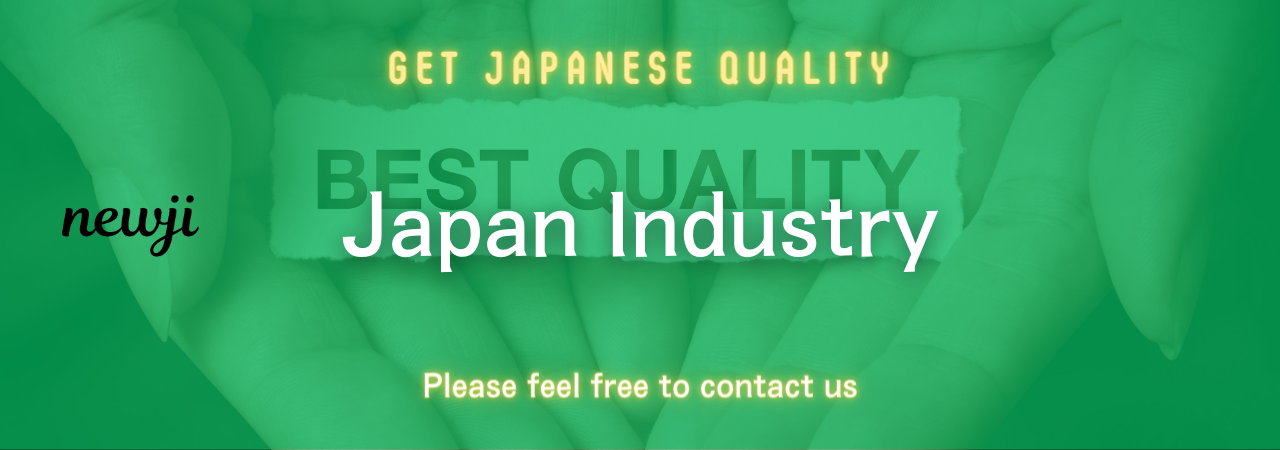
目次
Understanding Production Line Robotization
In today’s rapidly evolving industrial landscape, production line robotization is gaining significant attention.
Robotization refers to the integration of robotic systems into manufacturing processes to automate tasks that were traditionally performed by human workers.
This transformation not only enhances productivity but also boosts efficiency and precision.
As industries strive for optimization, understanding the specific methods and success stories of production line robotization becomes essential.
The Benefits of Robotization in Production Lines
One of the most compelling advantages of incorporating robots in production lines is the increase in productivity.
Robots can work tirelessly around the clock without fatigue, ensuring that manufacturing processes are continuous and efficient.
This is particularly beneficial in environments that demand high volumes of output, where a human workforce may struggle to meet the demand.
Additionally, robotization significantly enhances precision and accuracy in tasks.
Robots are programmed to perform specific actions repeatedly without deviation, reducing the likelihood of human error.
This degree of precision is crucial in industries such as electronics and automotive manufacturing, where even minute discrepancies can lead to significant challenges down the line.
Another profound benefit is the improvement in workplace safety.
By assigning hazardous or physically demanding tasks to robots, companies can safeguard their employees from potential injuries.
This not only protects the workforce but also reduces costs associated with workplace accidents and downtime.
Methods for Implementing Robotization
Robotization involves various specific methods, each tailored to the unique needs of a production line.
Understanding these methods can pave the way for successful integration of robotics into your manufacturing processes.
Task Identification and Analysis
The initial step in robotizing a production line is identifying tasks that can be automated.
This requires a comprehensive analysis of the production process to pinpoint repetitive, high-precision, or hazardous tasks that are ideal candidates for automation.
By evaluating current workflows, manufacturers can make informed decisions on where to deploy robotic systems for maximum impact.
Selection of Appropriate Robotic Technology
Once tasks are identified, the next phase involves selecting the appropriate robotic technology.
Different types of robots serve diverse functions: articulated robots, cartesian robots, and collaborative robots are just a few examples.
Collaborative robots, also known as cobots, are designed to work alongside human workers, enhancing productivity without replacing jobs.
Choosing the right type of robot is crucial to align with the specific requirements of the production line.
Robust Programming and Testing
After selecting the appropriate robots, programming is essential to ensure efficient operation.
Robots must be programmed to perform the identified tasks seamlessly, taking into account variables such as speed, accuracy, and environmental conditions.
Thorough testing is a critical step to verify that the robots function as intended, without causing disruptions to existing workflows.
Integration with Existing Systems
Successful robotization also requires the seamless integration of robotic systems with existing production infrastructure.
This process involves modifying current processes and equipment to accommodate robots while ensuring compatibility with software and control systems.
Well-executed integration ensures that robots complement human efforts and enhance the overall productivity of the production line.
Success Stories of Production Line Robotization
Numerous success stories demonstrate the transformative impact of robotization on manufacturing processes.
These stories offer valuable insights and inspiration for those considering the journey towards automation.
Case Study: Automotive Industry
In the automotive industry, robots have revolutionized assembly lines.
For instance, a leading car manufacturer integrated robots into their production process to handle tasks such as welding, painting, and assembly.
This move not only increased production speed but also improved the quality of the final product by maintaining consistent precision.
Moreover, the company’s workforce benefited from the reduction of physically demanding tasks, allowing workers to focus on more complex and value-added activities.
As a result, the manufacturer not only achieved higher output but also raised the level of employee satisfaction.
Case Study: Electronics Manufacturing
Electronics manufacturing is another sector that has experienced significant benefits from robotization.
A prominent electronics company implemented robots to handle delicate tasks such as component placement and soldering.
These robots ensured precision and consistency, critical for the reliable functioning of electronic devices.
The company reported a significant reduction in defects and an increase in production efficiency.
This success story underscores the importance of robotization for maintaining competitiveness in technology-driven industries.
Case Study: Food and Beverage Sector
In the food and beverage industry, robotization has optimized packaging and handling processes.
For example, a major beverage company deployed robots to automate the packaging of bottled products.
The robots’ ability to operate continuously resulted in faster turnaround times and minimized human intervention, reducing the risk of contamination.
This successful implementation not only increased operational efficiency but also ensured compliance with stringent hygiene standards, fundamental for food and beverage production.
The Future of Robotization in Manufacturing
As we look to the future, production line robotization will continue to evolve and expand across industries.
With advancements in artificial intelligence and machine learning, robots are becoming increasingly intelligent and capable of handling more complex tasks with greater autonomy.
Moreover, the development of collaborative robots that can work alongside humans opens up new possibilities for efficient and safe production environments.
These cobots allow human workers to leverage robotic assistance, resulting in a harmonious blend of human creativity and machine precision.
Ultimately, embracing robotization is key to staying competitive in an ever-changing global market.
By understanding specific methods and learning from success stories, manufacturers can unlock the full potential of robotic technology, driving innovation and success in their production lines.
資料ダウンロード
QCD管理受発注クラウド「newji」は、受発注部門で必要なQCD管理全てを備えた、現場特化型兼クラウド型の今世紀最高の受発注管理システムとなります。
ユーザー登録
受発注業務の効率化だけでなく、システムを導入することで、コスト削減や製品・資材のステータス可視化のほか、属人化していた受発注情報の共有化による内部不正防止や統制にも役立ちます。
NEWJI DX
製造業に特化したデジタルトランスフォーメーション(DX)の実現を目指す請負開発型のコンサルティングサービスです。AI、iPaaS、および先端の技術を駆使して、製造プロセスの効率化、業務効率化、チームワーク強化、コスト削減、品質向上を実現します。このサービスは、製造業の課題を深く理解し、それに対する最適なデジタルソリューションを提供することで、企業が持続的な成長とイノベーションを達成できるようサポートします。
製造業ニュース解説
製造業、主に購買・調達部門にお勤めの方々に向けた情報を配信しております。
新任の方やベテランの方、管理職を対象とした幅広いコンテンツをご用意しております。
お問い合わせ
コストダウンが利益に直結する術だと理解していても、なかなか前に進めることができない状況。そんな時は、newjiのコストダウン自動化機能で大きく利益貢献しよう!
(β版非公開)