- お役立ち記事
- Stress Relaxation Design and Warp Prevention in Semiconductor Packages
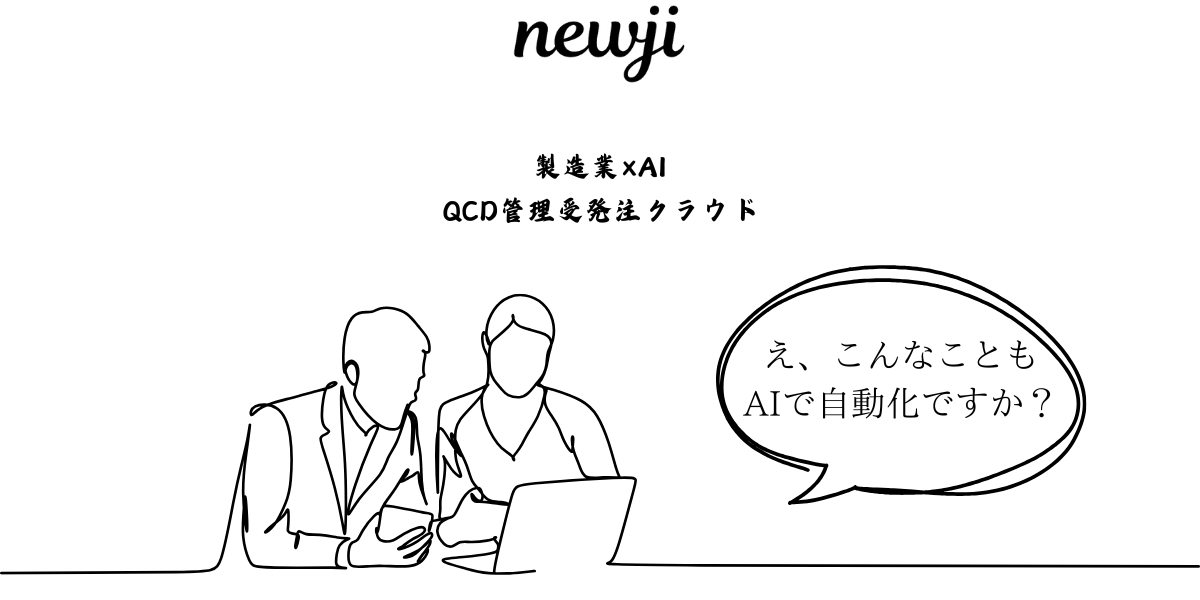
Stress Relaxation Design and Warp Prevention in Semiconductor Packages
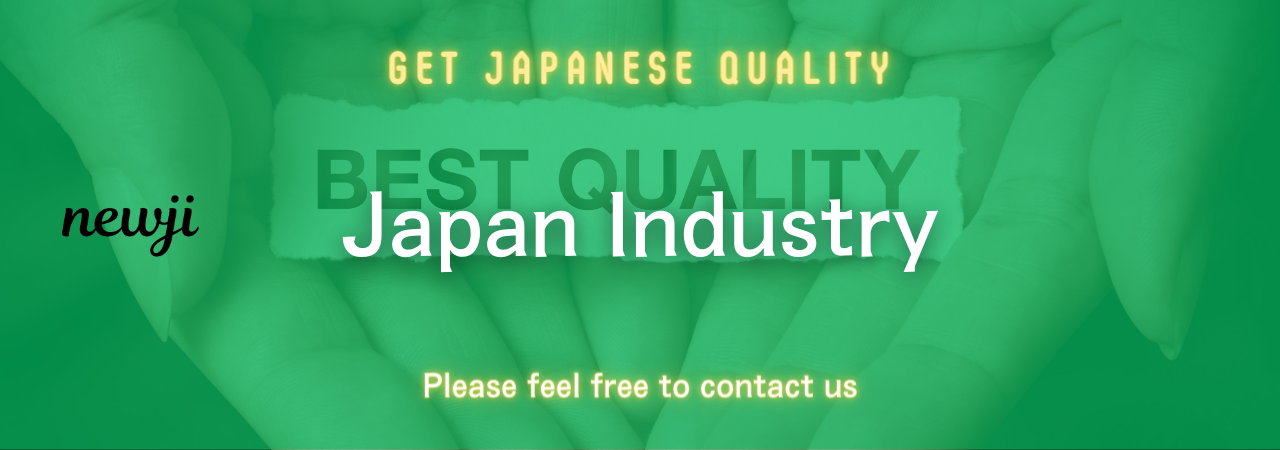
Semiconductor packages are intricate assemblies used to protect and connect electronic components.
They are essential in various electronics, such as smartphones, computers, and other digital devices.
To maintain the performance and reliability of these devices, a key consideration is the stress relaxation design and warp prevention in semiconductor packages.
Understanding the importance and methods of managing these factors is crucial for anyone in the field of electronics manufacturing.
目次
Why Stress Relaxation Design Matters
Stress relaxation design is crucial because it mitigates the effects of mechanical stress on the semiconductor package.
Mechanical stresses can arise from various sources, including differences in thermal expansion rates of the materials used, external forces, and even during the manufacturing process itself.
If not properly managed, these stresses can lead to package failures, such as cracking, delamination, or warping.
Sources of Mechanical Stress
Mechanical stresses originate from various sources in the manufacturing and operational phases.
During manufacturing, stresses can occur due to the high temperatures used in processes like solder reflow.
In operation, the cycles of heating and cooling that electronic devices undergo can cause stresses due to the different expansion rates of materials.
External factors, such as shocks, vibrations, and even regular usage, also contribute to the accumulation of stress over time.
Material Selection
Choosing the right materials is a foundation for effective stress relaxation design.
Materials with compatible thermal expansion coefficients minimize differential expansion-contraction patterns, thereby reducing stress.
Flexible and resilient materials, such as certain polymers and composite materials, can absorb some of the stress and prevent it from affecting the semiconductor die or other fragile components.
Structural Design Considerations
Thoughtful structural design is another critical component of stress relaxation.
Incorporating features like stress relief slots and compliant interconnections can significantly reduce stress concentrations.
Using a layered design can also help distribute stress more evenly across the package, thus avoiding localized failures.
Preventing Warp in Semiconductor Packages
Warp, also known as warpage, occurs when a package bends or twists.
This can lead to several issues, including misalignment during board assembly, impaired electrical connections, and physical damage to the semiconductor die.
Understanding the Causes of Warp
Warping occurs primarily due to thermal mismatches between the different materials used in the package.
These mismatches cause uneven expansion and contraction with temperature changes.
For example, metals and ceramics expand at different rates than polymers, leading to internal stresses that can cause the package to warp.
Moisture absorption can exacerbate this issue, as absorbed moisture can cause some materials to swell unevenly.
Design and Material Strategies
Preventing warp involves a combination of design strategies and careful material selection.
One popular approach is to use materials with similar coefficients of thermal expansion (CTE) to ensure uniform expansion and contraction.
Additionally, manufacturers can use balanced designs that distribute stresses symmetrically to avoid warping.
Pre-baking components to remove moisture before assembly and encapsulating sensitive components to protect them from environmental factors can also mitigate the risk of warp.
Advanced Manufacturing Techniques
Adopting advanced manufacturing techniques can also contribute significantly to warp prevention.
Using precision alignment and bonding techniques helps ensure that all elements of the package are perfectly aligned and bonded with minimal internal stresses.
Laser-assisted bonding and precision placement equipment offer higher accuracy and consistency, thus reducing the chances of warp.
Examples from Industry
Understanding the real-world applications of these practices can provide valuable insights into their effectiveness.
Several semiconductor manufacturers have successfully implemented these principles to enhance product reliability.
Case Study: XYZ Corporation
XYZ Corporation, a global leader in semiconductor manufacturing, faced significant challenges with warping in their advanced packaging solutions.
By adopting a strategic approach that combined material selection with structural design, they managed to eliminate most instances of warping.
They introduced materials with closely matched CTEs and incorporated stress relief slots in their designs.
Furthermore, they invested in advanced manufacturing equipment, which allowed for more precise alignment and lower residual stresses.
Case Study: ABC Electronics
ABC Electronics, another key player in the industry, focused on stress relaxation design to improve the reliability of their semiconductor packages.
They employed a combination of stress-analysis simulations and real-world testing to identify critical areas of stress concentration.
By modifying the package designs and selecting better-suited materials, they were able to significantly reduce mechanical stress.
The integration of flexible interconnections and layered design strategies also played a pivotal role in enhancing package reliability.
Conclusion
Stress relaxation design and warp prevention are integral to the reliability and performance of semiconductor packages.
Understanding the sources of mechanical stress, selecting suitable materials, and implementing thoughtful structural designs are key to managing these challenges.
Real-world examples from leading semiconductor manufacturers showcase the effectiveness of these strategies.
By prioritizing these considerations in the design and manufacturing processes, the reliability of semiconductor packages can be significantly enhanced, ensuring the optimal performance of electronic devices in various applications.
資料ダウンロード
QCD調達購買管理クラウド「newji」は、調達購買部門で必要なQCD管理全てを備えた、現場特化型兼クラウド型の今世紀最高の購買管理システムとなります。
ユーザー登録
調達購買業務の効率化だけでなく、システムを導入することで、コスト削減や製品・資材のステータス可視化のほか、属人化していた購買情報の共有化による内部不正防止や統制にも役立ちます。
NEWJI DX
製造業に特化したデジタルトランスフォーメーション(DX)の実現を目指す請負開発型のコンサルティングサービスです。AI、iPaaS、および先端の技術を駆使して、製造プロセスの効率化、業務効率化、チームワーク強化、コスト削減、品質向上を実現します。このサービスは、製造業の課題を深く理解し、それに対する最適なデジタルソリューションを提供することで、企業が持続的な成長とイノベーションを達成できるようサポートします。
オンライン講座
製造業、主に購買・調達部門にお勤めの方々に向けた情報を配信しております。
新任の方やベテランの方、管理職を対象とした幅広いコンテンツをご用意しております。
お問い合わせ
コストダウンが利益に直結する術だと理解していても、なかなか前に進めることができない状況。そんな時は、newjiのコストダウン自動化機能で大きく利益貢献しよう!
(Β版非公開)