- お役立ち記事
- Strategies for SMEs to Improve Efficiency in Grinding
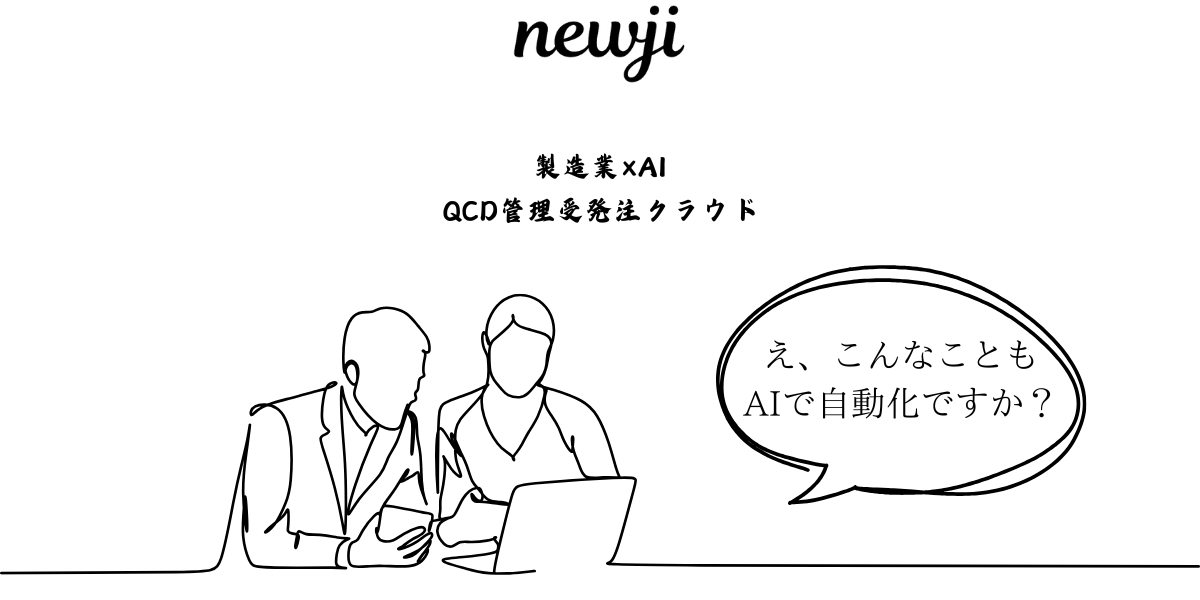
Strategies for SMEs to Improve Efficiency in Grinding
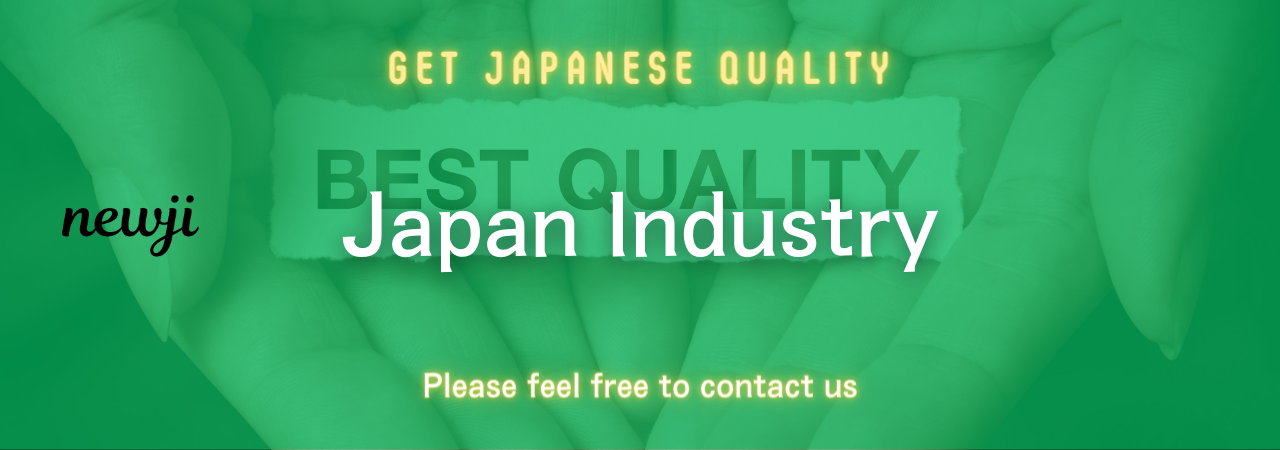
Efficient grinding is crucial for small and medium-sized enterprises (SMEs) in the manufacturing sector.
Implementing effective strategies can lead to significant improvements in productivity, cost savings, and product quality.
This article delves into practical strategies that SMEs can adopt to enhance their grinding processes.
By doing so, businesses can maintain a competitive edge in the market while maximizing resource utilization.
目次
Understand Your Grinding Needs
Before integrating any new strategies, it’s critical to understand your specific grinding requirements.
Every SME has different needs based on the type of material they’re working with and the desired end product.
Start by conducting a thorough analysis of your current grinding processes.
Identify the materials you grind, the volume of production, and the specific characteristics required for your final products.
Evaluate Grinding Equipment
One of the first steps in improving grinding efficiency is to evaluate the equipment in use.
Not all grinding machines are created equal.
Some are better suited to specific materials and tasks.
Ensure that the grinders you have on your shop floor are the best fit for your production needs.
If you discover that your equipment is outdated or not optimally suited, consider investing in newer, more specialized machinery.
Regular Maintenance of Equipment
Regular maintenance is essential to keep grinding equipment running smoothly.
Scheduled maintenance checks can prevent unexpected downtimes and prolong the life of your machinery.
Develop a maintenance schedule that includes cleaning, lubrication, and part replacements.
Train your staff on detecting early signs of wear and tear that might affect performance.
Having a proactive approach to maintenance ensures that the grinding process remains uninterrupted and efficient.
Maintain Grinding Wheels
The grinding wheel is an integral part of the equipment and deserves special attention.
Ensure they are maintained correctly by regular dressing and balancing.
Using a well-maintained grinding wheel can significantly improve grinding precision and efficiency.
Change the wheels promptly if they show signs of wear or damage.
A poorly maintained grinding wheel can lead to subpar product quality, increased waste, and higher operational costs.
Optimize Grinding Processes
Optimization of grinding processes can lead to substantial improvements in efficiency.
Analyze your current processes for any possible bottlenecks or inefficiencies.
Identify areas where improvements can be made, such as speed adjustments, feed rate changes, or incorporating automation.
Small tweaks in the process can lead to significant improvements in overall efficiency.
Use the Right Cooling and Lubrication
Effective cooling and lubrication are necessary during grinding to manage heat and friction.
Insufficient cooling can lead to overheating, which can damage the material and tools.
Select the appropriate coolant and lubrication fluids based on the material and grinding process.
Implement proper delivery systems to ensure that the fluids reach the desired spots efficiently.
This practice can prolong tool life, enhance product quality, and improve overall efficiency.
Invest in Staff Training
Human error is one of the leading causes of inefficiencies in manufacturing processes.
Invest in regular staff training programs to ensure your team is knowledgeable about the latest grinding techniques and best practices.
An educated workforce is better equipped to handle the intricacies of grinding operations.
They can troubleshoot issues effectively, leading to reduced downtime and improved productivity.
Encourage Continuous Improvement
Foster a culture of continuous improvement within your SME.
Encourage your team to provide feedback on existing processes and suggest improvements.
Implementing a system for continuous evaluation and improvement can lead to incremental gains in efficiency over time.
Regular performance reviews and feedback sessions can help in identifying areas that need attention and devising strategies for improvement.
Leverage Technology and Innovation
Adopting modern technologies and innovative solutions can tremendously impact grinding efficiency.
Consider integrating computerized numerical control (CNC) systems into your grinding operations.
CNC systems offer precision, repeatability, and efficiency that manual processes cannot match.
Investing in automated grinding solutions can reduce human error and increase production rates.
Implement Data Analytics
Data analytics can play a crucial role in optimizing grinding processes.
Collect data from your grinding operations, such as cycle times, tool wear, and production rates.
Analyze this data to identify patterns and areas where efficiency can be improved.
Implementing data-driven decision-making can lead to more effective strategies and sustained improvements.
Reduce Waste and Rework
Minimizing waste and rework are essential strategies for enhancing grinding efficiency.
Establish quality control measures to ensure that each piece produced meets the required standards.
By doing so, you can reduce the need for reworking defective pieces, which consumes additional time and resources.
Utilize precise measurement tools and inspection techniques to maintain high-quality standards throughout the process.
Embrace Lean Manufacturing Principles
Lean manufacturing principles can be beneficial in reducing waste and improving efficiencies.
They focus on creating more value with fewer resources by identifying and eliminating non-value-added activities.
Implementing lean practices in your grinding processes can streamline operations, improve workflow, and reduce unnecessary steps.
This approach can lead to significant time and cost savings for your SME.
Conclusion
Improving grinding efficiency is crucial for SMEs to remain competitive in the manufacturing industry.
By understanding specific grinding needs, maintaining equipment, optimizing processes, investing in staff training, and leveraging technology, SMEs can achieve significant improvements.
Additionally, reducing waste and embracing lean manufacturing principles further boosts efficiency.
Implementing these strategies can lead to enhanced productivity, cost savings, and better product quality, positioning SMEs for long-term success.
Incorporating these strategies into daily operations can create a more streamlined, efficient, and productive grinding process.
資料ダウンロード
QCD調達購買管理クラウド「newji」は、調達購買部門で必要なQCD管理全てを備えた、現場特化型兼クラウド型の今世紀最高の購買管理システムとなります。
ユーザー登録
調達購買業務の効率化だけでなく、システムを導入することで、コスト削減や製品・資材のステータス可視化のほか、属人化していた購買情報の共有化による内部不正防止や統制にも役立ちます。
NEWJI DX
製造業に特化したデジタルトランスフォーメーション(DX)の実現を目指す請負開発型のコンサルティングサービスです。AI、iPaaS、および先端の技術を駆使して、製造プロセスの効率化、業務効率化、チームワーク強化、コスト削減、品質向上を実現します。このサービスは、製造業の課題を深く理解し、それに対する最適なデジタルソリューションを提供することで、企業が持続的な成長とイノベーションを達成できるようサポートします。
オンライン講座
製造業、主に購買・調達部門にお勤めの方々に向けた情報を配信しております。
新任の方やベテランの方、管理職を対象とした幅広いコンテンツをご用意しております。
お問い合わせ
コストダウンが利益に直結する術だと理解していても、なかなか前に進めることができない状況。そんな時は、newjiのコストダウン自動化機能で大きく利益貢献しよう!
(Β版非公開)