- お役立ち記事
- Steps to reduce lead time by streamlining the procurement process
Steps to reduce lead time by streamlining the procurement process
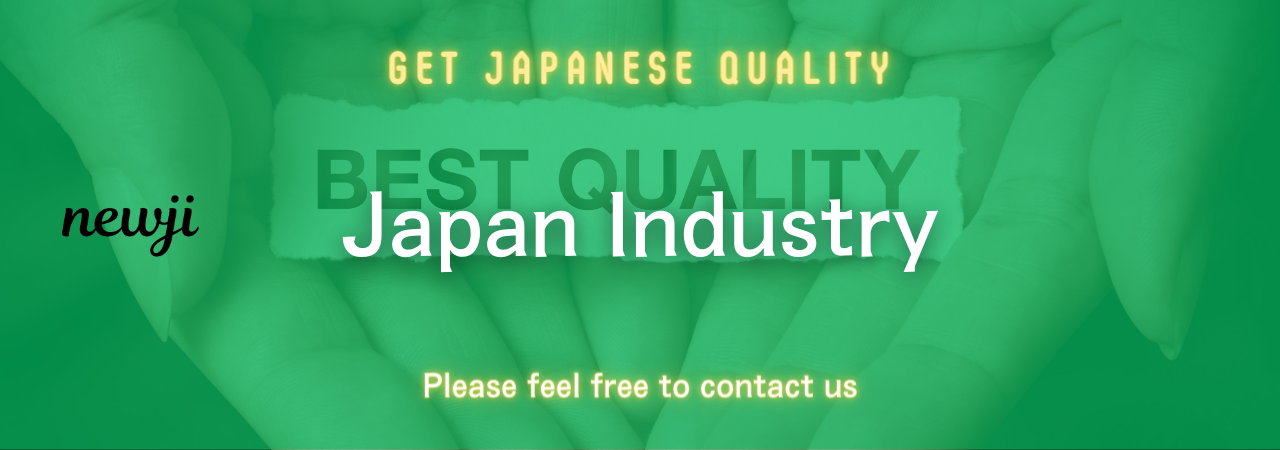
目次
Understanding Lead Time and Its Importance
Every business that relies on production knows the critical role of lead time in the supply chain process.
Lead time refers to the total time taken from placing an order to receiving the goods.
It affects the company’s ability to manage inventory, meet customer demands, and maintain operational efficiency.
Reducing lead time can lead to better customer satisfaction, lower costs, and improved agility.
The Impact of Long Lead Times
Long lead times can have several negative impacts.
It can cause excessive inventory holding costs and increase the risk of stockouts.
Furthermore, it may result in delays that frustrate customers, weaken loyalty, and lead to lost sales.
To avoid these pitfalls, companies should take proactive steps to streamline the procurement process.
Streamlining the Procurement Process
To reduce lead times, businesses need to optimize their procurement process.
This involves several strategic steps that focus on efficiency, communication, and technology.
1. Assess Current Procurement Procedures
The first step is a thorough assessment of current procurement procedures.
Understand where delays typically occur—whether it’s in vendor selection, order processing, or logistics.
Identify bottlenecks and areas that require improvement, using internal data and feedback from procurement staff.
2. Choose Reliable Suppliers
Selecting reliable suppliers is fundamental for reducing lead times.
Research and establish relationships with vendors known for timely deliveries and quality products.
It may involve diversifying the supplier base to reduce dependency on any single source.
3. Implement Vendor Management Software
Modern technology offers vendor management software solutions that streamline procurement functions.
These systems automate order placement, track shipments, and provide real-time updates.
They enhance transparency and communication, which are crucial for minimizing delays.
Effective Communication and Collaboration
4. Foster Strong Supplier Relationships
Building strong relationships with suppliers facilitates better understanding and cooperation, which can reduce lead times.
Communicate regularly and share relevant business information with them.
Consider strategic partnerships or agreements that can secure priority in production schedules.
5. Align Internal Teams
Ensure that all internal teams involved in procurement, from finance to warehouse management, are aligned and working towards common goals.
Effective cross-departmental communication can prevent misunderstandings and reduce processing delays.
Enhancing Inventory Management
6. Implement Just-In-Time Inventory
The Just-In-Time (JIT) inventory management approach reduces lead times by aligning orders with production schedules.
This minimizes excess inventory, reduces waste, and ensures that materials are available only when needed, directly impacting lead time reduction.
7. Forecast Demand Accurately
Accurate demand forecasting enables businesses to anticipate market needs, thus allowing proactive procurement planning.
Utilize data analytics to assess trends and predict demand, ensuring that you order products in an optimal time frame.
The Role of Technology in Reducing Lead Time
8. Embrace Automation
By automating repetitive tasks in the procurement process, companies can reduce administrative lead times.
Automation tools can handle order confirmations, invoice processing, and inventory counting, giving employees time to focus on value-added tasks.
9. Leverage Big Data
Implementing big data analytics provides insights into procurement trends and supplier performance.
It enables organizations to uncover inefficiencies and make data-driven decisions that streamline the procurement process.
Continual Improvement and Monitoring
10. Establish Key Performance Indicators (KPIs)
Define and monitor KPIs relevant to procurement and lead time reduction.
These may include metrics like order accuracy, supplier lead time, and inventory turnover ratios.
Regularly review performance against these indicators to identify new areas for improvement.
11. Solicit Feedback
Finally, encourage feedback from all stakeholders involved in the procurement chain.
Employees, suppliers, and customers can provide valuable insights into the effectiveness of the procurement process and offer suggestions for improvement.
Reducing lead time by streamlining the procurement process can greatly benefit companies seeking efficient and cost-effective operations.
Implementing the above steps creates a robust framework for managing the complexities of modern procurement.
By continuously improving and integrating technology, businesses can create a competitive advantage while meeting the evolving needs of their customers.
資料ダウンロード
QCD調達購買管理クラウド「newji」は、調達購買部門で必要なQCD管理全てを備えた、現場特化型兼クラウド型の今世紀最高の購買管理システムとなります。
ユーザー登録
調達購買業務の効率化だけでなく、システムを導入することで、コスト削減や製品・資材のステータス可視化のほか、属人化していた購買情報の共有化による内部不正防止や統制にも役立ちます。
NEWJI DX
製造業に特化したデジタルトランスフォーメーション(DX)の実現を目指す請負開発型のコンサルティングサービスです。AI、iPaaS、および先端の技術を駆使して、製造プロセスの効率化、業務効率化、チームワーク強化、コスト削減、品質向上を実現します。このサービスは、製造業の課題を深く理解し、それに対する最適なデジタルソリューションを提供することで、企業が持続的な成長とイノベーションを達成できるようサポートします。
オンライン講座
製造業、主に購買・調達部門にお勤めの方々に向けた情報を配信しております。
新任の方やベテランの方、管理職を対象とした幅広いコンテンツをご用意しております。
お問い合わせ
コストダウンが利益に直結する術だと理解していても、なかなか前に進めることができない状況。そんな時は、newjiのコストダウン自動化機能で大きく利益貢献しよう!
(Β版非公開)