- お役立ち記事
- Speeding up durable prototyping of plastic gears using a hybrid stress analysis system
月間76,176名の
製造業ご担当者様が閲覧しています*
*2025年3月31日現在のGoogle Analyticsのデータより
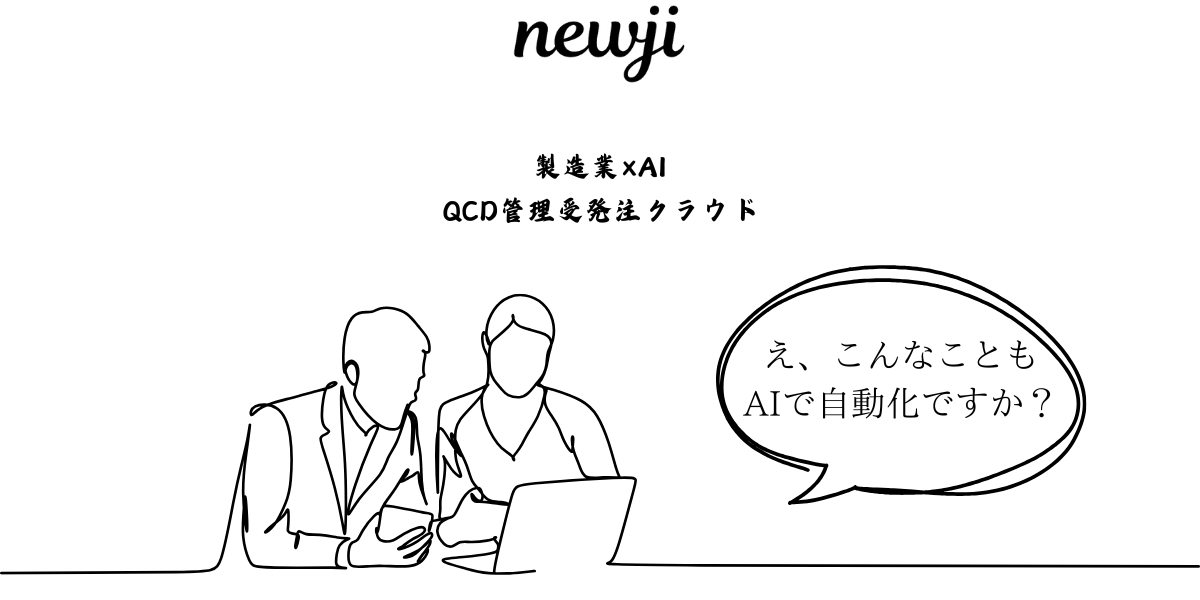
Speeding up durable prototyping of plastic gears using a hybrid stress analysis system
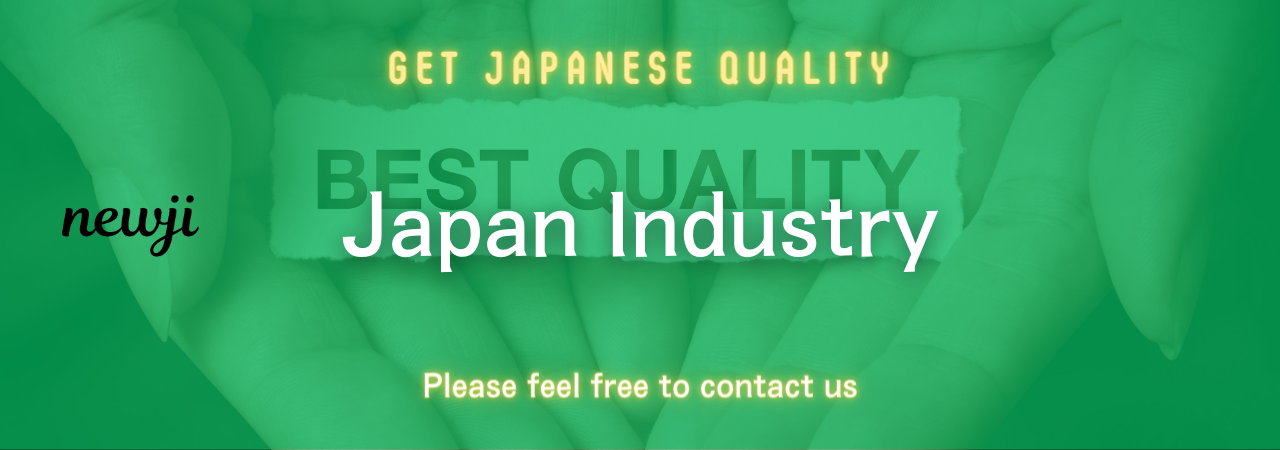
目次
Understanding the Basics of Plastic Gears
Plastic gears are an essential component in many mechanical systems, offering advantages such as cost-effectiveness, lightweight, and corrosion resistance.
These attributes make them suitable for a variety of applications, from simple household appliances to sophisticated automotive systems.
Unlike metal gears, plastic gears are often quieter and can absorb shock and vibration better.
Their versatility can greatly enhance the dynamic performance of a drive system.
The Importance of Stress Analysis in Gear Design
Stress analysis is a critical aspect of gear design, especially for plastic gears.
It involves assessing how the gear material will respond to different forces and conditions during operation.
A comprehensive stress analysis can ensure the gear operates efficiently and can validate that it can withstand its intended application without premature failure.
The process involves calculating stress distribution within the gear, identifying potential points of failure, and suggesting design modifications to mitigate those risks.
Challenges in Prototyping Plastic Gears
Developing new designs of plastic gears traditionally encounters several hurdles.
The primary challenge lies in the inability to rapidly test and tweak designs because of the time-consuming fabrication processes.
Traditional prototyping methods can be slow and costly, especially when iterative testing is needed to refine the gear’s performance and robustness.
Additionally, unwanted delays can stem from the intricacy of modeling the behavior of plastic materials accurately.
Stress distribution and material deformations under load require sophisticated analysis to predict accurately.
Introducing the Hybrid Stress Analysis System
The hybrid stress analysis system is a groundbreaking innovation designed to address the prototyping challenges of plastic gears.
It merges computational tools with experimental methods to rapidly evaluate and enhance plastic gear designs.
The system integrates advanced software simulations with real-world testing data, providing a comprehensive overview of gear performance.
By combining these two approaches, engineers can gain insights that were previously unattainable, allowing for faster design iterations and more robust product outcomes.
Benefits of the Hybrid System
The hybrid approach provides multiple benefits, including enhanced precision in stress prediction and a reduction in the prototyping cycle time.
The incorporation of both simulated and experimental data into the analysis means that potential defects can be identified and addressed much earlier in the design process.
This dual approach ensures a more reliable prediction of gear behavior under different operational conditions, leading to improvements in gear longevity and efficiency.
Steps Involved in Hybrid Stress Analysis
The process begins with computer-aided design (CAD) models that simulate the gear’s geometry and application environment.
These models employ finite element analysis (FEA) techniques to predict stress distribution across the gear tooth and body.
Once the simulation reaches a satisfactory level, prototyping and testing using physical models commence.
The physical models undergo rigorous testing to gather stress data which is then fed back into the simulation.
This iterative process refines the design simulations, making predictions more accurate and reliable.
Real-World Applications
The hybrid stress analysis system finds its application across numerous industries.
For instance, in the automotive industry, ensuring that plastic gears in transmission systems can withstand high-stress conditions while delivering smooth operation is paramount.
Consumer electronics also benefit significantly, as the need for compact, reliable, and cost-effective gearing solutions increases.
The hybrid system helps tailor gears to unique operating conditions, ensuring that performance is not compromised as technological advancements push devices to more extreme usage scenarios.
The Future of Gear Prototyping
As industries continue to evolve, the demand for high-performance, reliable, and cost-effective gears is set to surge.
The hybrid stress analysis system stands as a transformative tool in this landscape.
By accelerating the prototyping phase and improving gear quality, the system not only fosters innovation but also drastically reduces time to market.
This progression symbolizes a shift towards more adaptive and flexible design processes, tailored to meet the demands of rapid technological development.
Conclusion
The hybrid stress analysis system signifies a leap forward in the field of plastic gear prototyping.
With its proven ability to reduce development time and enhance design accuracy, it paves the way for more efficient, reliable, and sustainable mechanical systems.
As industries increasingly adopt this technology, it holds the promise of revolutionizing how engineers approach gear design, ultimately leading to a future where mechanical components are optimized for their roles like never before.
Through continued innovation, this system not only addresses current challenges but also contributes to creating the gears of tomorrow.
資料ダウンロード
QCD管理受発注クラウド「newji」は、受発注部門で必要なQCD管理全てを備えた、現場特化型兼クラウド型の今世紀最高の受発注管理システムとなります。
ユーザー登録
受発注業務の効率化だけでなく、システムを導入することで、コスト削減や製品・資材のステータス可視化のほか、属人化していた受発注情報の共有化による内部不正防止や統制にも役立ちます。
NEWJI DX
製造業に特化したデジタルトランスフォーメーション(DX)の実現を目指す請負開発型のコンサルティングサービスです。AI、iPaaS、および先端の技術を駆使して、製造プロセスの効率化、業務効率化、チームワーク強化、コスト削減、品質向上を実現します。このサービスは、製造業の課題を深く理解し、それに対する最適なデジタルソリューションを提供することで、企業が持続的な成長とイノベーションを達成できるようサポートします。
製造業ニュース解説
製造業、主に購買・調達部門にお勤めの方々に向けた情報を配信しております。
新任の方やベテランの方、管理職を対象とした幅広いコンテンツをご用意しております。
お問い合わせ
コストダウンが利益に直結する術だと理解していても、なかなか前に進めることができない状況。そんな時は、newjiのコストダウン自動化機能で大きく利益貢献しよう!
(β版非公開)