- お役立ち記事
- Stress concentration generation mechanism, key points of stress analysis by CAE, and application to fatigue strength evaluation
月間76,176名の
製造業ご担当者様が閲覧しています*
*2025年3月31日現在のGoogle Analyticsのデータより
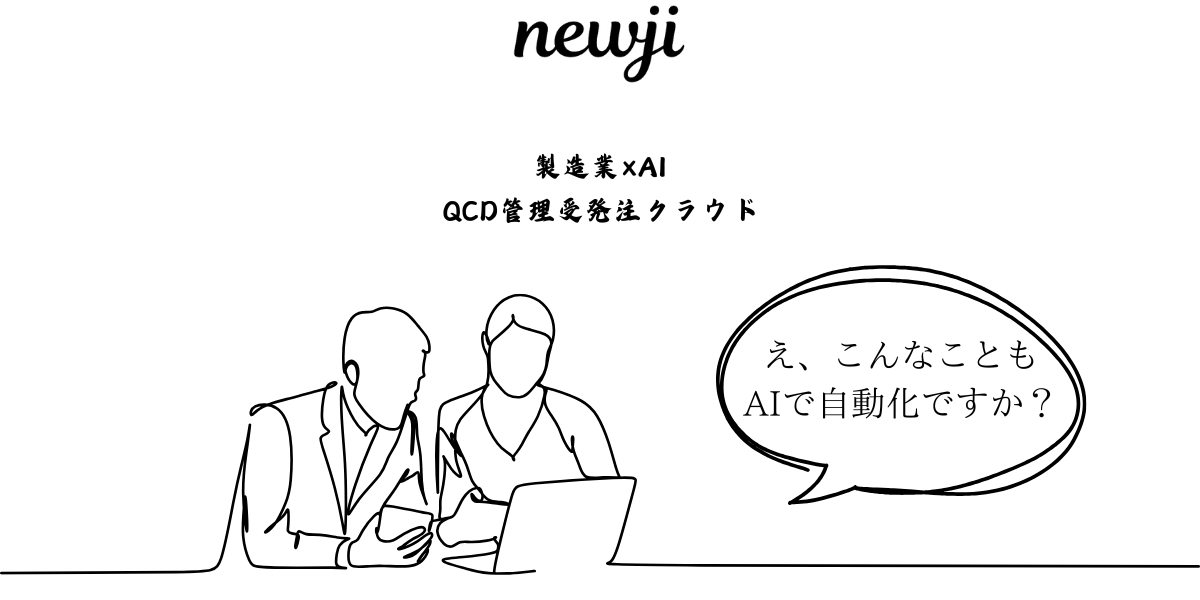
Stress concentration generation mechanism, key points of stress analysis by CAE, and application to fatigue strength evaluation
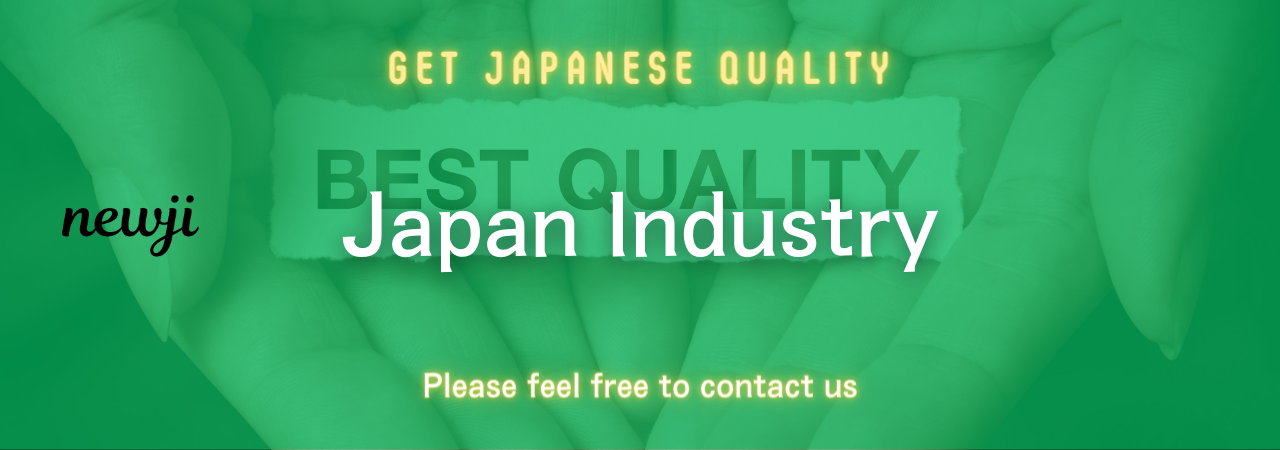
目次
Understanding Stress Concentration and Its Mechanism
The concept of stress concentration is integral in understanding material behavior under various conditions.
When components are under load, stress is not always uniformly distributed.
Stress concentration refers to locations within a material where stress is higher than the average stress experienced by the material overall.
Understanding how and why these concentrations occur is essential for engineers and designers in order to enhance the durability and safety of structures.
Stress concentration typically arises from geometric discontinuities or irregularities within a material or component.
These irregularities can include holes, grooves, notches, or any sudden changes in cross-section.
When material experiences force or load, these irregular features cause localized increases in stress levels.
The mechanism behind stress concentration is straightforward.
When a load is applied to a material with a geometric discontinuity, such as a notch, the material near the discontinuity cannot carry the load as effectively as the surrounding material.
As a result, stress is redistributed around the notch, leading to localized increases in stress.
This localized increase can be significant enough to cause premature failure at lower loads than anticipated.
Key Points of Stress Analysis by CAE
Computer-Aided Engineering (CAE) tools are crucial in stress analysis as they allow for detailed examination of how materials and structures respond under various loads.
Stress analysis through CAE helps to predict potential failure points and optimize design.
1. Accurate Geometry Modeling
One of the first steps in effective stress analysis is accurate geometry modeling.
CAE tools can simulate complex geometries and provide a faithful representation of the component.
This accuracy is crucial for pinpointing potential areas of stress concentration.
2. Material Properties
Correct attribution of material properties is another key aspect.
CAE tools require inputs regarding the material’s mechanical characteristics, such as Young’s modulus, Poisson’s ratio, and yield strength.
These properties significantly influence how stresses are distributed in the model.
3. Boundary Conditions and Loading
Accurate application of boundary conditions and loading situations is necessary to simulate real-life scenarios.
CAE software can efficiently replicate various loading conditions, including static, dynamic, thermal, and complex loading scenarios.
4. Mesh Quality and Refinement
Mesh generation is a critical step in CAE simulations.
A more refined mesh at anticipated areas of high stress concentration can provide more accurate results.
However, this requires balancing accuracy with computational resources.
5. Validation and Verification
Finally, it is important to validate and verify the CAE model against experimental data or established analytical solutions.
This process ensures that the model accurately predicts the behavior of the actual component under study.
Application to Fatigue Strength Evaluation
Fatigue strength evaluation is an area where stress analysis, particularly through CAE, plays a pivotal role.
Fatigue failure occurs due to repeated or cyclic loading, usually at stress levels lower than the material’s ultimate tensile strength.
1. Identifying Critical Areas
Stress analysis helps in identifying critical locations within a component where fatigue failure is likely to occur.
These are usually regions with high stress concentration.
2. Life Prediction
Using CAE tools, engineers can predict the component’s fatigue life by assessing the accumulated damage over repeated load cycles.
This assessment typically uses empirical data and models like the S-N curve, which plots stress amplitude against the number of cycles to failure.
3. Design Optimization
CAE-driven stress analysis enables engineers to modify designs to improve fatigue strength.
This might include changes in material selection, geometry, or surface treatments to mitigate stress concentration effects.
4. Sensitivity Analysis
Sensitivity analysis can help engineers understand how variations in design parameters affect fatigue life.
By simulating different scenarios, engineers can determine which factors have the most significant impact and adjust designs accordingly.
5. Case Studies and Implementation
Real-world case studies highlight the importance of stress analysis in fatigue strength evaluation.
For example, in the aerospace industry, components are subjected to rigorous stress analysis to ensure safety and reliability.
The use of CAE in these evaluations helps in preventing catastrophic failures and maintaining structural integrity over the lifespan of the component.
In conclusion, understanding the mechanism behind stress concentration and applying CAE tools effectively are key to enhancing the design and evaluation of components under stress.
The ability to predict potential failure points and optimize design through stress analysis ensures the safety, durability, and longevity of engineering structures.
資料ダウンロード
QCD管理受発注クラウド「newji」は、受発注部門で必要なQCD管理全てを備えた、現場特化型兼クラウド型の今世紀最高の受発注管理システムとなります。
ユーザー登録
受発注業務の効率化だけでなく、システムを導入することで、コスト削減や製品・資材のステータス可視化のほか、属人化していた受発注情報の共有化による内部不正防止や統制にも役立ちます。
NEWJI DX
製造業に特化したデジタルトランスフォーメーション(DX)の実現を目指す請負開発型のコンサルティングサービスです。AI、iPaaS、および先端の技術を駆使して、製造プロセスの効率化、業務効率化、チームワーク強化、コスト削減、品質向上を実現します。このサービスは、製造業の課題を深く理解し、それに対する最適なデジタルソリューションを提供することで、企業が持続的な成長とイノベーションを達成できるようサポートします。
製造業ニュース解説
製造業、主に購買・調達部門にお勤めの方々に向けた情報を配信しております。
新任の方やベテランの方、管理職を対象とした幅広いコンテンツをご用意しております。
お問い合わせ
コストダウンが利益に直結する術だと理解していても、なかなか前に進めることができない状況。そんな時は、newjiのコストダウン自動化機能で大きく利益貢献しよう!
(β版非公開)