- お役立ち記事
- Step-by-Step Explanation of the Casting Process
月間76,176名の
製造業ご担当者様が閲覧しています*
*2025年3月31日現在のGoogle Analyticsのデータより
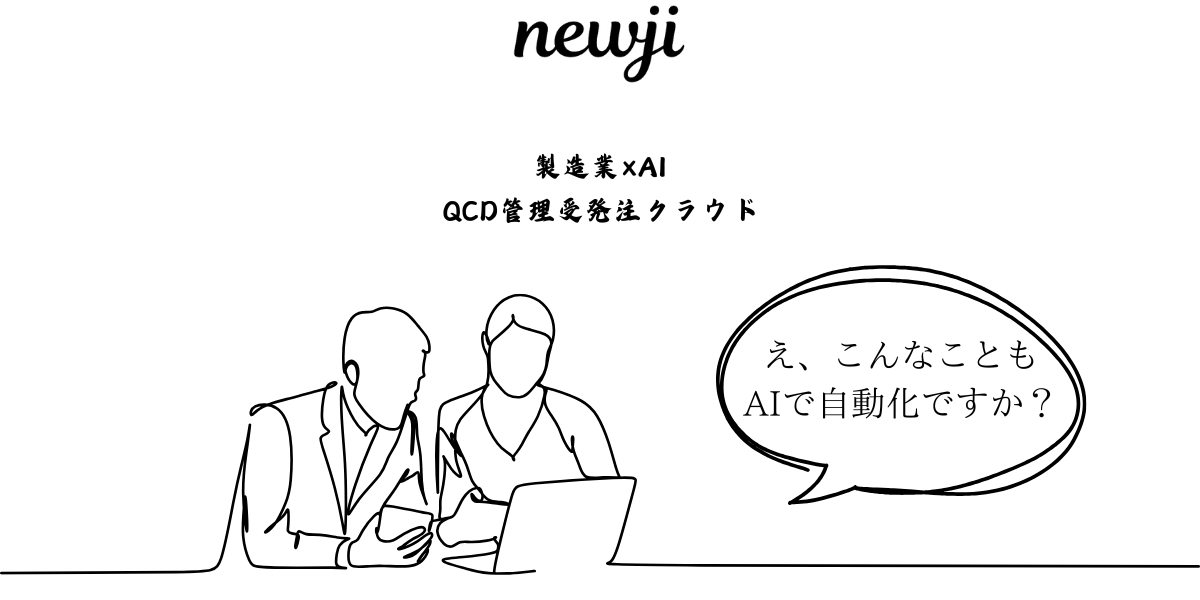
Step-by-Step Explanation of the Casting Process
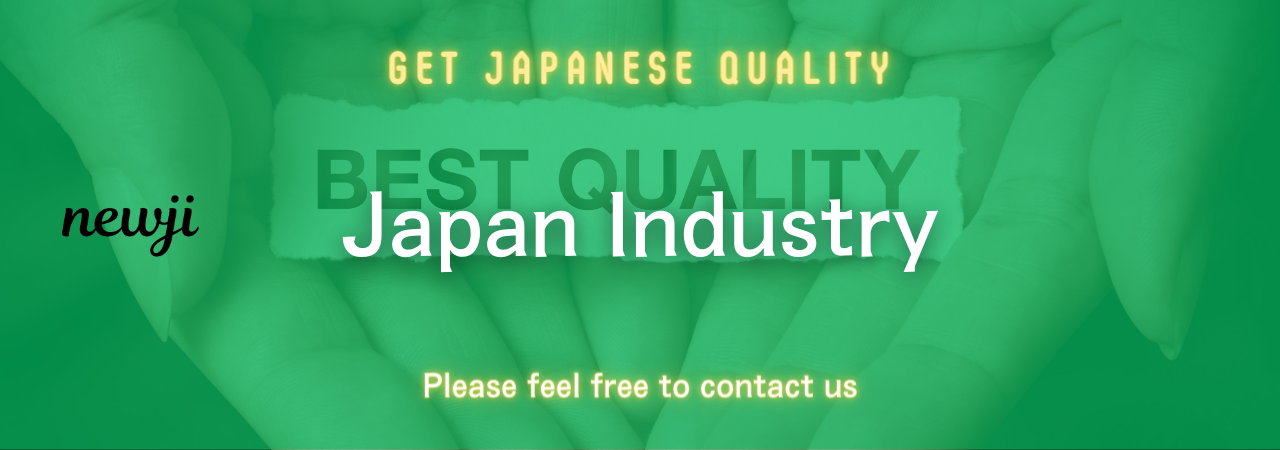
Casting is a fascinating process used to create complex metal objects. It plays an essential role in various industries, from automotive to construction. This article will provide a step-by-step explanation of the casting process.
目次
What is Casting?
Casting is a manufacturing process where a liquid material is poured into a mold containing a hollow cavity in the desired shape. The liquid then solidifies, forming the object.
Common materials used in casting include metals like aluminum, steel, and iron, as well as some plastics and ceramics.
Step 1: Creating the Pattern
The first step in the casting process is designing and creating a pattern. A pattern is a replica of the final casting. It is usually made from wood, metal, or plastic. This step is crucial because the accuracy of the pattern determines the final product’s quality.
Patterns must account for shrinkage, machining allowances, and draft angles. Shrinkage occurs as the material cools and contracts, so patterns are often slightly larger than the final product. A draft angle is a tapered angle on the pattern to help it release from the mold effortlessly.
Types of Patterns
There are different types of patterns based on the complexity of the casting:
– Single-piece pattern
– Split pattern
– Match plate pattern
Each type is chosen depending on the requirements of the casting shape and size.
Step 2: Making the Mold
Once the pattern is ready, the next step is to make the mold. Molds are typically made from sand, ceramics, or metals, depending on the casting method used. The two common types of molds are expendable molds and permanent molds.
Expendable molds, made from sand or plaster, are destroyed to retrieve the casting, while permanent molds are reused.
Types of Molding Techniques
Several molding techniques can be used, including:
– Green sand molding
– Shell molding
– Investment casting
– Die casting
Each technique has its advantages and serves different purposes within the casting industry.
Step 3: Melting the Material
Melting the material is a critical stage of the casting process. The chosen material is heated in a furnace until it becomes liquid. This involves careful monitoring of temperature to ensure the material achieves the proper fluidity for pouring.
Types of Furnaces
Different furnaces are used depending on the material being melted:
– Cupola furnace for iron
– Electric arc furnace for steel
– Crucible furnace for non-ferrous metals
Each type of furnace has its heating mechanism and is selected based on efficiency and material compatibility.
Step 4: Pouring the Liquid Metal
Once the material is in its liquid state, it is poured into the mold. Precision in this step ensures the final product’s shape and integrity. Techniques like bottom pouring or gravity pouring are used to minimize defects.
Pouring Techniques
The common techniques include:
– Tilt pouring
– Bottom pouring
– Direct pouring
Operators must wear protective gear due to the high risk associated with handling liquid metal.
Step 5: Cooling and Solidification
Once the liquid metal is poured, it needs time to cool and solidify. The cooling rate affects the metal’s microstructure, which impacts the final product’s mechanical properties. Slow cooling may result in coarse grains, while rapid cooling leads to fine grains.
Cooling Methods
Different cooling methods can be employed, such as:
– Air cooling
– Water cooling
– Forced cooling
The method chosen depends on the desired properties of the final casting.
Step 6: Removing the Casting from the Mold
After cooling, the solidified casting is extracted from the mold. This process, known as shakeout, varies depending on the type of mold used. Expendable molds, for example, are broken apart, while permanent molds are opened carefully to retrieve the casting.
Post-removal Processes
After the casting is removed, it undergoes several finishing processes to improve its appearance and functionality. These may include:
– Cleaning
– Grinding
– Heat treatment
Cleaning removes any remaining mold material, while grinding smooths the surfaces. Heat treatment enhances mechanical properties like hardness and ductility.
Step 7: Inspecting the Casting
The final step in the casting process is inspection. This ensures the casting meets quality and specification standards. Various techniques, such as visual inspection, ultrasonic testing, and X-ray analysis, can be employed.
Quality Control Techniques
Some of the most common inspection methods are:
– Visual inspection
– Dimensional measurement
– Non-destructive testing
Each method provides valuable information about the casting’s integrity and quality.
Conclusion
The casting process is a precise and intricate method for manufacturing complex shapes. From creating a pattern to final inspection, each step requires careful attention to detail to produce high-quality castings.
Whether for automotive parts, machinery, or household items, casting continues to be a vital process in manufacturing.
資料ダウンロード
QCD管理受発注クラウド「newji」は、受発注部門で必要なQCD管理全てを備えた、現場特化型兼クラウド型の今世紀最高の受発注管理システムとなります。
ユーザー登録
受発注業務の効率化だけでなく、システムを導入することで、コスト削減や製品・資材のステータス可視化のほか、属人化していた受発注情報の共有化による内部不正防止や統制にも役立ちます。
NEWJI DX
製造業に特化したデジタルトランスフォーメーション(DX)の実現を目指す請負開発型のコンサルティングサービスです。AI、iPaaS、および先端の技術を駆使して、製造プロセスの効率化、業務効率化、チームワーク強化、コスト削減、品質向上を実現します。このサービスは、製造業の課題を深く理解し、それに対する最適なデジタルソリューションを提供することで、企業が持続的な成長とイノベーションを達成できるようサポートします。
製造業ニュース解説
製造業、主に購買・調達部門にお勤めの方々に向けた情報を配信しております。
新任の方やベテランの方、管理職を対象とした幅広いコンテンツをご用意しております。
お問い合わせ
コストダウンが利益に直結する術だと理解していても、なかなか前に進めることができない状況。そんな時は、newjiのコストダウン自動化機能で大きく利益貢献しよう!
(β版非公開)