- お役立ち記事
- Structure and process of main printed wiring boards
Structure and process of main printed wiring boards
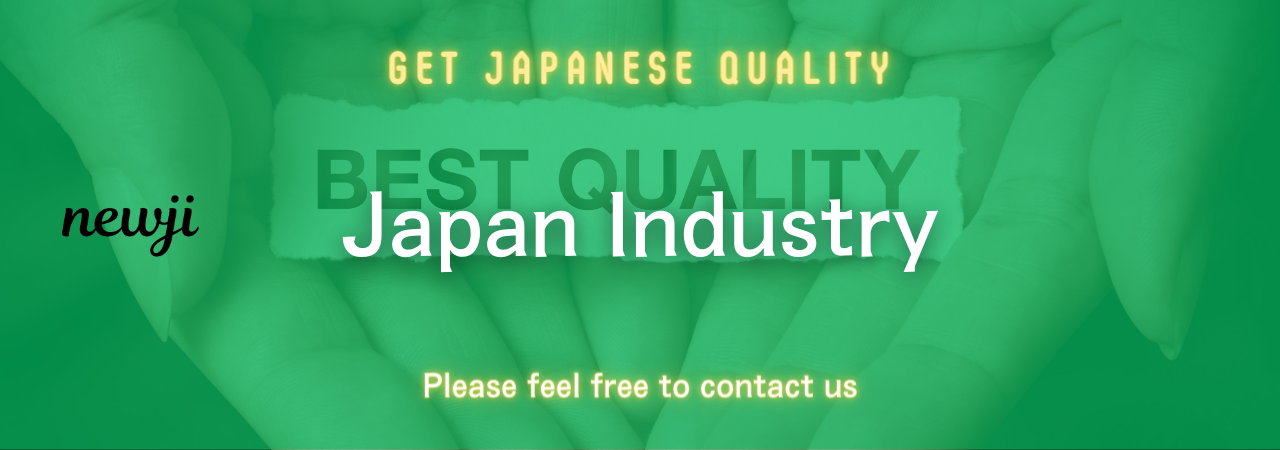
目次
Introduction to Printed Wiring Boards
Printed Wiring Boards (PWBs), often referred to as Printed Circuit Boards (PCBs), are essential components in virtually all electronic devices.
These boards mechanically support and electrically connect electronic components using conductive pathways, tracks, or signal traces.
Understanding the structure and process involved in creating PWBs is crucial for anyone interested in electronics and technology.
The Structure of Printed Wiring Boards
Printed wiring boards come in various forms based on their complexity and usage.
However, most PWBs share a standard structural format.
Let’s examine each layer and its role in the board’s functionality.
Base Material
The foundation of any PWB is the substrate, commonly made of fiberglass or epoxy composites.
The base material provides mechanical support and insulation to the board.
A widely used substrate is FR-4, a composite material made from woven fiberglass cloth with an epoxy resin binder that is flame resistant.
The choice of substrate depends significantly on the application’s environmental and mechanical requirements.
Copper Layers
Copper layers are crucial for PWBs because they conduct electricity.
These layers are installed above the substrate and are usually very thin copper foil adhered to the base material.
Single-layer boards have one copper layer, while double or multi-layer boards can have more than one.
The complexity of the PWB dictates the number of copper layers required.
Solder Mask
Above the copper layer lies the solder mask, typically a green layer, although other colors are available.
The solder mask serves mainly as a protective layer for the copper circuits.
It ensures that there is no accidental solder bridging between pathways and protects against environmental factors that might degrade the copper.
Silkscreen
The silkscreen is the topmost layer that adds labels to the PWB.
These labels can be symbols, numbers, or letters that identify different components and test points on the board.
Although not functional in terms of electronic performance, the silkscreen is essential for assembly, maintenance, and repairs.
The Process of PWB Manufacturing
Creating printed wiring boards involves a meticulous process that combines both mechanical and chemical techniques.
Let’s go through the main steps involved in manufacturing PWBs:
Design and Layout
The first step in the PWB manufacturing process is the design and layout.
Electrical engineers use specialized software like CAD (Computer-Aided Design) to layout the PWB’s schematic.
During this phase, they place the components and routing tracks.
Design considerations include minimizing interference, optimal positioning, and meeting size constraints.
Printing the Circuit Pattern
Once the design is finalized, the circuit pattern is printed directly onto the copper layers.
This is done using a photographic method for precision.
A photoresist layer, sensitive to ultraviolet light, is applied, which helps in transferring the circuit pattern onto the panel.
Etching
Etching is a crucial step in creating the PWB.
During this phase, chemical solutions are used to remove excess copper, leaving only the desired circuit paths.
Controlled etching ensures that the paths are precise, free of defects, and maintain the design integrity.
Lamination
In multi-layer PWBs, an additional process known as lamination is required.
Lamination fuses multiple layers of substrate and circuits together under heat and pressure.
The alignment during lamination is critical to ensure the electrical connections line up across layers.
Drilling
After lamination, holes need to be drilled into the PWB to prepare for component placement.
These holes serve as the connection points for through-hole components or inter-layer connections, referred to as vias.
Advanced machines using CAM (Computer-Aided Manufacturing) technology ensure precision and speed in this process.
Plating and Coating
The exposed surfaces and holes are plated with copper, providing a conductive layer that connects different board layers.
After plating, the boards are usually coated with a protective layer like solder mask to protect against oxidation and ensure reliability when components are soldered onto the board.
Testing and Quality Control
Once manufacturing is complete, the PWB undergoes thorough testing to ensure functionality and reliability.
Quality control checks, such as automated optical inspection (AOI) and electrical testing, assess the board for any defects or design discrepancies.
Only those that pass these stringent tests proceed to the assembly phase.
Conclusion
Understanding the structure and process of printed wiring boards is fundamental in the world of electronics.
The intricacies involved in their creation ensure that electronic devices operate efficiently and reliably.
Whether you’re an engineer, hobbyist, or simply curious, this knowledge provides insight into the backbone of modern electronic technology.
資料ダウンロード
QCD調達購買管理クラウド「newji」は、調達購買部門で必要なQCD管理全てを備えた、現場特化型兼クラウド型の今世紀最高の購買管理システムとなります。
ユーザー登録
調達購買業務の効率化だけでなく、システムを導入することで、コスト削減や製品・資材のステータス可視化のほか、属人化していた購買情報の共有化による内部不正防止や統制にも役立ちます。
NEWJI DX
製造業に特化したデジタルトランスフォーメーション(DX)の実現を目指す請負開発型のコンサルティングサービスです。AI、iPaaS、および先端の技術を駆使して、製造プロセスの効率化、業務効率化、チームワーク強化、コスト削減、品質向上を実現します。このサービスは、製造業の課題を深く理解し、それに対する最適なデジタルソリューションを提供することで、企業が持続的な成長とイノベーションを達成できるようサポートします。
オンライン講座
製造業、主に購買・調達部門にお勤めの方々に向けた情報を配信しております。
新任の方やベテランの方、管理職を対象とした幅広いコンテンツをご用意しております。
お問い合わせ
コストダウンが利益に直結する術だと理解していても、なかなか前に進めることができない状況。そんな時は、newjiのコストダウン自動化機能で大きく利益貢献しよう!
(Β版非公開)