- お役立ち記事
- Steps to Strengthen Collaboration Between Quality Control and Purchasing Departments
月間76,176名の
製造業ご担当者様が閲覧しています*
*2025年3月31日現在のGoogle Analyticsのデータより
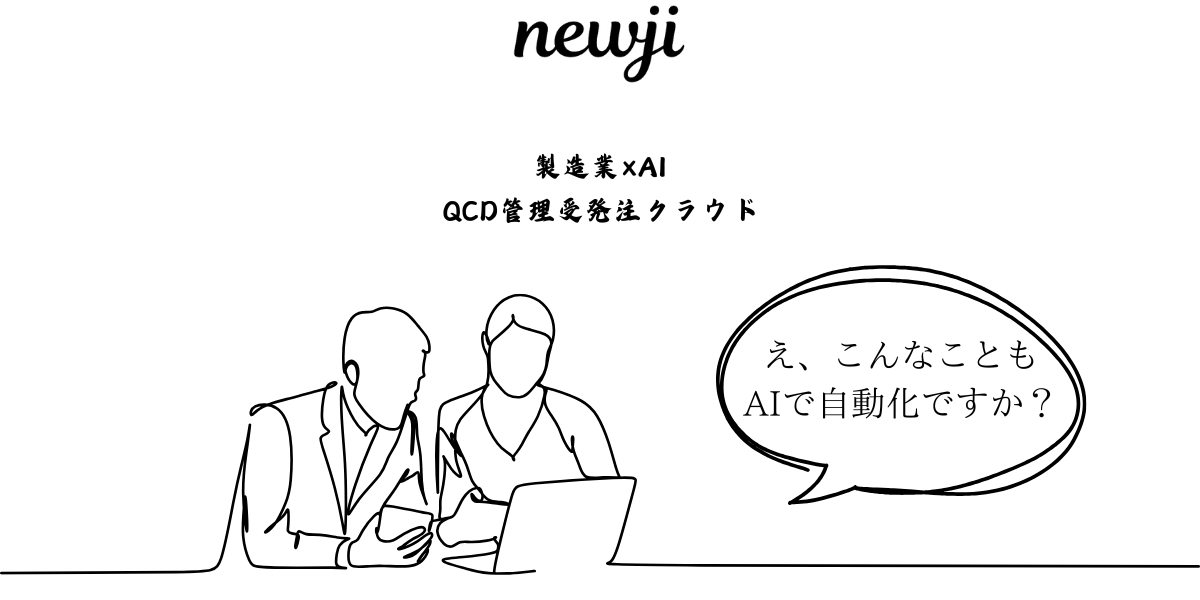
Steps to Strengthen Collaboration Between Quality Control and Purchasing Departments
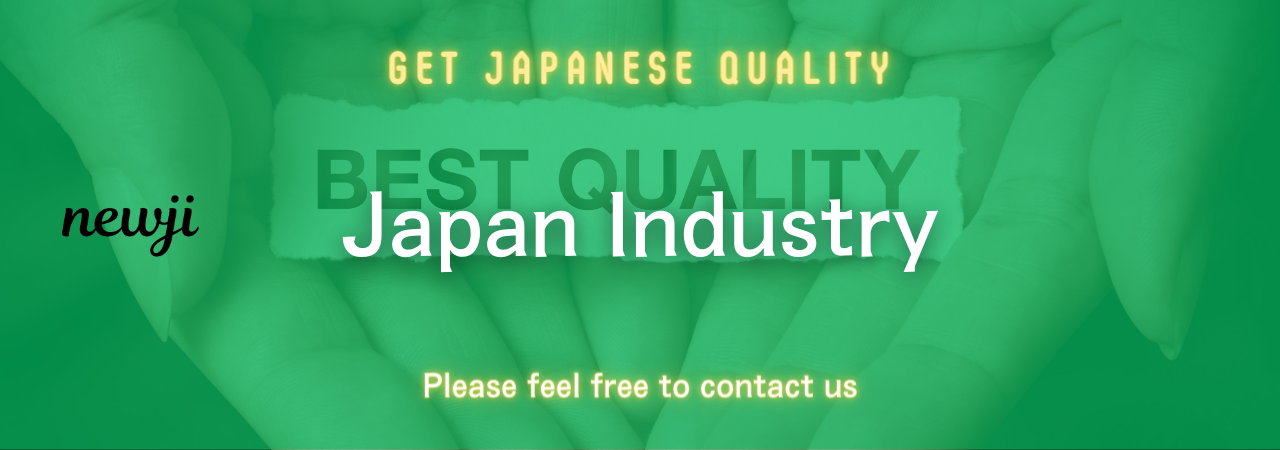
In today’s competitive business environment, strong internal collaboration between departments is essential to ensure efficiency, high product quality, and customer satisfaction.
One critical area where this collaboration can have a significant impact is between the Quality Control (QC) and Purchasing departments.
Working together effectively not only guarantees that the materials purchased meet desired quality standards but also helps in cost management and timely production.
Here, we will delve into some steps to strengthen collaboration between these two vital departments.
目次
Understanding Roles and Responsibilities
Before delving into strategies to enhance collaboration, it is crucial to understand the distinct roles and responsibilities of both the Quality Control and Purchasing departments.
Quality Control Department
The QC department focuses on ensuring that products and materials meet predefined quality standards.
They conduct inspections, audits, and tests to validate conformity and often set the quality criteria that purchased materials must satisfy.
Purchasing Department
On the other hand, the Purchasing department is responsible for acquiring materials, goods, and services needed for production and operations.
They negotiate with suppliers, manage inventory levels, and handle procurement processes to ensure the timely availability of quality materials.
Establishing Clear Communication Channels
Effective communication is the foundation of successful collaboration between departments.
Regular Meetings
Scheduling regular meetings between the QC and Purchasing departments can help bridge any communication gaps.
These meetings can be used to discuss ongoing issues, review supplier performance, and align on quality requirements.
Centralized Information Systems
Implementing a centralized information system where both departments can access and share data seamlessly will ensure everyone has real-time information and can act accordingly.
This system should include quality standards, inspection results, and supplier performance data.
Standardizing Quality Requirements
To avoid misunderstandings or discrepancies, it is essential to standardize quality requirements and ensure that both departments are on the same page.
Developing a Quality Manual
Creating a comprehensive quality manual that outlines all quality standards, inspection protocols, and criteria for materials can serve as a reference for both departments.
This manual should be regularly updated to keep up with any changes in quality requirements.
Training Sessions
Conducting joint training sessions where members from both departments learn about the quality requirements and procurement processes can foster a better understanding and improve collaboration.
Training should also include new updates or changes in standards to ensure continuous alignment.
Leveraging Technology and Tools
Utilizing the right tools and technologies can significantly enhance the collaboration between QC and Purchasing departments.
Quality Management Software (QMS)
Implementing Quality Management Software that both departments can access will help in tracking quality standards, inspection results, and supplier performance metrics.
A QMS can automate many processes, reduce errors, and improve overall efficiency.
Supplier Performance Dashboards
Using dashboards to monitor and review supplier performance in real-time can help Purchasing departments make informed decisions.
These dashboards can include metrics such as on-time delivery, defect rates, and compliance with quality standards.
Building Strong Supplier Relationships
Suppliers play a crucial role in the collaboration between QC and Purchasing departments.
Supplier Audits
Conducting regular supplier audits can help ensure that suppliers adhere to quality standards and contractual obligations.
Both QC and Purchasing departments should participate in these audits to get a comprehensive understanding of the supplier’s capabilities.
Feedback Loops
Establishing feedback loops where suppliers are informed about their performance, both positive and negative, can drive continuous improvement.
Feedback should be constructive and focus on areas where the supplier can enhance quality or efficiency.
Implementing Continuous Improvement Processes
Continuous improvement should be a core principle driving the collaboration between QC and Purchasing departments.
Root Cause Analysis
Whenever a quality issue arises, conducting a root cause analysis can help in identifying the underlying cause and implementing corrective actions.
Both departments should work together to address these issues and prevent recurrence.
Performance Reviews
Periodic performance reviews of both departments can help identify areas of improvement and recognize successes.
These reviews should include evaluations of how well the departments are collaborating and meeting their objectives.
Encouraging a Collaborative Culture
Creating a culture that encourages collaboration and open communication is vital.
Team Building Activities
Organizing team-building activities can help in fostering better relationships and understanding between members of the QC and Purchasing departments.
These activities can range from workshops and joint problem-solving sessions to social events.
Shared Goals and Objectives
Setting shared goals and objectives that both departments work towards can enhance collaboration.
These goals should focus on both quality and efficiency, ensuring that both departments align their efforts towards common objectives.
In conclusion, strengthening collaboration between Quality Control and Purchasing departments is essential for maintaining high quality and cost-effective operations.
By establishing clear communication channels, standardizing quality requirements, leveraging technology, building strong supplier relationships, implementing continuous improvement processes, and fostering a collaborative culture, businesses can achieve better alignment between these two critical departments.
This synergy will not only lead to better-quality products but also contribute to the overall success of the organization.
資料ダウンロード
QCD管理受発注クラウド「newji」は、受発注部門で必要なQCD管理全てを備えた、現場特化型兼クラウド型の今世紀最高の受発注管理システムとなります。
ユーザー登録
受発注業務の効率化だけでなく、システムを導入することで、コスト削減や製品・資材のステータス可視化のほか、属人化していた受発注情報の共有化による内部不正防止や統制にも役立ちます。
NEWJI DX
製造業に特化したデジタルトランスフォーメーション(DX)の実現を目指す請負開発型のコンサルティングサービスです。AI、iPaaS、および先端の技術を駆使して、製造プロセスの効率化、業務効率化、チームワーク強化、コスト削減、品質向上を実現します。このサービスは、製造業の課題を深く理解し、それに対する最適なデジタルソリューションを提供することで、企業が持続的な成長とイノベーションを達成できるようサポートします。
製造業ニュース解説
製造業、主に購買・調達部門にお勤めの方々に向けた情報を配信しております。
新任の方やベテランの方、管理職を対象とした幅広いコンテンツをご用意しております。
お問い合わせ
コストダウンが利益に直結する術だと理解していても、なかなか前に進めることができない状況。そんな時は、newjiのコストダウン自動化機能で大きく利益貢献しよう!
(β版非公開)