- お役立ち記事
- Stress Concentration Analysis and Fatigue Strength Evaluation Using CAE
Stress Concentration Analysis and Fatigue Strength Evaluation Using CAE
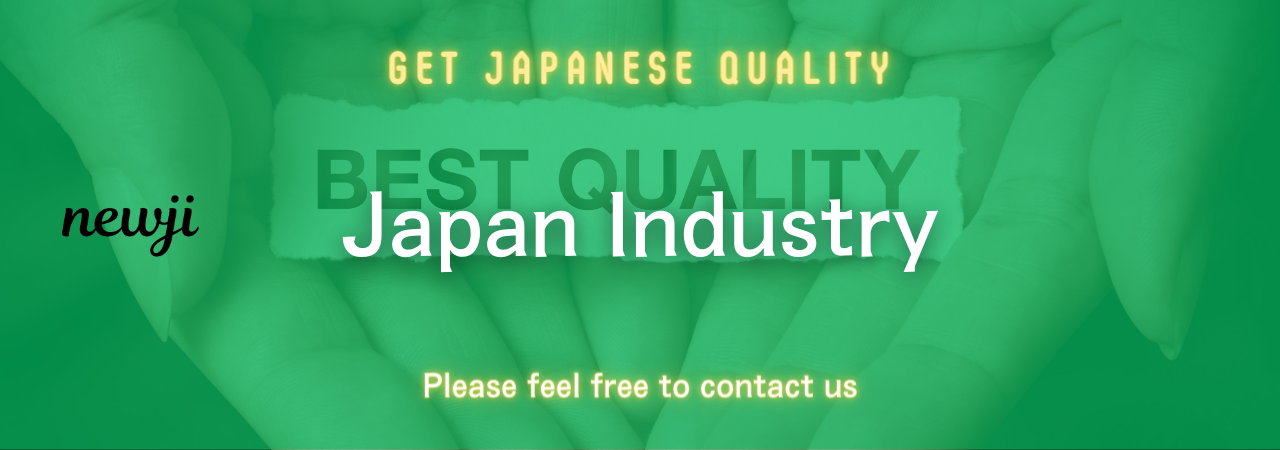
目次
Understanding Stress Concentration
Stress concentration refers to locations in a material where stress is significantly higher than the surrounding area.
These areas typically occur around abrupt changes in geometry, such as holes, notches, or sharp corners.
Understanding stress concentration is important because it can significantly impact the strength and fatigue life of a material or component.
When the stress exceeds the material’s strength in these localized areas, it can lead to failure, even if the rest of the component is not under significant stress.
In engineering, identifying and mitigating stress concentration points is critical to ensure durability and longevity of the components.
Without considering stress concentration, components may fail unexpectedly, leading to costly repairs or potentially catastrophic outcomes.
Causes of Stress Concentration
Stress concentration is primarily caused by the geometry of the component.
Any sudden change in the shape or material properties can cause stress to concentrate.
Common examples include holes, grooves, sharp corners, and various types of notches.
In some cases, abrupt changes in the material properties, such as a sudden transition from a stiff to a more flexible material, can also lead to stress concentration.
The degree of stress concentration is often quantified by a factor known as the Stress Concentration Factor (SCF).
This factor is the ratio of the highest stress in the component to the reference stress and varies depending on the geometry and loading conditions.
Fatigue Strength and Its Importance
Fatigue strength is the ability of a material to withstand cyclic loading without failure over an extended period.
It is a critical parameter in the design of components that experience repeated or fluctuating loads throughout their service life.
When a material is subject to cyclic loading, as opposed to a static load, it can fail at stress levels lower than its ultimate tensile strength.
This failure mechanism is known as fatigue.
Fatigue failure is characterized by the initiation and propagation of cracks, which ultimately leads to the fracture of the material.
Understanding and evaluating fatigue strength is crucial for designing safe and reliable components, especially in industries such as aerospace, automotive, and construction where components are subject to repetitive loading.
Factors Affecting Fatigue Strength
Several factors can influence the fatigue strength of a material.
Material properties such as tensile strength, ductility, and toughness play a significant role.
Environmental conditions, including temperature and corrosive environments, can also affect fatigue strength.
Furthermore, the presence of stress concentration points, as discussed earlier, can dramatically reduce fatigue strength.
A small crack or imperfection at a location of high stress concentration can quickly grow under cyclic loading, leading to premature failure.
An Overview of CAE in Stress Analysis
CAE, or Computer Aided Engineering, plays a crucial role in stress concentration analysis and fatigue strength evaluation.
CAE tools allow engineers to simulate and analyze structural components under various loads and conditions to predict how they will perform.
By using CAE, engineers can identify potential problem areas in a design before physical prototypes are built, saving both time and cost.
These tools provide visual representations of stress and deformation, making it easier for engineers to identify and address stress concentration points.
Benefits of Using CAE
The use of CAE offers numerous benefits in the context of stress analysis.
Firstly, it allows for rapid prototyping and testing of multiple design iterations without the need for physical models.
This significantly speeds up the design process and enables more innovative solutions.
CAE also improves the accuracy of stress and fatigue predictions by using advanced algorithms and real-world data to simulate different scenarios.
This means that potential issues can be identified and mitigated earlier in the design process, resulting in a more reliable end product.
Evaluating Fatigue Strength with CAE
Using CAE, engineers can evaluate the fatigue strength of components through simulations that mimic real-world operating conditions.
These simulations help in predicting how and where a component might fail due to fatigue.
By inputting various parameters, such as material properties, loading conditions, and environmental factors, engineers can assess the potential for fatigue failure and make informed decisions to improve the design.
For example, they might alter the geometry to reduce stress concentration or select a different material with better fatigue properties.
Implementing CAE Analysis
To implement CAE analysis effectively, engineers start by creating a detailed digital model of the component or assembly.
This model is then subjected to simulated loads and constraints to observe how it reacts.
The analysis software provides data on stress distribution and identifies critical areas prone to high stress concentration.
Based on these results, engineers can refine the design by smoothing out sharp corners, adding fillets, or making material changes to improve the component’s fatigue strength.
Conclusion
In conclusion, understanding stress concentration and evaluating fatigue strength are vital tasks in the engineering design process.
These aspects ensure that components can withstand operational demands without unexpected failures.
CAE tools have revolutionized how engineers approach these tasks, providing accurate simulations that enhance the reliability and safety of engineering designs.
By leveraging CAE for stress and fatigue analysis, engineers can optimize components for strength and durability, ultimately leading to more robust and longer-lasting products.
資料ダウンロード
QCD調達購買管理クラウド「newji」は、調達購買部門で必要なQCD管理全てを備えた、現場特化型兼クラウド型の今世紀最高の購買管理システムとなります。
ユーザー登録
調達購買業務の効率化だけでなく、システムを導入することで、コスト削減や製品・資材のステータス可視化のほか、属人化していた購買情報の共有化による内部不正防止や統制にも役立ちます。
NEWJI DX
製造業に特化したデジタルトランスフォーメーション(DX)の実現を目指す請負開発型のコンサルティングサービスです。AI、iPaaS、および先端の技術を駆使して、製造プロセスの効率化、業務効率化、チームワーク強化、コスト削減、品質向上を実現します。このサービスは、製造業の課題を深く理解し、それに対する最適なデジタルソリューションを提供することで、企業が持続的な成長とイノベーションを達成できるようサポートします。
オンライン講座
製造業、主に購買・調達部門にお勤めの方々に向けた情報を配信しております。
新任の方やベテランの方、管理職を対象とした幅広いコンテンツをご用意しております。
お問い合わせ
コストダウンが利益に直結する術だと理解していても、なかなか前に進めることができない状況。そんな時は、newjiのコストダウン自動化機能で大きく利益貢献しよう!
(Β版非公開)