- お役立ち記事
- Success Stories of Worksite Efficiency Improvement Through Work Improvement
Success Stories of Worksite Efficiency Improvement Through Work Improvement
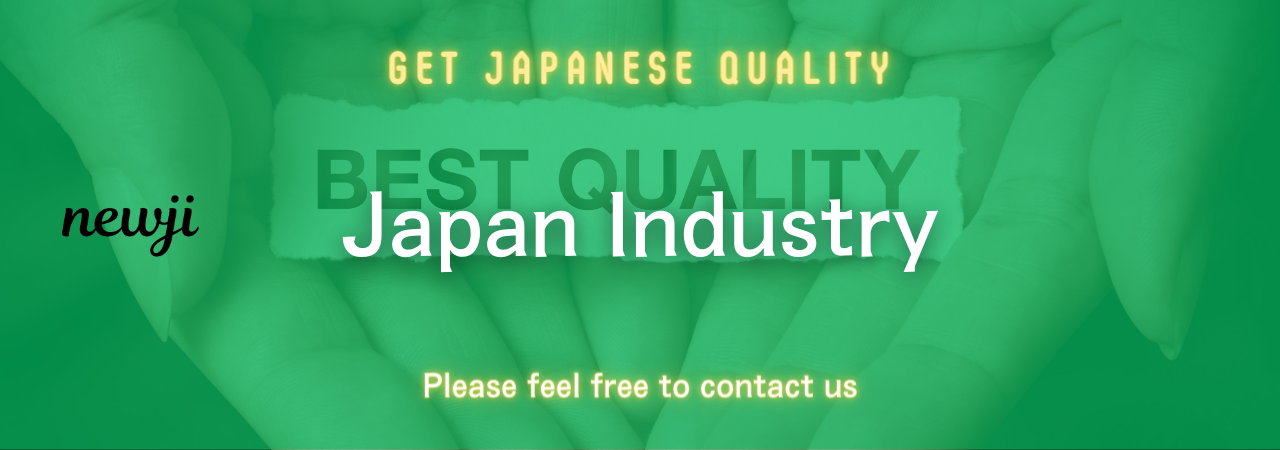
目次
Understanding Worksite Efficiency
Worksite efficiency is crucial for any organization aiming to achieve its goals promptly and cost-effectively.
When a worksite is efficient, less time and resources are wasted, leading to increased productivity and profitability.
Enhancing worksite efficiency involves optimizing workflows, cutting down unnecessary steps in processes, and ensuring that resources are used effectively.
In this post, we will explore some inspiring success stories of how various organizations have improved their worksite efficiency through strategic work improvement initiatives.
By examining these cases, we hope to provide valuable insights and actionable tips that can help you boost efficiency in your own workplace.
The Power of Communication and Collaboration
One of the key elements in improving worksite efficiency is enhancing communication and collaboration among team members.
A construction company based in Texas revolutionized its workflow by introducing regular team meetings and adopting collaboration tools.
Prior to these changes, miscommunication often led to delays and costly errors.
By implementing a structured communication process and using project management software, the company significantly reduced errors and improved project timelines.
Team members could easily share updates, track progress, and quickly address any issues that arose.
This example highlights how effective communication and collaboration can enhance worksite efficiency and lead to successful project completion.
Case Study: The Manufacturing Marvel
A mid-sized manufacturing company in Ohio faced challenges with production delays and high operational costs.
To address these issues, the company re-evaluated its production processes and identified bottlenecks that were slowing down operations.
Through a series of work improvement techniques, they managed to overhaul their efficiency.
The company integrated lean manufacturing principles, which focus on minimizing waste without compromising quality.
They reorganized the shop floor layout to ensure smoother workflow, introduced just-in-time inventory systems to reduce excess stock, and provided continuous training to employees on best practices in production.
As a result, the company saw a 30% increase in production speed and a significant reduction in waste and costs.
This case illustrates the impact of lean principles and continuous employee training in transforming worksite efficiency.
Leveraging Technology for Worksite Efficiency
In today’s digital age, technology plays a vital role in enhancing worksite efficiency.
A software development firm in California offers a quintessential example of this.
Facing problems with project tracking and deadline management, the company turned to advanced project management tools for solutions.
By adopting software like JIRA and Trello, the firm streamlined task allocation, progress tracking, and deadline management.
Teams were now able to prioritize tasks more effectively, communicate more seamlessly, and identify potential project risks well in advance.
This technological upgrade resulted in a 20% increase in project delivery speed and a remarkable reduction in project delays.
Case Study: The Retail Reinventor
A retail chain in New York was combating high employee turnover and long customer checkout times, both of which were affecting overall efficiency.
They decided to implement a robust employee training program coupled with state-of-the-art POS (Point of Sale) systems.
The training program focused on improving employee engagement and providing comprehensive knowledge about their roles.
The new POS systems streamlined the checkout process, making it faster and reducing errors.
As a result, customer satisfaction improved significantly, employee turnover dropped by 15%, and the checkout process became 25% more efficient.
This case study underscores how targeted employee training and modern technology can propel worksite efficiency.
Implementing Process Improvements
Process improvement is a strategic approach to enhancing worksite efficiency.
A logistics company in Illinois made significant strides in efficiency by focusing on optimizing their delivery routes and warehousing processes.
After conducting a detailed analysis of their delivery patterns and warehouse operations, they identified several inefficiencies such as suboptimal routing and poor layout.
By implementing route optimization software and reorganizing the warehouse layout, the company achieved remarkable improvements.
These changes led to a 40% reduction in delivery times and a significant decrease in fuel consumption.
Additionally, the optimized warehouse layout improved inventory management, resulting in fewer errors and quicker order fulfillment.
Case Study: The Healthcare Hero
A hospital in Florida faced challenges with patient flow and resource allocation.
To tackle these issues, the hospital introduced a comprehensive work improvement plan that included process mapping and lean methodologies.
Process mapping helped the hospital identify redundant steps in patient admission and discharge processes.
By eliminating these redundancies and streamlining workflows, the hospital reduced patient wait times and improved overall patient satisfaction.
Further, lean methodologies ensured that resources were allocated more efficiently, reducing waste and improving the quality of care.
This holistic approach led to a 15% increase in patient throughput and a significant improvement in operational efficiency.
Fostering a Culture of Continuous Improvement
Ultimately, worksite efficiency improvements are most sustainable when they are part of a broader culture of continuous improvement.
Companies that encourage employees to identify inefficiencies and propose solutions typically see better long-term results.
A global tech firm in Seattle exemplified this approach by creating an Innovation Lab where employees could experiment with new ideas and improve their workflows.
Employees were encouraged to submit ideas for improving efficiency, which were then tested and implemented if successful.
This culture of continuous improvement not only enhanced worksite efficiency but also boosted employee morale and engagement.
The results? A steady stream of innovative solutions that saved the company time and resources, leading to a 25% increase in operational efficiency over three years.
Conclusion
These success stories illustrate that improving worksite efficiency is not a one-size-fits-all approach.
Different work environments require different strategies, whether it’s leveraging technology, enhancing communication, adopting lean principles, or fostering a culture of continuous improvement.
By learning from these examples and applying the appropriate strategies to your own operations, you can enhance worksite efficiency, paving the way for success and growth in your organization.
資料ダウンロード
QCD調達購買管理クラウド「newji」は、調達購買部門で必要なQCD管理全てを備えた、現場特化型兼クラウド型の今世紀最高の購買管理システムとなります。
ユーザー登録
調達購買業務の効率化だけでなく、システムを導入することで、コスト削減や製品・資材のステータス可視化のほか、属人化していた購買情報の共有化による内部不正防止や統制にも役立ちます。
NEWJI DX
製造業に特化したデジタルトランスフォーメーション(DX)の実現を目指す請負開発型のコンサルティングサービスです。AI、iPaaS、および先端の技術を駆使して、製造プロセスの効率化、業務効率化、チームワーク強化、コスト削減、品質向上を実現します。このサービスは、製造業の課題を深く理解し、それに対する最適なデジタルソリューションを提供することで、企業が持続的な成長とイノベーションを達成できるようサポートします。
オンライン講座
製造業、主に購買・調達部門にお勤めの方々に向けた情報を配信しております。
新任の方やベテランの方、管理職を対象とした幅広いコンテンツをご用意しております。
お問い合わせ
コストダウンが利益に直結する術だと理解していても、なかなか前に進めることができない状況。そんな時は、newjiのコストダウン自動化機能で大きく利益貢献しよう!
(Β版非公開)