- お役立ち記事
- Successful examples of supplier quality standard setting promoted by the purchasing department
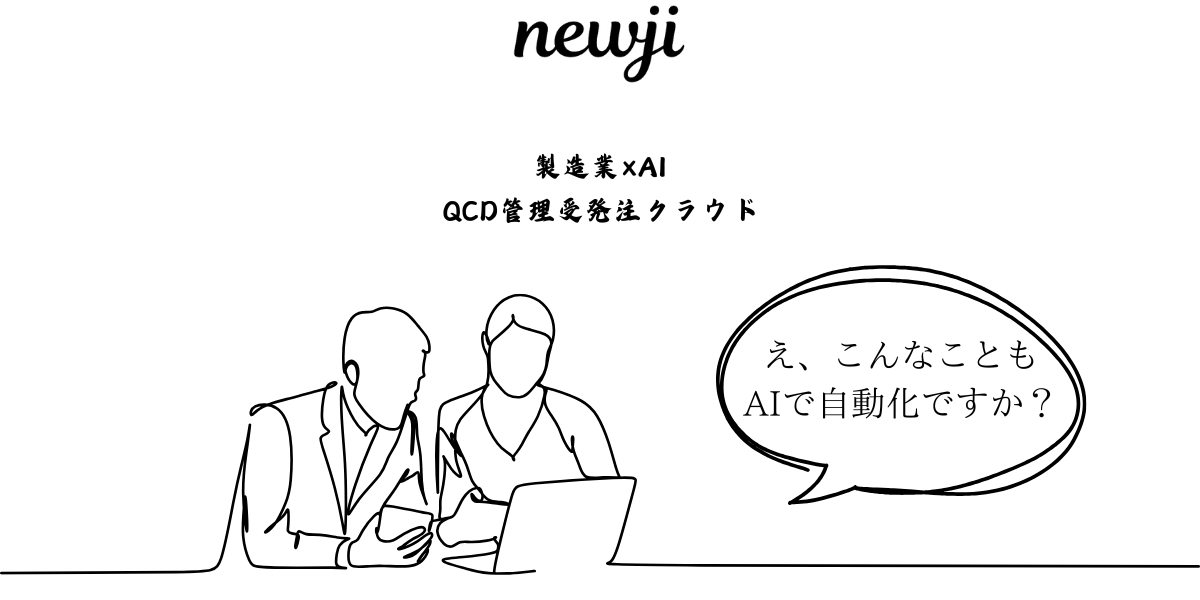
Successful examples of supplier quality standard setting promoted by the purchasing department
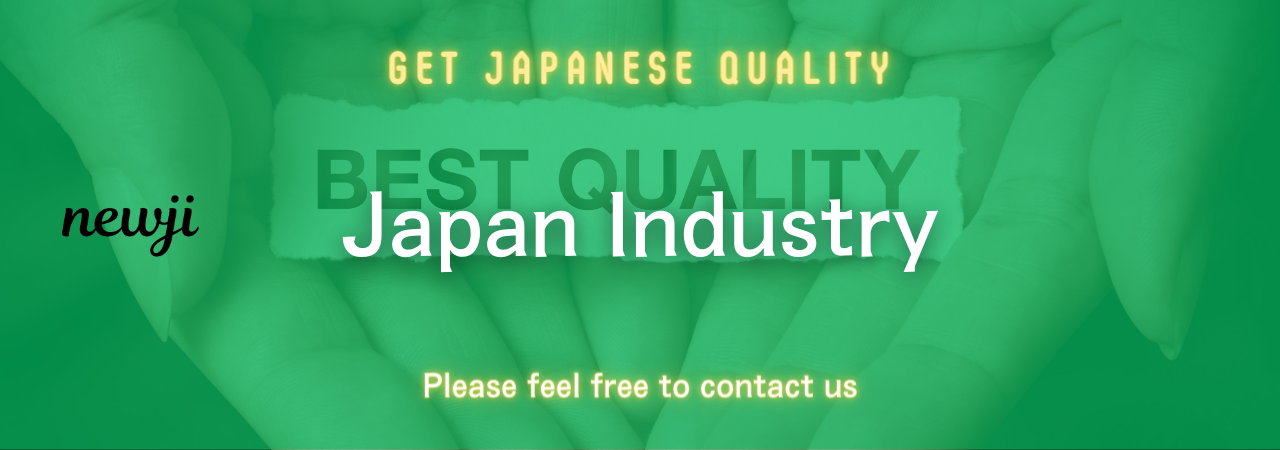
Understanding Supplier Quality Standards
Setting quality standards for suppliers is crucial for any company that relies on external sources for raw materials, products, or services.
These standards ensure that the suppliers meet the required specifications and quality levels, ultimately contributing to the success of the company’s end products and services.
In this article, we will explore successful examples of supplier quality standard setting, particularly those promoted by the purchasing department.
The Role of the Purchasing Department
The purchasing department plays a vital role in setting supplier quality standards.
It is responsible for selecting suppliers, negotiating contracts, and ensuring that the products or services meet the company’s needs.
By establishing clear quality expectations and benchmarks, the purchasing department ensures a smooth supply chain and helps in maintaining the overall quality of the company’s offerings.
Purchasing departments often collaborate with other departments such as production, quality assurance, and logistics to align their objectives and create a comprehensive quality standard.
By doing this, they ensure that all aspects of the supply chain are held to the same expectations.
Key Elements of Quality Standards
When drafting supplier quality standards, companies typically focus on several key elements:
– **Specifications of Products or Services:** Every product or service must meet certain specifications to ensure it aligns with the company’s requirements.
This includes dimensions, materials, functions, and any other essential criteria.
– **Performance Criteria:** Suppliers need to meet specific performance benchmarks, such as delivery time, reliability, and cost efficiency.
– **Regulatory Compliance:** Suppliers must adhere to any industry regulations and standards that apply to the products or services they provide.
– **Sustainability and Ethical Practices:** Many companies are now incorporating environmental and ethical standards into their quality requirements, ensuring suppliers maintain sustainable and responsible practices.
Successful Case Studies in Supplier Quality Standards
Several companies have excelled in setting supplier quality standards, leading to improved supplier performance and better product quality.
Here are a few examples:
Example 1: Toyota’s Supplier Quality Management
Toyota is renowned for its lean manufacturing processes and stringent quality requirements.
The company has implemented a Supplier Environmental Performance Assessment system that evaluates suppliers on various quality and environmental criteria.
Toyota’s purchasing department works closely with suppliers to ensure they meet these standards, providing guidance and training as necessary.
This collaborative approach not only improves quality but also solidifies the relationship between Toyota and its suppliers, leading to mutual benefits and continuous improvement.
Example 2: Apple’s Supplier Responsibility Program
Apple’s strict supplier quality standards are a significant element of its success.
Through its Supplier Responsibility Program, Apple sets high expectations for labor practices, environmental management, and workplace safety.
The purchasing department works to audit and monitor suppliers regularly and provides resources for improvement when necessary.
By holding suppliers to these robust standards, Apple maintains the integrity of its products while promoting ethical practices across its supply chain.
Example 3: Cisco’s Supplier Quality Excellence
Cisco has developed a Supplier Quality Excellence program that emphasizes collaboration and communication.
The company uses a Supplier Scorecard to assess performance, providing feedback to suppliers on how they can improve.
Cisco’s purchasing department actively supports suppliers by offering training and resources.
This partnership fosters innovation and efficiency, ultimately enhancing the quality and reliability of Cisco’s products.
Steps to Set Effective Supplier Quality Standards
Companies looking to implement successful supplier quality standards can follow these steps:
1. **Define Clear Objectives:** Establish what you want to achieve with your supplier quality standards, whether it’s improving product quality, reducing costs, or enhancing delivery times.
2. **Collaborate with Stakeholders:** Work with different departments within your company to gather insights and create a comprehensive set of standards that align with your overall business goals.
3. **Develop a Detailed Supplier Assessment:** Create an evaluation system to assess suppliers based on your defined criteria.
This could include performance metrics, audits, and feedback mechanisms.
4. **Communicate Expectations Clearly:** Ensure that your suppliers understand your quality standards from the outset.
Provide them with detailed documentation and any necessary support to meet these requirements.
5. **Foster Continuous Improvement:** Encourage suppliers to strive for continuous improvement by providing regular feedback and recognizing achievements.
This collaborative approach helps create stronger partnerships and promotes ongoing enhancements.
Benefits of Setting Supplier Quality Standards
Implementing effective supplier quality standards offers companies several advantages:
– **Consistency in Quality:** By ensuring all suppliers meet the same criteria, companies can maintain a consistent level of quality across their products and services.
– **Reduced Risk:** Clearly defined expectations minimize the risk of supply chain disruptions caused by subpar products or services.
– **Improved Supplier Relationships:** Effective communication and collaboration build strong partnerships, leading to better performance and mutual success.
– **Enhanced Brand Reputation:** Companies known for their high-quality standards gain a positive reputation in the market, attracting more customers and business opportunities.
By following these guidelines and learning from successful companies, organizations can set supplier quality standards that effectively enhance supply chain performance and contribute to overall business success.
資料ダウンロード
QCD調達購買管理クラウド「newji」は、調達購買部門で必要なQCD管理全てを備えた、現場特化型兼クラウド型の今世紀最高の購買管理システムとなります。
ユーザー登録
調達購買業務の効率化だけでなく、システムを導入することで、コスト削減や製品・資材のステータス可視化のほか、属人化していた購買情報の共有化による内部不正防止や統制にも役立ちます。
NEWJI DX
製造業に特化したデジタルトランスフォーメーション(DX)の実現を目指す請負開発型のコンサルティングサービスです。AI、iPaaS、および先端の技術を駆使して、製造プロセスの効率化、業務効率化、チームワーク強化、コスト削減、品質向上を実現します。このサービスは、製造業の課題を深く理解し、それに対する最適なデジタルソリューションを提供することで、企業が持続的な成長とイノベーションを達成できるようサポートします。
オンライン講座
製造業、主に購買・調達部門にお勤めの方々に向けた情報を配信しております。
新任の方やベテランの方、管理職を対象とした幅広いコンテンツをご用意しております。
お問い合わせ
コストダウンが利益に直結する術だと理解していても、なかなか前に進めることができない状況。そんな時は、newjiのコストダウン自動化機能で大きく利益貢献しよう!
(Β版非公開)