- お役立ち記事
- Strengthening Human Resource Development with Manufacturing Training Programs
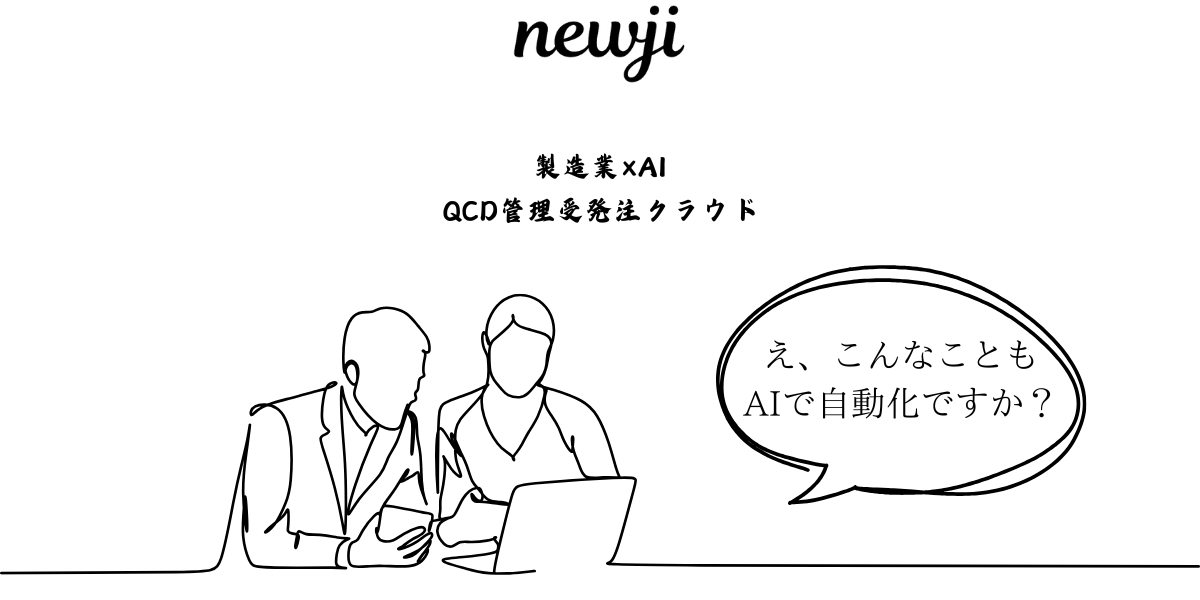
Strengthening Human Resource Development with Manufacturing Training Programs
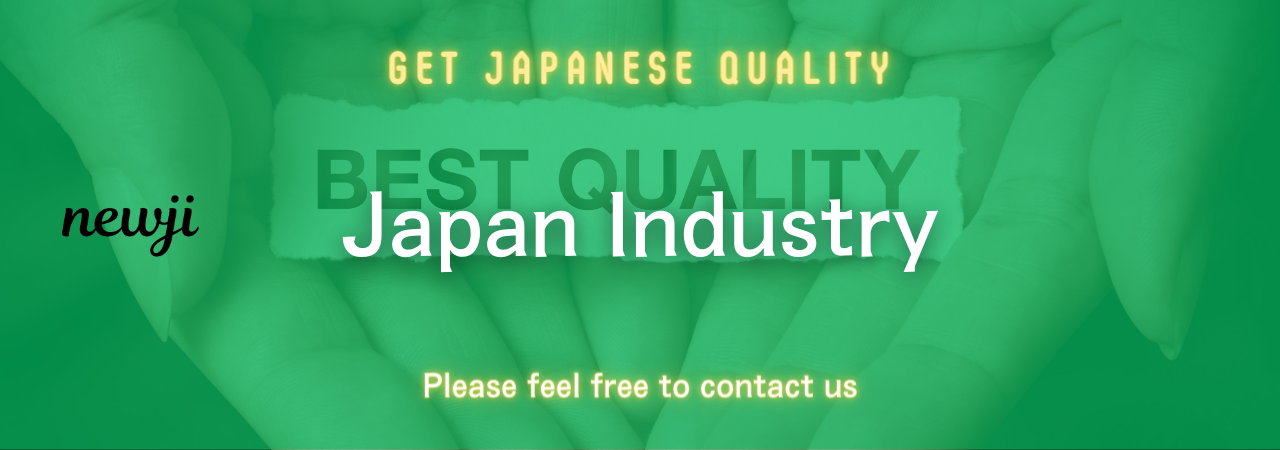
In today’s competitive market, the success of any manufacturing company hinges on its workforce.
Manufacturing training programs play a crucial role in bolstering human resource development, ensuring that employees are skilled, efficient, and capable of meeting the demands of modern production environments.
Let’s delve into how these training programs contribute to human resource development and why they are essential for the manufacturing sector.
目次
What Are Manufacturing Training Programs?
Manufacturing training programs are structured educational initiatives designed to enhance the skills and knowledge of employees in the manufacturing industry.
These programs can range from on-the-job training and apprenticeships to formal classroom-based courses and online learning modules.
By focusing on specific manufacturing processes, equipment operation, safety protocols, and quality control, these programs aim to create a highly skilled workforce capable of maintaining high production standards.
The Importance of Manufacturing Training Programs
1. Enhancing Technical Skills
One of the primary objectives of manufacturing training programs is to enhance the technical skills of employees.
Workers learn how to operate complex machinery, understand advanced production techniques, and troubleshoot issues effectively.
This not only improves productivity but also ensures that the company can maintain a competitive edge by keeping up with technological advancements.
2. Improving Safety Standards
Safety is paramount in any manufacturing environment.
Training programs educate employees on the latest safety protocols and emergency procedures.
This reduces the risk of accidents and injuries, creating a safer workplace.
A strong safety culture also boosts employee morale and reduces downtime, contributing to overall operational efficiency.
3. Boosting Employee Morale and Retention
Investing in employee development through training programs demonstrates a company’s commitment to its workforce.
This investment boosts employee morale and job satisfaction.
When employees feel valued and see opportunities for personal and professional growth, they are more likely to stay with the company.
This reduces turnover rates and the associated costs of recruiting and training new hires.
4. Ensuring Quality Control
Manufacturing training programs emphasize the importance of quality control and continuous improvement.
Employees learn how to adhere to stringent quality standards and identify potential defects or inefficiencies in the production process.
This focus on quality ensures that the end products meet or exceed customer expectations, enhancing the company’s reputation and customer satisfaction.
5. Fostering Innovation
A well-trained workforce is more likely to contribute to innovative solutions and process improvements.
Training programs encourage employees to think critically and creatively.
This fosters a culture of innovation where employees feel empowered to suggest new ideas and approaches.
Innovation is crucial for staying competitive and adapting to changing market demands.
Implementing Effective Manufacturing Training Programs
1. Assess Training Needs
The first step in implementing an effective training program is to assess the specific needs of your workforce.
Conducting a skills gap analysis can help identify areas where employees need improvement.
This ensures that the training program is tailored to address these gaps.
2. Develop a Comprehensive Curriculum
A well-structured curriculum is essential for the success of any training program.
It should cover all necessary technical skills, safety protocols, quality control measures, and soft skills like communication and teamwork.
Collaborate with industry experts and seasoned employees to create a comprehensive curriculum that meets industry standards.
3. Utilize Various Training Methods
Different employees have different learning preferences.
To cater to diverse learning styles, employ a mix of training methods such as hands-on training, classroom instruction, online courses, and simulations.
This ensures that all employees can benefit from the program, regardless of their preferred learning method.
4. Measure Training Effectiveness
It’s important to regularly evaluate the effectiveness of the training program.
Use metrics such as employee performance, productivity levels, and feedback to gauge the program’s impact.
Making adjustments based on these evaluations ensures continuous improvement in the training process.
5. Encourage Continuous Learning
Manufacturing is an ever-evolving field, with new technologies and processes constantly emerging.
Encourage a culture of continuous learning by providing ongoing training opportunities.
This ensures that employees can stay up-to-date with the latest industry developments and maintain their competitiveness.
Challenges in Manufacturing Training Programs and How to Overcome Them
1. Time Constraints
Finding time for training can be challenging, especially in a fast-paced manufacturing environment.
To overcome this, integrate training into regular work schedules or offer flexible online learning options that employees can complete at their own pace.
2. Limited Budget
Budget constraints can limit the ability to implement comprehensive training programs.
Consider leveraging grants, partnerships with educational institutions, or internal expertise to develop cost-effective training solutions.
Investing in employee training may have upfront costs, but the long-term benefits far outweigh the initial investment.
3. Resistance to Change
Employees may resist new training initiatives due to fear of change or lack of interest.
Clear communication about the benefits of the training program and involving employees in the development process can help mitigate resistance.
Highlighting success stories and providing incentives can also motivate employees to participate.
Conclusion
Manufacturing training programs are indispensable for strengthening human resource development in the industry.
By enhancing technical skills, improving safety standards, boosting employee morale, ensuring quality control, and fostering innovation, these programs contribute significantly to a company’s success.
Implementing effective training programs requires careful planning, a tailored curriculum, and a commitment to continuous learning.
Overcoming challenges such as time constraints, budget limitations, and resistance to change is crucial for maximizing the benefits of these programs.
Ultimately, a well-trained workforce is the backbone of any successful manufacturing company, capable of driving productivity, innovation, and growth.
資料ダウンロード
QCD調達購買管理クラウド「newji」は、調達購買部門で必要なQCD管理全てを備えた、現場特化型兼クラウド型の今世紀最高の購買管理システムとなります。
ユーザー登録
調達購買業務の効率化だけでなく、システムを導入することで、コスト削減や製品・資材のステータス可視化のほか、属人化していた購買情報の共有化による内部不正防止や統制にも役立ちます。
NEWJI DX
製造業に特化したデジタルトランスフォーメーション(DX)の実現を目指す請負開発型のコンサルティングサービスです。AI、iPaaS、および先端の技術を駆使して、製造プロセスの効率化、業務効率化、チームワーク強化、コスト削減、品質向上を実現します。このサービスは、製造業の課題を深く理解し、それに対する最適なデジタルソリューションを提供することで、企業が持続的な成長とイノベーションを達成できるようサポートします。
オンライン講座
製造業、主に購買・調達部門にお勤めの方々に向けた情報を配信しております。
新任の方やベテランの方、管理職を対象とした幅広いコンテンツをご用意しております。
お問い合わせ
コストダウンが利益に直結する術だと理解していても、なかなか前に進めることができない状況。そんな時は、newjiのコストダウン自動化機能で大きく利益貢献しよう!
(Β版非公開)