- お役立ち記事
- Strategies to avoid the risk of delivery delays faced by purchasing managers
月間76,176名の
製造業ご担当者様が閲覧しています*
*2025年3月31日現在のGoogle Analyticsのデータより
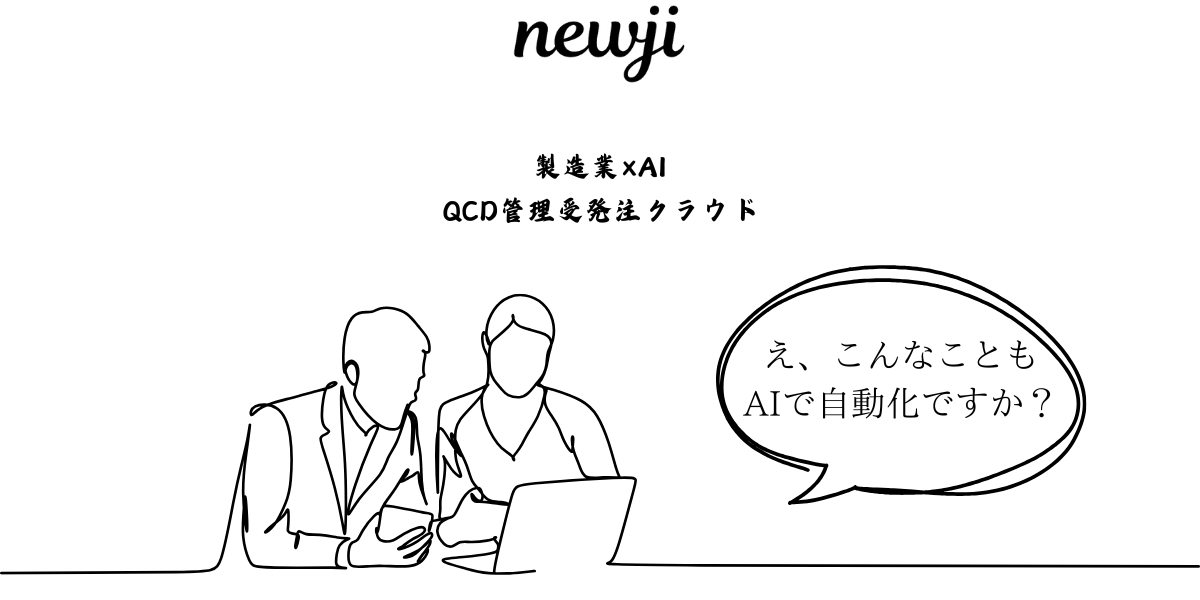
Strategies to avoid the risk of delivery delays faced by purchasing managers
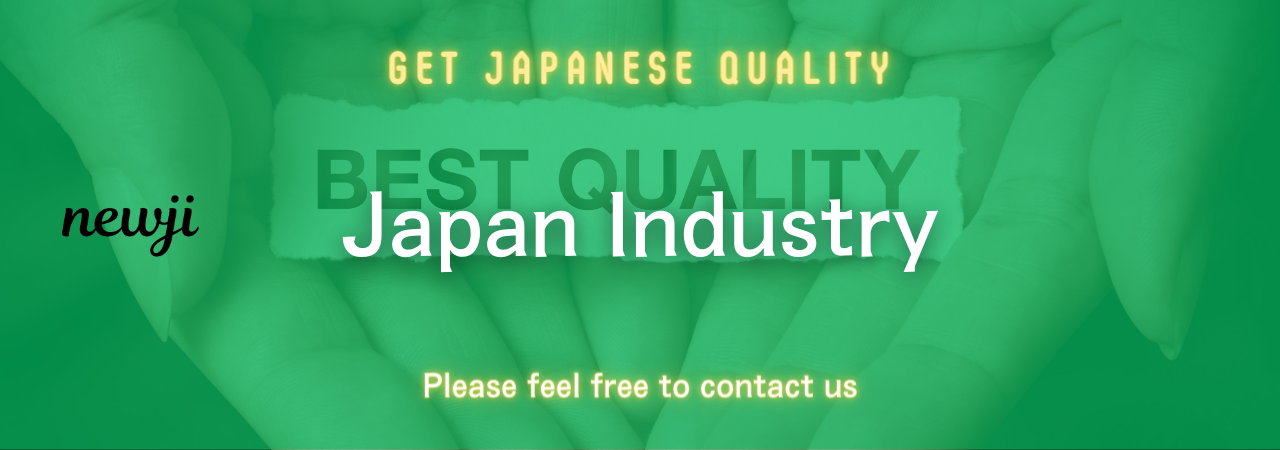
目次
Understanding the Causes of Delivery Delays
Delivery delays are a common challenge for purchasing managers in various industries.
Understanding the root causes of these delays is crucial in developing effective strategies to prevent them.
The reasons for delivery delays can vary widely, ranging from manufacturing issues to logistical challenges and unforeseen events.
One significant cause is production delays at the supplier’s end.
This can occur due to shortage of materials, labor strikes, or machinery breakdowns.
Another common cause is transportation issues, which can be affected by weather conditions, accidents, or logistical errors.
Customs clearance and regulatory compliance can also lead to delays, especially in international shipping.
Unanticipated demand spikes and supply chain disruptions are additional factors that contribute to setback in deliveries.
By identifying these potential causes, purchasing managers can better strategize to mitigate the risks of delivery delays.
The Importance of Supplier Relationships
Developing strong relationships with suppliers is a key strategy in minimizing delivery risks.
Establishing open lines of communication ensures that both parties are updated on potential issues that may cause delays.
Purchasing managers should engage in regular discussions with suppliers to stay informed about production timelines, inventory levels, and any challenges the supplier may be facing.
Having a good rapport with suppliers also facilitates quicker problem-solving when issues arise.
Additionally, purchasing managers should consider working with multiple suppliers.
This diversification reduces dependency on a single supplier and provides alternative sources if one supplier encounters delays.
Ultimately, cultivating strong supplier relationships fosters collaboration and helps in creating a more resilient supply chain.
Forecasting and Inventory Management
Accurate forecasting and effective inventory management are crucial in reducing delivery delay risks.
Purchasing managers need to analyze historical data and market trends to predict future demand accurately.
This foresight allows them to place orders well in advance, thereby accommodating any slight delays that might occur.
Inventory management involves maintaining an optimal stock level that can cater to unforeseen demand spikes without resulting in excessive inventory holding costs.
Implementing an inventory management system can help track stock levels in real-time and automate reorder processes.
Buffer stocks, or safety stocks, should also be considered.
These are additional quantities kept in reserve to protect against unforeseen demand or supply shocks.
With efficient forecasting and inventory management, purchasing managers can better navigate potential delivery delays.
Leveraging Technology for Improved Tracking
Technology plays a pivotal role in managing delivery processes more efficiently.
Using modern technology tools, purchasing managers can track shipments in real-time, gaining visibility over the entire supply chain.
This tracking allows managers to quickly identify and respond to any issues that may impact delivery schedules.
Logistics software can help in optimizing delivery routes, ensuring faster shipping times, and reducing the possibility of delays.
Additionally, technology can aid in documenting and automating various supply chain processes, thus reducing human errors that could lead to delays.
Investing in technology not only aids in managing current shipments but also improves data analysis for better future decision-making.
By leveraging technology, purchasing managers can enhance operational efficiency and reduce risks associated with delivery delays.
Preparedness for Contingencies
Having a contingency plan is essential for purchasing managers to effectively handle unexpected delivery delays.
This plan should include alternative solutions, such as backup suppliers or alternative transportation options.
Identifying critical paths and potential risk factors beforehand enables quicker decision-making when problems arise.
Training supply chain employees to respond adeptly to unforeseen situations also enhances the company’s ability to manage disruptions.
Regular drills and simulations can prepare the team to handle emergencies without significant impact on operations.
By being prepared for contingencies, purchasing managers can ensure continuity in the supply chain and reduce the impact of delays on their businesses.
Utilizing Collaborative Tools and Techniques
Collaboration is key to preventing delivery delays.
Purchasing managers should encourage collaboration within their organization and with external partners, such as suppliers and logistics providers.
Collaborative tools like shared platforms or communication software can facilitate real-time information sharing and immediate communication between all stakeholders.
This synergy ensures everyone involved is up to date and can collectively address any issues that arise promptly.
Techniques such as joint planning sessions with suppliers can help align expectations and timelines, further averting potential delays.
Mutual trust and collaborative efforts often lead to innovative solutions that benefit all parties involved.
Harnessing collaborative tools and fostering cooperation is a proactive approach to minimizing the likelihood of delivery delays.
Conclusion
Purchasing managers play a crucial role in ensuring smooth and timely deliveries.
By understanding the causes of delivery delays and implementing strategies like strengthening supplier relationships, using technology, effective inventory management, and preparing for contingencies, the risks associated with delays can be significantly reduced.
Additionally, fostering a collaborative culture and leveraging modern tools enhance the supply chain’s resilience against disruptions.
These strategies ensure that businesses can continue operations seamlessly, maintain customer satisfaction, and uphold their reputation in the market.
資料ダウンロード
QCD管理受発注クラウド「newji」は、受発注部門で必要なQCD管理全てを備えた、現場特化型兼クラウド型の今世紀最高の受発注管理システムとなります。
ユーザー登録
受発注業務の効率化だけでなく、システムを導入することで、コスト削減や製品・資材のステータス可視化のほか、属人化していた受発注情報の共有化による内部不正防止や統制にも役立ちます。
NEWJI DX
製造業に特化したデジタルトランスフォーメーション(DX)の実現を目指す請負開発型のコンサルティングサービスです。AI、iPaaS、および先端の技術を駆使して、製造プロセスの効率化、業務効率化、チームワーク強化、コスト削減、品質向上を実現します。このサービスは、製造業の課題を深く理解し、それに対する最適なデジタルソリューションを提供することで、企業が持続的な成長とイノベーションを達成できるようサポートします。
製造業ニュース解説
製造業、主に購買・調達部門にお勤めの方々に向けた情報を配信しております。
新任の方やベテランの方、管理職を対象とした幅広いコンテンツをご用意しております。
お問い合わせ
コストダウンが利益に直結する術だと理解していても、なかなか前に進めることができない状況。そんな時は、newjiのコストダウン自動化機能で大きく利益貢献しよう!
(β版非公開)