- お役立ち記事
- Successful examples of lead time reduction strategies promoted by purchasing departments
Successful examples of lead time reduction strategies promoted by purchasing departments
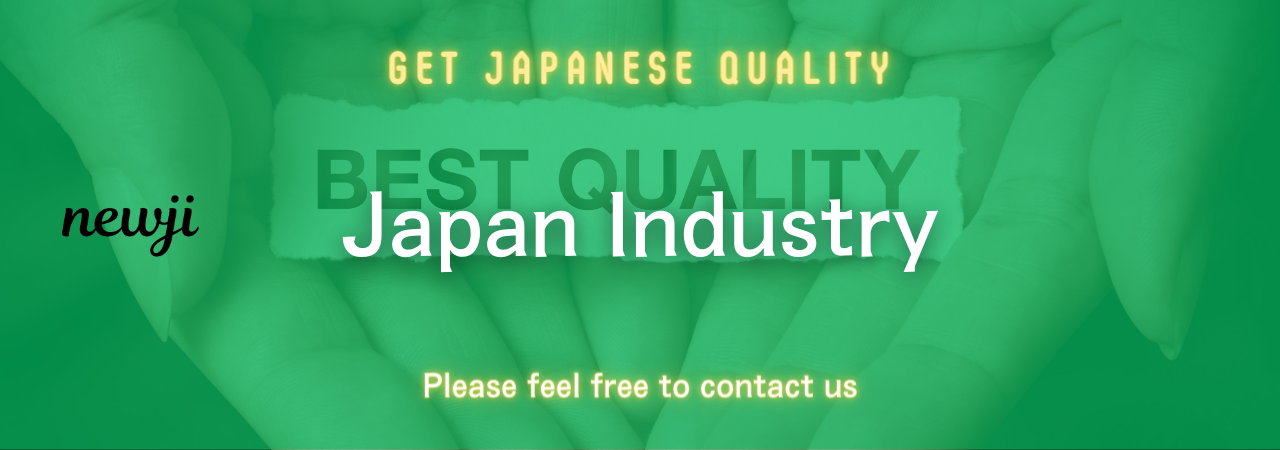
目次
Understanding Lead Time and Its Importance
Lead time refers to the period required from the initiation of a process to its completion.
In a purchasing context, it involves the time from when a purchase order is placed to when the item is received and ready for use.
Reducing lead time is crucial as it can enhance a company’s competitiveness by improving efficiency, responsiveness, and customer satisfaction.
Purchasing departments play a vital role in managing and minimizing lead times.
They are responsible for coordinating with suppliers, managing inventory, and ensuring there are no delays in the supply chain.
Lead time reduction strategies can positively influence production schedules, reduce inventory costs, and better respond to market demands.
Streamlining Supplier Relationships
One effective strategy for reducing lead times is to streamline relationships with suppliers.
Building strong, collaborative partnerships can lead to better communication and fewer delays.
Many companies have successfully implemented supplier relationship management (SRM) tools to improve collaboration.
SRM tools facilitate information sharing and enable faster decision-making processes.
For example, some companies have created automated systems that allow suppliers direct access to inventory levels.
This means suppliers can initiate restocking processes without waiting for formal purchase orders, significantly reducing lead times.
Another approach is to work closely with suppliers to identify and remove bottlenecks in the supply chain.
Regular meetings and workshops can uncover challenges and jointly develop solutions, leading to a more efficient supply chain and reduced lead times.
Improving Forecasting and Inventory Management
Effective demand forecasting and inventory management are crucial components of reducing lead times.
Accurate forecasting allows companies to anticipate demand more precisely, thus avoiding stockouts and reducing excessive inventory.
Using advanced analytics and software solutions can assist in predicting demand patterns.
For example, some companies have adopted machine learning algorithms to analyze historical data and identify trends, adjusting purchase orders accordingly.
An agile inventory management system also plays a significant role in lead time reduction.
By maintaining optimal inventory levels, companies can ensure they have enough stock to meet demand without overstocking, which ties up capital and space.
Case Study: A Global Electronics Manufacturer
A global electronics manufacturer improved its lead time by implementing just-in-time (JIT) inventory management strategies in conjunction with advanced forecasting tools.
By aligning inventory with actual demand, the company significantly minimized excess stocking and reduced lead times by over 30%.
Utilizing Technology for Efficiency
Technology stands as a powerful enabler in the quest to reduce lead times.
Many purchasing departments have benefited from implementing Enterprise Resource Planning (ERP) systems that integrate all functions of a business.
ERP systems help coordinate supply chain activities by providing real-time data sharing across departments.
This visibility ensures that any issues in procurement, production, or distribution are quickly identified and rectified.
Additionally, adopting automation tools can streamline procurement processes.
Automated purchase orders, invoice processing, and supplier communication can significantly reduce administrative burdens and accelerate the supply chain.
Case Study: A Leading Retail Chain
A leading retail chain successfully reduced its lead time by integrating an AI-driven purchasing system.
The system analyzed sales data in real-time and triggered automated purchase orders for high-demand products, effectively cutting lead time by 40%.
Implementing Agile Methodologies
Agile methodologies, originally developed for software development, have shown promise in supply chain management.
These methodologies focus on flexibility, iterative processes, and customer-centric approaches.
By adopting agile principles, purchasing departments can respond more swiftly to changes in supply and demand.
Regular iteration meetings, short feedback loops, and continuous improvement cycles allow teams to adapt to new information quickly.
Case Study: A Fast-Fashion Brand
A fast-fashion brand leveraged agile supply chain principles to keep up with rapidly changing fashion trends.
By focusing on short lead times and small production batches, the brand could react to market demands and fashion fads promptly, resulting in a 50% reduction in lead time.
Optimizing Transportation and Logistics
Transportation and logistics are critical components in the supply chain where significant lead time reductions can be achieved.
Optimizing these aspects involves choosing efficient shipping methods, exploring alternative routes, and improving coordination between different transportation modes.
Working with logistics providers to ensure timely delivery and exploring technological solutions such as GPS tracking and route optimization can further minimize delays.
A coordinated approach ensures products move swiftly through the supply chain, contributing to reduced lead times.
Case Study: A Global Supply Chain Leader
One global supply chain leader collaborated closely with logistics partners and employed advanced route optimization software.
By redesigning its transportation network and improving scheduling, the company reduced lead times by 25%.
Conclusion
Lead time reduction is a multifaceted strategy that involves optimizing supplier relationships, leveraging technology, improving forecasting, and employing agile methodologies.
Purchasing departments play a crucial role in this process by coordinating efforts across the organization and ensuring that every step in the procurement process is efficient.
By adopting these strategies, companies can achieve significant reductions in lead time, leading to enhanced competitiveness, better customer satisfaction, and improved operational efficiency.
資料ダウンロード
QCD調達購買管理クラウド「newji」は、調達購買部門で必要なQCD管理全てを備えた、現場特化型兼クラウド型の今世紀最高の購買管理システムとなります。
ユーザー登録
調達購買業務の効率化だけでなく、システムを導入することで、コスト削減や製品・資材のステータス可視化のほか、属人化していた購買情報の共有化による内部不正防止や統制にも役立ちます。
NEWJI DX
製造業に特化したデジタルトランスフォーメーション(DX)の実現を目指す請負開発型のコンサルティングサービスです。AI、iPaaS、および先端の技術を駆使して、製造プロセスの効率化、業務効率化、チームワーク強化、コスト削減、品質向上を実現します。このサービスは、製造業の課題を深く理解し、それに対する最適なデジタルソリューションを提供することで、企業が持続的な成長とイノベーションを達成できるようサポートします。
オンライン講座
製造業、主に購買・調達部門にお勤めの方々に向けた情報を配信しております。
新任の方やベテランの方、管理職を対象とした幅広いコンテンツをご用意しております。
お問い合わせ
コストダウンが利益に直結する術だと理解していても、なかなか前に進めることができない状況。そんな時は、newjiのコストダウン自動化機能で大きく利益貢献しよう!
(Β版非公開)