- お役立ち記事
- Strengthening Quality Control Through Measuring Equipment Selection
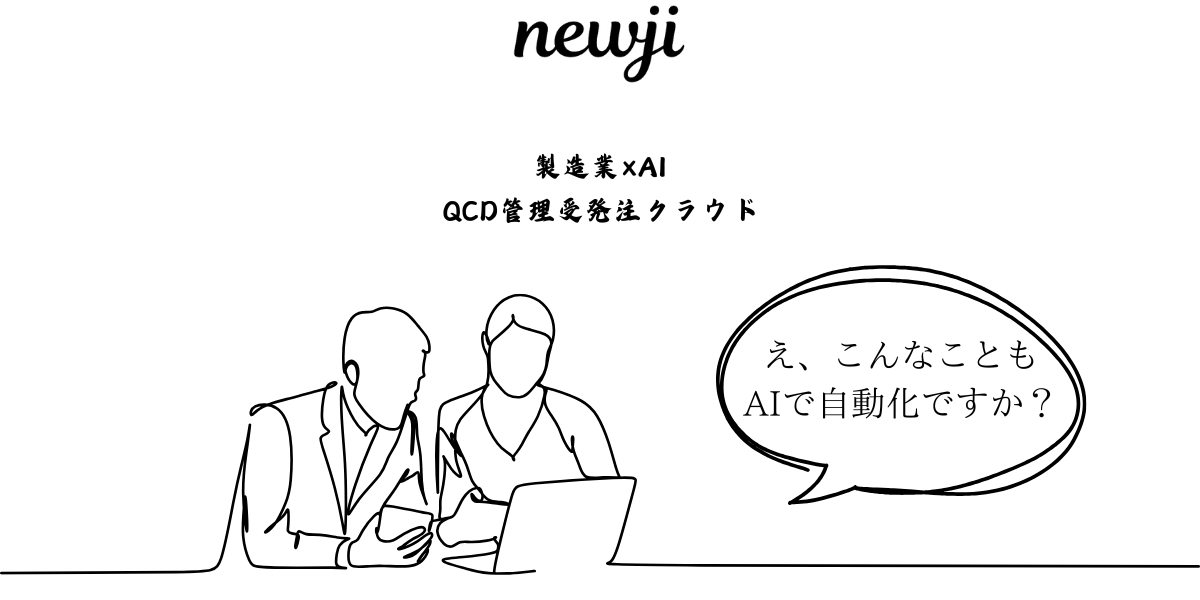
Strengthening Quality Control Through Measuring Equipment Selection
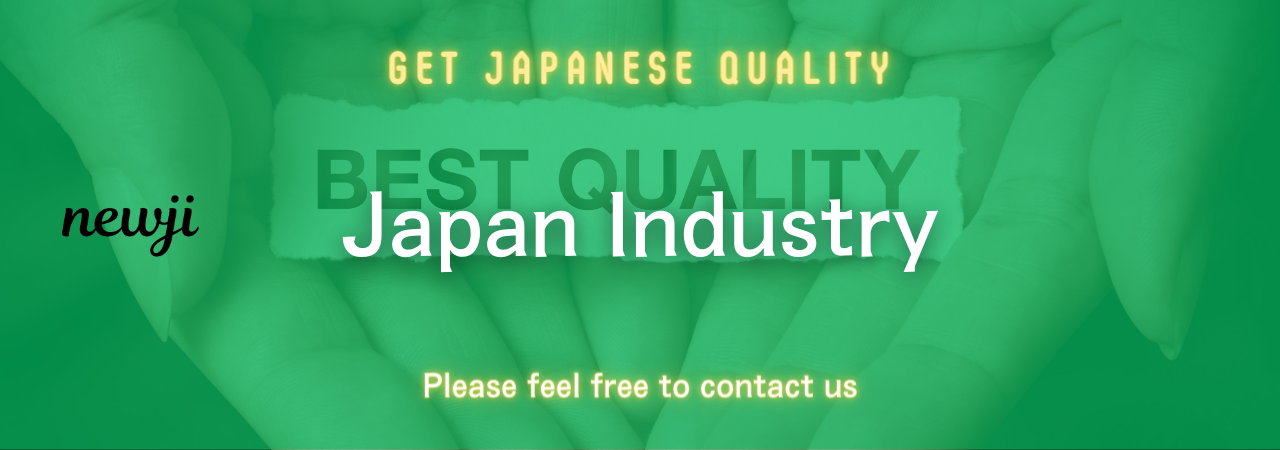
Quality control is a critical aspect of any manufacturing or production process.
Ensuring that products meet the required standards and specifications is vital to maintaining customer satisfaction and industry credibility.
One of the key elements in achieving robust quality control is the careful selection of measuring equipment.
Choosing the right tools can make a significant difference in your ability to monitor and maintain product quality consistently.
目次
Understanding Quality Control
Quality control (QC) involves all the activities and processes companies use to ensure their products meet specific standards.
Effective QC helps identify defects, reduce errors, and ensure consistent product quality.
Quality control measures can include inspections, testing, and the use of measuring equipment to verify product specifications.
The Role of Measuring Equipment in Quality Control
Measuring equipment is essential in the QC process.
Accurate measurements are crucial for verifying that products meet design specifications and customer expectations.
Incorrect or inconsistent measurements can lead to defective products, which can harm a company’s reputation and increase costs due to rework or returns.
Types of Measuring Equipment
Various types of measuring equipment are available for different applications.
Each tool is designed to measure specific parameters, such as length, weight, temperature, and more.
Some commonly used measuring equipment includes:
Calipers
Calipers are precision instruments used to measure the distance between two opposite sides of an object.
They come in digital, dial, and vernier formats and are essential for measuring small components with high accuracy.
Micrometers
Micrometers offer highly precise measurements for tiny objects.
They are particularly useful in mechanical engineering and manufacturing processes requiring fine tolerances.
Coordinate Measuring Machines (CMM)
CMMs are advanced tools that measure the physical geometrical characteristics of an object.
They use a probe to detect discrete points on the surface of the object and are often used in quality assurance and manufacturing processes.
Gauges
Gauges, such as go/no-go gauges, are used to quickly and easily check whether parts fall within specified tolerances.
They provide a simple pass-or-fail result.
Factors to Consider When Selecting Measuring Equipment
Choosing the right measuring equipment for your quality control processes requires careful consideration of several factors.
Each factor plays a crucial role in ensuring that the selected tool meets your specific needs and enhances your QC efforts.
Accuracy and Precision
Accuracy refers to how close a measurement is to the true value, while precision indicates the repeatability of the measurement.
Selecting equipment with high accuracy and precision is crucial to obtaining reliable data for quality control.
Measurement Range
The measurement range refers to the span of values a device can measure.
Ensure that the equipment you choose can measure the full range of dimensions or values you need to monitor.
Resolution
Resolution is the smallest increment a measuring device can detect.
Higher resolution provides more detailed measurement data, which can be critical for parts with tight tolerances.
Environmental Conditions
Consider the environmental conditions in which the measuring equipment will be used.
Factors such as temperature, humidity, and exposure to dust or water can affect the accuracy and reliability of the measurements.
Choose equipment that is designed to withstand the specific conditions of your production environment.
Benefits of Choosing the Right Measuring Equipment
Investing time and resources in selecting the appropriate measuring equipment can yield significant benefits for your quality control processes.
These benefits include:
Improved Product Quality
Using accurate and reliable measuring equipment ensures that your products consistently meet specifications.
This leads to higher product quality and reduces the likelihood of defects.
Increased Efficiency
Precision measuring tools can streamline your quality control processes.
Faster, more accurate measurements lead to quicker inspections and shorter production cycles.
Cost Savings
By reducing defects and ensuring consistent product quality, you can minimize the costs associated with rework, returns, and warranty claims.
This leads to significant cost savings in the long run.
Enhanced Reputation
Delivering high-quality products consistently enhances your company’s reputation in the market.
Satisfied customers are more likely to become repeat customers and recommend your products to others.
Common Challenges in Measuring Equipment Selection
While selecting measuring equipment is critical for quality control, it is not without challenges.
Understanding these challenges can help you make informed decisions and avoid potential pitfalls.
Cost Constraints
High-quality measuring equipment can be expensive.
Balancing the need for precision and accuracy with budget constraints can be challenging.
It’s essential to consider the long-term benefits and cost savings that reliable measuring equipment can provide.
Training Requirements
Properly using and maintaining measuring equipment often requires specialized training.
Ensuring that staff are adequately trained can be time-consuming and costly.
However, investing in training is crucial for achieving accurate measurements and maximizing the efficiency and longevity of the equipment.
Conclusion
Strengthening quality control through the careful selection of measuring equipment is a strategic investment that can yield substantial benefits for any manufacturing operation.
By understanding the role of various measuring tools, considering key factors, and addressing common challenges, you can enhance your quality control processes and deliver superior products to your customers.
Accurate measurements lead to better quality, increased efficiency, and cost savings, ultimately contributing to your company’s success and reputation in the marketplace.
資料ダウンロード
QCD調達購買管理クラウド「newji」は、調達購買部門で必要なQCD管理全てを備えた、現場特化型兼クラウド型の今世紀最高の購買管理システムとなります。
ユーザー登録
調達購買業務の効率化だけでなく、システムを導入することで、コスト削減や製品・資材のステータス可視化のほか、属人化していた購買情報の共有化による内部不正防止や統制にも役立ちます。
NEWJI DX
製造業に特化したデジタルトランスフォーメーション(DX)の実現を目指す請負開発型のコンサルティングサービスです。AI、iPaaS、および先端の技術を駆使して、製造プロセスの効率化、業務効率化、チームワーク強化、コスト削減、品質向上を実現します。このサービスは、製造業の課題を深く理解し、それに対する最適なデジタルソリューションを提供することで、企業が持続的な成長とイノベーションを達成できるようサポートします。
オンライン講座
製造業、主に購買・調達部門にお勤めの方々に向けた情報を配信しております。
新任の方やベテランの方、管理職を対象とした幅広いコンテンツをご用意しております。
お問い合わせ
コストダウンが利益に直結する術だと理解していても、なかなか前に進めることができない状況。そんな時は、newjiのコストダウン自動化機能で大きく利益貢献しよう!
(Β版非公開)