- お役立ち記事
- Strategies for SMEs to Gain Competitiveness with New Milling Technologies
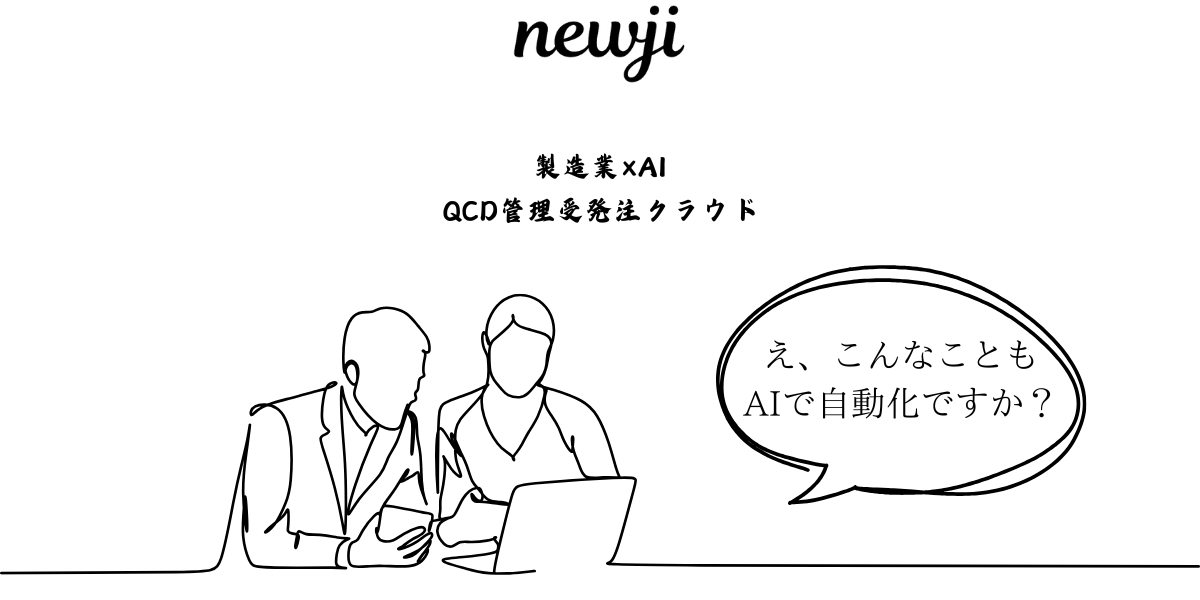
Strategies for SMEs to Gain Competitiveness with New Milling Technologies
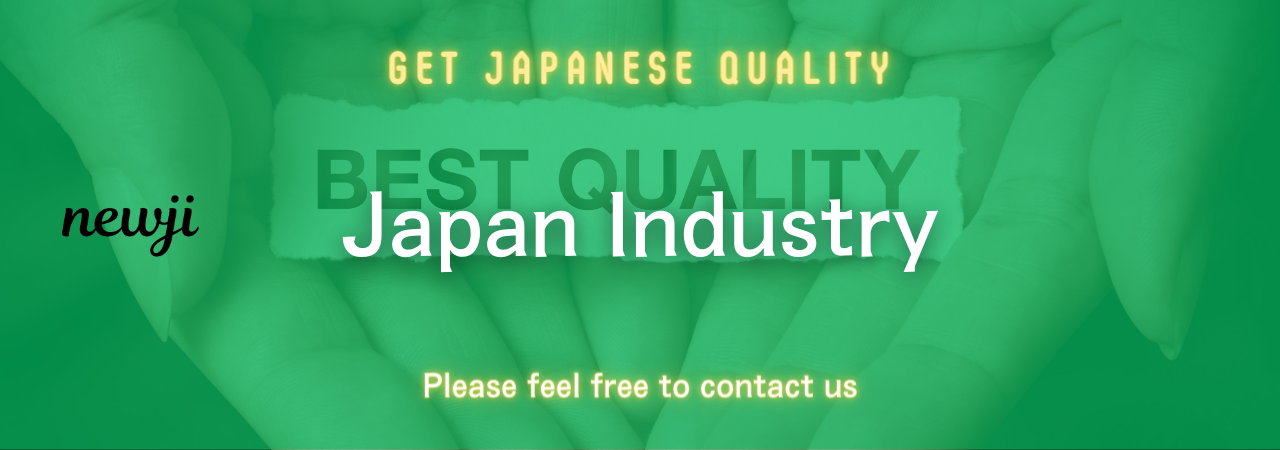
Small and medium-sized enterprises (SMEs) often face significant challenges in remaining competitive, especially in industries that rely heavily on precision and efficiency, such as manufacturing.
One effective way for these businesses to gain a competitive edge is by adopting new milling technologies.
These innovations can improve productivity, lower costs, and enhance product quality.
In this article, we will explore several strategies that can help SMEs leverage new milling technologies to boost their competitiveness.
目次
Understanding the Importance of Milling Technologies
Milling technologies are vital in many manufacturing processes.
They involve the machining of materials using rotary cutters, which helps in shaping, drilling, and cutting to precise measurements.
Historically, these processes could be time-consuming and prone to human error.
However, advancements in technology have introduced more efficient and accurate milling machines.
Advantages of Modern Milling Technologies
Modern milling technologies offer several benefits:
1. **Increased Precision**: Advanced CNC (Computer Numerical Control) machines provide exceptional accuracy, reducing the likelihood of errors.
2. **Higher Productivity**: Automated milling machines can operate continuously with minimal human intervention, significantly boosting production rates.
3. **Cost Savings**: Reduced waste and lower labor costs contribute to overall savings.
4. **Enhanced Versatility**: Modern milling machines can work with a variety of materials and perform multiple functions, making them versatile tools in any manufacturing setting.
Steps to Implement New Milling Technologies
Implementing new milling technologies requires careful planning and execution.
Here are some critical steps to consider:
1. Assess Your Current Capabilities
Before adopting new technologies, it’s essential to evaluate your current milling capabilities.
Identify areas where improvements are needed, such as precision, speed, or material handling.
Understanding your existing setup will help you determine what type of new technology will best address your needs.
2. Research and Choose the Right Technology
CNC milling machines come in various types and configurations.
Research the options available and choose the one that aligns with your business goals.
Consider factors like machine size, spindle speed, and compatibility with the materials you typically work with.
Additionally, look for machines that offer easy integration with your current processes and systems.
3. Budget and Financial Planning
Investing in new milling technologies can be costly.
However, it’s an investment that can result in long-term savings and increased revenue.
Work on a comprehensive budget plan that includes the cost of the machine, installation, training, and maintenance.
Also, explore financing options, grants, or incentives that may be available for SMEs investing in advanced manufacturing technologies.
4. Train Your Workforce
New technologies often require new skill sets.
Ensure that your employees receive adequate training to operate and maintain the new machinery.
Invest in training programs or workshops, and consider hiring skilled operators if necessary.
A well-trained workforce is crucial for maximizing the benefits of new milling technologies.
Optimizing the Use of Milling Technologies
Once you have implemented new milling technologies, it’s important to optimize their use to gain the maximum benefits.
Here are some strategies for optimization:
1. Routine Maintenance
Regular maintenance is essential to keep the machines running smoothly and efficiently.
Develop a maintenance schedule that includes routine inspections, cleaning, and parts replacement.
Proper maintenance not only prolongs the lifespan of the machines but also prevents unexpected breakdowns.
2. Monitor Performance Metrics
Use performance metrics to monitor the efficiency and productivity of your milling processes.
Metrics such as cycle time, downtime, and defect rates can provide valuable insights into areas that need improvement.
Implementing a robust monitoring system helps in making data-driven decisions to enhance performance.
3. Integrate with Other Technologies
For optimum performance, integrate your milling machines with other technologies such as ERP (Enterprise Resource Planning) systems and IoT (Internet of Things) devices.
This integration enables seamless data exchange and better coordination between different manufacturing processes.
It also helps in automating the workflow and reducing manual intervention.
4. Continuous Improvement
Adopt a culture of continuous improvement within your organization.
Encourage feedback from operators and other stakeholders, and use that feedback to make ongoing enhancements to your milling processes.
Stay updated with the latest advancements in milling technologies to ensure that your business remains competitive.
Case Studies: Successful Implementation of Milling Technologies
To further understand the impact of new milling technologies, let’s look at some real-world examples of SMEs that have successfully adopted these innovations.
Case Study 1: XYZ Manufacturing
XYZ Manufacturing, a small business specializing in custom metal parts, implemented high-speed CNC milling machines.
After the adoption, they saw a 30% increase in production efficiency and a 20% reduction in material waste.
The precision of the new machines also enabled them to enter new markets that require tighter tolerances.
Case Study 2: ABC Auto Parts
ABC Auto Parts, a medium-sized enterprise, integrated their new milling machines with IoT devices.
This integration allowed for real-time monitoring and predictive maintenance.
As a result, they experienced a 15% reduction in downtime and increased their overall equipment effectiveness by 25%.
Conclusion
For SMEs in the manufacturing sector, gaining a competitive edge is crucial for growth and sustainability.
New milling technologies present an excellent opportunity to improve precision, productivity, and cost-efficiency.
By carefully assessing current capabilities, choosing the right technology, planning financials, and training the workforce, SMEs can successfully implement these advanced milling machines.
Optimizing their use through regular maintenance, performance monitoring, and integration with other technologies will further enhance the benefits.
Real-world examples demonstrate that the adoption of new milling technologies can lead to significant improvements in efficiency and profitability.
So, take the plunge and explore how these innovative solutions can transform your business operations.
資料ダウンロード
QCD調達購買管理クラウド「newji」は、調達購買部門で必要なQCD管理全てを備えた、現場特化型兼クラウド型の今世紀最高の購買管理システムとなります。
ユーザー登録
調達購買業務の効率化だけでなく、システムを導入することで、コスト削減や製品・資材のステータス可視化のほか、属人化していた購買情報の共有化による内部不正防止や統制にも役立ちます。
NEWJI DX
製造業に特化したデジタルトランスフォーメーション(DX)の実現を目指す請負開発型のコンサルティングサービスです。AI、iPaaS、および先端の技術を駆使して、製造プロセスの効率化、業務効率化、チームワーク強化、コスト削減、品質向上を実現します。このサービスは、製造業の課題を深く理解し、それに対する最適なデジタルソリューションを提供することで、企業が持続的な成長とイノベーションを達成できるようサポートします。
オンライン講座
製造業、主に購買・調達部門にお勤めの方々に向けた情報を配信しております。
新任の方やベテランの方、管理職を対象とした幅広いコンテンツをご用意しております。
お問い合わせ
コストダウンが利益に直結する術だと理解していても、なかなか前に進めることができない状況。そんな時は、newjiのコストダウン自動化機能で大きく利益貢献しよう!
(Β版非公開)