- お役立ち記事
- Steps and effects of introducing automation systems that managers in production technology departments should know
Steps and effects of introducing automation systems that managers in production technology departments should know
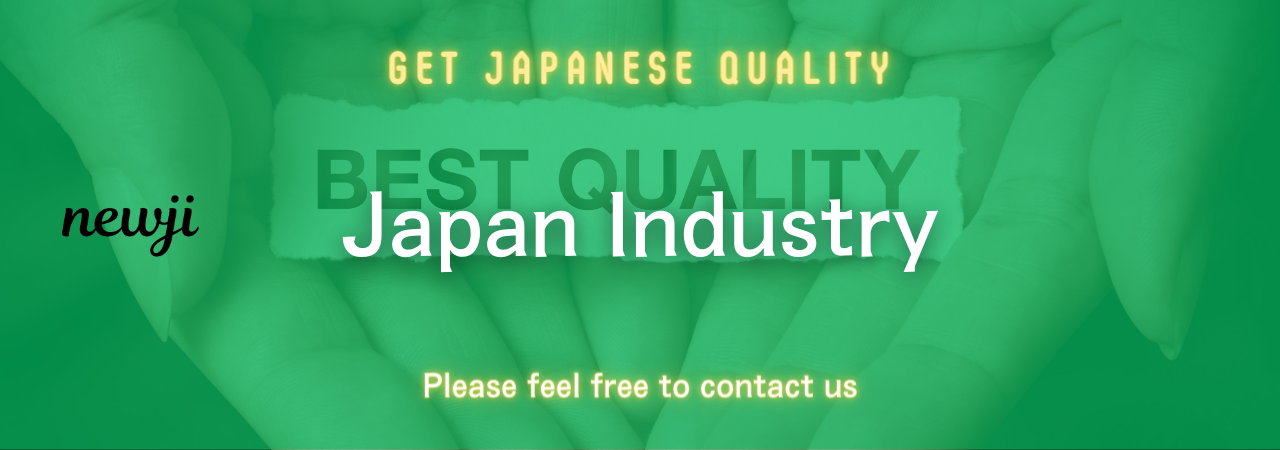
目次
Understanding Automation Systems
In today’s fast-paced manufacturing industry, embracing technology isn’t just beneficial; it’s essential for staying competitive.
Automation systems, specifically designed for production technology, can significantly enhance operational efficiency and reduce human error.
Understanding what these systems entail is the first step in leveraging their full potential.
Automation systems involve using control systems such as computers or robots to handle different processes and machinery in various industries.
They are designed to operate tasks with minimal human intervention, thereby increasing productivity.
The Importance of Automation in Manufacturing
Manufacturers across the globe are constantly looking for ways to streamline operations and cut down on costs.
Automation plays a crucial role in achieving these goals by minimizing manual tasks, which in turn reduces labor costs and improves production time.
Moreover, automation systems help in maintaining product quality through precision and repeatable processes.
Unlike humans, machines do not tire or deviate from instructions, ensuring the consistency of the product output.
Steps to Introduce Automation Systems
Adopting automation systems can be transformational, but it needs thoughtful implementation.
Here are key steps that production technology managers should follow:
1. Assess Current Operations
Before implementing any technology, understand the current state of operations.
Analyze existing workflows, bottlenecks, and areas where automation could bring improvements.
This assessment provides a baseline against which improvements can be measured.
2. Define Your Objectives
Set clear goals for what you want to achieve with automation.
Whether it’s increasing production rates, improving quality, or reducing costs, defining objectives will help guide your implementation strategy and measure success.
3. Choose the Right Technology
With various automation technologies available, selecting the right one for your needs is critical.
Consider factors such as scalability, ease of use, and integration capabilities with existing systems.
4. Design a Detailed Implementation Plan
Create a comprehensive plan outlining each step of the automation implementation process.
Include timelines, resource allocations, and key performance indicators (KPIs).
5. Train Your Workforce
Automation doesn’t eliminate the need for human intervention; instead, it changes the nature of work.
Invest in training programs to help employees adapt to new technologies and understand their new roles.
6. Pilot Test
Start with a small-scale pilot test to understand any challenges that might arise.
Analyze the test results and make necessary adjustments before full-scale roll-out.
7. Implement and Monitor
Once you have fine-tuned your pilot test, proceed with full implementation.
Continuously monitor the system to ensure it meets the set objectives and make improvements where necessary.
Effects of Introducing Automation Systems
Integrating automation systems into production technology can have profound effects on business operations.
Increased Productivity
Automation systems significantly boost productivity by enabling continuous production without breaks, unlike human workers who need rest.
This non-stop operation can lead to a substantial increase in output volume over time.
Cost Efficiency
While the initial cost of implementing an automated system can be high, the return on investment is substantial.
Reduced labor costs, minimized waste, and improved resource management contribute to long-term savings.
Improved Quality Control
Automation reduces human error and improves precision, leading to better quality products.
Consistent quality control is essential in maintaining brand reputation and customer satisfaction.
Enhanced Safety
Automation reduces the need for human workers to perform dangerous tasks, thus enhancing workplace safety.
Fewer manual processes mean a lower risk of accidents, leading to a safer working environment.
Flexible Production Capabilities
Modern automation systems are highly adaptable, allowing manufacturers to quickly switch between product lines or modify production rates as needed.
This flexibility is key in meeting varying market demands and staying competitive.
Challenges in Implementing Automation Systems
While automation offers numerous benefits, its introduction does come with challenges that need to be addressed.
High Initial Investment
The initial financial outlay for automation systems can be substantial.
It’s essential to evaluate the costs and plan finances carefully to ensure that the enterprise can support the investment long-term.
Resistance to Change
Employees may resist automation technologies due to fear of job loss or unfamiliarity with new tools.
Addressing these concerns through communication and training is critical to successful implementation.
Integration with Existing Systems
Achieving seamless integration with current processes and systems can be complex.
Select automation systems that are compatible with existing infrastructure and have robust support and documentation to help guide the integration process.
Conclusion
The introduction of automation systems in production technology departments is not merely about keeping up with technological advancements—it’s about redefining the production process for better efficiency, safety, and quality.
By carefully planning and executing strategic steps, businesses can successfully harness the power of automation to transform their operations, drive growth, and maintain a competitive edge in the market.
Educating and involving the workforce in this transition is crucial, as they are the ones who will ultimately drive the future of manufacturing.
資料ダウンロード
QCD調達購買管理クラウド「newji」は、調達購買部門で必要なQCD管理全てを備えた、現場特化型兼クラウド型の今世紀最高の購買管理システムとなります。
ユーザー登録
調達購買業務の効率化だけでなく、システムを導入することで、コスト削減や製品・資材のステータス可視化のほか、属人化していた購買情報の共有化による内部不正防止や統制にも役立ちます。
NEWJI DX
製造業に特化したデジタルトランスフォーメーション(DX)の実現を目指す請負開発型のコンサルティングサービスです。AI、iPaaS、および先端の技術を駆使して、製造プロセスの効率化、業務効率化、チームワーク強化、コスト削減、品質向上を実現します。このサービスは、製造業の課題を深く理解し、それに対する最適なデジタルソリューションを提供することで、企業が持続的な成長とイノベーションを達成できるようサポートします。
オンライン講座
製造業、主に購買・調達部門にお勤めの方々に向けた情報を配信しております。
新任の方やベテランの方、管理職を対象とした幅広いコンテンツをご用意しております。
お問い合わせ
コストダウンが利益に直結する術だと理解していても、なかなか前に進めることができない状況。そんな時は、newjiのコストダウン自動化機能で大きく利益貢献しよう!
(Β版非公開)