- お役立ち記事
- Successful cases of digitalization in the manufacturing industry and their key points
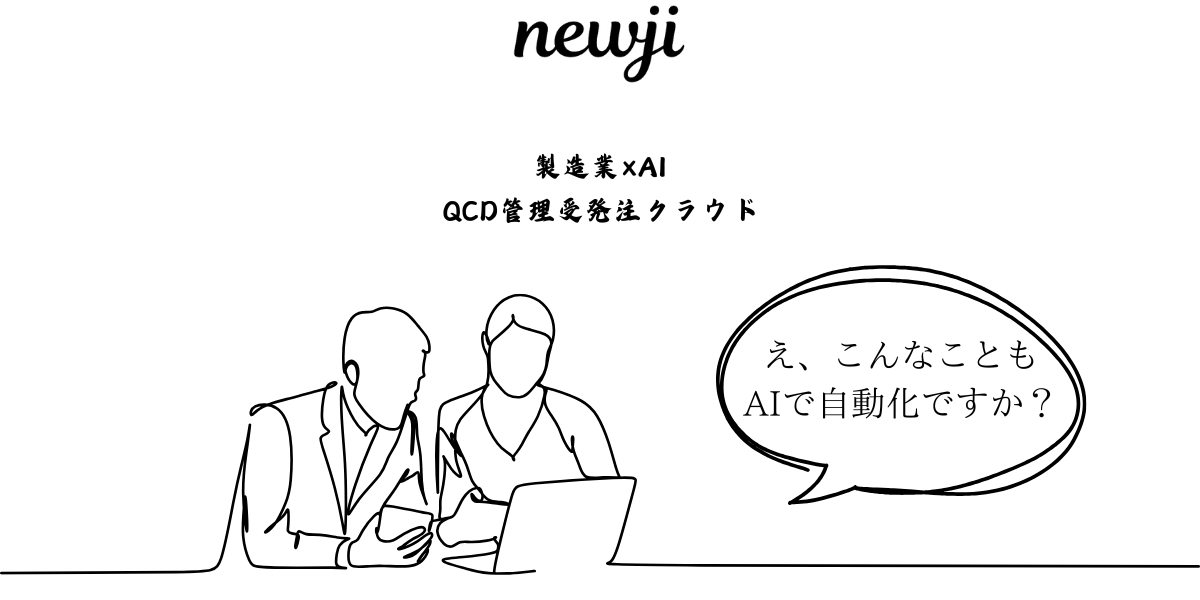
Successful cases of digitalization in the manufacturing industry and their key points
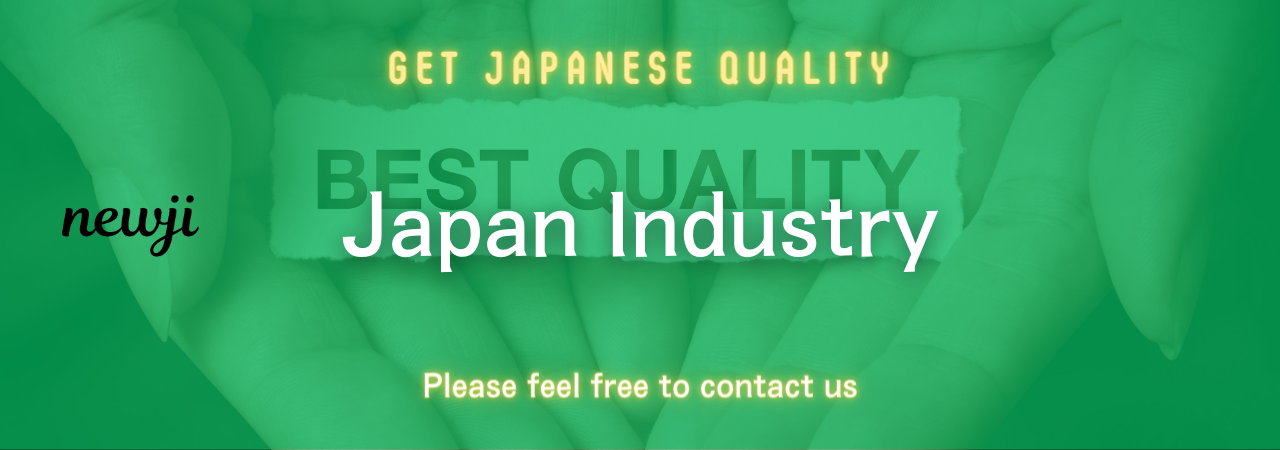
目次
Introduction to Digitalization in Manufacturing
Digitalization has become a fundamental shift in how industries operate, and the manufacturing sector is no exception.
Incorporating digital tools and technologies can lead to significant improvements in efficiency, productivity, and overall competitiveness.
This process involves using digital technologies to transform traditional manufacturing processes, making them more efficient and effective.
Successful digitalization in manufacturing not only optimizes operations but also fosters innovation and enhances product quality.
Benefits of Digitalization in Manufacturing
Digitalization offers several advantages to the manufacturing industry.
Firstly, it enhances operational efficiency by streamlining processes and reducing manual interventions, leading to higher productivity and cost savings.
Secondly, it improves decision-making capabilities through data analytics and real-time insights, allowing manufacturers to act swiftly in a dynamic market environment.
Finally, digitalization enables customization and flexibility in production, catering to the growing demand for personalized and varied products.
Case Study 1: Siemens and Predictive Maintenance
One notable example of successful digitalization is Siemens’ implementation of predictive maintenance.
By integrating IoT sensors and advanced data analytics into their machines, Siemens can anticipate equipment failures before they occur.
This approach reduces downtime and maintenance costs, optimizing the whole production process.
Data collected from equipment is analyzed to detect anomalies, enabling timely interventions and ensuring uninterrupted operations.
Key Points of Predictive Maintenance
The critical aspect of Siemens’ success lies in leveraging cutting-edge technologies for predictive maintenance.
AI and machine learning algorithms play a vital role in processing vast amounts of data and identifying patterns that suggest potential failures.
Furthermore, real-time monitoring allows quick responses, minimizing production interruptions and extending the lifespan of machinery.
Case Study 2: General Electric’s Digital Twin Technology
General Electric (GE) has emerged as a pioneer in adopting digital twin technology in manufacturing.
A digital twin is a virtual representation of a physical asset, process, or system.
By creating these virtual models, GE enables comprehensive monitoring and simulation of its complex machinery.
Key Points of Digital Twin Technology
Digital twin technology offers insights that go beyond regular monitoring.
It allows manufacturers to simulate different scenarios and predict outcomes, making it easier to fine-tune processes and improve product design.
Data-driven simulations provide a platform for continuous innovation, supporting GE’s commitment to enhancing product quality and operational efficiency.
Case Study 3: Caterpillar and Augmented Reality
Caterpillar, a global leader in heavy equipment manufacturing, successfully uses augmented reality (AR) to enhance training and support for its field technicians.
By overlaying digital content onto the physical environment, AR provides technicians with vital information and instructions.
Key Points of Augmented Reality
Caterpillar’s implementation of AR demonstrates its effectiveness in improving service productivity and reducing human error.
Technicians can visualize complex systems and receive step-by-step guidance during maintenance, leading to faster repairs and minimized downtime.
Moreover, AR reduces the need for extensive on-site training, cutting operational costs while maintaining quality.
Challenges and Considerations in Digitalization
Despite its numerous advantages, digitalization poses several challenges for manufacturing companies.
The initial investment in technology and infrastructure can be substantial.
Furthermore, integrating digital tools requires changes in company culture and adapting skillsets among employees.
Cybersecurity is another critical concern, as digital systems’ vulnerabilities can lead to data breaches and operational disruptions.
Addressing Challenges in Digitalization
To successfully navigate these challenges, companies must approach digitalization strategically.
Building a strong business case and developing a phased implementation plan can help manage costs.
Training programs should be established to equip employees with the skills needed to operate new technologies.
Moreover, investing in robust cybersecurity measures and continuous monitoring is essential to safeguard data and maintain smooth operations.
Conclusion: Embracing the Digital Future
Digitalization in manufacturing is no longer a matter of if, but when.
Successful cases from industry giants like Siemens, GE, and Caterpillar reveal the transformative impact digital technologies can have on operations.
These companies demonstrate that with the right strategies and technologies, manufacturers can optimize their processes, reduce costs, and stay competitive in an ever-evolving market.
As digitalization continues to reshape the industry landscape, embracing these advancements is crucial for achieving long-term success.
資料ダウンロード
QCD調達購買管理クラウド「newji」は、調達購買部門で必要なQCD管理全てを備えた、現場特化型兼クラウド型の今世紀最高の購買管理システムとなります。
ユーザー登録
調達購買業務の効率化だけでなく、システムを導入することで、コスト削減や製品・資材のステータス可視化のほか、属人化していた購買情報の共有化による内部不正防止や統制にも役立ちます。
NEWJI DX
製造業に特化したデジタルトランスフォーメーション(DX)の実現を目指す請負開発型のコンサルティングサービスです。AI、iPaaS、および先端の技術を駆使して、製造プロセスの効率化、業務効率化、チームワーク強化、コスト削減、品質向上を実現します。このサービスは、製造業の課題を深く理解し、それに対する最適なデジタルソリューションを提供することで、企業が持続的な成長とイノベーションを達成できるようサポートします。
オンライン講座
製造業、主に購買・調達部門にお勤めの方々に向けた情報を配信しております。
新任の方やベテランの方、管理職を対象とした幅広いコンテンツをご用意しております。
お問い合わせ
コストダウンが利益に直結する術だと理解していても、なかなか前に進めることができない状況。そんな時は、newjiのコストダウン自動化機能で大きく利益貢献しよう!
(Β版非公開)