- お役立ち記事
- Successful examples of schedule management in the prototyping process
月間76,176名の
製造業ご担当者様が閲覧しています*
*2025年3月31日現在のGoogle Analyticsのデータより
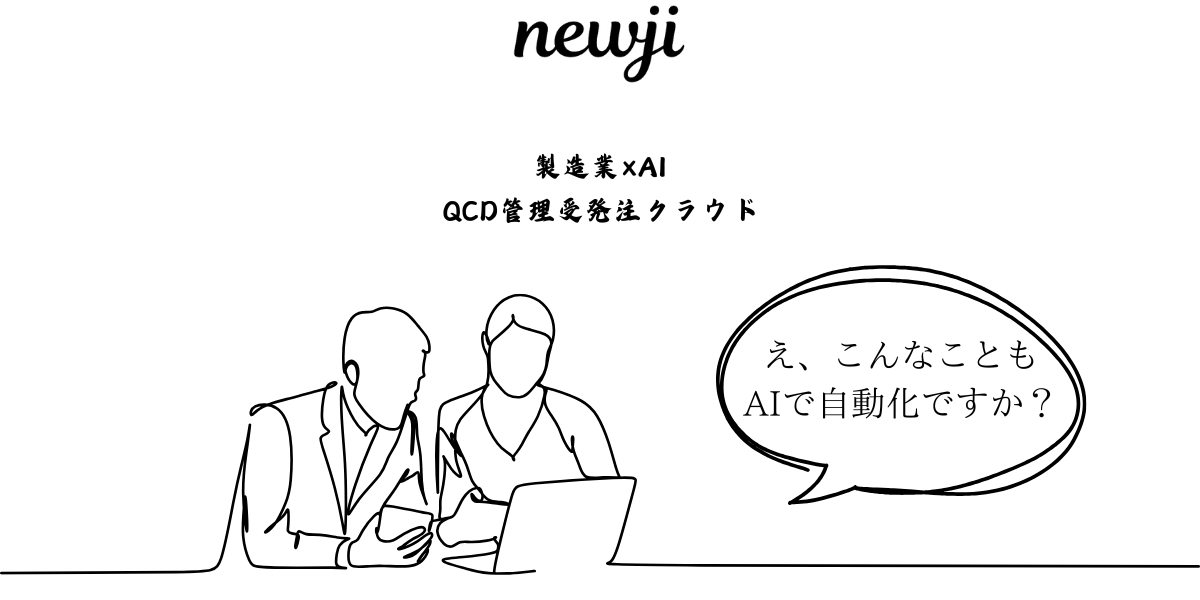
Successful examples of schedule management in the prototyping process
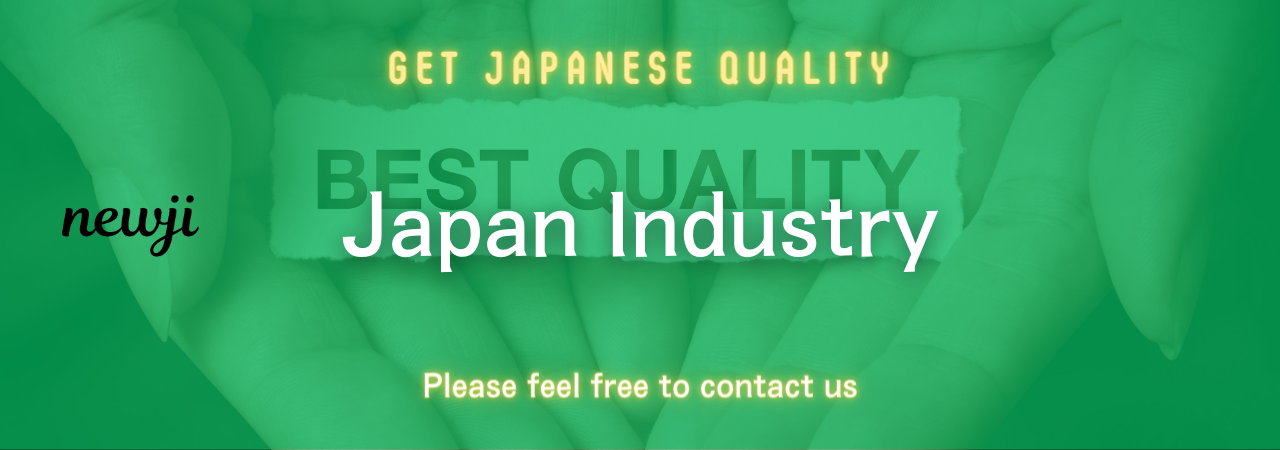
目次
Introduction to Schedule Management in Prototyping
The journey from an idea to a tangible product often begins with a prototype.
Prototyping allows creators to visualize concepts, test functionalities, and identify areas for improvement before finalizing the design.
However, the process of prototyping can become complex and time-consuming without proper schedule management.
Successful schedule management ensures that projects remain on track, resources are efficiently used, and deadlines are met.
In this article, we’ll explore some successful examples of schedule management in prototyping that illustrate how effective planning and organization contribute to innovative results.
Understanding Prototyping and Its Challenges
Prototyping is a critical phase in product development where concepts are transformed into physical models or samples.
While it is an essential step, several challenges can arise.
Common problems include resource constraints, technological limitations, and fluctuating requirements.
These issues can lead to delays and budget overruns if not managed properly.
Effective schedule management is crucial in navigating these challenges, as it helps streamline processes and keep the project on track.
Key Principles of Effective Schedule Management
Before diving into successful examples, it is important to comprehend the key principles of effective schedule management.
Firstly, **prioritization** is vital in identifying which tasks should be completed first to maximize productivity.
Secondly, **flexibility** allows teams to adjust plans and accommodate unforeseen changes.
Finally, **communication and collaboration** are vital in ensuring that every team member is aligned and aware of their responsibilities.
These principles form the foundation for effective schedule management in the prototyping process.
Case Study 1: Tech Innovators’ Agile Approach
Let’s take the example of a tech company, Tech Innovators, which embarked on creating a cutting-edge wearable device.
Faced with tight deadlines, they adopted an agile project management approach to streamline their prototyping process.
By breaking the project into smaller, manageable sprints, they set clear milestones that helped the team focus on specific tasks.
Regular meetings and feedback loops ensured everyone was aligned and allowed them to quickly identify and address issues.
This approach enabled Tech Innovators to deliver a working prototype ahead of schedule without compromising on quality.
Benefits of Agile Management in Prototyping
Agile management emphasizes short development cycles, known as sprints, that promote regular reassessment and adaptation.
This method proved successful for Tech Innovators as it provided flexibility and improved the team’s ability to manage time effectively.
Through frequent reviews and adjustments, they could make informed decisions swiftly and reduce downtime, contributing to their success in schedule management.
Case Study 2: Precision Engineering’s Resource Optimization
Precision Engineering, a company known for manufacturing industrial tools, faced the challenge of resource allocation in their prototyping phase.
To address this, they implemented a resource management strategy that focused on optimizing their available assets.
They conducted an initial assessment to determine the most critical resources required for each stage of the prototyping process.
By creating a resource schedule that prioritized key components and limited unnecessary expenses, Precision Engineering managed to complete their prototype within budget and on time.
Strategies for Effective Resource Management
Effective resource management involves forecasting, allocation, and monitoring.
Precision Engineering used a combination of resource leveling and resource smoothing techniques to ensure resources were used efficiently.
Resource leveling helped them maintain consistent workflow and avoid overloading any particular resource, while resource smoothing ensured that resources were allocated during non-peak times, minimizing delays.
Case Study 3: Creative Solutions’ Collaborative Environment
Creative Solutions, a startup focusing on eco-friendly products, adopted a collaborative approach to schedule management during prototyping.
They placed a strong emphasis on cross-departmental communication and teamwork.
Through regular brainstorming sessions and open communication channels, they promoted an environment where ideas flowed freely and challenges were addressed collectively.
This collaborative culture led to enhanced creativity and faster problem-solving, enabling them to adhere to their prototyping schedules consistently.
Fostering a Collaborative Workplace
The success of Creative Solutions highlights the importance of fostering a collaborative workplace.
By encouraging an inclusive work culture, teams can share insights and skills that contribute to effective schedule management.
When departments work collaboratively, they can anticipate potential issues and develop timely solutions, which reduces the risk of project delays.
Conclusion: The Impact of Effective Schedule Management
The examples of Tech Innovators, Precision Engineering, and Creative Solutions demonstrate the profound impact effective schedule management can have on the prototyping process.
Through agile methodologies, resource optimization, and collaborative practices, these companies successfully navigated the challenges of prototyping while meeting their deadlines and maintaining quality.
For organizations aiming to excel in product development, adopting and tailoring these schedule management techniques is critical for success.
As the landscape of innovation continues to evolve, efficient schedule management in prototyping will remain a key differentiator in turning ideas into reality.
資料ダウンロード
QCD管理受発注クラウド「newji」は、受発注部門で必要なQCD管理全てを備えた、現場特化型兼クラウド型の今世紀最高の受発注管理システムとなります。
ユーザー登録
受発注業務の効率化だけでなく、システムを導入することで、コスト削減や製品・資材のステータス可視化のほか、属人化していた受発注情報の共有化による内部不正防止や統制にも役立ちます。
NEWJI DX
製造業に特化したデジタルトランスフォーメーション(DX)の実現を目指す請負開発型のコンサルティングサービスです。AI、iPaaS、および先端の技術を駆使して、製造プロセスの効率化、業務効率化、チームワーク強化、コスト削減、品質向上を実現します。このサービスは、製造業の課題を深く理解し、それに対する最適なデジタルソリューションを提供することで、企業が持続的な成長とイノベーションを達成できるようサポートします。
製造業ニュース解説
製造業、主に購買・調達部門にお勤めの方々に向けた情報を配信しております。
新任の方やベテランの方、管理職を対象とした幅広いコンテンツをご用意しております。
お問い合わせ
コストダウンが利益に直結する術だと理解していても、なかなか前に進めることができない状況。そんな時は、newjiのコストダウン自動化機能で大きく利益貢献しよう!
(β版非公開)