- お役立ち記事
- Spindle Precision Testing and Evaluation Standards in Machine Tools
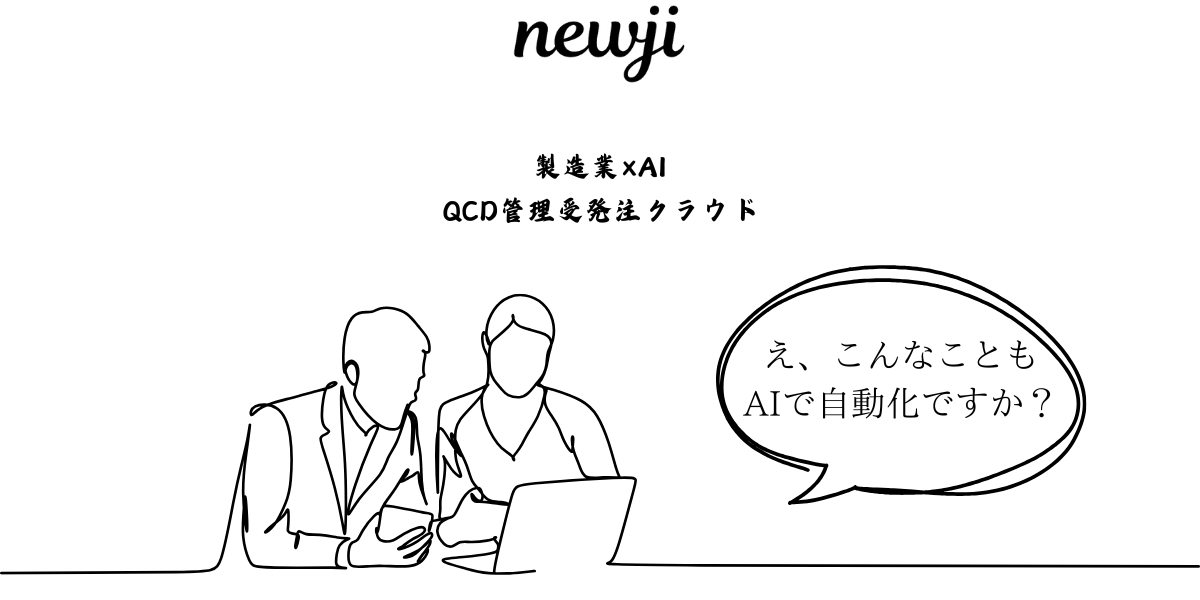
Spindle Precision Testing and Evaluation Standards in Machine Tools
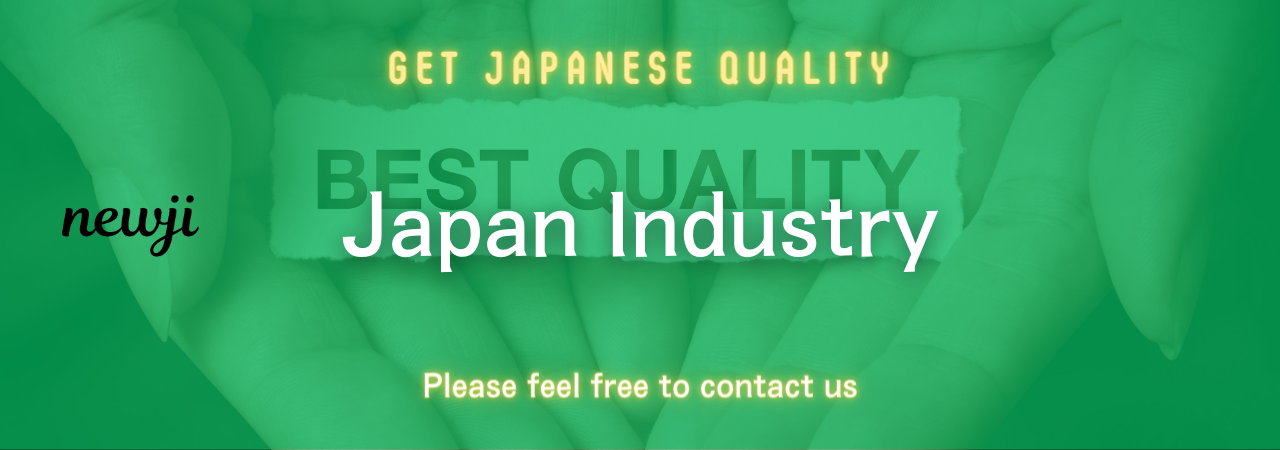
目次
Introduction to Spindles in Machine Tools
Spindles play a crucial role in the operation of machine tools, serving as the rotational axis for cutting, drilling, and similar processes.
They ensure that the tools function with consistency and precision.
Evaluating the precision and performance of spindles is essential to maintain machine efficiency, reduce downtime, and produce high-quality products.
In this article, we will discuss spindle precision testing and the standards used to evaluate their effectiveness.
What is Spindle Precision?
Spindle precision refers to the accuracy and reliability with which a spindle performs its functions in a machine tool.
This includes its ability to maintain a certain level of accuracy when rotating at various speeds and under different loads.
High precision means the spindle contributes to achieving tight tolerances, resulting in parts that meet exact specifications.
Precision is vital in industries such as aerospace, automotive, and manufacturing, where parts must meet stringent standards.
Testing Methods for Spindle Precision
There are several methods used to test the precision of spindles in machine tools.
Each method provides critical data that can be used to assess performance and identify areas for improvement.
Runout Measurement
Runout is the measure of how much a spindle deviates from its axis when rotating.
A high amount of runout can result in inaccuracies during the machining process, leading to defects in the final product.
To measure runout, a dial indicator is often placed near the spindle’s end, and the deviation is checked while the spindle is in motion.
Vibration Analysis
Vibration can significantly impact spindle performance and can lead to premature wear and tear.
Vibration analysis involves the use of sensors to measure the levels of vibration during machine operation.
By assessing vibrations, engineers can identify imbalances or misalignments that could affect the spindle’s long-term performance.
Thermal Analysis
The temperature at which a spindle operates is crucial for precision.
Excessive heat can expand materials and lead to misalignment or warping.
Thermal analysis involves monitoring the temperature gradients across the spindle during operation to ensure optimal performance.
Anomalies might indicate the need for better cooling or lubrication systems.
Load Testing
Spindles are subjected to various loads during machining processes.
Testing the spindle under different loads helps understand its ability to maintain accuracy and reliability.
Load testing simulates real-world conditions to ensure the spindle can handle the stress without compromising performance.
Standards for Spindle Evaluation
To ensure consistency and reliability in spindle performance evaluation, industry standards have been established.
These standards provide guidelines and criteria for precision testing.
ISO Standards
The International Organization for Standardization (ISO) has developed several standards related to spindle performance.
ISO 1940 and ISO 10816 are commonly referenced for balancing and vibration standards.
Compliance with these standards ensures that machine tools meet international quality benchmarks.
ANSI/ASME Standards
The American National Standards Institute (ANSI) and the American Society of Mechanical Engineers (ASME) offer guidelines for spindle testing, focusing on engineering practices and safety.
These standards are widely adopted in the United States and North America.
Manufacturer Standards
Additionally, some manufacturers of machine tools have developed their own specific standards and protocols for testing spindle precision.
These standards are often more stringent to ensure their machines perform optimally in specific applications.
The Importance of Regular Testing and Evaluation
Regular testing and evaluation of spindle precision have numerous benefits.
They help maintain machine efficiency, reduce operational costs, and extend the lifecycle of the equipment.
Moreover, routine checks can preemptively identify issues, preventing costly repairs and downtime.
In industries where precision is paramount, such as aerospace or medical device manufacturing, regular testing is not just beneficial but necessary to comply with regulatory requirements and maintain product quality.
Advancements in Spindle Technology
Technology advancements have significantly improved spindle precision testing.
The use of digital sensors and computer-aided testing methods has allowed for more accurate and comprehensive evaluations.
Furthermore, developments in materials technology have led to spindles that are more resistant to wear, reducing the need for constant calibration and adjustment.
These innovations contribute to a more efficient manufacturing process with fewer errors and higher-quality output.
Conclusion
Spindle precision testing and evaluation using established standards is critical for the efficient operation of machine tools.
Through various testing methods such as runout measurement, vibration analysis, thermal analysis, and load testing, businesses can ensure their equipment operates at peak performance.
Adherence to ISO, ANSI/ASME, or manufacturer-defined standards guarantees consistency and quality.
As technology continues to evolve, the precision and efficiency of spindles and their testing methods will further improve, benefiting industries reliant on high-quality machining practices.
資料ダウンロード
QCD調達購買管理クラウド「newji」は、調達購買部門で必要なQCD管理全てを備えた、現場特化型兼クラウド型の今世紀最高の購買管理システムとなります。
ユーザー登録
調達購買業務の効率化だけでなく、システムを導入することで、コスト削減や製品・資材のステータス可視化のほか、属人化していた購買情報の共有化による内部不正防止や統制にも役立ちます。
NEWJI DX
製造業に特化したデジタルトランスフォーメーション(DX)の実現を目指す請負開発型のコンサルティングサービスです。AI、iPaaS、および先端の技術を駆使して、製造プロセスの効率化、業務効率化、チームワーク強化、コスト削減、品質向上を実現します。このサービスは、製造業の課題を深く理解し、それに対する最適なデジタルソリューションを提供することで、企業が持続的な成長とイノベーションを達成できるようサポートします。
オンライン講座
製造業、主に購買・調達部門にお勤めの方々に向けた情報を配信しております。
新任の方やベテランの方、管理職を対象とした幅広いコンテンツをご用意しております。
お問い合わせ
コストダウンが利益に直結する術だと理解していても、なかなか前に進めることができない状況。そんな時は、newjiのコストダウン自動化機能で大きく利益貢献しよう!
(Β版非公開)