- お役立ち記事
- Step-by-Step Explanation of Part Inspection and Quality Control Processes
月間76,176名の
製造業ご担当者様が閲覧しています*
*2025年3月31日現在のGoogle Analyticsのデータより
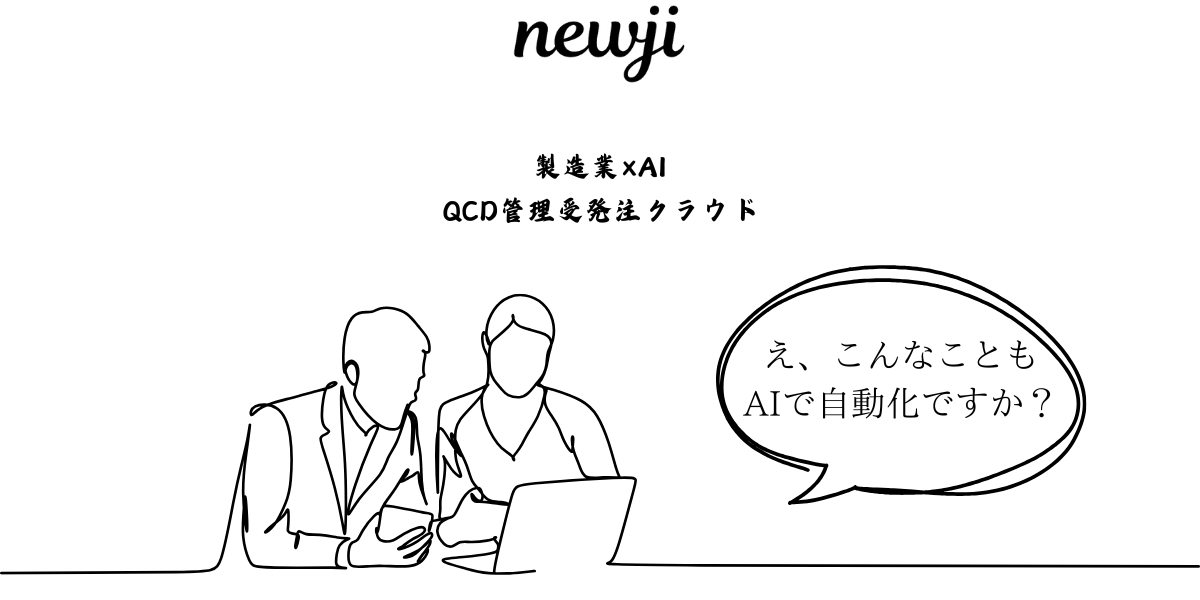
Step-by-Step Explanation of Part Inspection and Quality Control Processes
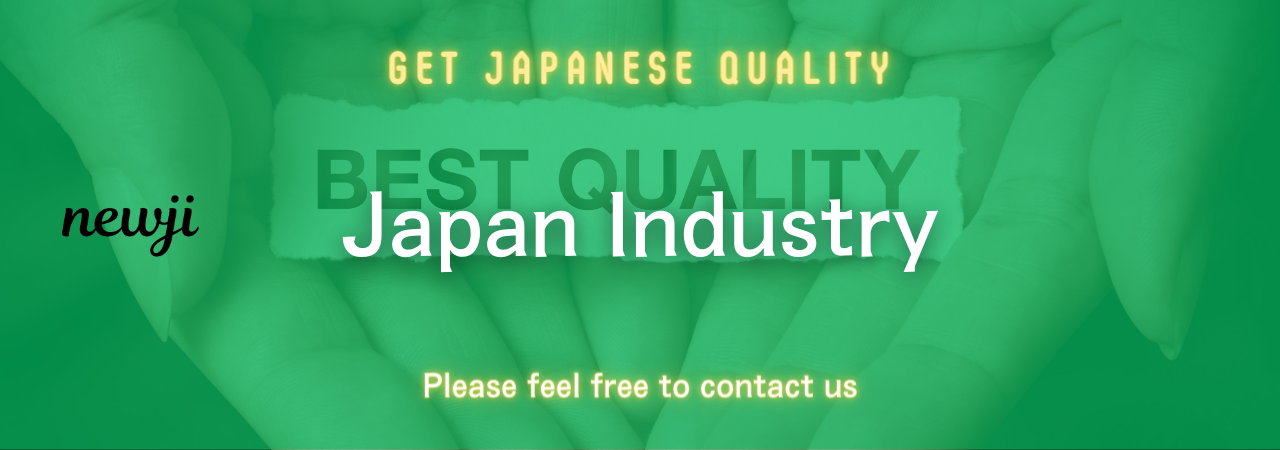
目次
Introduction to Part Inspection and Quality Control
Manufacturing industries depend heavily on the reliability of parts and products.
To ensure high-quality production, companies follow rigorous part inspection and quality control processes.
These procedures help maintain standards and reduce defects, which is essential for customer satisfaction and safety.
In this article, we will explore the steps involved in part inspection and quality control, making it easy to understand for everyone.
What is Part Inspection?
Part inspection is the process of examining and measuring a product or component to ensure it meets specified requirements and standards.
It can be performed at various stages of the production process, from the raw material stage to the final product.
Part inspection helps identify any defects or deviations from the standards, enabling corrective actions before the part reaches the customer.
Stages of Part Inspection
1. Incoming Inspection
Incoming inspection happens when raw materials or components are received from suppliers.
Inspectors check for any inconsistencies or defects in the materials and ensure they meet the required specifications.
This step is crucial because it prevents defective materials from entering the production line.
2. In-Process Inspection
In-process inspection occurs during the manufacturing process.
Quality control personnel inspect parts at various stages of production to ensure they meet the required standards.
This step allows for immediate detection and correction of any issues, minimizing waste and production delays.
3. Final Inspection
The final inspection is the last step before a product is released to the customer.
Inspectors conduct a thorough examination of the finished product to ensure it meets all specifications and standards.
Any defects found at this stage are either corrected or the product is rejected.
Tools and Techniques for Part Inspection
Part inspection involves various tools and techniques to measure and analyze components accurately.
Common Inspection Tools
1. Calipers
Calipers are precise instruments used to measure the dimensions of a part, such as its width, height, and depth.
They are essential for ensuring that parts meet specified measurements.
2. Micrometers
Micrometers provide highly accurate measurements of small dimensions, often used in machining and precision engineering.
They help verify that parts have been manufactured within the required tolerances.
3. Gauges
Gauges are devices used to measure specific dimensions or check the shape of a part.
They include ring gauges, plug gauges, and snap gauges, which are used for different types of measurements.
Advanced Inspection Techniques
1. Coordinate Measuring Machines (CMM)
CMMs are sophisticated machines that use probes to measure the geometry of a part.
They provide detailed and accurate measurements, which are essential for complex and high-precision components.
2. Non-Destructive Testing (NDT)
NDT methods, such as X-rays, ultrasound, and magnetic particle testing, are used to inspect parts without causing any damage.
These techniques help detect internal defects that are not visible to the naked eye.
3. Optical Inspection Systems
Optical inspection systems use cameras and image analysis software to check parts for defects.
They are commonly used in electronics and other industries where visual inspection is crucial.
Understanding Quality Control
Quality control (QC) is the process of ensuring that products meet the required quality standards through systematic inspection and testing.
It involves monitoring and controlling the production process to detect any issues that may affect the product’s quality.
Components of Quality Control
1. Quality Planning
Quality planning involves defining the quality standards and specifications that a product must meet.
It also involves developing procedures and processes to achieve these standards.
2. Quality Assurance
Quality assurance (QA) focuses on preventing defects by ensuring that the production process is well-designed and implemented.
It includes activities such as process control, training, and documentation.
3. Quality Improvement
Quality improvement seeks to enhance the production process and eliminate any sources of defects.
It involves continuous monitoring, analysis, and implementation of corrective actions.
Steps in the Quality Control Process
The quality control process is systematic and includes several key steps to ensure product quality.
1. Define Quality Standards
The first step is to establish the quality standards and specifications that the product must meet.
These standards should be based on customer requirements, industry regulations, and best practices.
2. Inspect Raw Materials
Before production begins, inspect the raw materials to ensure they meet the defined quality standards.
This step helps prevent defects from entering the production process.
3. Monitor the Production Process
Continuous monitoring of the production process helps detect any deviations from the defined standards.
Implement in-process inspections and use statistical process control (SPC) techniques to monitor and control the process.
4. Perform Final Inspection
Conduct a final inspection of the finished product to ensure it meets all the quality standards and specifications.
Any defects found at this stage should be addressed before the product is released to the customer.
5. Implement Feedback Loop
Establish a feedback loop to collect data on defects and issues identified during the inspection process.
Use this data to identify trends and implement corrective actions to prevent future defects.
Conclusion
Part inspection and quality control are essential processes in manufacturing that help ensure the reliability and quality of products.
By following a systematic approach and using the right tools and techniques, companies can detect and correct defects, maintain standards, and achieve customer satisfaction.
Understanding the steps involved in part inspection and quality control not only helps manufacturers produce high-quality products but also builds trust and credibility with their customers.
資料ダウンロード
QCD管理受発注クラウド「newji」は、受発注部門で必要なQCD管理全てを備えた、現場特化型兼クラウド型の今世紀最高の受発注管理システムとなります。
ユーザー登録
受発注業務の効率化だけでなく、システムを導入することで、コスト削減や製品・資材のステータス可視化のほか、属人化していた受発注情報の共有化による内部不正防止や統制にも役立ちます。
NEWJI DX
製造業に特化したデジタルトランスフォーメーション(DX)の実現を目指す請負開発型のコンサルティングサービスです。AI、iPaaS、および先端の技術を駆使して、製造プロセスの効率化、業務効率化、チームワーク強化、コスト削減、品質向上を実現します。このサービスは、製造業の課題を深く理解し、それに対する最適なデジタルソリューションを提供することで、企業が持続的な成長とイノベーションを達成できるようサポートします。
製造業ニュース解説
製造業、主に購買・調達部門にお勤めの方々に向けた情報を配信しております。
新任の方やベテランの方、管理職を対象とした幅広いコンテンツをご用意しております。
お問い合わせ
コストダウンが利益に直結する術だと理解していても、なかなか前に進めることができない状況。そんな時は、newjiのコストダウン自動化機能で大きく利益貢献しよう!
(β版非公開)