- お役立ち記事
- Successful examples of productivity improvement achieved by using IoT devices in factories
月間76,176名の
製造業ご担当者様が閲覧しています*
*2025年3月31日現在のGoogle Analyticsのデータより
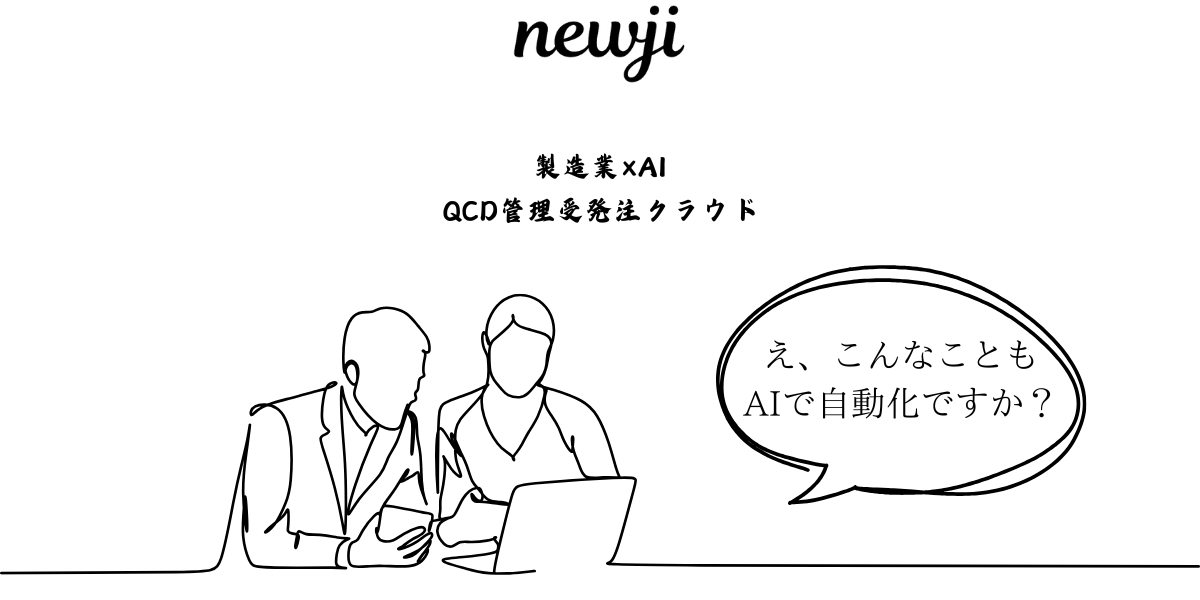
Successful examples of productivity improvement achieved by using IoT devices in factories
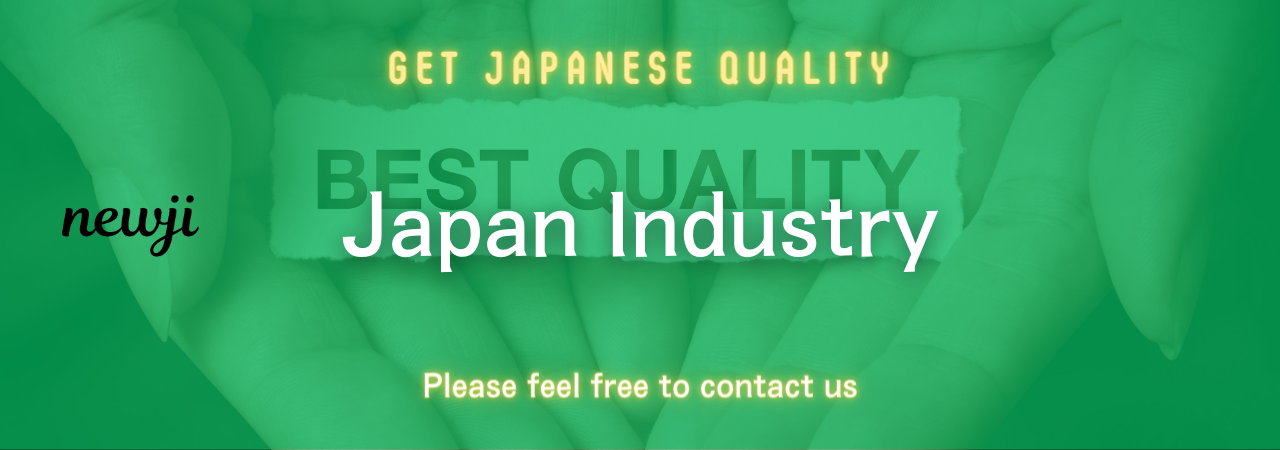
目次
Introduction to IoT in Factories
The industrial world is experiencing a seismic shift, thanks largely to the implementation of the Internet of Things (IoT) in manufacturing settings.
IoT devices are revolutionizing how factories operate by improving various aspects like efficiency, production quality, and safety.
By connecting machines, equipment, and sensors to the internet, factories gain incredible insights that were previously unimaginable.
This powerful technology collects real-time data, enabling enhanced decision-making and opening doors to unprecedented levels of productivity.
In this article, we will explore successful examples of factories using IoT devices to substantially increase productivity.
Predictive Maintenance for Optimal Efficiency
One of the most significant benefits of IoT in factories is predictive maintenance.
Traditional maintenance practices usually relied on routine checks or addressing breakdowns as they happened.
With IoT, factories can predict when a machine is likely to fail and schedule maintenance accordingly.
This prevents unexpected downtime and ensures that equipment is functioning at peak performance.
A great example is Rolls-Royce, which uses IoT to track the status of aircraft engines during flights.
By collecting data from their engines, they can accurately predict when maintenance is required.
This approach not only saves time but also reduces costs and increases safety.
In a factory setting, similar IoT applications can dramatically boost productivity through efficient maintenance strategies, reducing machine downtime, and extending equipment life.
Enhanced Quality Control through IoT
IoT devices have also redefined quality control processes in manufacturing.
Real-time data from sensors helps detect defects or errors much earlier in the production process.
This early detection ensures that only high-quality products proceed to the next stage, minimizing waste and inefficiencies.
For instance, BMW has implemented IoT in its production lines to monitor manufacturing processes.
Sensors meticulously track parameters such as temperature, pressure, and environmental conditions.
These sensors immediately alert operators if any parameter deviates from the set standards.
By catching these deviations early, BMW ensures that every car that rolls off the production line meets their stringent quality standards.
Such a data-driven approach to quality control not only improves the final product but also significantly boosts overall productivity and cost-effectiveness.
Real-Time Data for Decision Making
In the fast-paced world of manufacturing, access to real-time data can be a game-changer.
IoT devices provide this real-time data, enabling factory managers and operators to make more informed and timely decisions.
Consider the example of Ford, which uses IoT technology in its production facilities to collect data and provide insights into its manufacturing processes.
By analyzing this data, Ford can predict potential bottlenecks and resolve them before they escalate, enhancing the overall efficiency of their production lines.
Real-time monitoring also helps allocate resources more effectively, ensuring that production runs as smoothly as possible.
This real-time visibility into operations allows for faster responses to challenges, optimized workflows, and can lead to substantial increases in production capability.
Energy Management and Cost Savings
Energy consumption is a significant cost factor in factory operations.
IoT devices can help manage energy usage more efficiently by monitoring consumption patterns and identifying areas where energy is being wasted.
With this information, factories can implement solutions to optimize energy usage, reducing costs and environmental impact.
For example, General Electric (GE) has used IoT for energy optimization in its manufacturing facilities.
By leveraging IoT data, GE can predict when energy demand spikes or drops, allowing them to adjust power usage to match these patterns.
This has led to notable reductions in energy costs and a more sustainable manufacturing process.
Such smart energy management not only saves money but also supports a factory’s sustainability goals, aligning with increasing global emphasis on eco-friendly manufacturing practices.
Improved Workplace Safety with IoT
Safety is paramount in any manufacturing environment.
IoT solutions enhance workplace safety by providing critical data about environmental conditions, equipment health, and employee whereabouts.
Take the example of Dow Chemical, which uses IoT devices to ensure employee safety.
Sensors monitor environmental conditions such as temperature and the presence of hazardous gases.
Alerts are triggered if any readings present potential danger, enabling swift action to protect workers.
By adopting IoT-driven safety measures, factories reduce workplace accidents and create a safer working environment.
This not only safeguards human resources but also leads to fewer interruptions in production, thus improving productivity.
Conclusion
The integration of IoT devices in factories represents a transformative change in how manufacturing processes are managed and optimized.
Through predictive maintenance, enhanced quality control, real-time data insights, energy management, and improved safety measures, IoT has shown its potential to significantly boost productivity.
As factories continue to embrace these technologies, the future of manufacturing looks increasingly efficient and innovative.
By understanding and learning from successful examples, like those of Rolls-Royce, BMW, Ford, GE, and Dow Chemical, other manufacturers can implement IoT solutions tailored to their unique needs and operational challenges.
This progress not only benefits individual businesses but also contributes to the broader industry’s competitive edge on a global scale.
資料ダウンロード
QCD管理受発注クラウド「newji」は、受発注部門で必要なQCD管理全てを備えた、現場特化型兼クラウド型の今世紀最高の受発注管理システムとなります。
ユーザー登録
受発注業務の効率化だけでなく、システムを導入することで、コスト削減や製品・資材のステータス可視化のほか、属人化していた受発注情報の共有化による内部不正防止や統制にも役立ちます。
NEWJI DX
製造業に特化したデジタルトランスフォーメーション(DX)の実現を目指す請負開発型のコンサルティングサービスです。AI、iPaaS、および先端の技術を駆使して、製造プロセスの効率化、業務効率化、チームワーク強化、コスト削減、品質向上を実現します。このサービスは、製造業の課題を深く理解し、それに対する最適なデジタルソリューションを提供することで、企業が持続的な成長とイノベーションを達成できるようサポートします。
製造業ニュース解説
製造業、主に購買・調達部門にお勤めの方々に向けた情報を配信しております。
新任の方やベテランの方、管理職を対象とした幅広いコンテンツをご用意しております。
お問い合わせ
コストダウンが利益に直結する術だと理解していても、なかなか前に進めることができない状況。そんな時は、newjiのコストダウン自動化機能で大きく利益貢献しよう!
(β版非公開)