- お役立ち記事
- Success stories of multi-material manufacturing using 3D printing that design leaders in the precision machinery industry need to know
月間76,176名の
製造業ご担当者様が閲覧しています*
*2025年3月31日現在のGoogle Analyticsのデータより
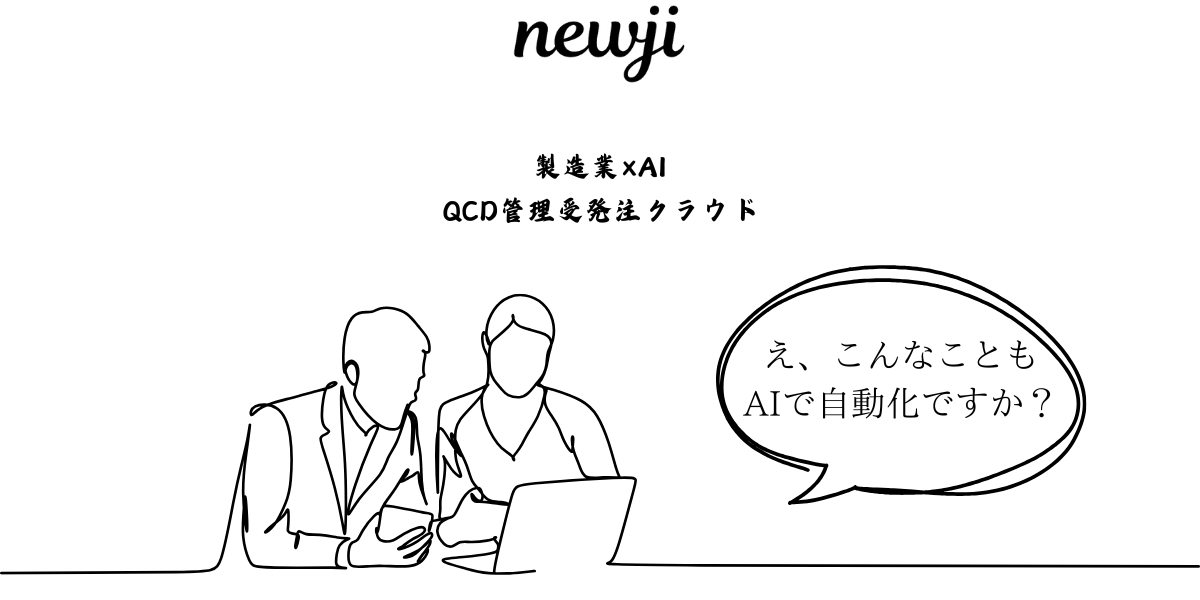
Success stories of multi-material manufacturing using 3D printing that design leaders in the precision machinery industry need to know
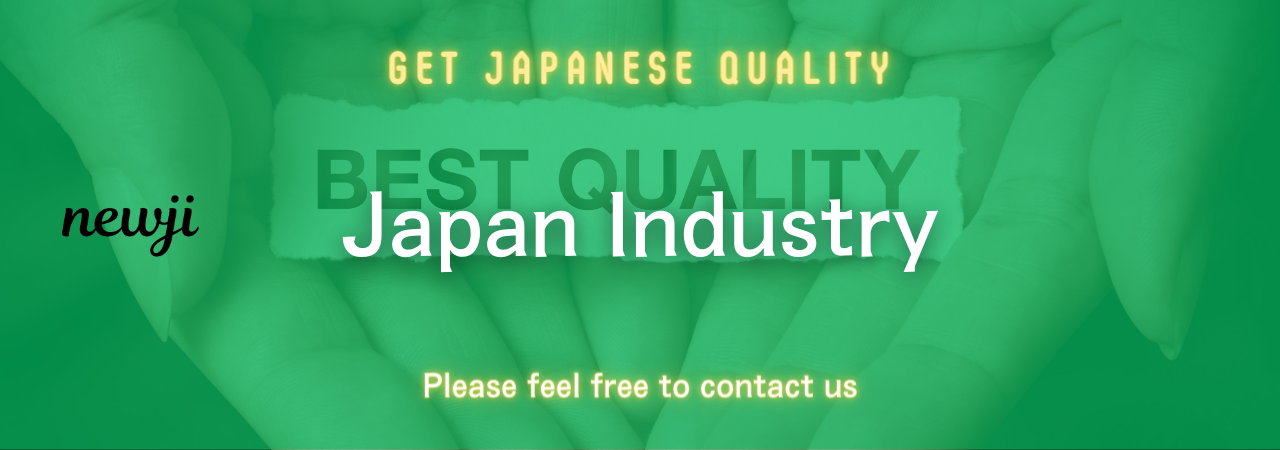
目次
Introduction to Multi-Material Manufacturing
The evolution of 3D printing has unlocked new horizons for innovation in various industries, particularly in precision machinery.
This remarkable technology has taken a step further with multi-material manufacturing, where different materials can be combined in a single 3D printed object.
This advancement presents exciting possibilities to design leaders, allowing them to explore novel ways of integrating diverse material properties into their products.
In multi-material 3D printing, objects are created layer by layer, incorporating multiple materials with varying properties such as stiffness, elasticity, or thermal conductivity.
This facilitates the creation of objects with enhanced functionality and performance.
It’s a game-changer for design leaders, offering the potential to revolutionize product designs and production processes in the precision machinery industry.
Key Benefits of Multi-Material 3D Printing
Multi-material 3D printing is not just about adding aesthetic value; it profoundly impacts functional capabilities.
Here are some essential benefits:
1. Enhanced Product Functionality
By utilizing different materials within a single print, design leaders can create products with enhanced functionality.
For instance, a single component can have rigid exteriors for protection and a soft, flexible interior for shock absorption.
This application opens innovative options for creating more efficient and versatile precision machinery parts.
2. Reduction in Assembly Time
The traditional manufacturing process often involves multiple separate components being manufactured and assembled.
Multi-material 3D printing allows for these parts to be produced as a single unit.
This minimizes assembly time, reduces potential points of failure, and streamlines the production process, making it more efficient and cost-effective.
3. Improved Material Utilization
The traditional approach often results in significant material waste due to cutting and subtractive methods.
With multi-material 3D printing, material is added only where necessary, minimizing waste and enhancing material utilization.
This technique is both environmentally friendly and cost-efficient, providing a sustainable alternative for the precision machinery industry.
4. Customization and Complex Geometries
3D printing inherently supports complex designs and customization because its layer-by-layer method does not have the same geometric limitations as traditional methods.
Multi-material processes extend this advantage further by enabling intricate designs that incorporate the strengths of different materials.
Products can then be tailored to specific needs, fulfilling niche requirements that were previously unattainable.
Success Stories in Precision Machinery
Leading companies in precision machinery have already started integrating multi-material 3D printing into their operations, achieving remarkable results.
1. Advanced Robotics Components
A robotics company aimed to develop multi-functional robotic arms with nuanced capabilities by utilizing multi-material 3D printing.
The firm successfully integrated rigid structures with embedded conductive pathways and flexible joints in a single print.
This breakthrough drastically improved the arm’s efficiency and longevity while reducing the weight.
As a result, the robotic arms needed less energy for operation, highlighting the potential of multi-material manufacturing in robotics.
2. Aerospace Innovations
In the aerospace sector, precision and weight are paramount.
A well-known aerospace company utilized multi-material 3D printing to fabricate parts with varying densities, ensuring strength in some areas and lightness in others.
This was particularly successful in manufacturing lightweight yet strong brackets used in aircraft cabins, illustrating the massive potential for multi-material 3D printing in reducing fuel consumption and increasing payload efficiency.
3. Medical Equipment Enhancements
The medical equipment industry has embraced multi-material 3D printing, particularly for creating custom prosthetics and implants.
A company designing custom-fit prosthetic limbs leveraged multi-material capabilities to print prosthetics with a hard outer shell for durability and soft, patient-specific interiors for comfort.
This innovation has allowed patients to achieve superior comfort and mobility, exemplifying the transformative impact of multi-material 3D printing in healthcare.
Overcoming Challenges in Multi-Material 3D Printing
Despite its potential, multi-material 3D printing faces several challenges that must be addressed.
1. Material Compatibility
Not all materials are compatible with each other or with the 3D printing process.
Material compatibility affects the strength, durability, and functionality of the finished product.
Design leaders must carefully select materials that not only meet the desired technical specifications but also work well together during the printing process.
2. Process Complexity
Multi-material 3D printing increases the complexity of the printing process.
It requires meticulous software and hardware management to synchronize the deposition of different materials accurately.
Designers and engineers must possess comprehensive knowledge and skills to handle sophisticated 3D printers, which can require a steep learning curve.
3. Cost Implications
While 3D printing can reduce material waste and shorten production times, the initial investment in multi-material 3D printers and training can be substantial.
Cost-benefit analyses and strategic planning are essential for ensuring that the implementation of multi-material 3D printing is financially viable.
Conclusion
Multi-material 3D printing represents a frontier of innovation that design leaders in the precision machinery industry must explore.
The technology is pushing boundaries and is poised to transform product design and manufacturing processes.
Success stories in robotics, aerospace, and medical equipment illustrate the potential for increased functionality, efficiency, and customization brought about by combining various materials in single prints.
As companies navigate the challenges of material compatibility, process complexity, and cost, the path forward will involve strategic planning and continuous learning.
Embracing this technology could lead to groundbreaking advancements, setting new standards in the precision machinery industry and beyond.
資料ダウンロード
QCD管理受発注クラウド「newji」は、受発注部門で必要なQCD管理全てを備えた、現場特化型兼クラウド型の今世紀最高の受発注管理システムとなります。
ユーザー登録
受発注業務の効率化だけでなく、システムを導入することで、コスト削減や製品・資材のステータス可視化のほか、属人化していた受発注情報の共有化による内部不正防止や統制にも役立ちます。
NEWJI DX
製造業に特化したデジタルトランスフォーメーション(DX)の実現を目指す請負開発型のコンサルティングサービスです。AI、iPaaS、および先端の技術を駆使して、製造プロセスの効率化、業務効率化、チームワーク強化、コスト削減、品質向上を実現します。このサービスは、製造業の課題を深く理解し、それに対する最適なデジタルソリューションを提供することで、企業が持続的な成長とイノベーションを達成できるようサポートします。
製造業ニュース解説
製造業、主に購買・調達部門にお勤めの方々に向けた情報を配信しております。
新任の方やベテランの方、管理職を対象とした幅広いコンテンツをご用意しております。
お問い合わせ
コストダウンが利益に直結する術だと理解していても、なかなか前に進めることができない状況。そんな時は、newjiのコストダウン自動化機能で大きく利益貢献しよう!
(β版非公開)