- お役立ち記事
- Successful examples of procurement risk assessment told by purchasing department experts
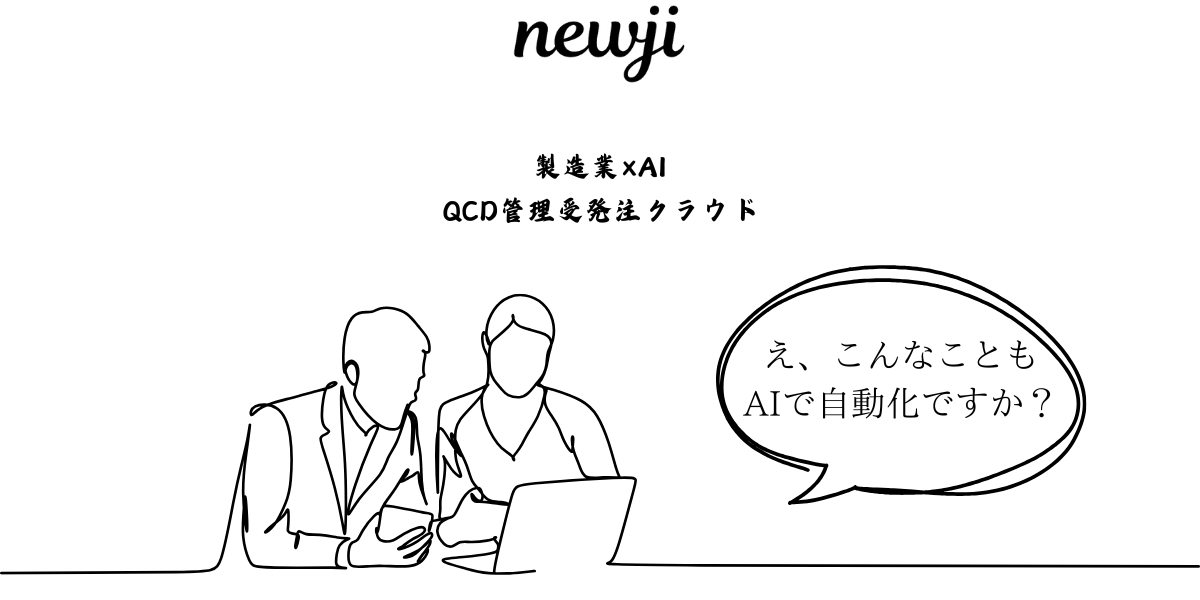
Successful examples of procurement risk assessment told by purchasing department experts
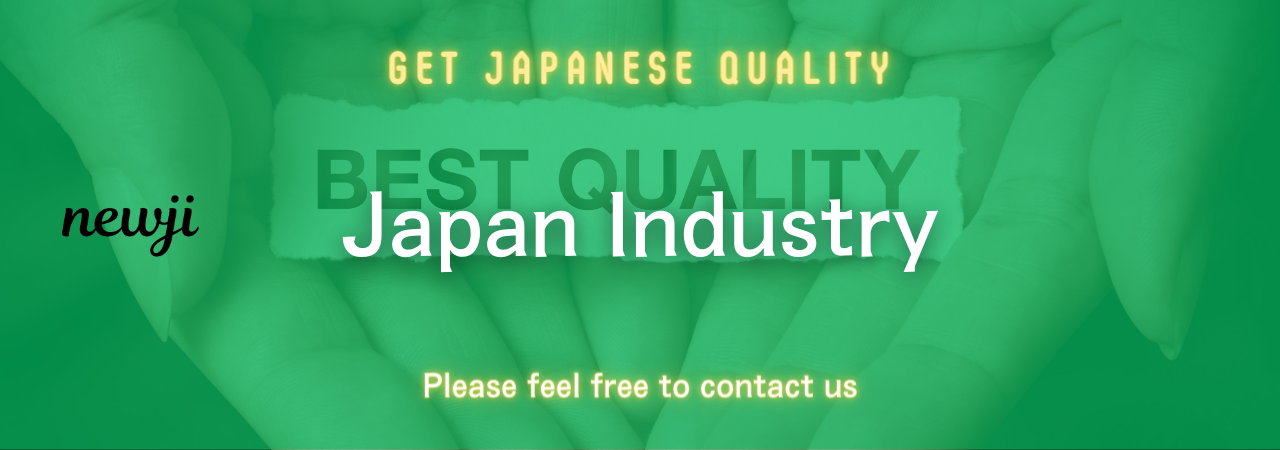
Understanding Procurement Risk Assessment
Procurement risk assessment is a vital process in supply chain management that helps organizations identify, evaluate, and mitigate potential risks that could disrupt their procurement activities.
It’s an important tool that purchasing department experts use to ensure that the organization’s supply chain remains robust and effective.
Assessing these risks involves analyzing different factors that could impact the procurement process, such as supplier reliability, market dynamics, geopolitical issues, and more.
When conducted effectively, procurement risk assessment can save companies from unforeseen disruptions, financial losses, and reputational damage.
Identifying Potential Risks
The first step in successful procurement risk assessment is identifying the various risks that could affect the procurement process.
These risks could be internal or external, controllable or uncontrollable.
For example, supplier reliability is a major concern.
Suppliers who frequently delay deliveries or fail to meet quality standards pose a significant risk.
External factors like geopolitical tensions or natural disasters can also impact the supply chain, leading to delays or increased costs.
Market volatility is another risk factor that needs careful consideration.
Fluctuations in prices for raw materials can dramatically alter the cost of procurement.
Currency exchange rates can also impact costs, especially for organizations that deal with international suppliers.
Understanding these risks is the first step towards mitigating them.
Analyzing and Evaluating Risks
Once potential risks have been identified, the next step is to analyze and evaluate them.
This involves assessing the likelihood of each risk and its potential impact on the organization’s operations.
Purchasing department experts use various tools and methodologies to evaluate these risks, such as risk matrices and scoring systems.
These tools help prioritize risks so that organizations can focus on the most severe and probable ones.
Quantitative analysis, like statistical models and simulation, can provide insight into the potential impact and likelihood of risks.
For instance, using past data to forecast supplier performance or market changes can help assess future risks.
Qualitative analysis, such as expert opinions or scenario planning, can also be instrumental in understanding complex or intangible risks.
Developing Risk Mitigation Strategies
Having identified and evaluated the risks, the next step is developing strategies to mitigate them.
Risk mitigation is about reducing the impact and likelihood of risks.
One common strategy is to diversify the supplier base.
Relying on a single supplier can be risky if that supplier faces challenges.
By working with multiple suppliers, organizations can reduce dependency and lower supply chain risks.
Another mitigation strategy is to establish strong contractual agreements with clear terms and conditions.
These contracts can include clauses that protect the organization from changes in market conditions or supplier failures.
Investing in technology for better supply chain visibility is also vital.
With real-time data and advanced analytics, purchasing departments can anticipate and respond to risks more effectively.
Implementing and Monitoring
Once risk mitigation strategies are in place, they must be implemented and continuously monitored.
Effective implementation requires commitment from all levels of the organization.
Regular training ensures that staff understands risk management processes and can respond accordingly.
Monitoring is ongoing and involves keeping track of risk indicators and the external environment.
Regular audits and reviews help ensure that risk mitigation strategies are functioning as intended.
They also allow for adjustments in response to changing circumstances.
Advanced technologies like AI and machine learning offer enhanced monitoring capabilities, enabling organizations to predict potential risks more accurately and take preemptive action.
Learning from Successful Examples
Many organizations have successfully applied procurement risk assessment to safeguard their operations.
For example, a multinational electronics company faced challenges due to political instability in a key supplier’s country.
By proactively assessing this risk, the company diversified its supplier base well before the political situation worsened, ensuring uninterrupted production.
Another example is a retail giant that used data analytics to anticipate weather-related disruptions in its logistics network.
By identifying regions at high risk of natural disasters, the company adjusted its inventory levels and distribution strategies, minimizing the impact of such disruptions.
Conclusion
Procurement risk assessment is not just a one-time task but an ongoing process that supports organizational resilience and efficiency.
By identifying potential risks, evaluating their impact, and developing robust mitigation strategies, purchasing department experts can protect their companies from unforeseen disruptions and financial setbacks.
Learning from successful examples reinforces the importance of proactive risk management and the role it plays in maintaining a robust supply chain.
With consistent monitoring and adaptation, organizations can navigate the complex landscape of global procurement with confidence.
資料ダウンロード
QCD調達購買管理クラウド「newji」は、調達購買部門で必要なQCD管理全てを備えた、現場特化型兼クラウド型の今世紀最高の購買管理システムとなります。
ユーザー登録
調達購買業務の効率化だけでなく、システムを導入することで、コスト削減や製品・資材のステータス可視化のほか、属人化していた購買情報の共有化による内部不正防止や統制にも役立ちます。
NEWJI DX
製造業に特化したデジタルトランスフォーメーション(DX)の実現を目指す請負開発型のコンサルティングサービスです。AI、iPaaS、および先端の技術を駆使して、製造プロセスの効率化、業務効率化、チームワーク強化、コスト削減、品質向上を実現します。このサービスは、製造業の課題を深く理解し、それに対する最適なデジタルソリューションを提供することで、企業が持続的な成長とイノベーションを達成できるようサポートします。
オンライン講座
製造業、主に購買・調達部門にお勤めの方々に向けた情報を配信しております。
新任の方やベテランの方、管理職を対象とした幅広いコンテンツをご用意しております。
お問い合わせ
コストダウンが利益に直結する術だと理解していても、なかなか前に進めることができない状況。そんな時は、newjiのコストダウン自動化機能で大きく利益貢献しよう!
(Β版非公開)