- お役立ち記事
- Strengthen risk management by reviewing evaluation criteria for business partners Purchasing department risk management
月間76,176名の
製造業ご担当者様が閲覧しています*
*2025年3月31日現在のGoogle Analyticsのデータより
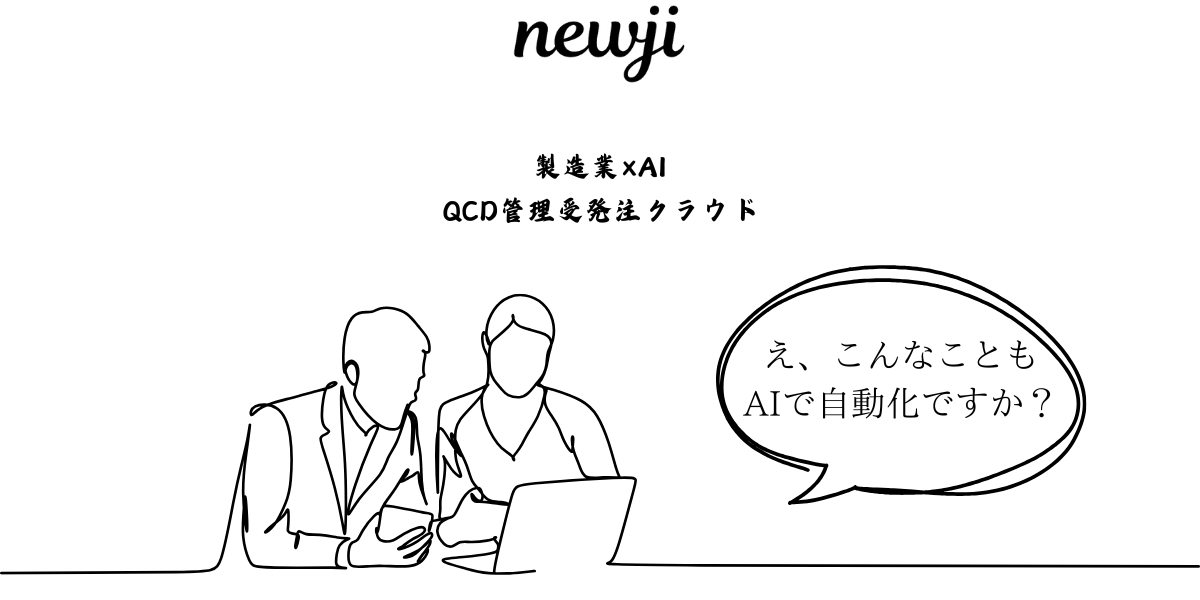
Strengthen risk management by reviewing evaluation criteria for business partners Purchasing department risk management
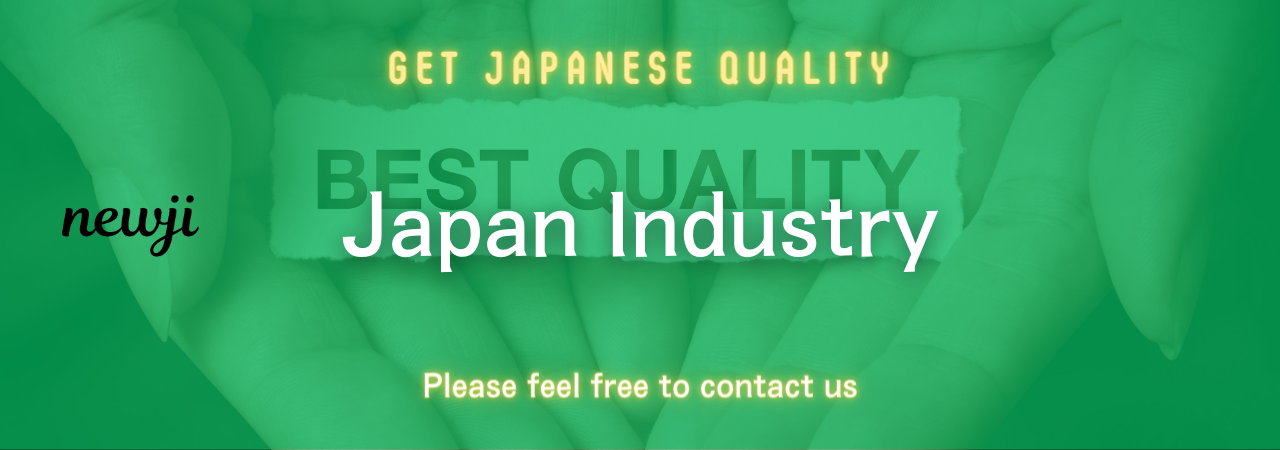
目次
Understanding Risk Management in the Purchasing Department
Risk management is a crucial aspect of every organization, especially in the purchasing department, where decisions can significantly impact the entire business operations.
In essence, risk management involves identifying potential risks, evaluating them, and implementing strategies to mitigate these risks.
The purchasing department must be adept at managing risks associated with supplier selection, inventory management, and changing market conditions.
One of the most effective ways to strengthen risk management in this vital department is by reviewing and updating the evaluation criteria for business partners.
The Importance of Supplier Evaluation Criteria
Evaluating business partners or suppliers is a critical step in the procurement process.
It involves assessing various factors, such as the supplier’s financial stability, quality of goods and services, delivery performance, and compliance with industry standards.
By updating their evaluation criteria, organizations can make informed decisions that minimize risks like supply chain disruptions, financial losses, and reputational damage.
Assessing Financial Stability
A crucial aspect of evaluating business partners is assessing their financial stability.
Suppliers with strong financial health are more likely to withstand economic downturns and continue delivering goods and services consistently.
Purchasing departments should review financial statements, credit ratings, and other indicators of financial health.
Regular monitoring of these indicators helps in anticipating and mitigating risks related to supplier bankruptcy or financial distress.
Quality Assurance and Compliance
Ensuring that suppliers meet quality standards and comply with industry regulations is another vital aspect of risk management.
Purchasing departments should establish clear criteria for quality assurance, such as testing procedures, certification requirements, and quality control processes.
Evaluating suppliers based on their ability to meet these criteria minimizes the risk of receiving substandard products, which can lead to increased returns, wasted resources, and customer dissatisfaction.
Delivery Performance
Reliable delivery performance is essential to maintaining a smooth supply chain and meeting customer demands.
When evaluating suppliers, the purchasing department should consider factors like on-time delivery rates, lead times, order accuracy, and flexibility to accommodate changes in demand.
By setting high standards for delivery performance, organizations can reduce the risk of delays, stockouts, and potential revenue losses.
Maintaining Long-Term Relationships
In addition to the above criteria, the ability to forge and maintain long-term relationships with suppliers is a key consideration.
Building strong partnerships with reliable suppliers can provide a competitive advantage, ensuring consistent quality, favorable pricing, and innovation opportunities.
Flexible and adaptable suppliers tend to contribute towards a more resilient supply chain, reducing overall risk exposure.
Implementing a Risk-Based Approach
To enhance risk management further, purchasing departments should adopt a risk-based approach in evaluating suppliers.
This involves categorizing suppliers according to their risk level and tailoring evaluation criteria based on these categories.
High-Risk Suppliers
High-risk suppliers are those that are critical to the organization’s operations but have potential vulnerabilities, such as limited financial resources or being located in geopolitically unstable regions.
For these suppliers, more stringent evaluation criteria and continuous monitoring are necessary to ensure potential risks are identified early and mitigated effectively.
Low-Risk Suppliers
Low-risk suppliers, on the other hand, are those with minimal risks and a proven track record of reliability.
While these require regular evaluation, the focus should primarily be on maintaining the existing relationship and ensuring consistent performance.
Integrating Technology in Risk Management
Another effective strategy for strengthening risk management is leveraging technology in the evaluation process.
Advances in technology provide tools that can enhance the purchasing department’s ability to assess and manage supplier risks efficiently.
Supplier Management Software
Adopting supplier management software helps in storing and analyzing data from multiple suppliers in one central location.
This platform facilitates smoother communication, easier comparison of supplier performance, and improved decision-making based on real-time data.
Automation and Data Analytics
Automating processes through data analytics offers insights into supplier trends, compliance issues, and potential risks, enabling the purchasing department to take proactive measures.
Predictive analytics, for instance, can identify potential risks even before they become apparent, allowing the organization to act swiftly to avoid disruptions.
Regular Review and Continuous Improvement
Finally, strengthening risk management requires a continuous focus on reviewing and improving evaluation criteria for suppliers.
Regular audits, supplier performance reviews, and feedback mechanisms are essential to ensure the criteria remain relevant and effective.
Stakeholder Involvement
Engaging stakeholders in the evaluation process helps in gaining diverse perspectives and ensuring that all potential risks are considered.
Collaboration across departments ensures a comprehensive understanding of supplier performance and enhances risk management strategies.
Adapting to Changing Market Conditions
Moreover, as market conditions change, so should evaluation criteria.
The purchasing department must stay informed of industry trends, economic shifts, and technological advancements to anticipate and address new risks that may arise.
By optimizing risk management through reviewing and updating evaluation criteria for business partners, organizations can fortify their purchasing departments against uncertainties.
A well-managed procurement process leads to reduced risk exposure, enhanced supplier relationships, and ultimately, improved business continuity and success.
資料ダウンロード
QCD管理受発注クラウド「newji」は、受発注部門で必要なQCD管理全てを備えた、現場特化型兼クラウド型の今世紀最高の受発注管理システムとなります。
ユーザー登録
受発注業務の効率化だけでなく、システムを導入することで、コスト削減や製品・資材のステータス可視化のほか、属人化していた受発注情報の共有化による内部不正防止や統制にも役立ちます。
NEWJI DX
製造業に特化したデジタルトランスフォーメーション(DX)の実現を目指す請負開発型のコンサルティングサービスです。AI、iPaaS、および先端の技術を駆使して、製造プロセスの効率化、業務効率化、チームワーク強化、コスト削減、品質向上を実現します。このサービスは、製造業の課題を深く理解し、それに対する最適なデジタルソリューションを提供することで、企業が持続的な成長とイノベーションを達成できるようサポートします。
製造業ニュース解説
製造業、主に購買・調達部門にお勤めの方々に向けた情報を配信しております。
新任の方やベテランの方、管理職を対象とした幅広いコンテンツをご用意しております。
お問い合わせ
コストダウンが利益に直結する術だと理解していても、なかなか前に進めることができない状況。そんな時は、newjiのコストダウン自動化機能で大きく利益貢献しよう!
(β版非公開)