- お役立ち記事
- Success Stories in Product Development by Minimizing Weld Lines
Success Stories in Product Development by Minimizing Weld Lines
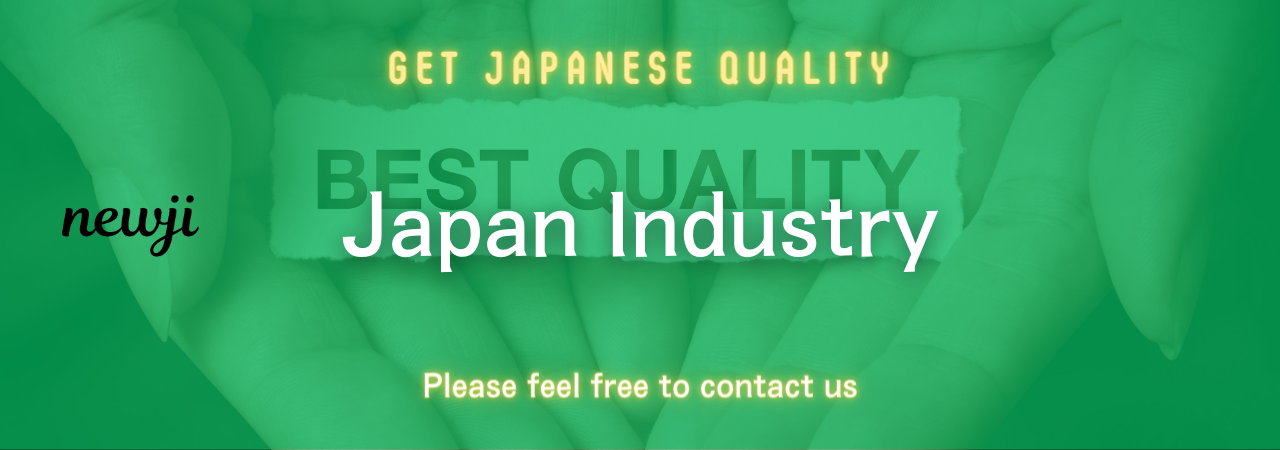
目次
Understanding Weld Lines in Product Development
In the world of product development, the presence of weld lines can present significant challenges.
These lines, which occur during the manufacturing process, can affect the strength and appearance of a product.
Minimizing or eliminating weld lines is crucial for creating high-quality products that meet the demands of both manufacturers and consumers.
Weld lines are formed when two or more flow fronts of molten material meet and solidify during the molding process.
They can be found in products made through injection molding, where plastics or metals are melted and injected into a mold.
Weld lines can result in weak spots in the product, where the material might be more prone to breaking or fracturing.
Understanding how weld lines are formed is a crucial step in addressing their impact.
By studying these lines, engineers can develop strategies to minimize their appearance, thereby enhancing the overall quality of the product.
Strategies to Minimize Weld Lines
Several strategies have been developed to minimize weld lines during the product development process.
Each strategy involves adjustments in the machine settings, material selection, or design improvements.
1. Optimize Injection Molding Parameters
One effective approach is to optimize the parameters of the injection molding process.
This includes factors like the temperature of the material, the injection speed, and the pressure applied during the process.
By finely tuning these variables, manufacturers can reduce the formation of weld lines.
For example, higher temperatures can allow the molten material to flow more smoothly, reducing the chances of weld line formation.
Similarly, optimizing the injection speed can ensure a more uniform flow of material, leading to a more seamless product.
2. Material Selection
Another crucial factor is the selection of materials used in product manufacturing.
Some materials are more prone to weld line formation than others.
By selecting materials with appropriate flow and bonding properties, manufacturers can significantly reduce the occurrence of weld lines.
In recent years, advances in material science have led to the development of specialty materials designed to minimize weld lines.
These materials are engineered to have better flow properties and enhanced bonding capabilities, resulting in fewer and less noticeable weld lines.
3. Design Improvements
Product design plays a vital role in minimizing weld lines.
Engineers can develop designs that encourage more uniform flow of material within the mold.
By strategically placing gates and vents, the points where the material enters the mold, designers can guide the material flow to reduce the formation of weld lines.
Design simulations can also be employed to predict where weld lines might form, allowing designers to adjust their designs accordingly.
This proactive approach enables the creation of products with superior structural integrity and visual appeal.
Success Stories in Minimizing Weld Lines
There are numerous success stories in the field of product development where minimizing weld lines has led to significant improvements in product quality.
Case Study: Automotive Parts Manufacturing
In the automotive industry, weld lines are a common challenge, especially in plastic components.
One leading car manufacturer successfully applied advanced molding techniques and material innovations to reduce weld lines in their bumper production.
By implementing optimized injection parameters and using a specially formulated polymer blend, the company managed to produce bumpers with minimal weld lines, leading to enhanced durability and an improved finish.
This not only boosted customer satisfaction but also reduced the need for costly post-production modifications.
Case Study: Consumer Electronics
In the realm of consumer electronics, weld lines can affect the sleek appearance and tactile feel of products.
A tech giant focused on reducing weld lines in their smartphone casings.
Through a combination of design adjustments and specialized material selection, they achieved a significant reduction in weld line visibility.
This resulted in a more seamless and visually appealing product, which contributed to a stronger market presence.
Case Study: Medical Device Manufacturing
The medical device industry demands high precision and reliability, making it crucial to minimize weld lines.
One medical device company overcame this challenge through the use of advanced computer-aided design (CAD) and simulation tools.
By predicting potential weld line locations during the design phase, they could adjust the mold and process parameters effectively.
This approach led to the production of more robust and reliable medical devices, enhancing patient safety and healthcare outcomes.
The Future of Minimizing Weld Lines
As technology advances, the future of minimizing weld lines in product development looks promising.
Emerging technologies like 3D printing and advanced simulation tools offer new opportunities to tackle the weld line problem from different angles.
3D printing is being increasingly adopted to create complex product designs without the necessity of traditional mold-based processes.
This technology reduces the occurrence of weld lines by allowing the direct fabrication of parts in layers, bypassing the traditional injection molding method.
Furthermore, advancements in simulation and modeling technologies allow engineers to predict and mitigate weld line formation more effectively.
These tools provide valuable insights into the flow of materials and the potential areas of concern, enabling developers to refine designs before production begins.
In conclusion, minimizing weld lines is an essential aspect of producing high-quality products in various industries.
By optimizing manufacturing processes, selecting appropriate materials, and refining product designs, companies can significantly reduce weld lines, resulting in products that meet high standards of quality and durability.
As technology continues to evolve, the ability to address this challenge will improve, leading to even more successful product development stories in the future.
資料ダウンロード
QCD調達購買管理クラウド「newji」は、調達購買部門で必要なQCD管理全てを備えた、現場特化型兼クラウド型の今世紀最高の購買管理システムとなります。
ユーザー登録
調達購買業務の効率化だけでなく、システムを導入することで、コスト削減や製品・資材のステータス可視化のほか、属人化していた購買情報の共有化による内部不正防止や統制にも役立ちます。
NEWJI DX
製造業に特化したデジタルトランスフォーメーション(DX)の実現を目指す請負開発型のコンサルティングサービスです。AI、iPaaS、および先端の技術を駆使して、製造プロセスの効率化、業務効率化、チームワーク強化、コスト削減、品質向上を実現します。このサービスは、製造業の課題を深く理解し、それに対する最適なデジタルソリューションを提供することで、企業が持続的な成長とイノベーションを達成できるようサポートします。
オンライン講座
製造業、主に購買・調達部門にお勤めの方々に向けた情報を配信しております。
新任の方やベテランの方、管理職を対象とした幅広いコンテンツをご用意しております。
お問い合わせ
コストダウンが利益に直結する術だと理解していても、なかなか前に進めることができない状況。そんな時は、newjiのコストダウン自動化機能で大きく利益貢献しよう!
(Β版非公開)