- お役立ち記事
- Strategy for distributing orders to multiple suppliers A method for purchasing departments to manage costs and risks
月間76,176名の
製造業ご担当者様が閲覧しています*
*2025年3月31日現在のGoogle Analyticsのデータより
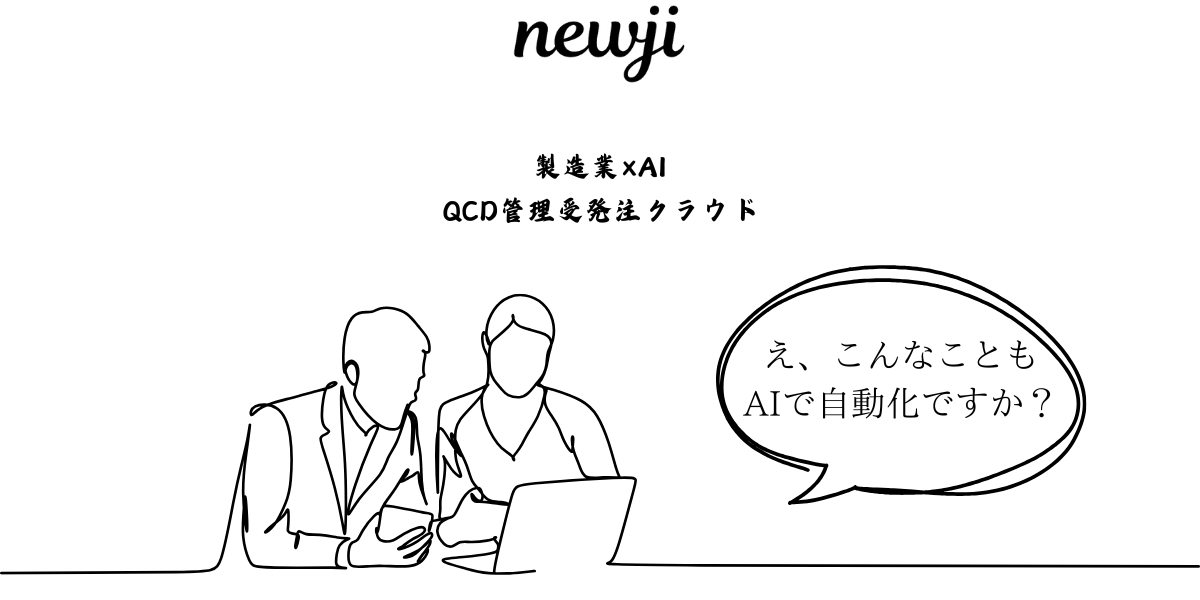
Strategy for distributing orders to multiple suppliers A method for purchasing departments to manage costs and risks
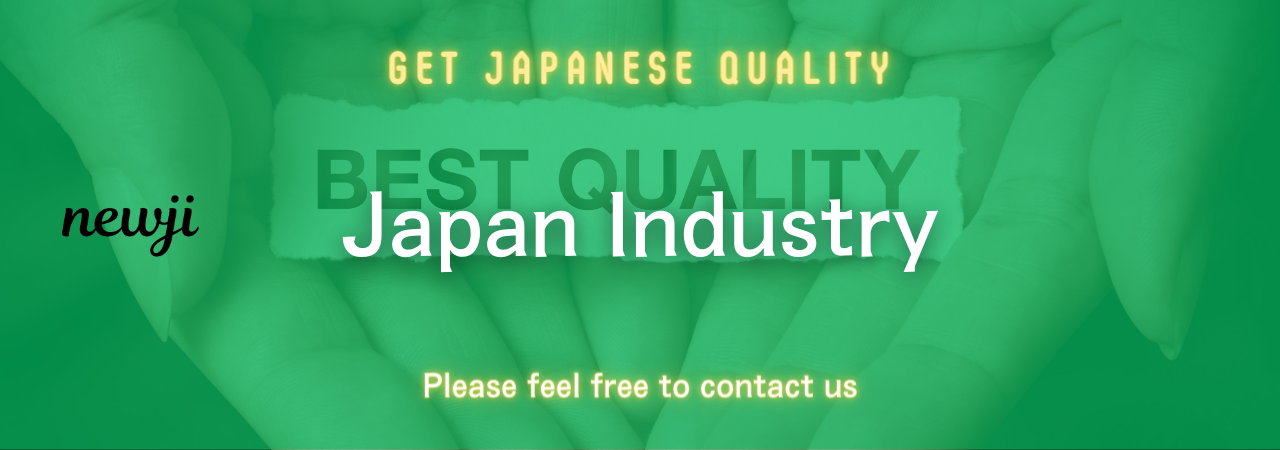
目次
Understanding the Importance of Supplier Diversification
In today’s globalized economy, businesses often rely on multiple suppliers to meet their manufacturing and operational needs.
However, solely depending on a single supplier poses significant risks.
Issues like supply chain disruptions, natural disasters, or political instability can severely impact a company’s ability to procure necessary materials.
To mitigate such risks, many businesses adopt a strategy of distributing orders to multiple suppliers.
Supplier diversification not only helps manage risk but also enhances the ability to negotiate better terms with vendors.
By having multiple suppliers, organizations can ensure competitiveness in pricing and maintain a steady supply of materials, thus safeguarding their operations from unforeseen disruptions.
Balancing Cost and Risk in Procurement
One of the primary goals for purchasing departments is to manage costs effectively while minimizing risk.
When distributing orders among different suppliers, it is crucial to strike a balance between these two factors.
While opting for the lowest-cost supplier might seem advantageous in the short term, it may leave a company vulnerable if that supplier fails to deliver.
Conversely, working with higher-cost suppliers, which may offer more reliability, can strain budgets.
Therefore, purchasing departments must evaluate the cost-risk trade-off by considering a supplier’s reliability, capacity, location, lead times, and financial stability.
Creating a Supplier Evaluation Framework
Before distributing orders among multiple suppliers, businesses should develop a comprehensive supplier evaluation framework.
This framework should encompass several criteria essential for making informed decisions.
Supplier Reliability
Reliability is a critical factor in supplier selection.
Purchasing departments should examine the supplier’s past performance, delivery timelines, and overall ability to consistently meet their contractual obligations.
Quality Standards
Maintaining product quality is imperative.
Therefore, assessing the quality standards of potential suppliers is crucial to avoid compromising on the final product.
Financial Stability
Financial stability ensures that suppliers can continue operations without interruptions.
Examining financial records and stability indicators can help determine whether a supplier is a viable long-term partner.
Capacity and Scalability
A supplier’s capacity to handle variation in order volumes is crucial for flexible inventory management.
Scalability is especially important in meeting increased demand without compromising service quality.
Geographical Location
The location of a supplier can significantly impact lead times and shipping costs.
Preferably, choosing suppliers that are strategically located can reduce transportation costs and improve response times during supply chain emergencies.
Implementing an Order Distribution Strategy
Once suppliers are evaluated and selected, the next step is to implement an effective order distribution strategy.
Segmentation of Orders
Order segmentation involves dividing purchase orders among different suppliers based on their strengths and capacities.
This practice ensures that no supplier is overburdened while maintaining a safety net in case one supplier encounters issues.
Long-term Contracts with Flexible Terms
While long-term contracts offer stability, incorporating flexible terms allows purchasing departments to adjust orders based on current needs.
This flexibility is vital in adapting to market changes and optimizing costs.
Regular Performance Review
Continual monitoring and evaluation of supplier performance help ensure consistent service quality.
Regular reviews also provide opportunities to reassess relationships and make necessary adjustments in order distribution.
Collaboration and Relationship Building
Building strong relationships with suppliers fosters trust and open communication.
Collaborative partnerships encourage suppliers to prioritize your company, offering better terms and innovative solutions.
Technology’s Role in Supplier Management
Technology plays a significant role in optimizing the process of distributing orders to multiple suppliers.
Innovative tools and software solutions allow for streamlined procurement processes, better data management, and improved decision-making.
Inventory Management Systems
Advanced inventory management systems enable real-time tracking of inventory levels and automatic reordering, optimizing order distribution among suppliers.
Supplier Relationship Management (SRM) Software
SRM software assists in maintaining comprehensive details about supplier interactions, performance metrics, and historical data, enhancing decision-making processes.
Procurement Analytics
Utilizing analytics, businesses can evaluate supplier performance effectively.
Data-driven insights improve negotiation strategies and help in identifying potential areas for cost savings.
Concluding Remarks
For purchasing departments, managing costs and risks is integral to supporting overall business success.
Implementing a strategic approach to distribute orders across multiple suppliers significantly mitigates risks, ensures reliability, and can lead to cost savings.
By establishing a robust supplier evaluation framework and leveraging technology, procurement professionals can efficiently navigate the complexities of the modern supply chain landscape.
Ultimately, a well-executed supplier diversification strategy contributes to the long-term resilience and profitability of a business.
資料ダウンロード
QCD管理受発注クラウド「newji」は、受発注部門で必要なQCD管理全てを備えた、現場特化型兼クラウド型の今世紀最高の受発注管理システムとなります。
ユーザー登録
受発注業務の効率化だけでなく、システムを導入することで、コスト削減や製品・資材のステータス可視化のほか、属人化していた受発注情報の共有化による内部不正防止や統制にも役立ちます。
NEWJI DX
製造業に特化したデジタルトランスフォーメーション(DX)の実現を目指す請負開発型のコンサルティングサービスです。AI、iPaaS、および先端の技術を駆使して、製造プロセスの効率化、業務効率化、チームワーク強化、コスト削減、品質向上を実現します。このサービスは、製造業の課題を深く理解し、それに対する最適なデジタルソリューションを提供することで、企業が持続的な成長とイノベーションを達成できるようサポートします。
製造業ニュース解説
製造業、主に購買・調達部門にお勤めの方々に向けた情報を配信しております。
新任の方やベテランの方、管理職を対象とした幅広いコンテンツをご用意しております。
お問い合わせ
コストダウンが利益に直結する術だと理解していても、なかなか前に進めることができない状況。そんな時は、newjiのコストダウン自動化機能で大きく利益貢献しよう!
(β版非公開)