- お役立ち記事
- Spindle Precision Management Techniques in General Machinery
Spindle Precision Management Techniques in General Machinery
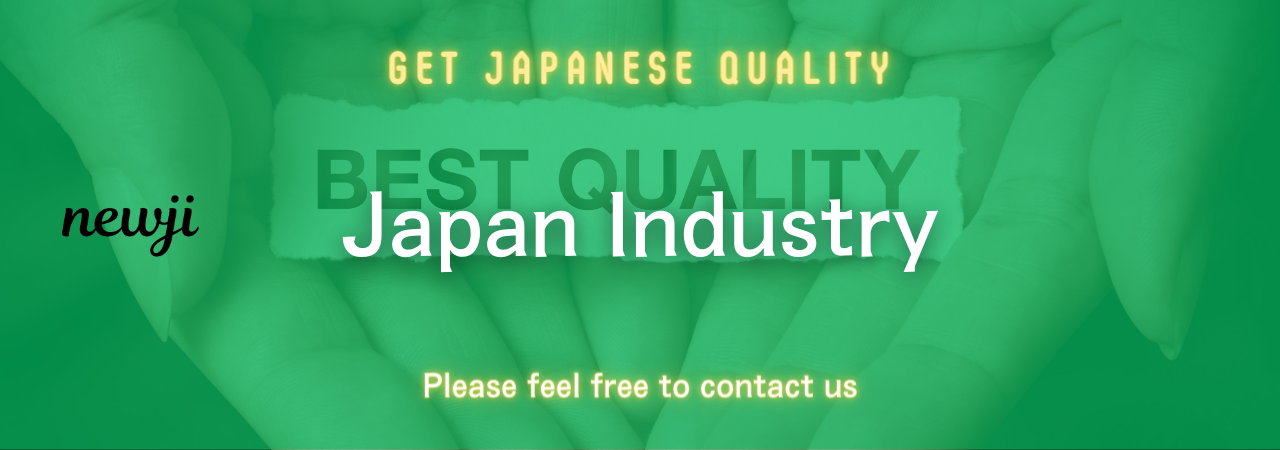
目次
Understanding the Importance of Spindle Precision in General Machinery
In the world of general machinery, spindle precision plays a critical role in ensuring the quality and efficiency of operations.
Spindles are essentially the heart of machines such as CNC machines, lathes, and milling machines.
They are responsible for rotating parts with high accuracy and high speed, which is vital for many machining processes.
Precision in spindle management is important because it affects the overall performance of the machinery.
Any deviation or error in their movement can lead to poor quality parts, increased wear and tear, and even machine breakdowns.
Therefore, understanding spindle precision and how to manage it effectively is crucial for anyone involved in manufacturing and machining processes.
Key Factors Influencing Spindle Precision
To manage spindle precision effectively, it is essential to understand the various factors that can affect it.
These factors include the design and quality of the spindle, the type of bearings used, and the lubrication systems in place.
Additionally, environmental factors such as temperature and humidity can also have an impact on spindle precision.
Regular maintenance and monitoring are necessary to ensure these factors do not negatively affect spindle performance.
Design and Quality
The design and quality of the spindle are foundational to its precision.
High-quality spindles are designed with tight tolerances and durable materials to handle the strains of machining processes.
Selecting the right spindle based on the specific requirements of the machine and operation is critical.
Bearings
Bearings are a crucial component of spindles that help ensure smooth rotation.
They support high loads and must be of high quality to maintain precision.
Choosing the correct type of bearing, whether it be ball bearings, roller bearings, or others, depends on the specific needs of the spindle and the application.
Lubrication Systems
Proper lubrication reduces friction and wear on the spindle components, enhancing precision and extending the life of the spindle.
Lubrication systems must be well-maintained to ensure they provide consistent performance.
Using the right type of lubricant can make a significant difference in spindle precision and longevity.
Techniques for Managing Spindle Precision
There are several techniques and practices that can help manage spindle precision effectively.
These techniques focus on regular maintenance, monitoring equipment, and adopting proper operational practices.
Regular Maintenance
Routine maintenance is key to maintaining spindle precision.
This includes checking and replacing bearings as needed, ensuring proper alignment, and conducting regular inspections.
A well-defined maintenance schedule can reduce the likelihood of unexpected failures and prolong the lifespan of the spindle.
Monitoring Equipment
Using advanced monitoring equipment can provide real-time data on the spindle’s performance, allowing for early detection of potential issues.
Vibration analysis, thermal imaging, and other monitoring tools can help identify problems before they lead to significant downtime.
Proper Operational Practices
Operators should be trained in the best practices for using machinery, adhering to recommended speed and feed rates, and avoiding overloading the spindle.
Properly setting up and calibrating machining tasks can prevent unnecessary stress on the spindle.
The Impact of Spindle Precision on Production Quality
Spindle precision directly influences the quality of products manufactured by machinery.
When spindles operate with high precision, they produce parts that meet the exact design specifications, resulting in consistent quality and reducing the need for rework.
Additionally, precision management can lead to increased production efficiency.
Machines that operate optimally spend less time in production and experience fewer downtimes due to breakdowns.
This efficiency leads to higher output and cost savings for manufacturers.
Conclusion
In conclusion, spindle precision is a critical aspect of general machinery management.
By understanding and addressing the factors that influence spindle precision, implementing effective management techniques, and prioritizing regular maintenance, manufacturers can enhance their production processes.
This not only results in better-quality products but also optimizes the operational efficiency of the machinery.
Ultimately, a focus on spindle precision translates to improved productivity and profitability in manufacturing operations.
資料ダウンロード
QCD調達購買管理クラウド「newji」は、調達購買部門で必要なQCD管理全てを備えた、現場特化型兼クラウド型の今世紀最高の購買管理システムとなります。
ユーザー登録
調達購買業務の効率化だけでなく、システムを導入することで、コスト削減や製品・資材のステータス可視化のほか、属人化していた購買情報の共有化による内部不正防止や統制にも役立ちます。
NEWJI DX
製造業に特化したデジタルトランスフォーメーション(DX)の実現を目指す請負開発型のコンサルティングサービスです。AI、iPaaS、および先端の技術を駆使して、製造プロセスの効率化、業務効率化、チームワーク強化、コスト削減、品質向上を実現します。このサービスは、製造業の課題を深く理解し、それに対する最適なデジタルソリューションを提供することで、企業が持続的な成長とイノベーションを達成できるようサポートします。
オンライン講座
製造業、主に購買・調達部門にお勤めの方々に向けた情報を配信しております。
新任の方やベテランの方、管理職を対象とした幅広いコンテンツをご用意しております。
お問い合わせ
コストダウンが利益に直結する術だと理解していても、なかなか前に進めることができない状況。そんな時は、newjiのコストダウン自動化機能で大きく利益貢献しよう!
(Β版非公開)