- お役立ち記事
- Standard framework for purchasing departments to audit supplier quality assurance systems
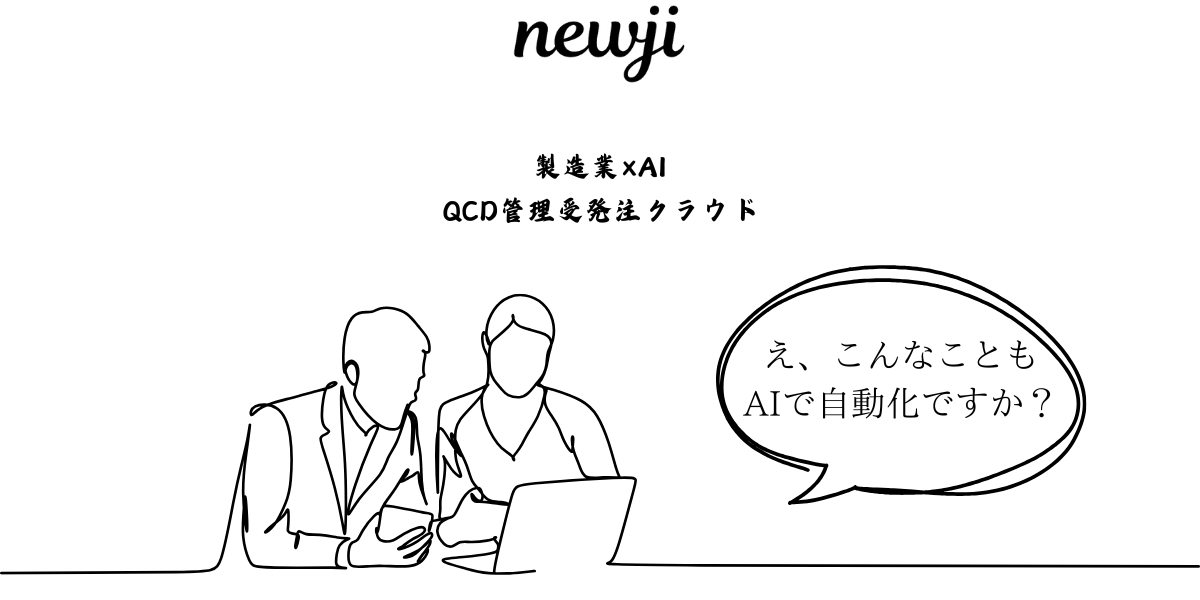
Standard framework for purchasing departments to audit supplier quality assurance systems
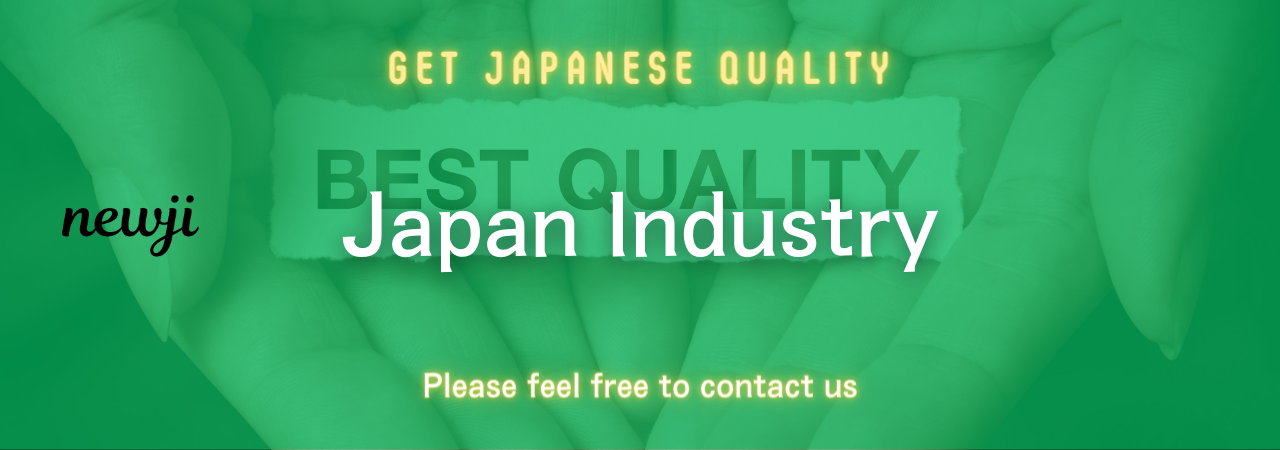
目次
Introduction to Supplier Quality Assurance Systems
Every purchasing department knows the importance of supplier quality assurance systems.
These systems are critical in maintaining the integrity and consistency of products that an organization procures.
This framework serves as a lifeline, ensuring suppliers adhere to quality standards and requirements.
But how does one audit these systems effectively?
This article dives into the standard framework that purchasing departments can use for auditing supplier quality assurance systems, providing insights and practical steps for optimal results.
Understanding the Importance of Quality Assurance
Before delving into the audit process, it’s important to understand the role of quality assurance in the supply chain.
Quality assurance systems ensure that suppliers provide products that meet the agreed-upon specifications and standards.
They help in minimizing defects, reducing waste, and ultimately increasing customer satisfaction.
When suppliers fail to maintain quality, it leads to a domino effect that can adversely impact production timelines, increase costs, and tarnish the organization’s reputation.
Establishing Audit Objectives
The first step in the framework is to establish clear audit objectives.
The purchasing department must identify what they aim to achieve through the audit.
These objectives can vary, from verifying compliance with industry standards to evaluating the effectiveness of the supplier’s quality control processes.
Having clear objectives helps align resources and efforts and provides a roadmap for the audit process.
Preparing for the Audit
Preparation is key to a successful audit.
The purchasing department should gather relevant documents and information about the supplier’s quality management system.
This includes reviewing contracts, previous audit reports, and any corrective actions that were previously taken.
Understanding the supplier’s history with quality assurance will provide valuable context for the upcoming audit.
The department should also assemble an audit team with the right expertise and experience to conduct a thorough assessment.
Developing an Audit Plan
An audit plan is crucial as it outlines the scope, objectives, and methodology of the audit.
The plan should detail the areas to be audited, the criteria for evaluation, and the timeline for the audit.
It should also designate responsibilities to the audit team members.
This structured approach ensures a comprehensive assessment and avoids any oversight.
Conducting the Audit
Once the preparation is complete, it’s time to conduct the audit.
The purchasing department should visit the supplier’s facility to observe the processes in action.
Interviews with the supplier’s personnel can also provide insights into their understanding and execution of quality assurance practices.
It’s important to collect evidence to support the findings, such as process documentation, inspection records, and testing data.
Assessing Compliance and Effectiveness
During the audit, the purchasing department assesses the supplier’s compliance with quality standards and the effectiveness of their quality assurance systems.
This involves checking if the supplier adheres to industry standards like ISO 9001 and whether their processes result in consistent product quality.
Identifying areas of non-compliance or inefficiency is crucial for improving supplier performance.
Reviewing Audit Findings
After completing the audit, the purchasing department reviews the findings.
This involves analyzing the data collected and identifying any deviations from the standards.
It’s critical to distinguish between critical and non-critical issues to prioritize action plans.
The audit team should also discuss the findings with the supplier to address any discrepancies and foster open communication.
Reporting Audit Results
The next step in the framework is to compile a detailed audit report.
This report should document the findings, evidence, and any recommendations for improvement.
Clear and concise reporting is vital as it serves as a reference for both the purchasing department and the supplier.
The report should also outline agreed-upon corrective actions and their timelines.
Implementing Corrective Actions
The supplier must take ownership of the corrective actions to address the audit findings.
The purchasing department should monitor the implementation of these actions and follow up to ensure completion.
This ensures that the supplier addresses the root causes of the issues and prevents recurrence.
Continuous monitoring and communication can foster a strong supplier relationship and drive long-term improvement in quality assurance practices.
Continuous Improvement
Auditing supplier quality assurance systems is not a one-time event.
The purchasing department should adopt a mindset of continuous improvement.
Regular audits and reviews help in maintaining high-quality standards and identifying opportunities for enhancement.
Engaging in continuous improvement practices can lead to a more resilient and reliable supply chain.
Conclusion
A well-structured framework for auditing supplier quality assurance systems is essential for any purchasing department.
It ensures that suppliers deliver products that meet quality expectations and comply with industry standards.
By establishing clear objectives, preparing thoroughly, conducting comprehensive audits, and encouraging implementation of corrective actions, organizations can create a robust auditing process.
This not only elevates the quality of products and services but also strengthens supplier relationships, ultimately contributing to the organization’s overall success.
資料ダウンロード
QCD調達購買管理クラウド「newji」は、調達購買部門で必要なQCD管理全てを備えた、現場特化型兼クラウド型の今世紀最高の購買管理システムとなります。
ユーザー登録
調達購買業務の効率化だけでなく、システムを導入することで、コスト削減や製品・資材のステータス可視化のほか、属人化していた購買情報の共有化による内部不正防止や統制にも役立ちます。
NEWJI DX
製造業に特化したデジタルトランスフォーメーション(DX)の実現を目指す請負開発型のコンサルティングサービスです。AI、iPaaS、および先端の技術を駆使して、製造プロセスの効率化、業務効率化、チームワーク強化、コスト削減、品質向上を実現します。このサービスは、製造業の課題を深く理解し、それに対する最適なデジタルソリューションを提供することで、企業が持続的な成長とイノベーションを達成できるようサポートします。
オンライン講座
製造業、主に購買・調達部門にお勤めの方々に向けた情報を配信しております。
新任の方やベテランの方、管理職を対象とした幅広いコンテンツをご用意しております。
お問い合わせ
コストダウンが利益に直結する術だと理解していても、なかなか前に進めることができない状況。そんな時は、newjiのコストダウン自動化機能で大きく利益貢献しよう!
(Β版非公開)