- お役立ち記事
- Steel decarburization technology and its contribution to production cost reduction [for industry]
月間77,185名の
製造業ご担当者様が閲覧しています*
*2025年2月28日現在のGoogle Analyticsのデータより
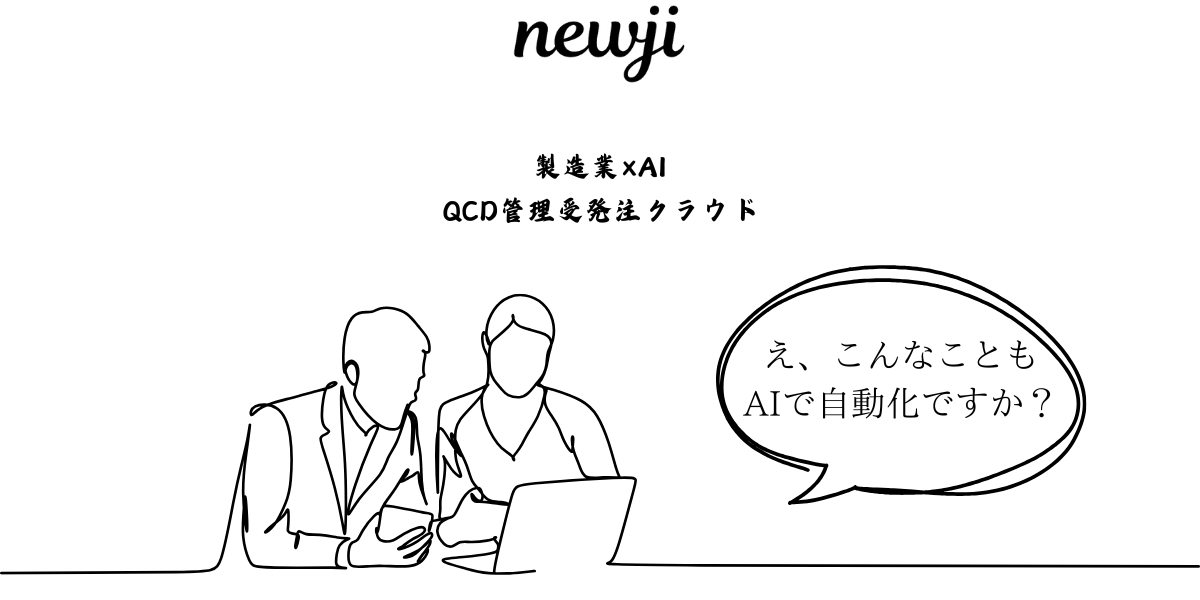
Steel decarburization technology and its contribution to production cost reduction [for industry]
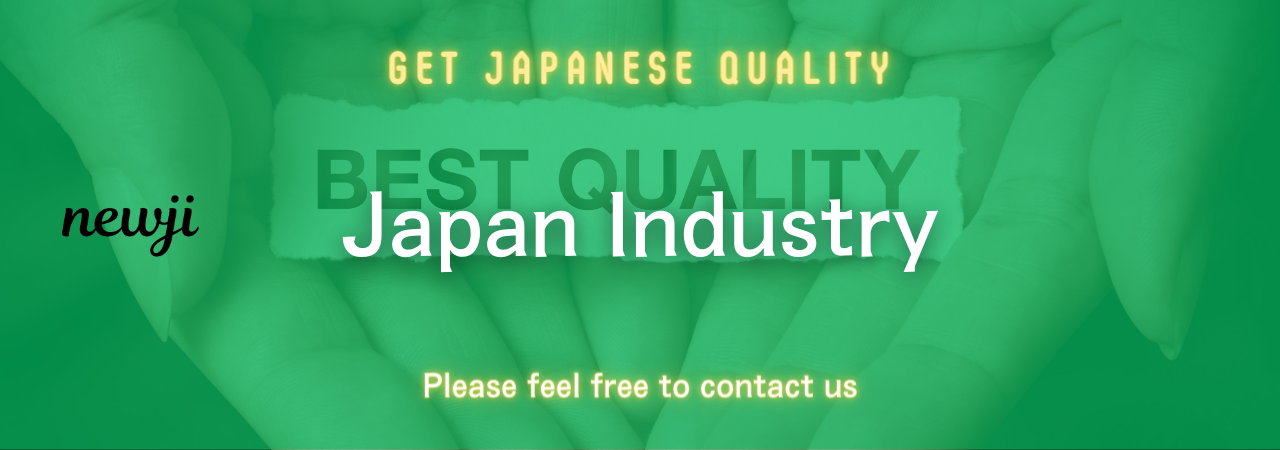
目次
Understanding Steel Decarburization
Steel decarburization is a crucial process in the steel manufacturing industry.
It involves reducing the carbon content in steel to enhance its properties and suitability for various applications.
This process contributes significantly to improving the quality of the final product and is also pivotal in reducing production costs.
Carbon is a fundamental element in steel that impacts its hardness and strength.
However, excessive carbon can make steel brittle and difficult to work with.
Therefore, the decarburization process is essential to achieving the desired balance of strength, ductility, and workability.
Methods of Steel Decarburization
There are several methods employed in the steel industry to carry out decarburization, each with unique advantages.
One common method is the Basic Oxygen Steelmaking (BOS) process.
In this method, oxygen is blown into the molten iron to reduce the carbon content.
Oxidation occurs, and carbon is converted to carbon dioxide gas, which escapes from the melt.
Another prevalent technique is Electric Arc Furnace (EAF) steelmaking.
This method uses high-temperature electric arcs to melt scrap steel and reduce its carbon content.
Decarburization occurs as oxygen is introduced to react with carbon, forming gases that are removed from the furnace.
There is also Vacuum Degassing, which involves the use of low-pressure environments to facilitate the removal of carbon.
By employing a vacuum, gases dissolved in the molten steel are drawn out, effectively reducing carbon levels.
Each of these methods can be tailored to match specific production needs and desired steel characteristics.
The Economic Impact of Decarburization
Decarburization technology plays a crucial role in reducing production costs for steel manufacturers.
Firstly, by enhancing steel quality through optimized carbon levels, manufacturers can produce higher-grade products that fulfill commercial demands.
This increased product quality translates to better market value and customer satisfaction.
Moreover, efficient decarburization reduces energy consumption during manufacturing.
Lower carbon content leads to less energy required for subsequent processing steps, saving on energy costs.
Decarburization also minimizes material wastage.
Controlling the carbon content precisely prevents overproduction of brittle, unusable steel, which reduces scrap rates and leads to cost savings.
Furthermore, regulatory compliance is crucial, as many countries impose strict emissions standards.
Decarburization reduces the carbon footprint of steel production by lowering carbon emissions and ensuring adherence to environmental regulations.
Compliance helps avoid potential fines and improves the manufacturer’s public image, fostering trust and loyalty among consumers.
Innovations in Steel Decarburization
Innovations enhanced decarburization efficiency and further reduced manufacturing costs.
Technological advancements allow real-time monitoring of carbon levels during the steel production process.
Advanced sensors and automated systems ensure precise control over the decarburization phase, optimizing the balance of energy and resources.
Predictive models utilizing machine learning and artificial intelligence play an integral role in forecasting optimal decarburization conditions.
These models help in adjusting processes dynamically to achieve precise carbon levels, significantly boosting efficiency.
Research focuses on developing more sustainable decarburization methods.
Efforts include exploring alternative methods such as microbial and biotechnological approaches, which could offer environmentally friendly and energy-efficient solutions.
Challenges in Decarburization
Despite its benefits, steel decarburization presents several challenges.
Control of carbon content must be precise to prevent alteration of desired steel properties.
Ensuring accuracy requires sophisticated equipment and skilled personnel, which can increase initial investment costs.
Balancing decarburization with other metallurgical processes requires careful planning, as changes can affect overall production schedules.
Additionally, while reducing carbon emissions is beneficial for the environment, processes must be continuously improved to minimize their ecological impact further, posing an ongoing challenge.
Conclusion
Steel decarburization technology significantly contributes to production cost reduction.
By optimizing the properties of steel, reducing energy and material waste, and ensuring regulatory compliance, manufacturers can enhance profitability and sustainability.
As innovations and strategies evolve, the steel industry is poised to overcome challenges and achieve even greater efficiencies in the future.
Investing in state-of-the-art decarburization techniques will remain essential for maintaining competitiveness and meeting the ever-growing demand for high-quality steel products.
資料ダウンロード
QCD管理受発注クラウド「newji」は、受発注部門で必要なQCD管理全てを備えた、現場特化型兼クラウド型の今世紀最高の受発注管理システムとなります。
ユーザー登録
受発注業務の効率化だけでなく、システムを導入することで、コスト削減や製品・資材のステータス可視化のほか、属人化していた受発注情報の共有化による内部不正防止や統制にも役立ちます。
NEWJI DX
製造業に特化したデジタルトランスフォーメーション(DX)の実現を目指す請負開発型のコンサルティングサービスです。AI、iPaaS、および先端の技術を駆使して、製造プロセスの効率化、業務効率化、チームワーク強化、コスト削減、品質向上を実現します。このサービスは、製造業の課題を深く理解し、それに対する最適なデジタルソリューションを提供することで、企業が持続的な成長とイノベーションを達成できるようサポートします。
製造業ニュース解説
製造業、主に購買・調達部門にお勤めの方々に向けた情報を配信しております。
新任の方やベテランの方、管理職を対象とした幅広いコンテンツをご用意しております。
お問い合わせ
コストダウンが利益に直結する術だと理解していても、なかなか前に進めることができない状況。そんな時は、newjiのコストダウン自動化機能で大きく利益貢献しよう!
(β版非公開)