- お役立ち記事
- Success Stories of Manufacturing Using 3D Printers and OEM
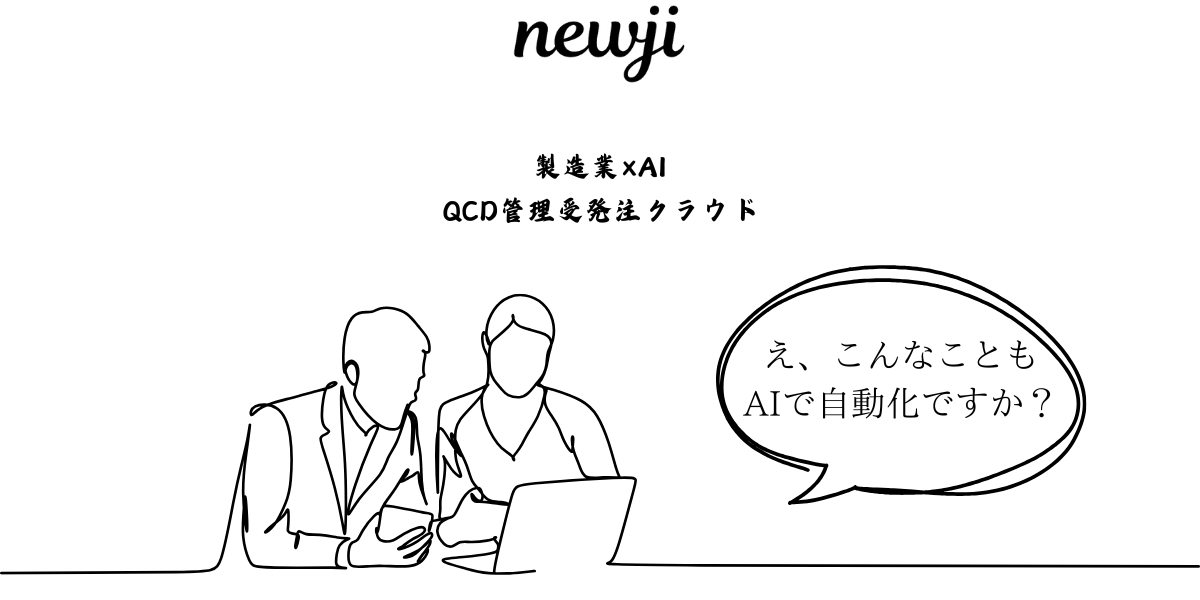
Success Stories of Manufacturing Using 3D Printers and OEM
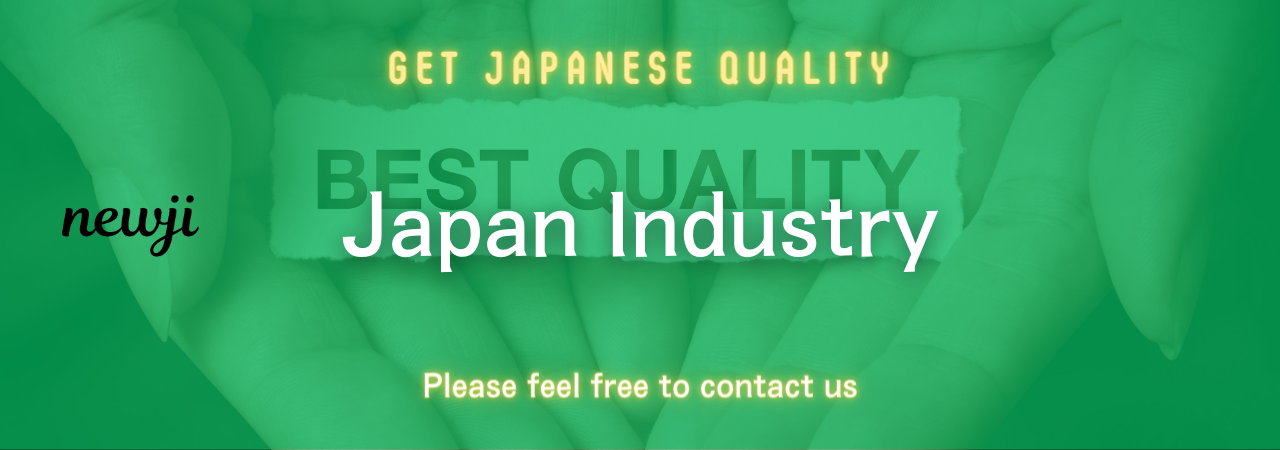
In today’s rapidly advancing technological world, 3D printing is revolutionizing the manufacturing industry.
The term Original Equipment Manufacturer (OEM) along with 3D printing has opened new doors for companies aiming to innovate.
This combination allows for streamlined manufacturing processes and custom solutions.
Let’s delve deeper into the success stories of manufacturing using 3D printers and OEM.
目次
Transforming Production with 3D Printing
Whether it’s creating prototypes, replacing damaged parts, or devising new products, 3D printing provides a flexible and efficient approach.
A prominent example is General Electric (GE).
GE has embraced 3D printing in the production of jet engine parts.
By using 3D printers, GE can develop parts that are both lighter and stronger than their traditionally manufactured counterparts.
This not only improves engine performance but also significantly reduces fuel consumption.
Another success story is the automotive industry.
Ford Motor Company has adopted 3D printing to produce tools, fixtures, and prototype parts.
By doing this, Ford slashes prototyping costs, reducing their expense by millions of dollars annually.
It also speeds up the design process, allowing Ford to get new models to market faster than ever.
OEM Partnerships Leading the Way
OEM partnerships are vital in bringing innovative solutions to market.
Through collaboration, companies can leverage each other’s strengths to produce top-quality products.
For instance, BMW has partnered with HP to incorporate additive manufacturing in their production line.
HP’s Multi Jet Fusion technology allows BMW to produce high-quality, custom automotive parts.
This partnership means BMW can now produce parts that are more complex, yet cost-effective, optimizing both the design and manufacturing process.
Similarly, in the healthcare sector, Stryker, a leading medical device company, has collaborated with OEMs to utilize 3D printing technologies.
They manufacture custom orthopedic implants tailored to patients’ needs.
This precise customizability enhances patient recovery times and reduces complications after surgery.
Customization: An Attractive Feature
3D printing and OEM partnerships have allowed for heightened levels of customization in manufacturing.
Take Adidas, for instance.
They developed a line of custom sneakers called Futurecraft 4D, integrating 3D-printed midsoles.
These midsoles are tailored to the individual buyer’s foot shape and particular needs.
By utilizing OEM technologies, Adidas offers consumers a unique product, positioning themselves as leaders in customization.
The aviation industry also benefits immensely from customization via 3D printing.
Companies like Airbus use 3D printing to manufacture custom aircraft parts.
This allows them to design more efficient components, reducing overall aircraft weight and improving fuel efficiency.
Such advancements are crucial in maintaining competitive advantage in a fast-paced industry.
Cost Efficiency and Waste Reduction
One significant advantage of 3D printing is the reduction in production costs and waste.
For example, in traditional manufacturing processes, excess materials are often discarded, leading to wastage.
However, 3D printing builds products layer by layer, using only the necessary amount of material.
Less waste translates into cost savings.
Local Motors, a vehicle company, showcases this in their manufacturing process.
They produce 3D-printed electric cars, reducing material waste and production times significantly.
By leveraging the efficiencies of 3D printing, they have positioned themselves as pioneers in eco-friendly vehicle manufacturing.
Similarly, the fashion industry is looking to 3D printing for sustainable solutions.
Companies like Ministry of Supply are producing 3D-knitted apparel, reducing fabric waste that typically occurs during traditional manufacturing.
This environmentally friendly approach attracts eco-conscious consumers and aligns with global sustainability efforts.
Streamlined Supply Chains
3D printing can significantly streamline the supply chain.
Gone are the days when companies need to maintain large inventories.
Companies can instead produce parts on demand.
DHL, a global logistics leader, has embraced 3D printing for just this purpose.
They use the technology to produce spare parts as needed, eliminating the need for large stockpiles, reducing storage costs, and enhancing efficiency.
Equally, Nike has utilized 3D printing to streamline their supply chain.
By printing prototypes and small batches in-house, they cut down on lead time and logistics costs.
This agility allows Nike to respond to market trends swiftly and efficiently.
Made for Medical Marvels
The medical field is reaping significant benefits from 3D printing innovations.
One particularly inspiring success story involves the creation of patient-specific prosthetics.
e-NABLE, a volunteer-based organization, provides 3D-printed hands and arms to children and adults in need.
These custom prosthetics not only improve the quality of life but are also produced at a fraction of the cost of traditional prosthetic devices.
Moreover, dental professionals have started using 3D printing to produce custom-fit dental implants and aligners.
Smile Direct Club, for example, uses 3D printed dental aligners to offer affordable orthodontic solutions.
This approach provides patients with custom-fit aligners made faster and cheaper than traditional methods.
Educational Advantages
3D printing is also transforming the education sector.
Many educational institutions are integrating 3D printing into their curriculum.
This hands-on experience fosters students’ creativity, enabling them to bring their designs to life quickly.
MIT’s MakerWorks, for instance, is equipped with multiple 3D printers to help students in prototyping and developing innovative projects.
Additionally, the availability of 3D printing technology in schools prepares students for future careers in various fields, including engineering, healthcare, and design.
The Future of Manufacturing
As we look to the future, it’s evident that 3D printing and OEM partnerships will continue to play a crucial role in manufacturing.
These technologies not only facilitate innovation but also promote sustainability and efficiency.
Industries from aerospace to healthcare are already recognizing and reaping the benefits.
The ability to produce customized, high-quality products in a cost-effective manner is transforming how we think about manufacturing.
With continuous advancements, the potential applications of 3D printing will only expand, heralding a new era of innovation and possibility in the industrial world.
The success stories of today are just the beginning, and the future holds endless opportunities for those willing to embrace this transformative technology.
資料ダウンロード
QCD調達購買管理クラウド「newji」は、調達購買部門で必要なQCD管理全てを備えた、現場特化型兼クラウド型の今世紀最高の購買管理システムとなります。
ユーザー登録
調達購買業務の効率化だけでなく、システムを導入することで、コスト削減や製品・資材のステータス可視化のほか、属人化していた購買情報の共有化による内部不正防止や統制にも役立ちます。
NEWJI DX
製造業に特化したデジタルトランスフォーメーション(DX)の実現を目指す請負開発型のコンサルティングサービスです。AI、iPaaS、および先端の技術を駆使して、製造プロセスの効率化、業務効率化、チームワーク強化、コスト削減、品質向上を実現します。このサービスは、製造業の課題を深く理解し、それに対する最適なデジタルソリューションを提供することで、企業が持続的な成長とイノベーションを達成できるようサポートします。
オンライン講座
製造業、主に購買・調達部門にお勤めの方々に向けた情報を配信しております。
新任の方やベテランの方、管理職を対象とした幅広いコンテンツをご用意しております。
お問い合わせ
コストダウンが利益に直結する術だと理解していても、なかなか前に進めることができない状況。そんな時は、newjiのコストダウン自動化機能で大きく利益貢献しよう!
(Β版非公開)