- お役立ち記事
- Successful Case Study in Epoxy Resin OEM: Improving Product Durability and Performance with High-Quality Materials
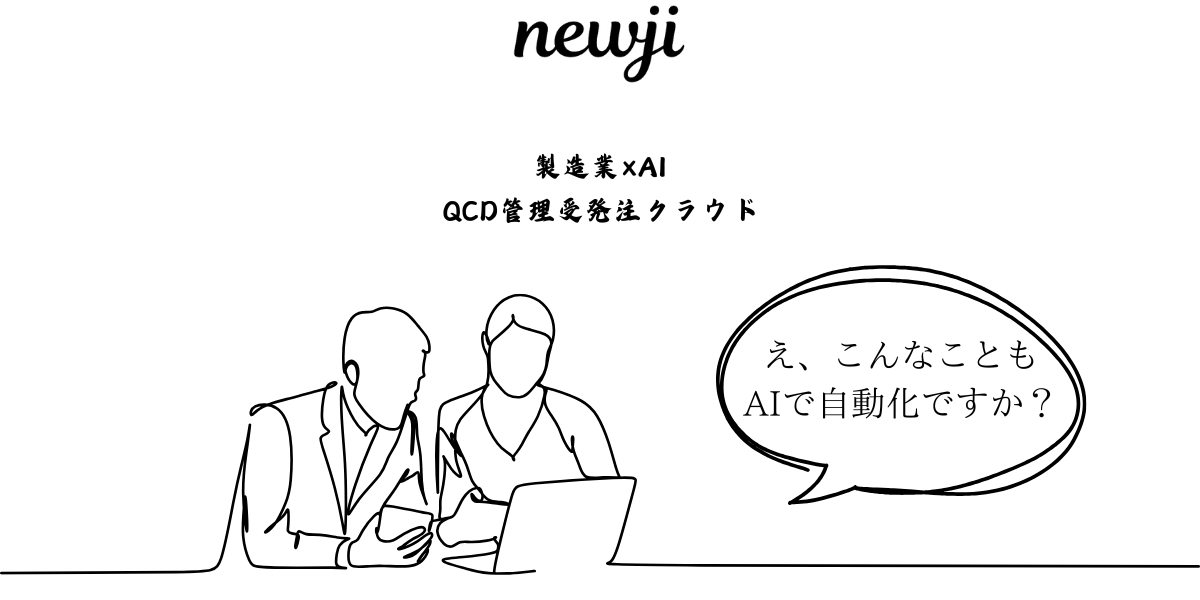
Successful Case Study in Epoxy Resin OEM: Improving Product Durability and Performance with High-Quality Materials
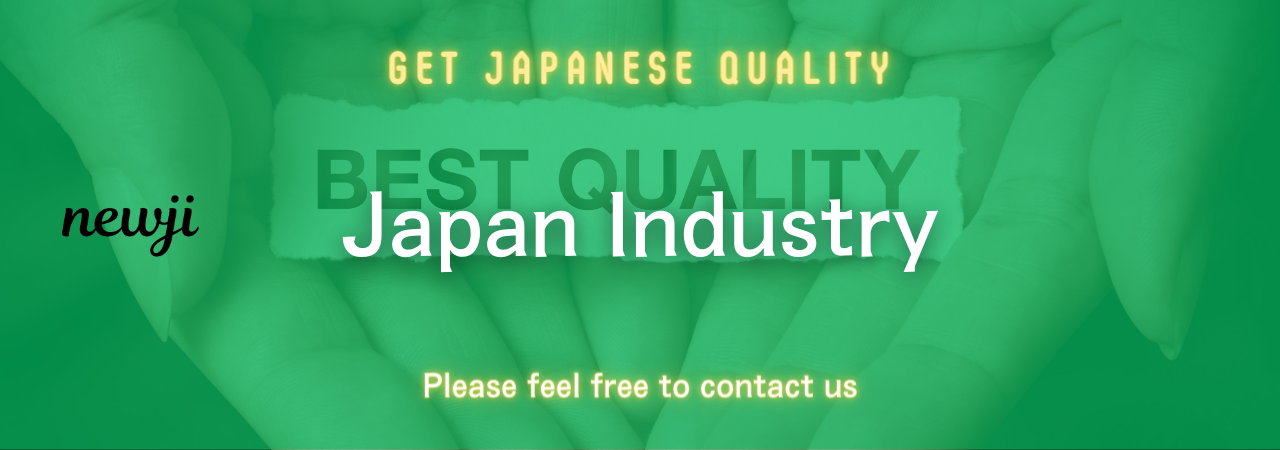
Epoxy resin OEMs have been playing a crucial role in various industries, including construction, automotive, and electronics. These Original Equipment Manufacturers (OEMs) develop and supply customized epoxy resin formulations that meet the specific needs of their clients. Over the years, epoxy resins have gained popularity due to their excellent adhesion, high mechanical properties, and resistance to chemical and environmental degradation. This article will explore a successful case study in epoxy resin OEM, emphasizing how the use of high-quality materials has led to improved product durability and performance.
目次
Understanding Epoxy Resin
Epoxy resin is a versatile material commonly used for a range of applications. It is a type of polymer that hardens when mixed with a curing agent. Epoxy resins are known for their outstanding strength, durability, and chemical resistance. These properties make them ideal for use in coatings, adhesives, and composite materials.
But what exactly makes one epoxy resin better than another? The quality of the raw materials used can have a significant impact on the final product’s performance. In this case study, we will look at how an epoxy resin OEM leveraged high-quality materials to improve the durability and performance of their products.
The Challenge
One of the key challenges faced by the epoxy resin OEM was the need to improve the durability and performance of their products. Customers were increasingly demanding epoxy resins that could withstand harsh environmental conditions, resist chemical exposure, and maintain their mechanical properties over time. To meet these demands, the OEM needed to enhance the formulation of their epoxy resins without compromising on other important attributes like ease of application and cost-effectiveness.
The Solution: Using High-Quality Materials
To address the challenge, the epoxy resin OEM decided to invest in high-quality raw materials. This involved sourcing materials from reputable suppliers known for their stringent quality control processes. The following improvements were made:
1. Enhanced Resin Base
The OEM selected a premium resin base with higher molecular weight. This base material provided better cross-linking density, resulting in a more robust and durable final product. The improved resin base also offered superior chemical resistance, making it ideal for applications in harsh environments.
2. Advanced Curing Agents
The choice of curing agents can significantly impact the properties of the final epoxy resin. The OEM opted for advanced curing agents that offered a balanced combination of fast curing time and high-performance characteristics. These curing agents ensured that the epoxy resin reached its full potential in terms of strength and durability.
3. High-Quality Fillers and Additives
Incorporating high-quality fillers and additives into the epoxy resin formulation was another critical step. The OEM used specialty fillers that enhanced the mechanical properties of the epoxy resin, such as impact resistance and rigidity. Additionally, the inclusion of UV stabilizers and antioxidants helped protect the epoxy resin from degradation due to exposure to sunlight and other environmental factors.
The Implementation Process
Implementing the new formulation involved several key steps:
1. Research and Development
The OEM’s research and development team conducted extensive testing to evaluate the performance of various raw materials. This involved experimenting with different resin bases, curing agents, and fillers to identify the optimal combination that would meet the desired performance criteria.
2. Quality Control
Strict quality control measures were put in place to ensure that all raw materials met the required specifications. The OEM worked closely with their suppliers to establish clear quality standards and conducted regular audits to verify compliance.
3. Production and Testing
The updated epoxy resin formulation was scaled up for production. During the production process, the OEM continued to monitor the quality of the raw materials and the final product. Samples of the epoxy resin were subjected to rigorous testing to verify that they met or exceeded the performance benchmarks.
The Results
The investment in high-quality materials paid off, resulting in a significant improvement in the durability and performance of the epoxy resin products. The following benefits were observed:
1. Increased Durability
The enhanced resin base and advanced curing agents contributed to a more robust and long-lasting epoxy resin. The final product demonstrated excellent resistance to wear and tear, making it suitable for demanding applications.
2. Improved Chemical Resistance
The upgraded formulation exhibited superior resistance to chemicals, including acids, alkalis, and solvents. This made the epoxy resin ideal for use in environments where chemical exposure was a concern.
3. Enhanced Environmental Stability
The inclusion of UV stabilizers and antioxidants helped protect the epoxy resin from degradation due to sunlight and other environmental factors. This resulted in longer-lasting performance, even in outdoor applications.
4. Customer Satisfaction
The improved epoxy resin products received positive feedback from customers. They appreciated the enhanced performance and durability, which translated into better end products and reduced maintenance costs.
Conclusion
This case study highlights the importance of using high-quality materials in the formulation of epoxy resins. By investing in premium raw materials and implementing stringent quality control measures, the epoxy resin OEM was able to meet the growing demands of their customers for durable and high-performance products. The success of this approach underscores the critical role that materials play in determining the overall quality and performance of epoxy resins, and serves as a valuable lesson for other manufacturers in the industry.
資料ダウンロード
QCD調達購買管理クラウド「newji」は、調達購買部門で必要なQCD管理全てを備えた、現場特化型兼クラウド型の今世紀最高の購買管理システムとなります。
ユーザー登録
調達購買業務の効率化だけでなく、システムを導入することで、コスト削減や製品・資材のステータス可視化のほか、属人化していた購買情報の共有化による内部不正防止や統制にも役立ちます。
NEWJI DX
製造業に特化したデジタルトランスフォーメーション(DX)の実現を目指す請負開発型のコンサルティングサービスです。AI、iPaaS、および先端の技術を駆使して、製造プロセスの効率化、業務効率化、チームワーク強化、コスト削減、品質向上を実現します。このサービスは、製造業の課題を深く理解し、それに対する最適なデジタルソリューションを提供することで、企業が持続的な成長とイノベーションを達成できるようサポートします。
オンライン講座
製造業、主に購買・調達部門にお勤めの方々に向けた情報を配信しております。
新任の方やベテランの方、管理職を対象とした幅広いコンテンツをご用意しております。
お問い合わせ
コストダウンが利益に直結する術だと理解していても、なかなか前に進めることができない状況。そんな時は、newjiのコストダウン自動化機能で大きく利益貢献しよう!
(Β版非公開)