- お役立ち記事
- Success stories of manufacturing industry DX to realize wage increases
月間77,185名の
製造業ご担当者様が閲覧しています*
*2025年2月28日現在のGoogle Analyticsのデータより
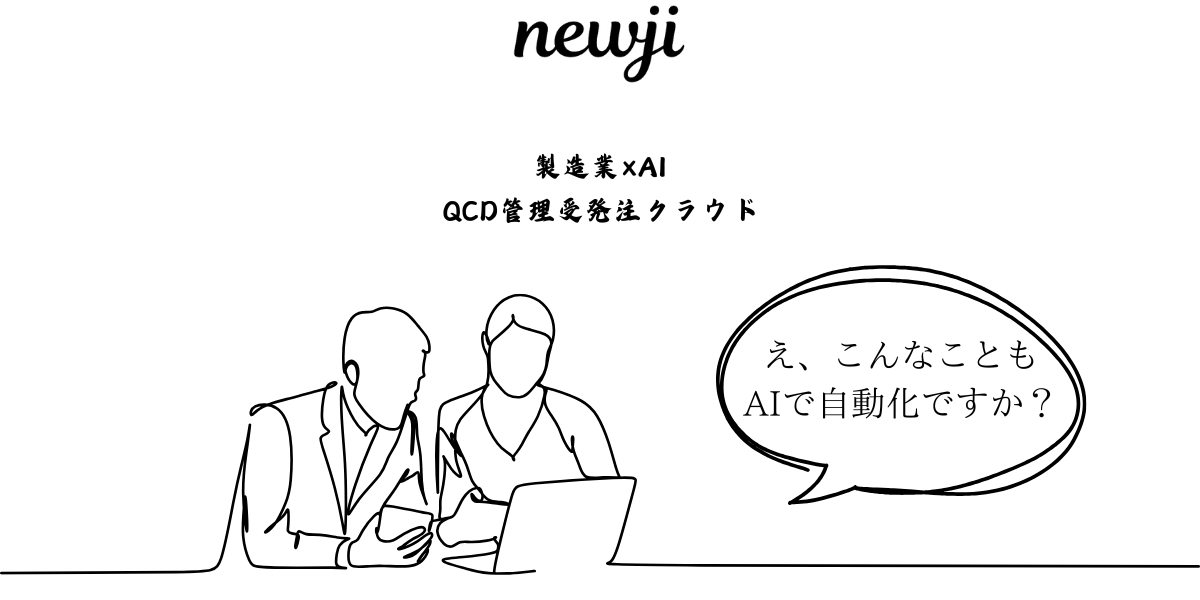
Success stories of manufacturing industry DX to realize wage increases
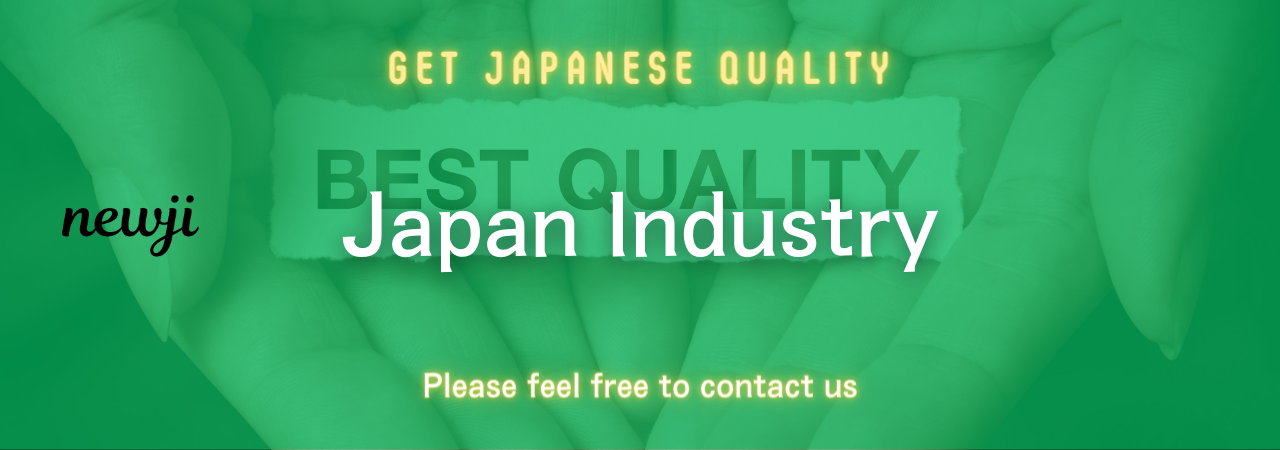
目次
Introduction to Manufacturing Industry DX
The manufacturing industry is continuously evolving, often driven by technological advancements and changing economic landscapes.
Digital transformation, commonly known as DX, is one of the key strategies being embraced by this sector to drive significant improvements in productivity, efficiency, and profitability.
One of the most compelling outcomes of DX in the manufacturing industry is the potential for wage increases, resulting from improved business performance and enhanced operations.
This article explores some inspiring success stories of companies that have effectively integrated DX to realize worker wage increases.
Understanding the Benefits of Digital Transformation
Before delving into individual success stories, it’s important to understand what digital transformation entails and how it can benefit the manufacturing industry.
DX involves the integration of digital technologies into all aspects of a business, significantly altering how a business operates and delivers value to customers.
For manufacturers, this can mean adopting new tools like Internet of Things (IoT) devices, predictive analytics, cloud computing, or robotics to optimize manufacturing processes.
This transformation can lead to various benefits such as increased efficiency, improved product quality, reduced downtime, enhanced supply chain management, and ultimately, cost savings.
As businesses become more profitable due to these efficiencies, they are better positioned to pass on financial benefits to their employees through wage increases.
Success Story 1: Company A’s Journey to Wage Increase
Company A, a leading automotive parts manufacturer, embarked on its digital transformation journey five years ago.
Facing intense global competition and fluctuating market demands, the company knew that it needed to innovate to stay ahead.
They began by implementing IoT solutions on their production line which enabled real-time monitoring and data collection.
The adoption of IoT devices drastically reduced machine downtime and improved the precision in production scheduling, leading to a 30% increase in production efficiency.
With these impressive gains, Company A reinvested part of the increased profits into their workforce, providing a notable salary increase to its employees.
This strategy not only improved the quality of life for their staff but also promoted a more engaged and motivated workforce leading to further productivity gains.
A Healthier Work Environment
In tandem with wage increases, Company A leveraged technology to promote a healthier work environment.
They used data analytics to optimize shift patterns, ensuring employees received adequate rest.
This approach reduced fatigue and errors, leading to better work conditions and happier employees.
Success Story 2: Company B Harnessing Automation
Company B, a consumer electronics manufacturer, faced challenges with labor costs and supply chain inefficiencies.
The company implemented an advanced automation system, including robotics and AI-driven production lines, to streamline its assembly processes.
The automation reduced labor-intensive tasks allowing employees to focus on higher-value work.
As a result, productivity increased by 25%, and operational costs declined significantly.
Recognizing these savings, Company B prioritized boosting employee wages and enhancing benefits such as health insurance and retirement plans.
Skills Development and Retraining
Company B did not just invest in technology but also in their employees’ futures.
To align with their digital shift, the company initiated robust training programs to upskill their staff, equipping them with the necessary competencies to work alongside advanced technologies.
This investment in human capital not only resulted in wage hikes but also fostered loyalty and reduced staff turnover.
Success Story 3: Company C’s Data-Driven Approach
Company C, specializing in heavy machinery, turned to data analytics to improve decision-making processes and drive business success.
The company developed an integrated data management system that provided comprehensive insights into production, sales, and customer feedback.
By harnessing these insights, Company C enhanced its product offerings and streamlined supply chain operations, cutting costs and boosting revenues.
This newfound efficiency allowed them to initiate a performance-based pay increase strategy, aligning compensation directly with productivity improvements.
Fostering a Culture of Innovation
Company C encouraged a culture of innovation by involving employees in digital transformation initiatives.
Workshops and hackathons were introduced to foster creative problem solving and continuous improvement, empowering employees to take ownership of innovation.
As a result, employees felt more valued and engaged, knowing their contributions were directly linked to the company’s success and their personal growth.
Conclusion: The Future of DX in Manufacturing
The success stories of Companies A, B, and C illustrate the transformative potential of digital technologies in the manufacturing industry.
By leveraging DX, these companies not only enhanced their operational efficiency and competitiveness but also reinvested in their workforce through wage increases, thereby nurturing a more motivated and skilled workforce.
As the manufacturing industry continues to advance, other companies can draw inspiration from these stories to embark on their digital transformation journeys.
By doing so, not only can they achieve operational success, but they can also uplift their employees’ livelihoods, fostering a more productive and sustainable industry.
With digital transformation, the manufacturing sector is set to witness more success stories that link technology adoption with tangible benefits such as wage increases and improved employee satisfaction.
The future holds immense promise for those willing to innovate and adapt, reaping both financial rewards and creating a positive impact on the workforce.
資料ダウンロード
QCD管理受発注クラウド「newji」は、受発注部門で必要なQCD管理全てを備えた、現場特化型兼クラウド型の今世紀最高の受発注管理システムとなります。
ユーザー登録
受発注業務の効率化だけでなく、システムを導入することで、コスト削減や製品・資材のステータス可視化のほか、属人化していた受発注情報の共有化による内部不正防止や統制にも役立ちます。
NEWJI DX
製造業に特化したデジタルトランスフォーメーション(DX)の実現を目指す請負開発型のコンサルティングサービスです。AI、iPaaS、および先端の技術を駆使して、製造プロセスの効率化、業務効率化、チームワーク強化、コスト削減、品質向上を実現します。このサービスは、製造業の課題を深く理解し、それに対する最適なデジタルソリューションを提供することで、企業が持続的な成長とイノベーションを達成できるようサポートします。
製造業ニュース解説
製造業、主に購買・調達部門にお勤めの方々に向けた情報を配信しております。
新任の方やベテランの方、管理職を対象とした幅広いコンテンツをご用意しております。
お問い合わせ
コストダウンが利益に直結する術だと理解していても、なかなか前に進めることができない状況。そんな時は、newjiのコストダウン自動化機能で大きく利益貢献しよう!
(β版非公開)