- お役立ち記事
- Success Stories of SMEs Improving Productivity with Hot Plate Welding
Success Stories of SMEs Improving Productivity with Hot Plate Welding
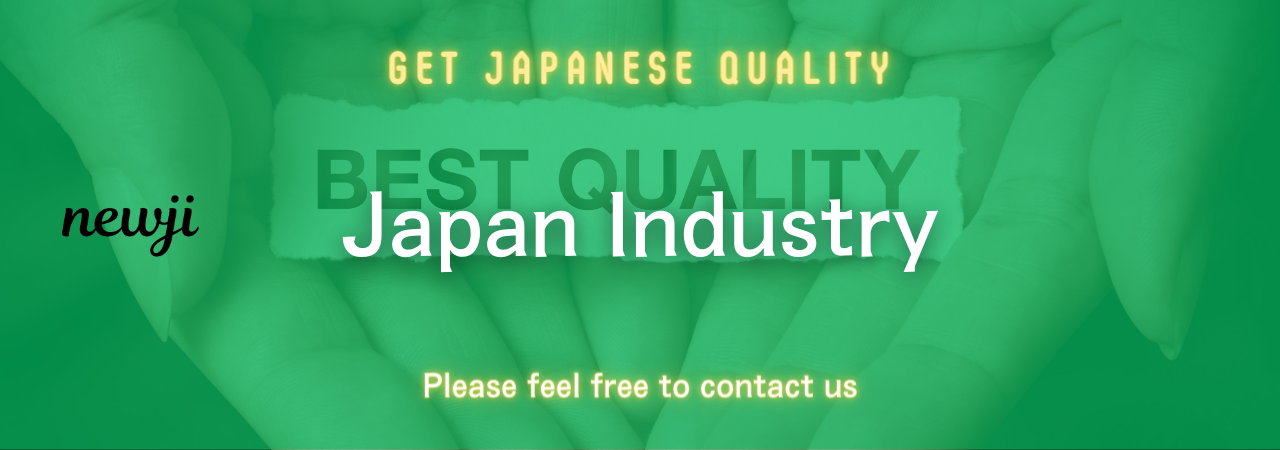
Small and medium-sized enterprises (SMEs) face numerous challenges in today’s competitive market.
One area that significantly impacts their success is productivity.
Improving productivity can determine whether an SME thrives or struggles to stay afloat.
One innovative method that has shown promise for enhancing productivity is hot plate welding.
This article explores various success stories of SMEs leveraging hot plate welding to achieve remarkable improvements in their operational efficiency.
目次
What is Hot Plate Welding?
Hot plate welding, also known as mirror welding, is a process that joins thermoplastic materials using heat.
A hot plate, typically made from metal, is heated to a specific temperature and used to melt the surfaces of the parts to be joined.
Once the surfaces are sufficiently molten, the hot plate is removed and the parts are pressed together, allowing them to fuse as they cool.
This method is particularly effective for bonding large, complex, or irregular-shaped parts.
Advantages of Hot Plate Welding
Hot plate welding offers numerous advantages over traditional welding techniques.
It provides strong, durable bonds and is suitable for various materials, including polyethylene, polypropylene, and PVC.
The process is relatively simple, making it easy to integrate into existing manufacturing lines.
Additionally, hot plate welding produces clean, aesthetically pleasing joints without the need for additional adhesives or fasteners.
Case Study: Automotive Components Manufacturer
One notable success story comes from an automotive components manufacturer that specializes in producing various plastic parts.
The company was looking for a reliable way to join complex parts efficiently.
After trialing different methods, they decided to implement hot plate welding due to its precision and effectiveness.
The results were impressive.
The company reported a 25% increase in production efficiency and a significant reduction in defective parts.
The robust joints created by hot plate welding met the stringent quality standards required in the automotive industry.
This improvement not only boosted productivity but also enhanced customer satisfaction and loyalty.
Streamlined Production Process
By incorporating hot plate welding into their production line, the manufacturer was able to streamline their process.
The automated system minimized human error and ensured consistent quality.
Employees could focus on other critical tasks, further enhancing overall productivity.
Case Study: Medical Device Manufacturer
Another SME that benefited from hot plate welding is a medical device manufacturer.
The company produces a range of plastic components used in medical devices, including housings and enclosures.
Given the critical nature of their products, the manufacturer required a welding method that provided strong, reliable bonds.
Hot plate welding proved to be the ideal solution.
The company experienced a 30% decrease in production time and a 20% reduction in material waste.
The consistent, high-quality welds ensured their devices met stringent regulatory standards, and the efficiency gains allowed them to meet increasing demand without compromising quality.
Enhanced Quality Control
The medical device manufacturer was able to enhance their quality control processes significantly.
The precise, uniform welds produced by hot plate welding made it easier to meet rigorous industry standards.
This, in turn, elevated the company’s reputation in the market, leading to more contracts and business opportunities.
Case Study: Consumer Goods Manufacturer
A consumer goods manufacturer specializing in household plastic products also saw significant benefits from adopting hot plate welding.
This company was struggling with slow production rates and high defect rates using traditional welding methods.
Upon switching to hot plate welding, the company noticed a 40% improvement in production speed and a 15% decline in defective products.
This increase in efficiency allowed the manufacturer to expand their product line and take on larger orders, driving business growth.
Investment in Innovation
By investing in hot plate welding technology, the consumer goods manufacturer positioned themselves as an innovator in their industry.
This not only improved their operational efficiency but also enhanced their brand image.
Customers recognized the superior quality of their products, resulting in higher sales and market share.
Case Study: Agricultural Equipment Manufacturer
An agricultural equipment manufacturer provides another compelling example of hot plate welding’s impact on SME productivity.
This company produces durable plastic components used in farming machinery.
High-strength bonds were essential to ensure the reliability and longevity of their products.
With hot plate welding, the manufacturer achieved a 35% increase in production capacity and a 25% reduction in labor costs.
The robust joints created by this method were able to withstand the harsh conditions agricultural machinery often faces, ensuring long-term product reliability.
Reduction in Downtime
Implementing hot plate welding also led to a significant reduction in production downtime.
The automated welding process was faster and more reliable, minimizing the frequency of breakdowns and repairs.
This enabled the company to maintain a steady production flow, fulfilling orders promptly and boosting customer satisfaction.
Conclusion
Hot plate welding has proven to be a valuable asset for SMEs looking to improve productivity and quality in their manufacturing processes.
The success stories of various SMEs across different industries demonstrate the versatility and effectiveness of this welding method.
By reducing production costs, enhancing product quality, and increasing production speed, hot plate welding helps SMEs stay competitive and grow their business.
資料ダウンロード
QCD調達購買管理クラウド「newji」は、調達購買部門で必要なQCD管理全てを備えた、現場特化型兼クラウド型の今世紀最高の購買管理システムとなります。
ユーザー登録
調達購買業務の効率化だけでなく、システムを導入することで、コスト削減や製品・資材のステータス可視化のほか、属人化していた購買情報の共有化による内部不正防止や統制にも役立ちます。
NEWJI DX
製造業に特化したデジタルトランスフォーメーション(DX)の実現を目指す請負開発型のコンサルティングサービスです。AI、iPaaS、および先端の技術を駆使して、製造プロセスの効率化、業務効率化、チームワーク強化、コスト削減、品質向上を実現します。このサービスは、製造業の課題を深く理解し、それに対する最適なデジタルソリューションを提供することで、企業が持続的な成長とイノベーションを達成できるようサポートします。
オンライン講座
製造業、主に購買・調達部門にお勤めの方々に向けた情報を配信しております。
新任の方やベテランの方、管理職を対象とした幅広いコンテンツをご用意しております。
お問い合わせ
コストダウンが利益に直結する術だと理解していても、なかなか前に進めることができない状況。そんな時は、newjiのコストダウン自動化機能で大きく利益貢献しよう!
(Β版非公開)