- お役立ち記事
- Strategies for Strengthening Product Quality Assurance with QC Process Charts
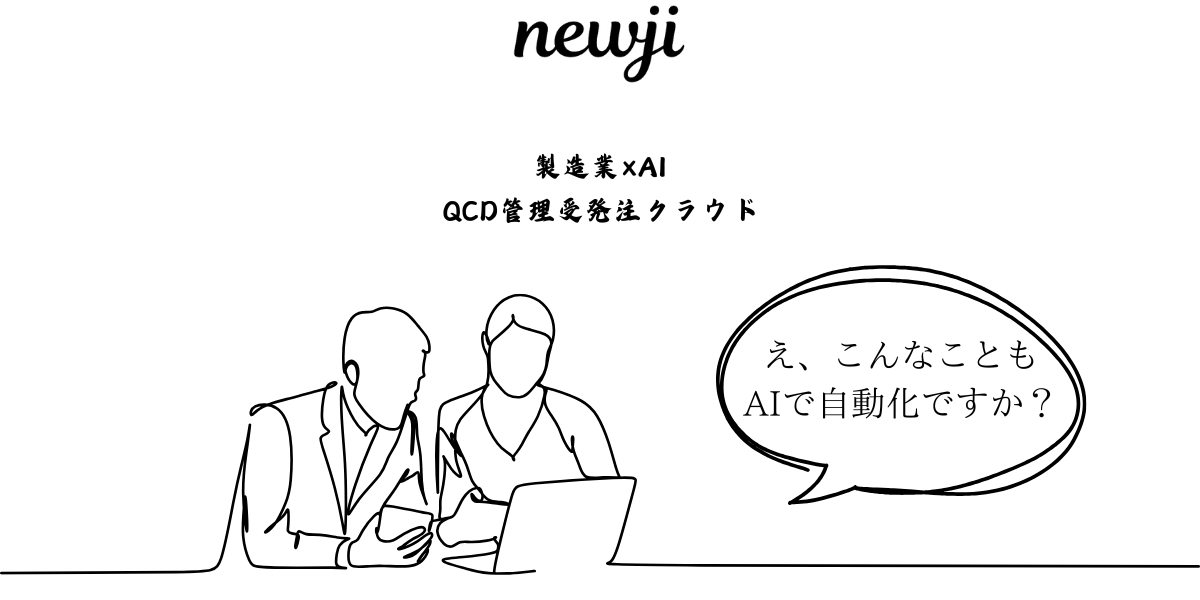
Strategies for Strengthening Product Quality Assurance with QC Process Charts
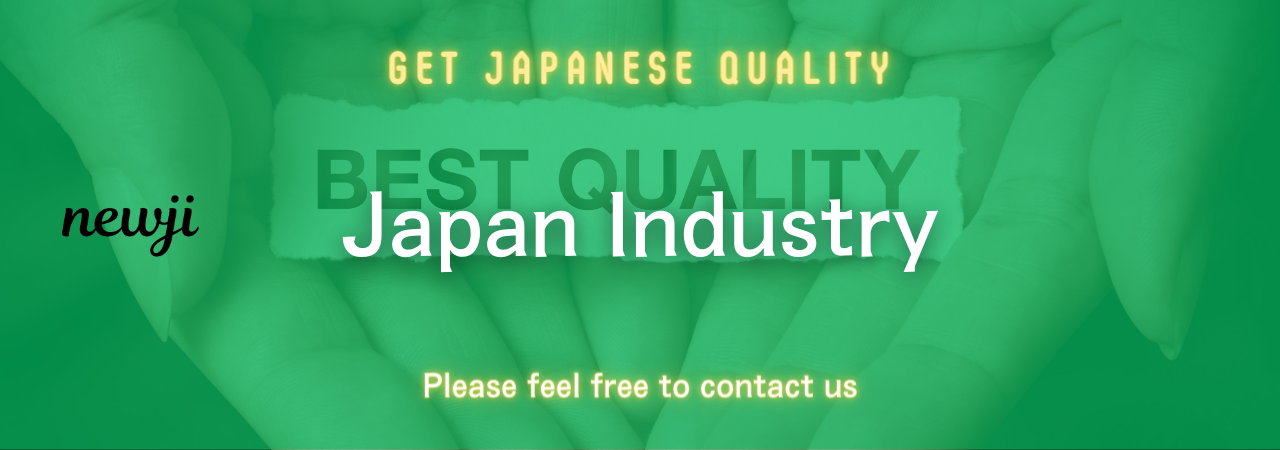
目次
Understanding Quality Assurance and Its Importance
Quality assurance (QA) is an essential process in any industry that ensures products meet specified standards and customer expectations.
It involves systematic procedures aimed at preventing mistakes or defects in manufactured products.
QA is crucial as it helps build consumer trust, ensures compliance with regulatory standards, and minimizes the costs associated with product failures.
A strong QA process helps a company maintain its reputation and competitive edge.
What Are QC Process Charts?
Quality Control (QC) process charts are vital tools used within the QA framework.
These charts are graphical representations that help monitor and control the quality of manufacturing processes.
By utilizing QC charts, organizations can visualize variations in processes and products, highlighting areas needing improvement and ensuring consistency in quality.
There are different types of QC charts, including control charts, histograms, Pareto charts, and cause-and-effect diagrams.
Control charts, for instance, depict data over time, allowing the identification of trends and potential issues before they escalate.
Each type of chart serves a specific purpose in analyzing and improving quality.
Steps to Implement QC Process Charts
Implementing QC process charts requires a strategic approach to maximize their benefit.
The following steps provide a guideline for effectively incorporating these charts into your QA strategy:
Identify Key Processes
The first step is to identify critical processes that directly impact product quality.
Focus on areas where deviations can lead to significant defects or where improvements will have the greatest effect.
Once these processes are identified, you can then decide the type of QC chart that will be most beneficial.
Collect Data
For QC charts to be effective, accurate and comprehensive data collection is necessary.
Collect data regarding various metrics such as product dimensions, temperatures, or output rates.
Consistency in data collection ensures reliability in your QC charts, leading to sound decision-making.
Select the Appropriate QC Chart
Different QC charts serve different purposes, so selecting the right type for your data is critical.
For time-related data analysis, control charts are highly effective.
Pareto charts help prioritize issues by distinguishing the most common defects.
Choose the chart that best suits your analysis needs and objectives.
Analyze and Interpret the Data
Once data is plotted on the QC chart, analyze it to identify patterns and areas of concern.
Interpret the chart to determine if processes are within control limits and investigate any outliers or shifts in trends.
Clear interpretation helps pinpoint root causes and guides corrective actions.
Implement Improvements
Based on the analysis, implement necessary changes to correct deviations and enhance quality.
Improvements can involve adjusting manufacturing processes, retraining staff, or redesigning product components.
Monitor the effectiveness of these changes using subsequent QC charts to ensure desired improvements are achieved.
Challenges in Using QC Process Charts
Although QC process charts are valuable, they come with their own set of challenges:
Data Accuracy
The effectiveness of QC charts heavily relies on the accuracy of the data collected.
Inaccurate or incomplete data can lead to erroneous interpretations and ineffective corrective actions.
Complexity
Interpreting QC charts can sometimes be complex, requiring specialized knowledge and training.
Ensuring staff are proficient in analyzing these charts is vital for effective QA processes.
Resistance to Change
Improving quality often necessitates change, which can be met with resistance from employees accustomed to existing processes.
Effective change management strategies are essential to mitigate resistance and promote a culture focused on quality.
Benefits of Strengthening Product Quality Assurance
By effectively using QC process charts, organizations can significantly enhance their QA efforts.
Benefits include:
Improved Product Quality
With clear insights into quality issues, organizations can produce higher-quality products, reducing defects and customer complaints.
This leads to increased customer satisfaction and loyalty.
Cost Reduction
Identifying quality issues early in the production process saves costs associated with rework, scrap, and warranty claims.
A proactive approach often costs less than reactive measures after defects occur.
Regulatory Compliance
Consistent product quality ensures adherence to industry standards and regulations, avoiding legal repercussions and potential fines.
Competitive Advantage
High-quality products differentiate a company from competitors, often allowing for premium pricing.
A strong reputation for quality can enhance a company’s brand and market position.
Conclusion
Strengthening product quality assurance through the strategic use of QC process charts is integral for companies aiming to deliver high-quality products consistently.
By visualizing process variations and identifying opportunities for improvement, organizations can proactively address quality issues.
Successfully implementing these strategies results in improved product quality, cost savings, and a solid reputation in the marketplace.
As industries grow ever more competitive, prioritizing quality assurance is not only beneficial but essential.
資料ダウンロード
QCD調達購買管理クラウド「newji」は、調達購買部門で必要なQCD管理全てを備えた、現場特化型兼クラウド型の今世紀最高の購買管理システムとなります。
ユーザー登録
調達購買業務の効率化だけでなく、システムを導入することで、コスト削減や製品・資材のステータス可視化のほか、属人化していた購買情報の共有化による内部不正防止や統制にも役立ちます。
NEWJI DX
製造業に特化したデジタルトランスフォーメーション(DX)の実現を目指す請負開発型のコンサルティングサービスです。AI、iPaaS、および先端の技術を駆使して、製造プロセスの効率化、業務効率化、チームワーク強化、コスト削減、品質向上を実現します。このサービスは、製造業の課題を深く理解し、それに対する最適なデジタルソリューションを提供することで、企業が持続的な成長とイノベーションを達成できるようサポートします。
オンライン講座
製造業、主に購買・調達部門にお勤めの方々に向けた情報を配信しております。
新任の方やベテランの方、管理職を対象とした幅広いコンテンツをご用意しております。
お問い合わせ
コストダウンが利益に直結する術だと理解していても、なかなか前に進めることができない状況。そんな時は、newjiのコストダウン自動化機能で大きく利益貢献しよう!
(Β版非公開)