- お役立ち記事
- Strength design, stress analysis and residual stress reduction molding technology for plastic molded products
Strength design, stress analysis and residual stress reduction molding technology for plastic molded products
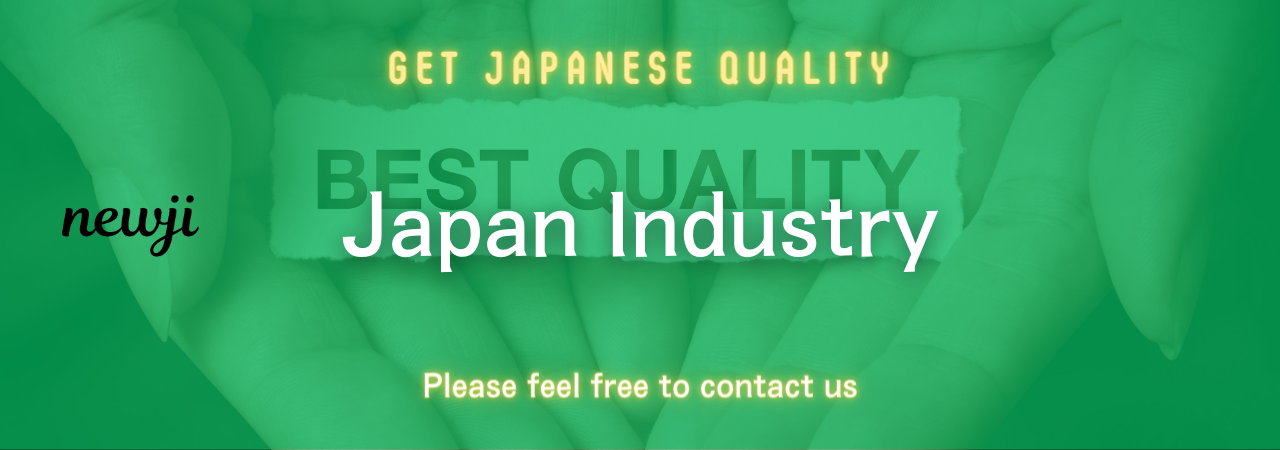
目次
Understanding Plastic Molded Products
Plastic molded products are an integral part of our daily lives, from household items and packaging to automotive parts and medical devices.
Their popularity stems from their lightweight, cost-effectiveness, and versatility in design and application.
However, to ensure these products maintain their quality and functionality, understanding the intricacies of their strength design, stress analysis, and residual stress reduction is vital.
What is Strength Design?
Strength design in plastic molded products refers to the process of optimizing their structural integrity to withstand expected loads without failure.
It encompasses considering the material properties, intended use, and physical dimensions.
Plastic materials, due to their varied polymer structures, exhibit different mechanical behaviors under stress.
Hence, choosing the right type of plastic and design criteria is crucial for ensuring durability.
A key aspect of strength design is determining the material’s tensile strength, which signifies how much pulling force the material can bear before it breaks.
Additionally, factors like flexibility, impact resistance, and environmental stability must be understood.
Together, these elements ensure that a product not only fulfills its function but also has a satisfactory lifespan.
The Role of Stress Analysis
Stress analysis plays a critical role in the development of plastic molded products by assessing how applied forces and pressures affect the material.
Understanding the distribution of stress across a molding helps designers and engineers predict potential points of failure.
Types of Stress
There are several types of stress that can impact plastic molded products:
1. **Tensile Stress:** Occurs when materials are stretched.
2. **Compressive Stress:** Occurs with forces that compress or squeeze the material.
3. **Shear Stress:** Results from forces acting in parallel but opposite directions.
Finite element analysis (FEA) is a common technique used in stress analysis.
FEA simulations involve creating a model of the product and approximating how it reacts under various physical conditions.
By identifying stress concentrations, engineers can tweak designs to enhance resistance against potential deformations or failures.
Reducing Residual Stresses
Residual stress refers to the stress retained in a material after the initial force or load is removed.
In plastic molded products, these stresses can result from manufacturing processes, including cooling rates, pressure during molding, and differential shrinkage.
The Impact of Residual Stress
Residual stresses can lead to issues such as warping, cracking, and dimensional inaccuracies, which can compromise the structural integrity and aesthetic appeal of the product.
Therefore, mitigating residual stress is essential to ensure the quality and reliability of plastic molded goods.
Techniques for Residual Stress Reduction
Several methods can be employed to reduce residual stress in plastic molded products:
1. **Controlled Cooling:** Managing the cooling rate during the molding process can help in minimizing thermal gradients, thus reducing residual stresses.
2. **Annealing:** Heating the molded product to a specific temperature and allowing it to cool gradually can relieve induced stresses.
3. **Process Optimization:** Adjusting parameters such as mold temperature, injection speed, and holding pressure during the molding process can significantly impact the level of residual stress.
Advancements in Molding Technology
Technological advancements in molding processes contribute significantly to improving the strength, reducing stress, and minimizing residual stress in plastic molded products.
Continuous research and development are driving innovations that result in better product quality and efficiency.
Injection Molding Innovations
Injection molding remains the dominant method for creating plastic parts.
Recent innovations aim to enhance accuracy and reduce waste:
– **Multi-cavity molds**: These allow for the production of multiple parts in a single cycle, improving efficiency and reducing scrap.
– **Hot runner systems**: Instead of cooling and reheating, hot runner systems keep the plastic material in a molten state, reducing stress-induced defects.
Alternative Molding Methods
While injection molding is widely used, alternative methods such as extrusion, blow molding, and thermoforming also offer benefits in certain applications.
Each technique has unique advantages in terms of material use, production speed, and stress reduction.
– **Extrusion** is effective for products with a consistent cross-sectional profile, such as pipes and hoses.
– **Blow molding** is ideal for creating hollow parts like bottles and containers, offering high strength and low residual stress.
– **Thermoforming** allows for extensive design flexibility and is cost-effective for large parts with minimal geometric complexity.
Conclusion
The integration of strength design, stress analysis, and residual stress reduction techniques is essential in manufacturing high-quality plastic molded products.
By understanding the nuances of material properties and employing the latest technological advancements in molding, manufacturers can produce robust, reliable, and durable products that meet the demands of various industries.
As technology continues to evolve, we anticipate more innovations that will further enhance the performance and sustainability of plastic molded products.
Investing in these areas ensures that we maximize the benefits offered by plastic materials while minimizing potential drawbacks.
資料ダウンロード
QCD調達購買管理クラウド「newji」は、調達購買部門で必要なQCD管理全てを備えた、現場特化型兼クラウド型の今世紀最高の購買管理システムとなります。
ユーザー登録
調達購買業務の効率化だけでなく、システムを導入することで、コスト削減や製品・資材のステータス可視化のほか、属人化していた購買情報の共有化による内部不正防止や統制にも役立ちます。
NEWJI DX
製造業に特化したデジタルトランスフォーメーション(DX)の実現を目指す請負開発型のコンサルティングサービスです。AI、iPaaS、および先端の技術を駆使して、製造プロセスの効率化、業務効率化、チームワーク強化、コスト削減、品質向上を実現します。このサービスは、製造業の課題を深く理解し、それに対する最適なデジタルソリューションを提供することで、企業が持続的な成長とイノベーションを達成できるようサポートします。
オンライン講座
製造業、主に購買・調達部門にお勤めの方々に向けた情報を配信しております。
新任の方やベテランの方、管理職を対象とした幅広いコンテンツをご用意しております。
お問い合わせ
コストダウンが利益に直結する術だと理解していても、なかなか前に進めることができない状況。そんな時は、newjiのコストダウン自動化機能で大きく利益貢献しよう!
(Β版非公開)