- お役立ち記事
- Strengthening Manufacturing Communication Networks with CAN Bus
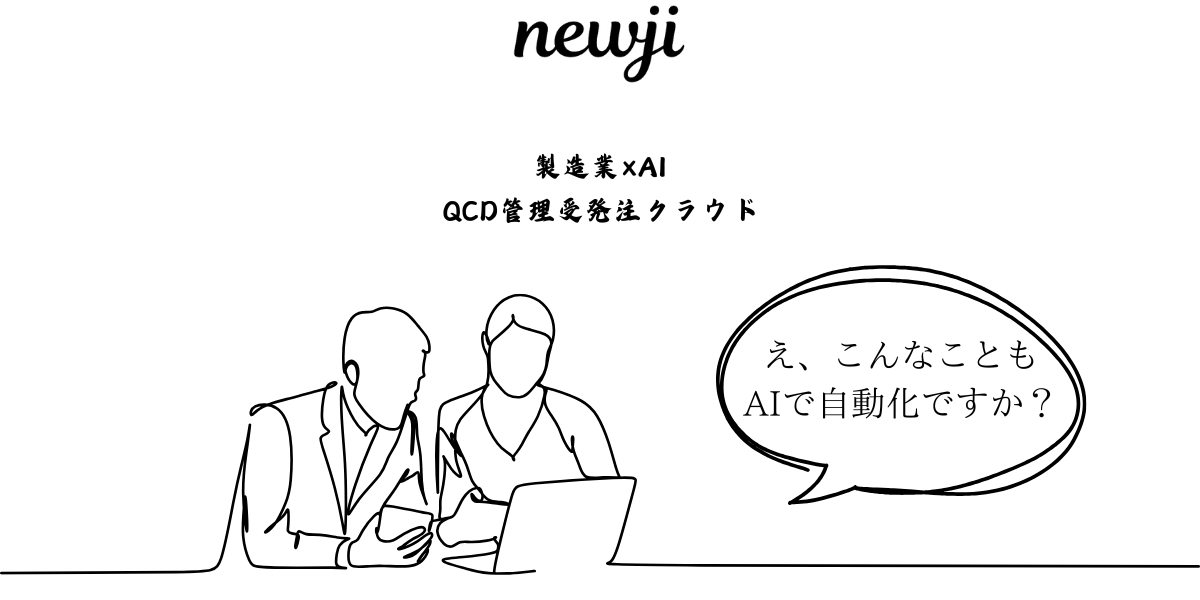
Strengthening Manufacturing Communication Networks with CAN Bus
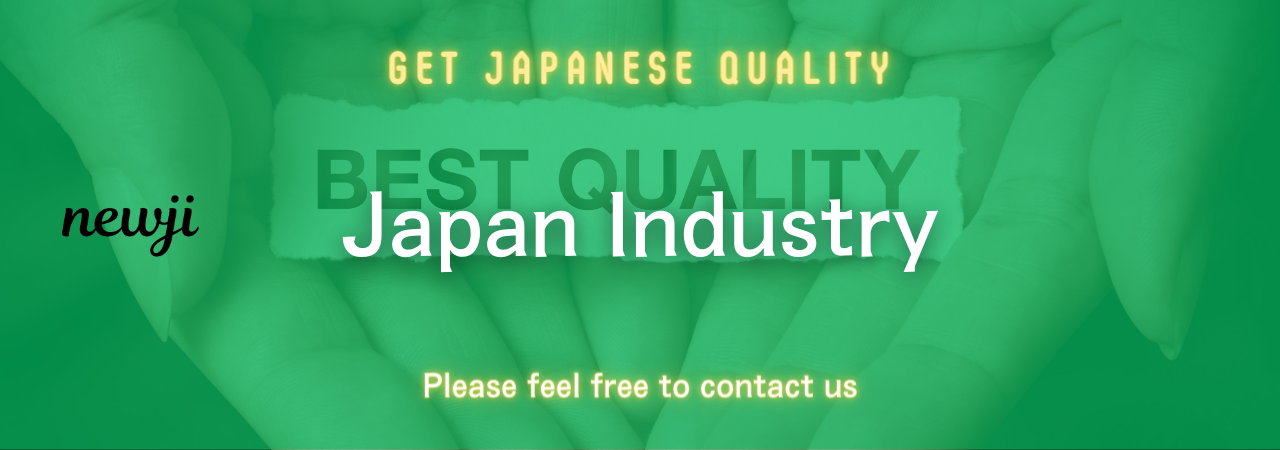
目次
What is CAN Bus?
The Controller Area Network (CAN) bus is a robust vehicle bus standard designed to allow microcontrollers and devices to communicate with each other’s applications.
Without a host computer.
It was developed by Bosch in the late 1980s.
Since then, the CAN bus has become a popular choice for vehicle manufacturers due to its reliability, efficiency, and simplicity.
CAN bus systems are now found not only in automobiles but also in manufacturing and industrial automation sectors.
Benefits of CAN Bus in Manufacturing
Improved Communication
One of the primary benefits of CAN bus in manufacturing is the improvement in communication between devices and systems.
CAN bus allows for multiple microcontrollers to communicate without requiring a host computer.
This improves the efficiency of the entire system, as tasks can be distributed among various devices seamlessly.
Enhanced Reliability
CAN bus is known for its reliability.
It is designed to handle the noisy environment typical in manufacturing plants.
CAN bus uses a robust method of error detection and correction, ensuring that the information being communicated is accurate and undistorted.
This is crucial in manufacturing settings where precision and accuracy are paramount.
Scalability
Another significant benefit of CAN bus in manufacturing is its scalability.
It can support a large number of devices within a network, allowing for future expansion without significant infrastructure changes.
This scalability makes it an attractive option for growing manufacturing plants looking to streamline their processes over time.
Implementing CAN Bus in Manufacturing Systems
Understanding the Requirements
Before implementing CAN bus in a manufacturing system, it is important to understand the specific requirements of the application.
This includes the type and number of devices that need to communicate, the data transmission speed, and the level of fault tolerance required.
Properly assessing these factors can help in configuring the CAN bus system optimally.
Choosing the Right Components
Selecting the right components is critical for the successful implementation of CAN bus in a manufacturing setting.
This involves choosing appropriate microcontrollers, transceivers, and connectors.
It’s important to select components that can withstand the harsh environmental conditions often found in manufacturing plants.
Network Configuration
Setting up a CAN bus network involves configuring the network topology.
Typically, a CAN bus network follows a linear bus topology with nodes connected in parallel.
Proper configuration ensures that data is transmitted efficiently and with minimal delays.
Ensuring that the network is properly terminated at both ends is essential to avoid signal reflections.
Challenges in Using CAN Bus
Noise Interference
One challenge in using CAN bus in manufacturing is noise interference.
Manufacturing environments are full of electromagnetic interference, which can affect the CAN bus signals.
However, using proper shielding and grounding techniques can greatly minimize the impact of noise on the CAN bus network.
Data Collision
Another potential issue is data collision.
Since multiple devices share the same bus for communication, there is a possibility of data collision.
CAN bus employs a method called Carrier Sense Multiple Access/Collision Detection (CSMA/CD) to manage this risk.
While this method is effective, it can introduce slight delays in data transmission.
Limited Data Transmission Speed
CAN bus is not the fastest communication protocol available.
Its data transmission speed is lower compared to some other protocols.
While it is sufficient for many manufacturing applications, it may not be ideal for those requiring extremely high-speed data communication.
Best Practices for Optimizing CAN Bus Performance
Proper Network Design
Proper network design is crucial for optimizing CAN bus performance.
Ensuring that the network topology is designed to minimize data collisions and transmission delays is key.
Also, the placement of nodes should be strategic to enhance communication efficiency.
Regular Maintenance
Regular maintenance of the CAN bus network is essential to keep it functioning efficiently.
This includes periodic checks of connections, cables, and components.
Replacing worn-out parts promptly can prevent potential communication breakdowns that can disrupt manufacturing processes.
Training and Education
Training and educating personnel on how to manage and maintain CAN bus networks can significantly improve the overall performance of the system.
Understanding the protocol’s intricacies and knowing how to troubleshoot common issues can help in maintaining uptime and productivity in manufacturing plants.
Conclusion
The implementation of CAN bus in manufacturing communication networks offers numerous advantages, including improved communication, enhanced reliability, and scalability.
While there are challenges to its use, such as noise interference and data collision, following best practices and proper implementation can mitigate these issues.
By understanding the requirements, choosing the right components, and maintaining the network, manufacturers can greatly benefit from the robust and efficient communication that CAN bus provides.
資料ダウンロード
QCD調達購買管理クラウド「newji」は、調達購買部門で必要なQCD管理全てを備えた、現場特化型兼クラウド型の今世紀最高の購買管理システムとなります。
ユーザー登録
調達購買業務の効率化だけでなく、システムを導入することで、コスト削減や製品・資材のステータス可視化のほか、属人化していた購買情報の共有化による内部不正防止や統制にも役立ちます。
NEWJI DX
製造業に特化したデジタルトランスフォーメーション(DX)の実現を目指す請負開発型のコンサルティングサービスです。AI、iPaaS、および先端の技術を駆使して、製造プロセスの効率化、業務効率化、チームワーク強化、コスト削減、品質向上を実現します。このサービスは、製造業の課題を深く理解し、それに対する最適なデジタルソリューションを提供することで、企業が持続的な成長とイノベーションを達成できるようサポートします。
オンライン講座
製造業、主に購買・調達部門にお勤めの方々に向けた情報を配信しております。
新任の方やベテランの方、管理職を対象とした幅広いコンテンツをご用意しております。
お問い合わせ
コストダウンが利益に直結する術だと理解していても、なかなか前に進めることができない状況。そんな時は、newjiのコストダウン自動化機能で大きく利益貢献しよう!
(Β版非公開)