- お役立ち記事
- Standardization and effective utilization of sensory testing that quality assurance departments should focus on
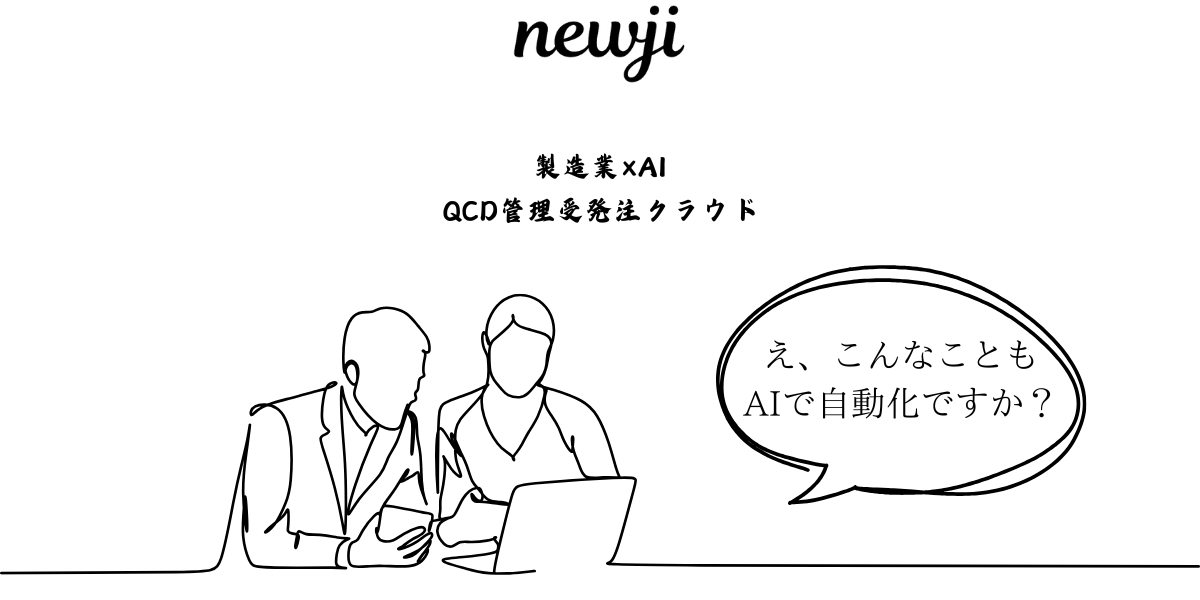
Standardization and effective utilization of sensory testing that quality assurance departments should focus on
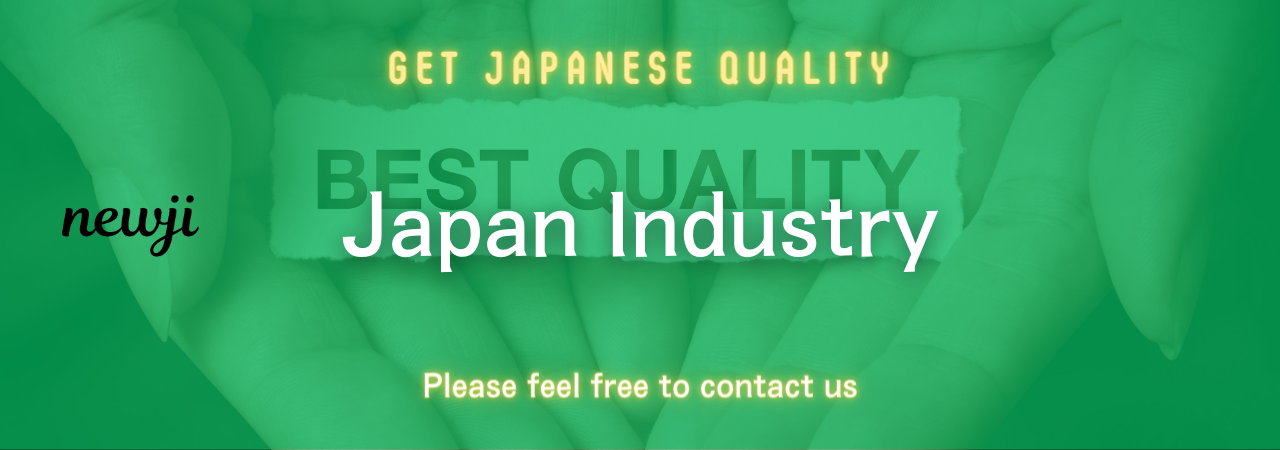
目次
Understanding Sensory Testing
Quality assurance departments have long played a crucial role in maintaining the standards of products and services across various industries.
One of the tools at their disposal is sensory testing, a method used to evaluate products based on the senses of sight, smell, taste, touch, and hearing.
Sensory testing provides invaluable insights into how consumers perceive a product, helping companies enhance quality and customer satisfaction.
The Importance of Sensory Testing in Quality Assurance
Sensory testing is more than just a subjective analysis.
It is a structured approach to understanding consumer preferences and expectations.
By effectively utilizing sensory testing, quality assurance departments can ensure that their products meet the desired standards.
This is particularly important in industries like food and beverage, cosmetics, and textiles, where sensory attributes can significantly impact consumer choice.
Through sensory testing, companies can identify subtle differences between product batches, aiding in consistency and quality control.
It helps in refining products before they reach consumers, ensuring that they fulfill the promise made by their packaging and marketing.
Moreover, sensory testing can uncover areas for improvement, leading to product innovation and enhanced market competitiveness.
Standardizing Sensory Testing Methods
To fully leverage the benefits of sensory testing, it is essential to standardize the methods used across the quality assurance process.
Standardization ensures consistency, reliability, and repeatability of results, making it a cornerstone of effective quality assurance.
Developing Clear Testing Protocols
Standardization begins with developing clear testing protocols.
This involves defining the objectives of the sensory test, selecting appropriate methodologies, and establishing criteria for evaluation.
Clear protocols help remove subjectivity and bias, ensuring that the results are dependable and actionable.
Training is a critical aspect of protocol development.
Panelists, or the individuals conducting the tests, must be adequately trained to ensure consistency in evaluations.
Training helps in calibrating sensory responses, reducing variability, and improving the quality of data collected from sensory testing sessions.
Utilizing Objective Measurements
While sensory testing inherently involves subjective evaluations, incorporating objective measurements can bolster the reliability of the results.
Utilizing tools like colorimeters, texture analyzers, and gas chromatographs can provide quantitative data that complements the sensory perceptions.
These measurements can serve as benchmarks, helping interpret sensory data within the context of physical attributes.
By combining subjective assessments with objective measures, quality assurance departments can gain a comprehensive understanding of product characteristics.
Effective Utilization of Sensory Testing
Once standardized methods are in place, the focus shifts to effectively utilizing sensory testing within the quality assurance framework.
This involves integrating sensory test results into the broader quality management system, ensuring that insights are translated into tangible product improvements.
Incorporating Consumer Feedback
One of the primary goals of sensory testing is to align products with consumer expectations.
By incorporating consumer feedback into sensory evaluations, quality assurance departments can ensure that the test results are relevant and applicable.
Involving consumers in sensory testing panels can provide a direct line to consumer perceptions and preferences, allowing firms to make informed decisions regarding product development and refinement.
Data Analysis and Interpretation
The data generated from sensory testing must be analyzed and interpreted within the context of the product and the market.
This involves identifying patterns, trends, and correlations that can inform product quality strategies.
Advanced statistical tools and software can aid in data analysis, providing insights that manual methods might overlook.
Regularly reviewing and interpreting sensory data helps in maintaining product consistency and identifying areas for strategic improvements.
Challenges in Sensory Testing
Despite its potential benefits, sensory testing can pose challenges that quality assurance departments need to address to maximize its efficacy.
Managing Subjectivity and Bias
One of the primary challenges in sensory testing is managing subjectivity and bias.
Even with standardized procedures, individual perceptions can vary, leading to inconsistencies in results.
Implementing rigorous panelist selection and training programs can help mitigate these issues, ensuring that evaluations are as objective as possible.
Balancing Cost and Benefits
Sensory testing can be resource-intensive, requiring investments in trained personnel, testing facilities, and analysis tools.
Quality assurance departments need to balance these costs with the benefits derived from sensory testing outcomes.
Conducting cost-benefit analyses can help justify the investment in sensory testing and ensure that it aligns with the company’s strategic goals.
Conclusion
Standardizing and effectively utilizing sensory testing is of paramount importance for quality assurance departments striving to maintain high product standards.
Through clear protocols, objective measurements, and consumer feedback integration, sensory testing can offer invaluable insights into product quality and consumer preferences.
By overcoming challenges related to subjectivity and resource allocation, companies can leverage sensory testing to enhance product offerings, ensuring that they not only meet but exceed customer expectations.
In doing so, sensory testing becomes a powerful tool in the quality assurance arsenal, fostering innovation and delivering value to both the company and its consumers.
資料ダウンロード
QCD調達購買管理クラウド「newji」は、調達購買部門で必要なQCD管理全てを備えた、現場特化型兼クラウド型の今世紀最高の購買管理システムとなります。
ユーザー登録
調達購買業務の効率化だけでなく、システムを導入することで、コスト削減や製品・資材のステータス可視化のほか、属人化していた購買情報の共有化による内部不正防止や統制にも役立ちます。
NEWJI DX
製造業に特化したデジタルトランスフォーメーション(DX)の実現を目指す請負開発型のコンサルティングサービスです。AI、iPaaS、および先端の技術を駆使して、製造プロセスの効率化、業務効率化、チームワーク強化、コスト削減、品質向上を実現します。このサービスは、製造業の課題を深く理解し、それに対する最適なデジタルソリューションを提供することで、企業が持続的な成長とイノベーションを達成できるようサポートします。
オンライン講座
製造業、主に購買・調達部門にお勤めの方々に向けた情報を配信しております。
新任の方やベテランの方、管理職を対象とした幅広いコンテンツをご用意しております。
お問い合わせ
コストダウンが利益に直結する術だと理解していても、なかなか前に進めることができない状況。そんな時は、newjiのコストダウン自動化機能で大きく利益貢献しよう!
(Β版非公開)