- お役立ち記事
- Step-by-Step Explanation of Part Inspection and Quality Control Processes
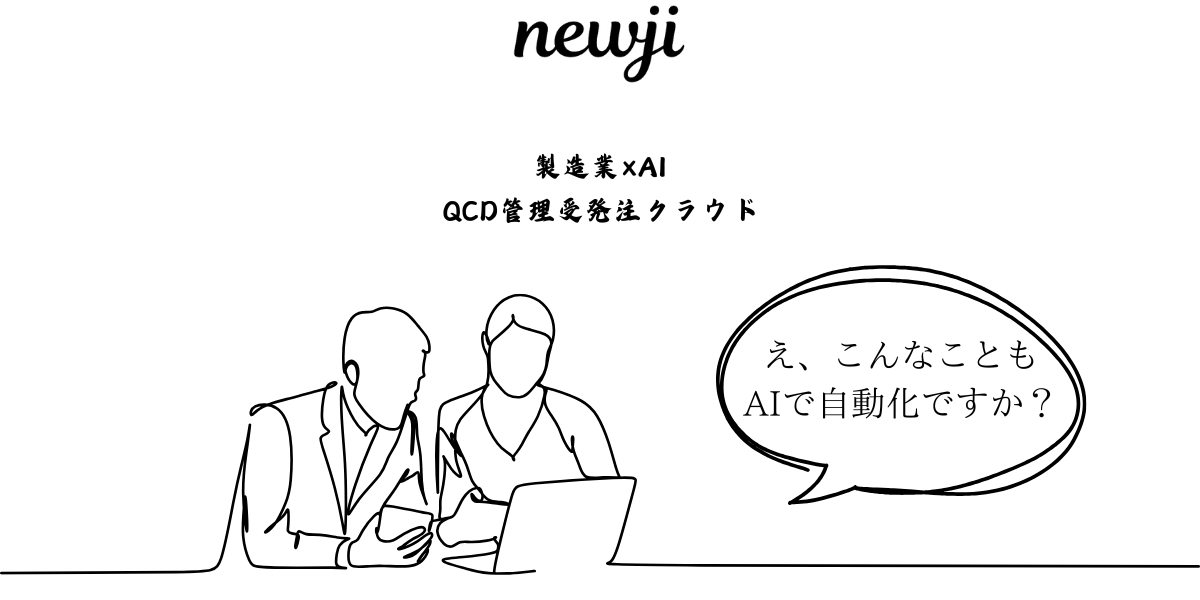
Step-by-Step Explanation of Part Inspection and Quality Control Processes
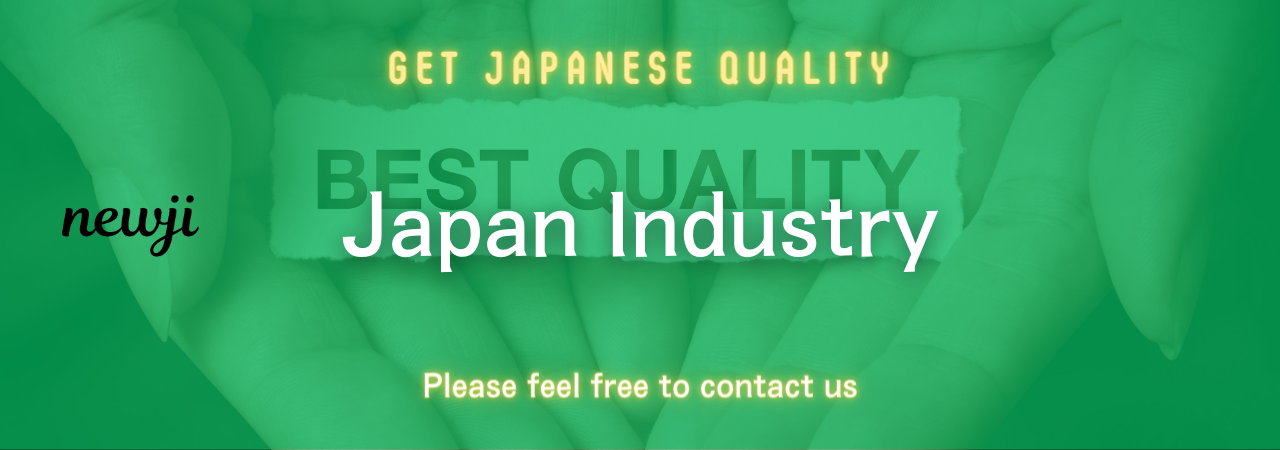
目次
Understanding Part Inspection Processes
Part inspection is a critical component in manufacturing and production.
It ensures that every component meets the required specifications and quality standards before it moves to the next stage of the process.
This meticulous check helps prevent issues further down the line and ensures the final product is of the highest quality.
Visual Inspection
Visual inspection is the most basic form of part inspection.
It involves looking at the part with the naked eye or using tools like magnifying glasses and microscopes.
This method helps in identifying surface defects such as cracks, scratches, or other imperfections.
Even though it’s simple, visual inspection is highly effective in spotting visible flaws quickly.
Dimensional Inspection
Dimensional inspection is a more precise method, where the physical dimensions of a part are measured.
This could include checking the length, width, diameter, and thickness.
Tools like calipers, micrometers, and coordinate measuring machines (CMM) are commonly used.
The goal is to ensure the component matches the design specifications exactly, which is crucial for parts that must fit together perfectly.
Material Testing
Material testing is important to verify that the components are made from the correct materials.
This can be done through techniques like X-ray fluorescence (XRF), spectrometry, or even chemical analysis.
By confirming the material composition, manufacturers can ensure the durability and performance of the part.
Non-Destructive Testing (NDT)
NDT methods are used to inspect parts without causing any damage.
Techniques like ultrasonic testing, radiographic testing, and magnetic particle testing fall under this category.
These methods are particularly useful for detecting internal flaws that are not visible on the surface.
NDT is essential in industries where safety is paramount, such as aerospace and automotive manufacturing.
Grasping Quality Control Processes
Quality control (QC) processes ensure that products meet customer and regulatory requirements.
It is an overarching process that includes part inspection, but also extends to evaluating the final product and identifying areas for improvement.
Quality Planning
Quality planning is the first step in quality control.
It involves defining quality standards and how they can be met.
Companies often use quality management systems (QMS) like ISO 9001 to establish these standards.
By setting clear guidelines, they ensure consistency in production and output.
In-Process Quality Control
In-process quality control happens during the manufacturing process.
Engineers and operators monitor the production to catch defects early.
This could involve regular sampling, automated inspections, or real-time monitoring systems.
By identifying issues as they occur, manufacturers can make immediate adjustments to correct them.
Final Product Inspection
Final product inspection is the last check before a product is shipped to customers.
This thorough inspection includes checking the overall assembly, function, and appearance of the product.
Products that do not meet the quality standards are either reworked or discarded.
This step is crucial to maintaining a company’s reputation and customer satisfaction.
Continuous Improvement
Quality control is not a one-time effort.
Continuous improvement ensures that the processes themselves are constantly evaluated and refined.
Tools like Six Sigma, Lean Manufacturing, and Total Quality Management (TQM) help in this ongoing process.
By continuously seeking ways to improve, companies can reduce waste, increase efficiency, and maintain high standards.
Benefits of Effective Quality Control and Inspection
Effective quality control and inspection processes offer numerous benefits.
First, they ensure the safety and reliability of products, which is critical in sectors such as healthcare, automotive, and aerospace.
Second, they help in reducing costs by minimizing wastage and rework.
Third, they improve customer satisfaction by delivering products that meet or exceed expectations.
Finally, they enhance a company’s reputation by consistently offering high-quality products.
Implementing Quality Control and Inspection in Your Business
To successfully implement quality control and inspection processes, businesses should start with a thorough understanding of their specific needs and goals.
Investing in the right tools and technologies is crucial.
Training employees and fostering a culture of quality are also important steps.
By making quality control an integral part of the workflow, companies can achieve greater success and customer loyalty.
In conclusion, understanding and implementing proper part inspection and quality control processes are essential in any manufacturing and production scenario.
They help ensure every product is reliable, safe, and meets the highest standards of quality.
Through continuous improvement and attention to detail, businesses can reap significant benefits and thrive in competitive markets.
資料ダウンロード
QCD調達購買管理クラウド「newji」は、調達購買部門で必要なQCD管理全てを備えた、現場特化型兼クラウド型の今世紀最高の購買管理システムとなります。
ユーザー登録
調達購買業務の効率化だけでなく、システムを導入することで、コスト削減や製品・資材のステータス可視化のほか、属人化していた購買情報の共有化による内部不正防止や統制にも役立ちます。
NEWJI DX
製造業に特化したデジタルトランスフォーメーション(DX)の実現を目指す請負開発型のコンサルティングサービスです。AI、iPaaS、および先端の技術を駆使して、製造プロセスの効率化、業務効率化、チームワーク強化、コスト削減、品質向上を実現します。このサービスは、製造業の課題を深く理解し、それに対する最適なデジタルソリューションを提供することで、企業が持続的な成長とイノベーションを達成できるようサポートします。
オンライン講座
製造業、主に購買・調達部門にお勤めの方々に向けた情報を配信しております。
新任の方やベテランの方、管理職を対象とした幅広いコンテンツをご用意しております。
お問い合わせ
コストダウンが利益に直結する術だと理解していても、なかなか前に進めることができない状況。そんな時は、newjiのコストダウン自動化機能で大きく利益貢献しよう!
(Β版非公開)