- お役立ち記事
- Strategies for the manufacturing industry to manage working hours and improve equipment utilization
月間77,185名の
製造業ご担当者様が閲覧しています*
*2025年2月28日現在のGoogle Analyticsのデータより
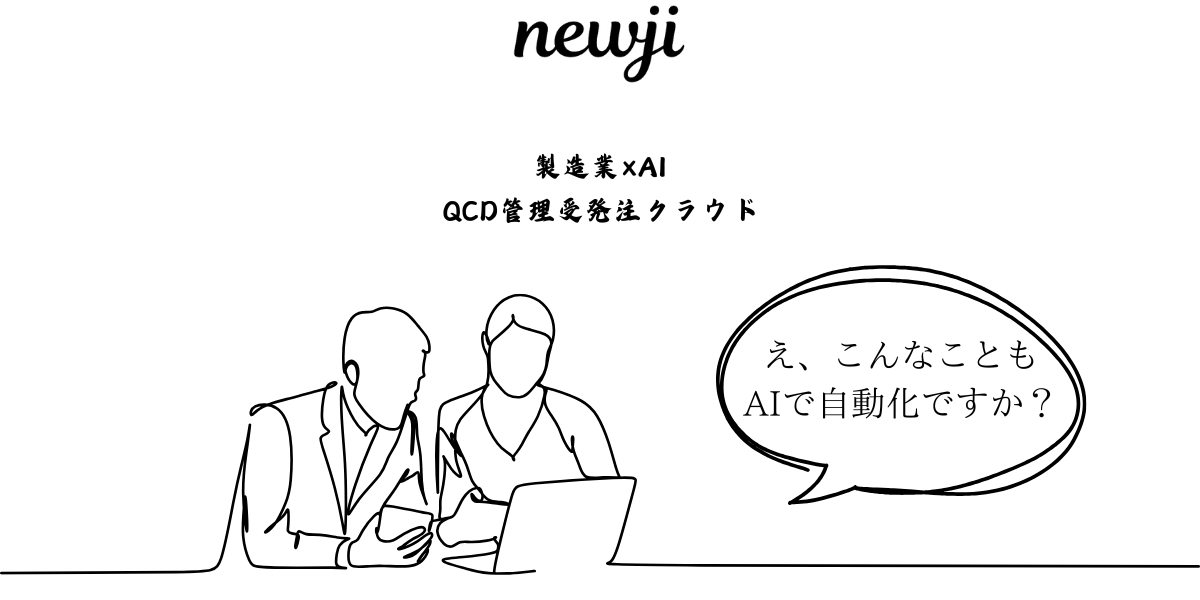
Strategies for the manufacturing industry to manage working hours and improve equipment utilization
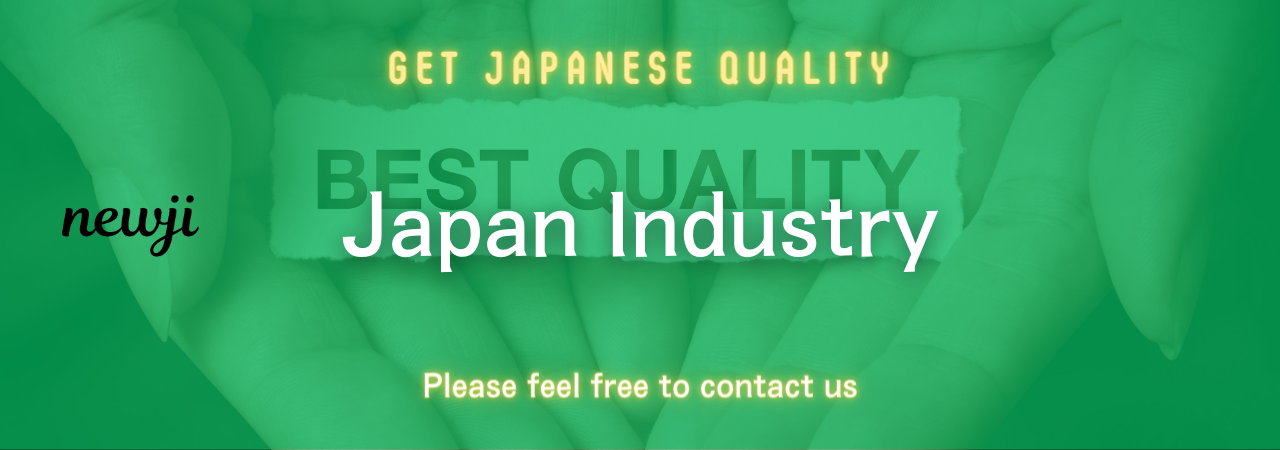
目次
Understanding the Importance of Working Hours Management
Managing working hours effectively in the manufacturing industry is crucial for maximizing productivity and ensuring smooth operations.
In a sector where efficiency can greatly influence profitability, understanding how to allocate and utilize time is essential.
Proper management of working hours helps not only in boosting production but also in enhancing employee satisfaction and overall operational efficiency.
When working hours are managed well, employees are less likely to feel overwhelmed, leading to a healthier work environment and reduced turnover rates.
This also ensures that all machinery and equipment get the attention they need, reducing downtime, and subsequently, losses.
Staggering Shifts for Enhanced Productivity
One effective strategy for managing working hours involves staggering shifts among workers.
This approach allows certain teams to cover different times of the day, ensuring that the manufacturing process continues without interruptions.
By staggering shifts, businesses can meet demand spikes more efficiently and reduce idle time for equipment.
It also allows managers to plan maintenance during off-peak hours, increasing equipment longevity and utilization.
Furthermore, staggered shifts can better accommodate employee needs, offering them flexibility that can lead to improved output and morale.
Utilizing Shift Rotation
Shift rotation is another strategy that enhances equipment utilization by distributing workload evenly among employees.
Rotating shifts help in preventing skill stagnation, as employees gain exposure to different tasks, building a more versatile workforce.
This practice can effectively reduce operational strain and prevent any single piece of equipment from being overused, preserving its functionality over time.
Moreover, shift rotation can lead to the detection of equipment inefficiencies sooner, as fresh eyes can often spot issues that routine may overlook.
Incorporating Technology and Automation
Implementing advanced technologies and automation in the manufacturing process is key to improving working hours management.
These technologies can process real-time data to help managers make informed decisions about shift planning and equipment use.
Automation reduces the need for human intervention in repetitive tasks, allowing employees to focus on more strategic roles.
This not only optimizes the labor force but also ensures that machinery is utilized more effectively, as automated systems can run continuously without downtime.
Monitor systems and software can track equipment performance around the clock, alerting management to potential issues before they escalate.
The Role of Internet of Things (IoT)
The Internet of Things (IoT) is particularly beneficial in enhancing working hours management.
IoT-enabled devices offer insights into equipment performance, helping to streamline operations and foresee maintenance needs.
With IoT sensors and devices, data about production processes can be analyzed to refine schedules and increase equipment efficiency.
This means less unscheduled downtime and better maintenance scheduling, ensuring that equipment is available and functioning correctly when needed most.
Prioritizing Employee Training and Development
An often-overlooked component of managing working hours effectively is the importance of investing in employee training.
Continuous training ensures that the workforce can handle varied shifts and operate complex machinery confidently and safely.
When employees are well-trained, they can execute tasks quickly and accurately, minimizing wasted time and errors that could disrupt production.
Moreover, training fosters a culture of adaptability, preparing staff to handle technological advancements and new equipment with ease.
Building a Collaboration-Driven Environment
Promoting collaboration among teams can lead to innovative solutions for reducing downtime and utilizing working hours efficiently.
Encouraging communication between departments enables smoother workflow transitions, reducing the bottlenecks that can waste valuable time.
Regular team meetings focused on sharing insights can highlight strategies for better equipment utilization and identify areas for improvement.
Having a collaborative environment ensures that everyone is aligned with the company’s operational goals, working together effectively across different shifts.
Analyzing and Refining Processes Regularly
To maintain high levels of productivity, it’s important to continually review and refine the processes in place.
Through regular analysis, management can identify patterns, revealing potential areas where working hours can be optimized.
This feedback loop is instrumental in adjusting processes to handle shifts more efficiently and maximize equipment use.
Utilizing metrics and performance indicators allows companies to track progress and implement improvements based on concrete data.
By remaining proactive, firms can stay ahead of challenges and make necessary adjustments promptly.
Conclusion
Managing working hours and improving equipment utilization requires a multifaceted approach, integrating strategic planning with advanced technology.
By staggering shifts, embracing automation, and fostering continuous learning and collaboration, the manufacturing industry can optimize its operations.
Regular process analysis and refinement based on reliable data ensure sustained improvements in productivity and efficiency.
Ultimately, these strategies not only enhance operational performance but also support a positive, dynamic work environment essential for growth and innovation.
資料ダウンロード
QCD管理受発注クラウド「newji」は、受発注部門で必要なQCD管理全てを備えた、現場特化型兼クラウド型の今世紀最高の受発注管理システムとなります。
ユーザー登録
受発注業務の効率化だけでなく、システムを導入することで、コスト削減や製品・資材のステータス可視化のほか、属人化していた受発注情報の共有化による内部不正防止や統制にも役立ちます。
NEWJI DX
製造業に特化したデジタルトランスフォーメーション(DX)の実現を目指す請負開発型のコンサルティングサービスです。AI、iPaaS、および先端の技術を駆使して、製造プロセスの効率化、業務効率化、チームワーク強化、コスト削減、品質向上を実現します。このサービスは、製造業の課題を深く理解し、それに対する最適なデジタルソリューションを提供することで、企業が持続的な成長とイノベーションを達成できるようサポートします。
製造業ニュース解説
製造業、主に購買・調達部門にお勤めの方々に向けた情報を配信しております。
新任の方やベテランの方、管理職を対象とした幅広いコンテンツをご用意しております。
お問い合わせ
コストダウンが利益に直結する術だと理解していても、なかなか前に進めることができない状況。そんな時は、newjiのコストダウン自動化機能で大きく利益貢献しよう!
(β版非公開)