- お役立ち記事
- Success Stories in Manufacturing Micro Components Using Precision Injection Molding
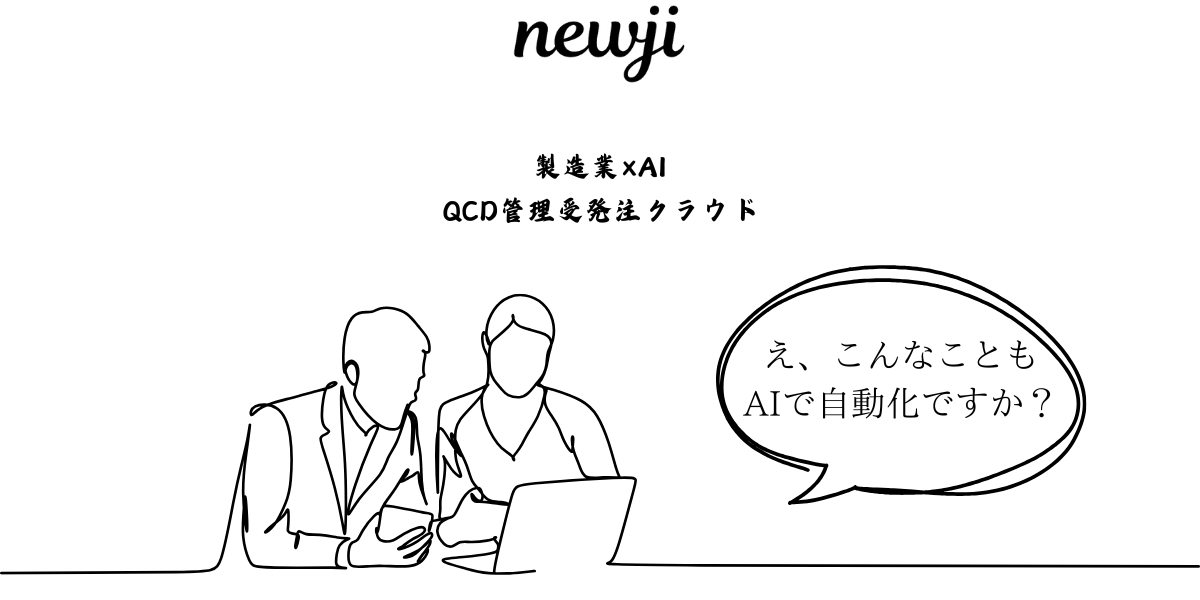
Success Stories in Manufacturing Micro Components Using Precision Injection Molding
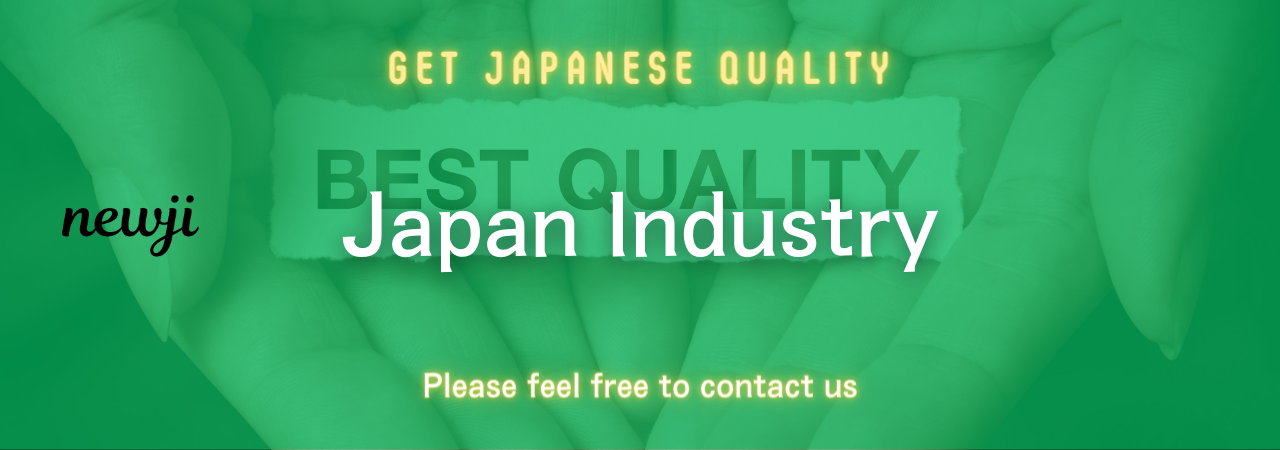
目次
Understanding Precision Injection Molding
Precision injection molding is a highly specialized process used to create tiny, complex components with exact specifications.
This manufacturing technique involves injecting molten materials, often plastics, into a mold cavity, under high pressure.
It is widely used in industries where consistency, strength, and intricate details matter the most.
Micro components manufactured through precision injection molding play critical roles in various applications, from consumer electronics to medical devices.
As technology advances, the demand for smaller, more precise components continues to grow, making this form of injection molding increasingly relevant.
Key Factors in Successful Precision Molding
The success of precision injection molding depends on several crucial factors.
The mold design is arguably the most important, as it dictates the shape, complexity, and quality of the final product.
A well-designed mold allows for optimum material flow, minimum waste, and effective cooling, all of which are essential for high-quality outcomes.
Another critical factor is the choice of materials.
The material must have the right properties to withstand both the mold-making and injection processes.
Commonly used materials include thermoplastics, which are known for their durability and versatility.
Moreover, the injection process itself requires meticulous control over parameters such as temperature, pressure, and timing.
Precision in these aspects ensures the finished components meet the necessary tolerances and specifications.
Success Stories in Micro Component Manufacturing
There are numerous success stories demonstrating the potential of precision injection molding in creating micro components.
One such example is within the medical industry where manufacturers produce tiny, yet highly complex parts for devices such as hearing aids and surgical tools.
These components require not only precision but also biocompatibility – a feature well-achieved through precision injection molding.
By using specialized medical-grade materials, manufacturers can produce parts that meet strict regulatory standards.
In the electronics industry, the creation of components for smartphones and wearables is another success story.
Manufacturers use this technique to produce small yet complex parts such as connectors and housings.
These components must be robust enough to handle daily wear while maintaining the technology’s sleek design.
Improving Manufacturing Efficiency
Beyond simply making quality parts, precision injection molding offers significant advantages in terms of manufacturing efficiency.
This process is known for its high repeatability, meaning manufacturers can produce large volumes of identical components without variations.
This consistency not only ensures product quality but also reduces waste, saving both materials and costs.
Moreover, advancements in technology such as computer-aided design (CAD) and computer-aided manufacturing (CAM) have further optimized the injection molding process.
These tools allow for accurate design and simulation, which helps predict potential issues before mass production, thereby reducing trial and error.
The Role of Innovation
Innovation continues to drive the success of precision injection molding in the manufacturing of micro components.
From materials science to automation, ongoing advancements are constantly pushing the boundaries of what’s possible.
For instance, newer materials are being developed to address specific industry needs, such as resistance to extreme temperatures or enhanced structural properties.
These innovations make it possible to create components that were previously impossible or impractical to produce.
Additionally, the integration of automation and robotics into injection molding setups improves not just speed but also accuracy and safety.
Robots can handle more complex tasks at different stages of the process, from loading materials to assembling parts, further enhancing the precision and efficiency of manufacturing efforts.
Challenges and Solutions in Precision Molding
Despite its many advantages, precision injection molding does present several challenges.
Achieving the desired precision often requires significant expertise and experience, especially in mold design and material selection.
Moreover, the initial costs for setting up a precision injection molding operation can be high, which may be a barrier for some manufacturers.
However, the long-term benefits of reduced waste, high quality, and increased efficiency often offset these initial costs.
To overcome these challenges, it’s crucial for manufacturers to invest in training and development, ensuring that their workforce is equipped with the necessary skills and knowledge.
Collaboration with design engineers and material scientists can also enhance the product development process, leading to better design solutions and more effective manufacturing practices.
The Future of Micro Component Manufacturing
As industries continue to evolve, the future of micro component manufacturing looks promising.
With advancements in 3D printing, nanotechnology, and smart materials, the precision injection molding field is poised for even greater breakthroughs.
Continuous innovation will likely lead to even smaller, more intricate components that are lighter and more efficient.
These developments will open up new possibilities across various sectors, from healthcare to aerospace, where precision and miniaturization are increasingly critical.
In conclusion, precision injection molding is not just about producing micro components, but about revolutionizing the manufacturing process to meet the needs of modern technology and industrial applications.
Through expertise, innovation, and an eye for detail, manufacturers can harness this powerful technique to achieve remarkable success stories, creating components that are integral to our everyday lives.
資料ダウンロード
QCD調達購買管理クラウド「newji」は、調達購買部門で必要なQCD管理全てを備えた、現場特化型兼クラウド型の今世紀最高の購買管理システムとなります。
ユーザー登録
調達購買業務の効率化だけでなく、システムを導入することで、コスト削減や製品・資材のステータス可視化のほか、属人化していた購買情報の共有化による内部不正防止や統制にも役立ちます。
NEWJI DX
製造業に特化したデジタルトランスフォーメーション(DX)の実現を目指す請負開発型のコンサルティングサービスです。AI、iPaaS、および先端の技術を駆使して、製造プロセスの効率化、業務効率化、チームワーク強化、コスト削減、品質向上を実現します。このサービスは、製造業の課題を深く理解し、それに対する最適なデジタルソリューションを提供することで、企業が持続的な成長とイノベーションを達成できるようサポートします。
オンライン講座
製造業、主に購買・調達部門にお勤めの方々に向けた情報を配信しております。
新任の方やベテランの方、管理職を対象とした幅広いコンテンツをご用意しております。
お問い合わせ
コストダウンが利益に直結する術だと理解していても、なかなか前に進めることができない状況。そんな時は、newjiのコストダウン自動化機能で大きく利益貢献しよう!
(Β版非公開)