- お役立ち記事
- Successful example of reviewing the purchasing department’s procurement flow to avoid material shortages
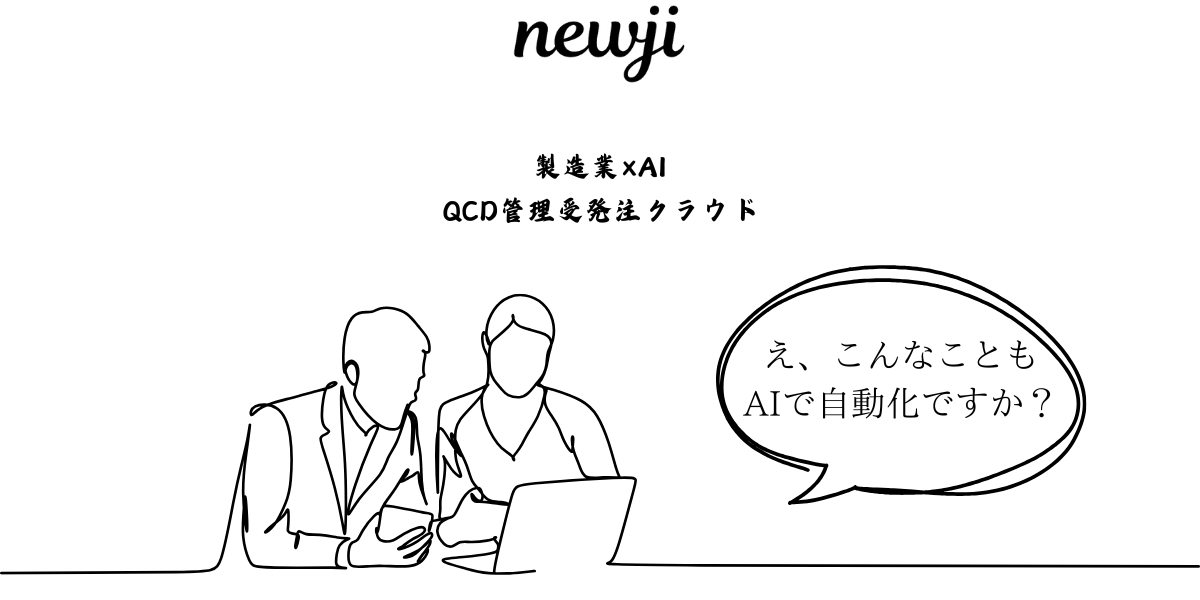
Successful example of reviewing the purchasing department’s procurement flow to avoid material shortages
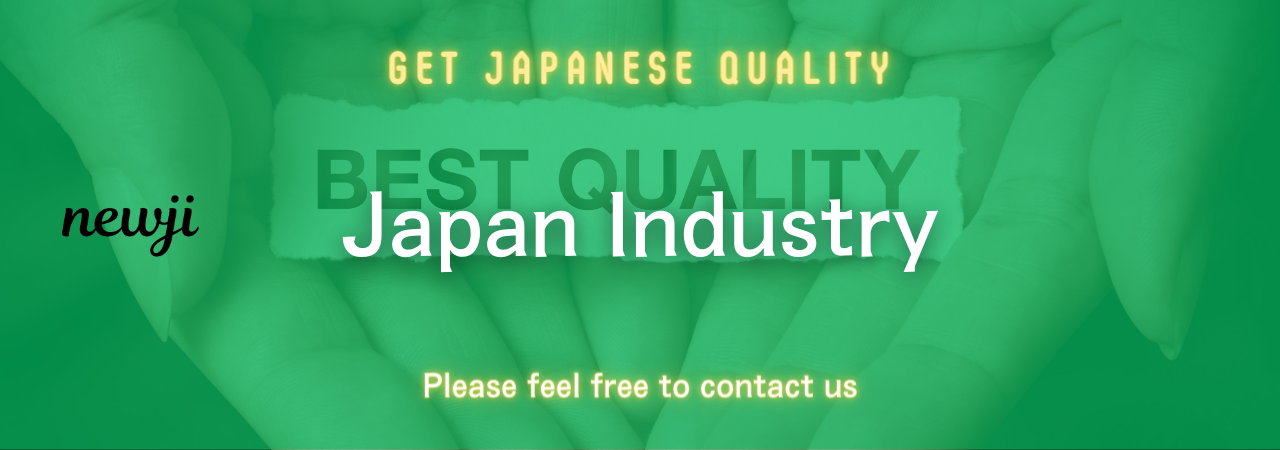
目次
Understanding the Importance of Procurement Flow
In any organization, the purchasing department plays a crucial role in maintaining smooth operations.
However, material shortages can become a major roadblock, hindering productivity and leading to losses.
This is where reviewing the procurement flow becomes essential.
By optimizing procurement processes, companies can avoid material shortages and set the stage for uninterrupted progress.
The Challenges of Material Shortages
Material shortages are more than just a supply chain hiccup.
They can lead to production delays, increased costs, unsatisfied customers, and can damage a company’s reputation.
These issues highlight the need for a robust procurement flow that can anticipate and mitigate such risks.
Steps to Review the Procurement Flow
Reviewing the procurement flow is not a one-step process.
It’s a thorough evaluation of existing procedures and identifying improvements.
Here’s how companies can successfully review their procurement flow:
1. Assess the Current Process
The first step is to understand the existing procurement system.
This involves mapping out each step, from identifying needs to placing orders and managing inventory.
Consider talking to team members to gain insights on what works well and what doesn’t.
2. Identify and Address Bottlenecks
Material shortages often arise from bottlenecks in the procurement flow.
These can occur at any stage, such as slow approval processes, delayed communications with suppliers, or inefficiencies in inventory management.
Once identified, these bottlenecks need targeted solutions, such as streamlining approval processes or improving communication channels.
3. Leverage Technology
Technology can be a game-changer for procurement processes.
Implementing electronic procurement systems can increase efficiency and accuracy, reduce manual errors, and provide real-time data.
For instance, using inventory management software can help monitor stock levels and automatically reorder materials before shortages occur.
4. Collaborate with Suppliers
Building strong relationships with suppliers is key to avoiding material shortages.
Regular communication ensures that suppliers understand your needs and can anticipate demand.
Collaborative forecasting, where suppliers and buyers work together to predict future requirements, can also be beneficial.
5. Establish a Contingency Plan
Despite best efforts, unforeseen circumstances like natural disasters or global shortages may disrupt the supply chain.
Having a contingency plan in place can mitigate these risks.
Options include diversifying suppliers, maintaining a safety stock, or having alternative materials that can be used temporarily.
Successful Examples of Optimized Procurement Flow
Several companies have successfully revised their procurement processes to prevent shortages.
By examining these examples, businesses can derive practical insights.
Case Study: ABC Manufacturing
ABC Manufacturing, a company struggling with frequent material shortages, re-evaluated its procurement flow.
They identified that delays mainly occurred due to slow communication with suppliers.
By implementing automated ordering systems and improving supplier relations, ABC Manufacturing significantly reduced delays.
They also adopted technology that provides real-time inventory updates, further minimizing stock outages.
Case Study: XYZ Retail
XYZ Retail faced challenges in maintaining adequate stock during peak seasons.
Their approach involved collaborating closely with suppliers to enhance demand forecasting.
Moreover, XYZ Retail fine-tuned their ordering schedule and established a buffer stock during high-demand periods.
As a result, they improved stocking efficiency and customer satisfaction.
Key Takeaways
Reviewing and streamlining your procurement flow is essential for avoiding material shortages.
Through understanding the current process and employing strategic solutions, companies can achieve more resilient supply chains.
By leveraging technology, fostering supplier relationships, and preparing for contingencies, organizations can avert disruptions and maintain smooth operations.
Ultimately, a proactive approach to procurement can enhance efficiency, reduce costs, and strengthen market standing.
資料ダウンロード
QCD調達購買管理クラウド「newji」は、調達購買部門で必要なQCD管理全てを備えた、現場特化型兼クラウド型の今世紀最高の購買管理システムとなります。
ユーザー登録
調達購買業務の効率化だけでなく、システムを導入することで、コスト削減や製品・資材のステータス可視化のほか、属人化していた購買情報の共有化による内部不正防止や統制にも役立ちます。
NEWJI DX
製造業に特化したデジタルトランスフォーメーション(DX)の実現を目指す請負開発型のコンサルティングサービスです。AI、iPaaS、および先端の技術を駆使して、製造プロセスの効率化、業務効率化、チームワーク強化、コスト削減、品質向上を実現します。このサービスは、製造業の課題を深く理解し、それに対する最適なデジタルソリューションを提供することで、企業が持続的な成長とイノベーションを達成できるようサポートします。
オンライン講座
製造業、主に購買・調達部門にお勤めの方々に向けた情報を配信しております。
新任の方やベテランの方、管理職を対象とした幅広いコンテンツをご用意しております。
お問い合わせ
コストダウンが利益に直結する術だと理解していても、なかなか前に進めることができない状況。そんな時は、newjiのコストダウン自動化機能で大きく利益貢献しよう!
(Β版非公開)