- お役立ち記事
- Strategic logistics design method for purchasing department to minimize transportation costs
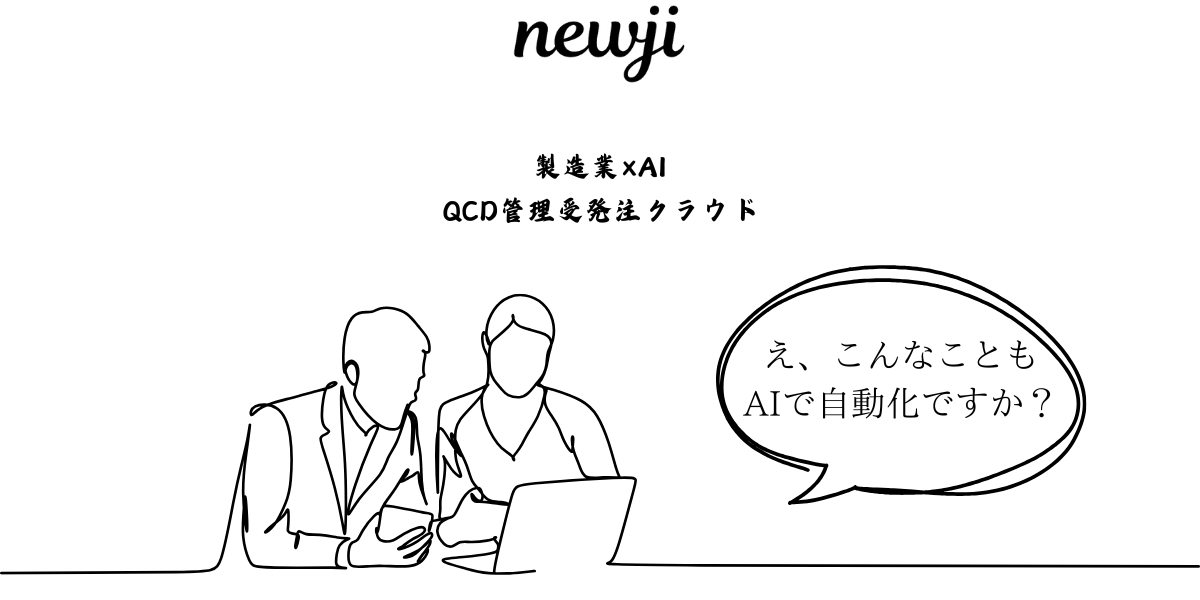
Strategic logistics design method for purchasing department to minimize transportation costs
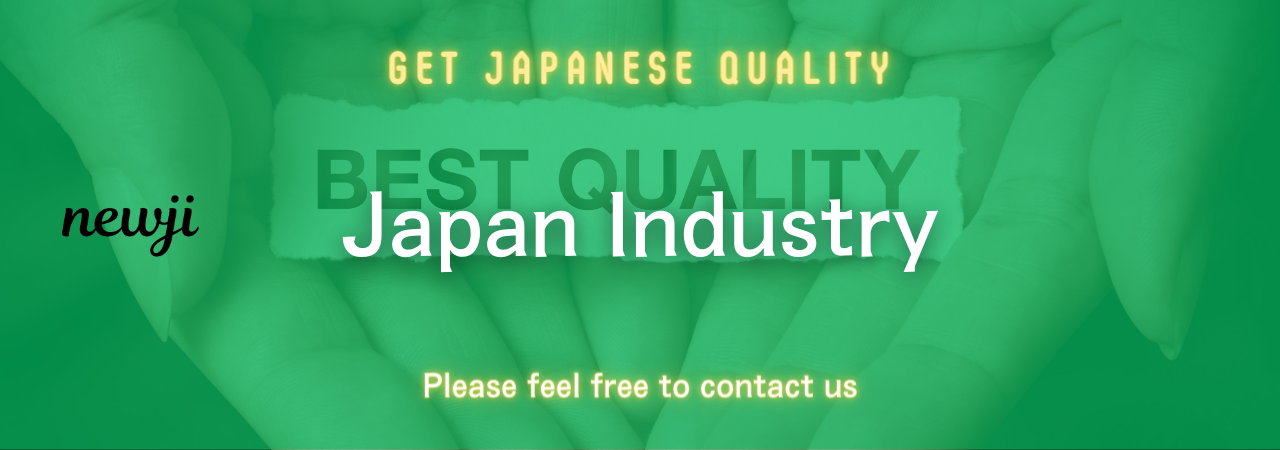
目次
Understanding Strategic Logistics Design
Logistics is a critical aspect of any business that deals with physical goods.
Effective logistics management ensures that products are delivered to the right place, at the right time, and in the most cost-effective manner.
For purchasing departments, minimizing transportation costs is an essential objective to improve overall efficiency and profitability.
The strategic logistics design involves planning and implementing a logistics network that aligns with the company’s goals.
It requires careful analysis of various factors such as location, transportation modes, inventory management, and supplier relationships.
By optimizing these elements, businesses can significantly reduce their transportation costs and improve service levels.
Components of Strategic Logistics Design
Network Design
The first step in strategic logistics design is to create an efficient network design.
This involves determining the best locations for warehouses, distribution centers, and suppliers.
An optimal network design considers factors like proximity to major markets, transportation infrastructure, and cost of operations.
A well-planned network design helps in reducing transportation time and costs.
It also allows for more responsive and flexible logistics operations.
Advanced tools and software can assist in simulating different network scenarios, helping companies choose the best design.
Transportation Mode Selection
Selecting the right mode of transportation is crucial for minimizing costs.
Each mode—be it road, rail, air, or sea—has its own advantages and disadvantages.
For example, while air transport is fast, it is also expensive.
Conversely, sea transport is cost-effective but slower.
Companies need to evaluate the specific needs of their shipments, considering factors like delivery time, cost, and reliability.
A mixed-mode approach can often provide the best solution, optimizing cost and efficiency based on shipment characteristics.
Inventory Management
Effective inventory management is a key component of logistics design.
It involves balancing the cost of carrying inventory with the need to meet customer demand.
By optimizing inventory levels, businesses can reduce storage costs and transportation expenses.
Techniques such as Just-In-Time (JIT) and Economic Order Quantity (EOQ) help in finding the right balance.
Incorporating technology solutions like warehouse management systems (WMS) can further enhance inventory accuracy and efficiency.
Supplier Relationship Management
Building strong relationships with suppliers is crucial for strategic logistics design.
Collaborating closely with suppliers can lead to better pricing, more reliable deliveries, and improved overall efficiency.
Effective communication and partnership can also lead to innovative solutions such as shared transportation networks or consignment inventory arrangements, reducing costs for both parties.
Steps to Implement Strategic Logistics Design
Analysis and Assessment
Begin by conducting a thorough analysis of the current logistics operations.
Identify areas where costs can be reduced or efficiency can be improved.
This may involve studying transportation routes, inventory levels, warehouse locations, and suppliers.
Setting Objectives
Define clear objectives for what you want to achieve with your strategic logistics design.
This could include reducing transportation costs by a specific percentage, improving delivery times, or enhancing service quality.
Developing a Plan
Based on the analysis and objectives, develop a logistics plan that outlines how you will achieve your goals.
This should include details on network design, transportation modes, inventory management strategies, and supplier collaborations.
Implementation
Implement the logistics plan by coordinating with all relevant departments and stakeholders.
Ensure that everyone understands their role and the expected outcomes.
Utilize technology and tools for efficient execution and monitoring.
Monitoring and Continuous Improvement
Once implemented, continuously monitor the logistics operations to measure the effectiveness of the strategic design.
Collect data, analyze performance, and identify areas for improvement.
Engage in regular reviews and make necessary adjustments to stay aligned with business objectives.
Benefits of Strategic Logistics Design
Implementing a strategic logistics design can yield numerous benefits for the purchasing department and the company as a whole.
Cost Reduction
One of the most significant benefits is the reduction in overall transportation costs.
By optimizing routes, selecting the right transportation modes, and improving inventory management, businesses can cut expenses significantly.
Improved Efficiency
A well-designed logistics strategy leads to improved operational efficiency.
This results in faster delivery times, reduced errors, and better utilization of resources.
Enhanced Customer Satisfaction
Delivering products on time and in excellent condition boosts customer satisfaction, leading to repeat business and increased sales.
Competitive Advantage
Companies with strategic logistics have a competitive edge in the marketplace.
They can offer better service levels at lower costs, making them more attractive to customers.
Conclusion
A well-crafted strategic logistics design is essential for any purchasing department aiming to minimize transportation costs.
By understanding the components of logistics design and following an effective implementation approach, businesses can gain significant cost savings and improve their overall supply chain performance.
Continuously monitoring logistics operations and making data-driven adjustments will ensure long-term success and sustainability in the competitive market landscape.
資料ダウンロード
QCD調達購買管理クラウド「newji」は、調達購買部門で必要なQCD管理全てを備えた、現場特化型兼クラウド型の今世紀最高の購買管理システムとなります。
ユーザー登録
調達購買業務の効率化だけでなく、システムを導入することで、コスト削減や製品・資材のステータス可視化のほか、属人化していた購買情報の共有化による内部不正防止や統制にも役立ちます。
NEWJI DX
製造業に特化したデジタルトランスフォーメーション(DX)の実現を目指す請負開発型のコンサルティングサービスです。AI、iPaaS、および先端の技術を駆使して、製造プロセスの効率化、業務効率化、チームワーク強化、コスト削減、品質向上を実現します。このサービスは、製造業の課題を深く理解し、それに対する最適なデジタルソリューションを提供することで、企業が持続的な成長とイノベーションを達成できるようサポートします。
オンライン講座
製造業、主に購買・調達部門にお勤めの方々に向けた情報を配信しております。
新任の方やベテランの方、管理職を対象とした幅広いコンテンツをご用意しております。
お問い合わせ
コストダウンが利益に直結する術だと理解していても、なかなか前に進めることができない状況。そんな時は、newjiのコストダウン自動化機能で大きく利益貢献しよう!
(Β版非公開)