- お役立ち記事
- Standards and practices for supplier selection in the aircraft industry
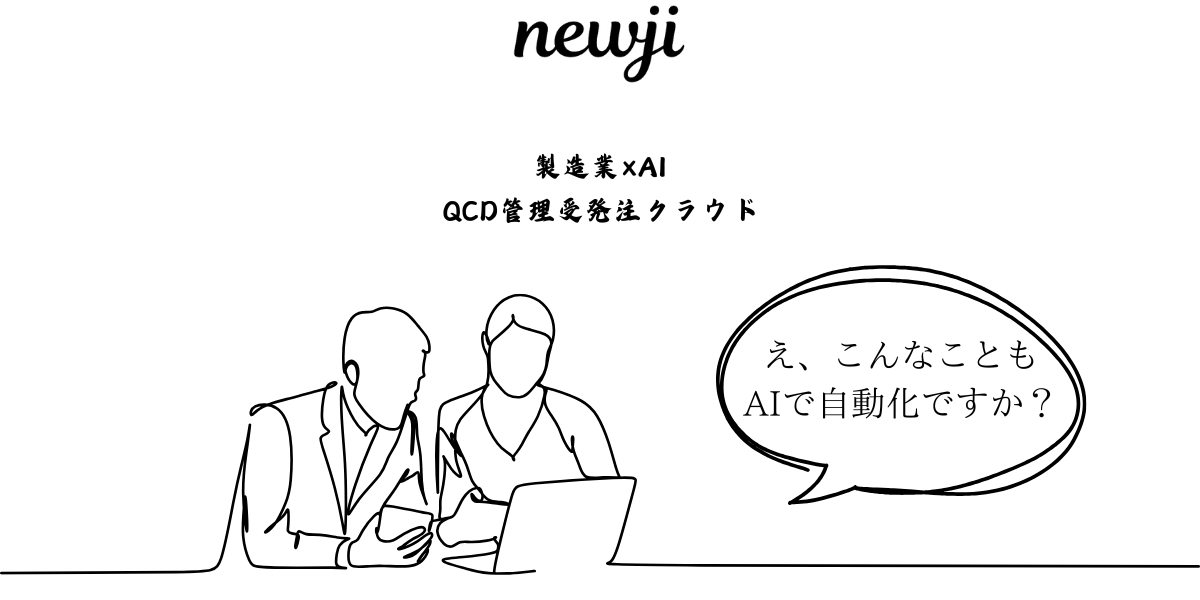
Standards and practices for supplier selection in the aircraft industry
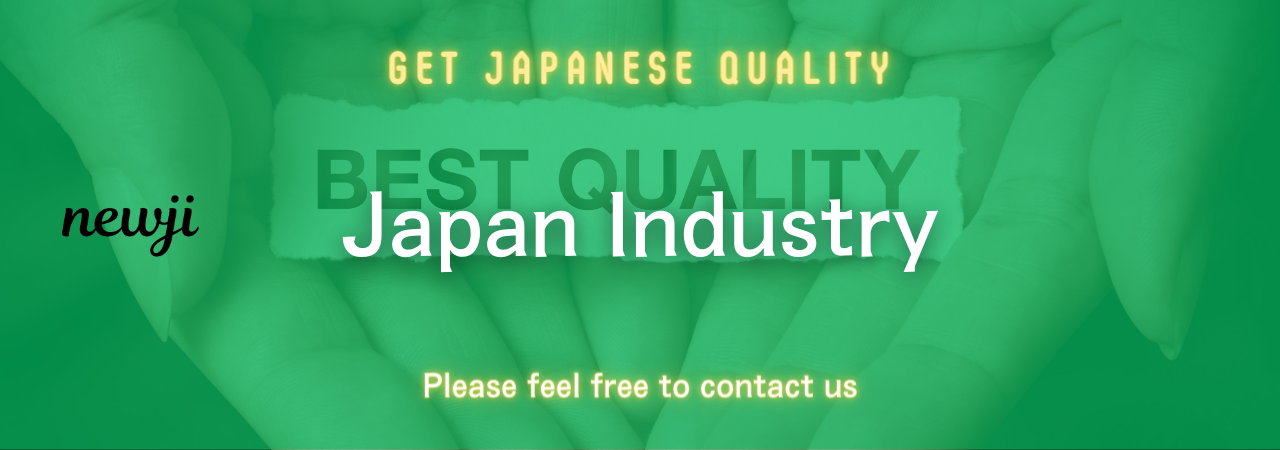
Understanding Supplier Selection in the Aircraft Industry
In the aircraft industry, choosing the right supplier is crucial for maintaining high quality, safety, and compliance standards.
This process is not just about procuring components but ensuring that every part meets strict regulatory and performance standards essential for the safety and operational efficiency of aircraft.
The Importance of Supply Chain Management
Effective supply chain management in the aircraft industry is vital for maintaining smooth operations.
The complexity of aircraft systems means that even a small defect can lead to significant safety risks and operational challenges.
Therefore, selecting suppliers that adhere to the highest standards is crucial.
Suppliers must ensure that their products are reliable, consistent, and meet the precise specifications required by aircraft manufacturers.
This necessitates a robust supplier evaluation process that includes assessing their capabilities, financial stability, and a proven track record of quality and compliance.
Key Criteria for Supplier Selection
When selecting suppliers in the aircraft industry, several criteria are considered essential:
Quality Assurance
Quality is non-negotiable in the aircraft industry.
Suppliers must have comprehensive quality assurance systems in place.
This typically involves certifications like AS9100, which aligns with ISO 9001 but with additional requirements specific to the aerospace industry.
These certifications ensure that the supplier maintains a systematic approach to quality management.
Regulatory Compliance
Suppliers must comply with aviation regulations and standards.
This includes adhering to guidelines from bodies such as the Federal Aviation Administration (FAA) in the USA and the European Union Aviation Safety Agency (EASA).
Compliance ensures that the components meet safety and operational standards essential for aircraft performance.
Technical Capability
The ability of a supplier to produce components that meet specific technical specifications is crucial.
This includes having advanced manufacturing capabilities and the technical expertise to produce high-precision parts.
Suppliers should also have the ability to innovate and adapt to new technologies and materials used in the aircraft industry.
Reliability and Performance History
A proven track record of reliability and high performance is a significant consideration in supplier selection.
Aircraft manufacturers prefer suppliers with a history of delivering quality components consistently on time.
Their past performance is often a predictor of future reliability.
Cost Competitiveness
While cost should not compromise quality, it remains an important consideration.
Suppliers need to offer competitive pricing without sacrificing the standards required in the aviation industry.
Cost evaluations are typically performed alongside assessments of quality and reliability to ensure value for money.
Supply Chain Flexibility and Responsiveness
The ability to respond quickly to changes in demand or to unforeseen challenges is essential for suppliers in the aircraft industry.
This means having flexible production capabilities and a responsive supply chain that can adapt to changes without compromising on quality or delivery schedules.
Steps in Supplier Selection
The process of selecting suppliers in the aircraft industry involves several critical steps:
Pre-Qualification
Pre-qualification involves initial screening based on key criteria such as certifications, financial stability, and past performance.
This helps narrow down potential suppliers to those that meet the basic requirements of the industry.
Request for Proposal (RFP) or Request for Quotation (RFQ)
Once a short list of suppliers is prepared, manufacturers issue a Request for Proposal (RFP) or a Request for Quotation (RFQ).
These documents outline the requirements for the components and allow suppliers to submit proposals or bids.
The proposals are assessed based on technical compliance, price, delivery timelines, and other specified criteria.
Evaluation and Selection
The proposals are evaluated through a detailed assessment process.
This includes technical evaluations, site visits, and inspections of facilities and processes to ensure compliance with industry standards.
The evaluation team typically consists of experts from different departments, including engineering, quality assurance, and procurement.
Supplier Audits
Conducting audits of the supplier’s facilities is an essential part of the evaluation process.
This involves a detailed inspection and verification of the supplier’s production capabilities, quality control systems, and compliance with industry standards.
Supplier audits help ensure that they can consistently deliver products that meet the required specifications.
Conclusion and Contracting
Once a supplier has been selected, contract negotiations begin.
These contracts are comprehensive and outline all aspects of the supply arrangement, including product specifications, pricing, delivery schedules, and terms of quality assurance.
The contract serves as a binding agreement to ensure that suppliers adhere to the required standards throughout the duration of the partnership.
Challenges in Supplier Selection
The aircraft industry faces several challenges in supplier selection, such as:
Rapid Technological Advances
The aerospace industry is continually evolving with technological advancements.
Suppliers need to keep pace with changes in materials, manufacturing processes, and innovations to remain competitive and meet customer expectations.
Global Supply Chain Risks
Operating in a global marketplace means dealing with supply chain risks, including geopolitical issues, natural disasters, and economic uncertainties.
Manufacturers must ensure suppliers have robust risk management strategies to mitigate potential disruptions.
Conclusion
In the aircraft industry, selecting the right suppliers is a critical strategic decision that impacts safety, quality, and operational efficiency.
By thoroughly evaluating potential suppliers against a robust set of criteria, aircraft manufacturers can ensure they maintain the highest standards in their supply chain and continue to deliver safe and reliable aircraft to the market.
資料ダウンロード
QCD調達購買管理クラウド「newji」は、調達購買部門で必要なQCD管理全てを備えた、現場特化型兼クラウド型の今世紀最高の購買管理システムとなります。
ユーザー登録
調達購買業務の効率化だけでなく、システムを導入することで、コスト削減や製品・資材のステータス可視化のほか、属人化していた購買情報の共有化による内部不正防止や統制にも役立ちます。
NEWJI DX
製造業に特化したデジタルトランスフォーメーション(DX)の実現を目指す請負開発型のコンサルティングサービスです。AI、iPaaS、および先端の技術を駆使して、製造プロセスの効率化、業務効率化、チームワーク強化、コスト削減、品質向上を実現します。このサービスは、製造業の課題を深く理解し、それに対する最適なデジタルソリューションを提供することで、企業が持続的な成長とイノベーションを達成できるようサポートします。
オンライン講座
製造業、主に購買・調達部門にお勤めの方々に向けた情報を配信しております。
新任の方やベテランの方、管理職を対象とした幅広いコンテンツをご用意しております。
お問い合わせ
コストダウンが利益に直結する術だと理解していても、なかなか前に進めることができない状況。そんな時は、newjiのコストダウン自動化機能で大きく利益貢献しよう!
(Β版非公開)