- お役立ち記事
- Strengthening Manufacturing Lines with DC Motor OEM Implementation
Strengthening Manufacturing Lines with DC Motor OEM Implementation
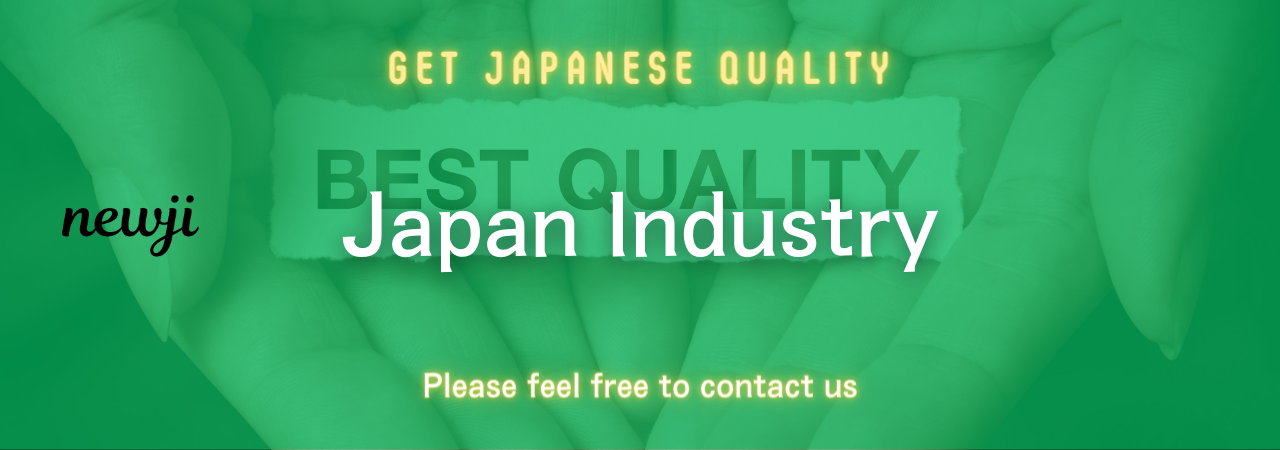
In the ever-evolving landscape of manufacturing, efficiency, and precision are paramount to success.
One area where significant advancements have been made is in the use of Direct Current (DC) motors.
By partnering with a DC motor Original Equipment Manufacturer (OEM), manufacturing operations can benefit greatly from reduced costs, enhanced efficiency, and consistent performance.
Let’s examine how implementing DC motor OEMs can offer a robust solution for strengthening manufacturing lines.
目次
Understanding DC Motors
DC motors convert electrical energy into mechanical energy through the interaction of magnetic fields.
They are renowned for their reliability, efficiency, and versatility.
These motors come in various types, including brushless, brushed, and servo motors, each suited for different applications in the manufacturing industry.
Brushless DC Motors
Brushless DC motors are favored for their low maintenance requirements.
They lack the brushes that wear out over time, making them suitable for long-term use in manufacturing setups.
These motors are efficient and offer high speed and torque characteristics.
Brushed DC Motors
Brushed DC motors, although requiring more maintenance due to brush replacement, offer outstanding performance for applications requiring precise control and positioning.
Their simplicity and cost-effectiveness make them an attractive option for certain manufacturing operations.
Servo Motors
Servo motors are a subtype of DC motors designed for applications requiring precise control of position, speed, and acceleration.
They are often used in robotics and other high-precision manufacturing processes.
Advantages of OEM Partnership
Partnering with a DC motor OEM offers numerous benefits, some of which directly enhance manufacturing line performance.
Here are some key advantages:
Customized Solutions
An OEM partnership allows for tailored DC motor solutions that meet the specific needs of a manufacturing line.
OEMs can design and produce motors with specific torque, speed, and voltage requirements, ensuring optimal performance.
Quality Assurance
DC motor OEMs adhere to stringent quality control processes, ensuring that each motor meets high standards of performance and reliability.
This minimizes the risk of motor failure and downtime in manufacturing operations.
Technical Support and Services
OEMs provide comprehensive technical support, from installation to ongoing maintenance.
This ensures that any issues are promptly addressed, keeping the manufacturing line running smoothly and efficiently.
Cost Efficiency
By sourcing DC motors directly from an OEM, manufacturers can often achieve significant cost savings.
OEMs usually offer competitive pricing compared to third-party suppliers.
Additionally, tailored solutions can lead to energy savings and reduced operational costs over time.
Implementing DC Motors in Manufacturing
The integration of DC motors into manufacturing lines can revolutionize operations.
Here’s how:
Improved Precision and Control
DC motors offer unparalleled precision and control, essential for applications like conveyor systems, robotic arms, and assembly lines.
This precision leads to higher product quality and reduced waste.
Enhanced Efficiency
DC motors are known for their high efficiency, converting a greater percentage of electrical energy into mechanical energy.
This efficiency translates to lower energy consumption, reducing operational costs and supporting sustainability initiatives.
Increased Production Speed
With their superior speed control, DC motors can increase the overall production speed of a manufacturing line.
This allows manufacturers to meet higher demand without compromising on quality.
Reduced Maintenance Requirements
Especially with brushless DC motors, the need for maintenance is significantly reduced.
Limited downtime for repairs and maintenance leads to a more continuous production process.
Scalability
DC motors are highly adaptable and can be easily scaled to accommodate changes in production volume or process requirements.
This flexibility ensures that the manufacturing line can grow and evolve with market demands.
Case Studies of Successful Implementation
Examples abound where companies have successfully integrated DC motors through OEM partnerships.
Automotive Manufacturing
In automotive manufacturing, precision is crucial.
A well-known car manufacturer partnered with a DC motor OEM to design motors for its robotic assembly line.
The result was a 15% increase in production speed and a 20% reduction in energy consumption.
Additionally, the customized motors required less frequent maintenance, resulting in significant cost savings.
Food and Beverage Industry
A leading food processing company integrated brushless DC motors into its conveyor systems.
The OEM provided motors that met specific hygiene standards and offered enhanced speed control.
This led to improved production efficiency and better quality control, allowing the company to meet stringent industry standards.
Textile Manufacturing
A textile manufacturer sought to improve its fabric weaving processes.
By integrating servo motors from a DC motor OEM, the company achieved precise control over the weaving machinery.
This resulted in a 30% increase in production output and a noticeable improvement in fabric quality.
Future Trends in DC Motor OEM Implementation
The future looks promising for DC motor OEM integration in manufacturing.
IoT Integration
The Internet of Things (IoT) is set to transform manufacturing operations.
Future DC motors will likely feature IoT-enabled components, allowing real-time monitoring and predictive maintenance.
This will further enhance efficiency and reduce downtime.
Energy Efficiency Innovations
As sustainability becomes a critical concern, DC motor OEMs are focusing on developing motors with even higher energy efficiency.
This will help manufacturers reduce their carbon footprint and operational costs.
Conclusion
Strengthening manufacturing lines through the implementation of DC motor OEM solutions is a strategic move for any manufacturer aiming to boost efficiency, precision, and overall performance.
The benefits of customized solutions, quality assurance, technical support, and cost efficiency make OEM partnerships highly advantageous.
As the manufacturing landscape continues to evolve, the integration of advanced DC motor technologies will play a pivotal role in driving success.
Embrace the future of manufacturing by leveraging the power of DC motor OEMs.
資料ダウンロード
QCD調達購買管理クラウド「newji」は、調達購買部門で必要なQCD管理全てを備えた、現場特化型兼クラウド型の今世紀最高の購買管理システムとなります。
ユーザー登録
調達購買業務の効率化だけでなく、システムを導入することで、コスト削減や製品・資材のステータス可視化のほか、属人化していた購買情報の共有化による内部不正防止や統制にも役立ちます。
NEWJI DX
製造業に特化したデジタルトランスフォーメーション(DX)の実現を目指す請負開発型のコンサルティングサービスです。AI、iPaaS、および先端の技術を駆使して、製造プロセスの効率化、業務効率化、チームワーク強化、コスト削減、品質向上を実現します。このサービスは、製造業の課題を深く理解し、それに対する最適なデジタルソリューションを提供することで、企業が持続的な成長とイノベーションを達成できるようサポートします。
オンライン講座
製造業、主に購買・調達部門にお勤めの方々に向けた情報を配信しております。
新任の方やベテランの方、管理職を対象とした幅広いコンテンツをご用意しております。
お問い合わせ
コストダウンが利益に直結する術だと理解していても、なかなか前に進めることができない状況。そんな時は、newjiのコストダウン自動化機能で大きく利益貢献しよう!
(Β版非公開)